The manufacturing landscape is undergoing a profound transformation in the era of Industry 4.0, characterized by the integration of digital technologies, automation, and data-driven decision-making. Production systems and machines are now required to be faster and more flexible while adapting to continuously changing manufactured products.
Quality 4.0 is at the heart of this evolution. It is not a standalone concept but instead focuses on applying Industry 4.0 principles to quality management and assurance. It encompasses digitizing assets, seamless communication between machines, and applying the Internet of Things (IoT) mindset to the manufacturing sector.
Quality 4.0 holds the potential to empower quality engineers and professionals, elevating the responsibilities and importance of the quality department within organizations. The key to this transformation lies in harnessing the vast amounts of data generated by interconnected machines that show trends and relationships in a manufacturing space that were previously unknown. Quality engineers are uniquely positioned to leverage this data because they have been analyzing and interpreting manufacturing data for decades.
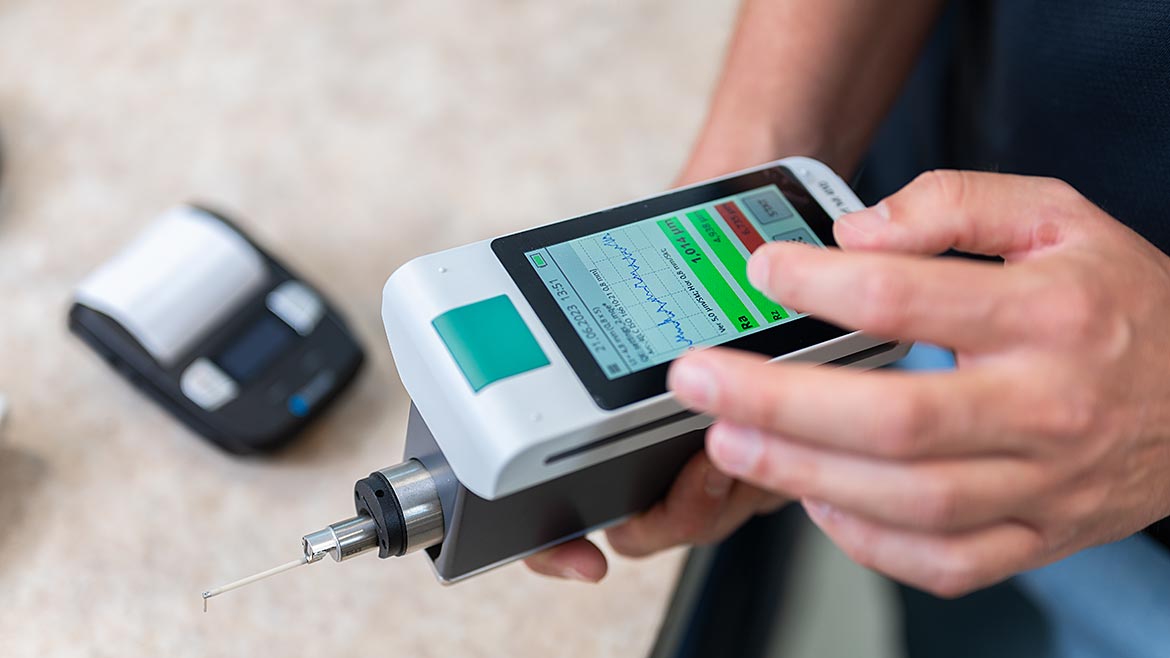
Industry Trends Driving The Need For Quality 4.0
While Quality 4.0 is gaining attention and standards are being developed, it is still in the relatively early phase of widespread adoption. However, several compelling trends are propelling Quality 4.0 forward.
The first trend driving adoption is the increasing demands of major manufacturers in highly regulated industries, including automotive, aerospace, and healthcare. These manufacturers operate with a “trust but verify” mentality and require more comprehensive quality control processes and data collection. This includes the wealth of data generated from in-process floor measurements.
Quality 4.0 provides a robust system for documenting and verifying quality practices, offering complete visibility into the manufacturing process from the beginning through final inspection, emphasizing traceability and tracking. This data is critical for quality control, liability protection, and ensuring the safety of products.
Another core driver of Quality 4.0 adoption is its ability to identify and mitigate risks early in the production process. The cost of testing and verifying product quality, especially in critical industries, far outweighs the manufacturing costs. Hence, ensuring quality and reducing the risk of failure is paramount.
These factors are essential in industries where product failure can have severe consequences, like those mentioned above.
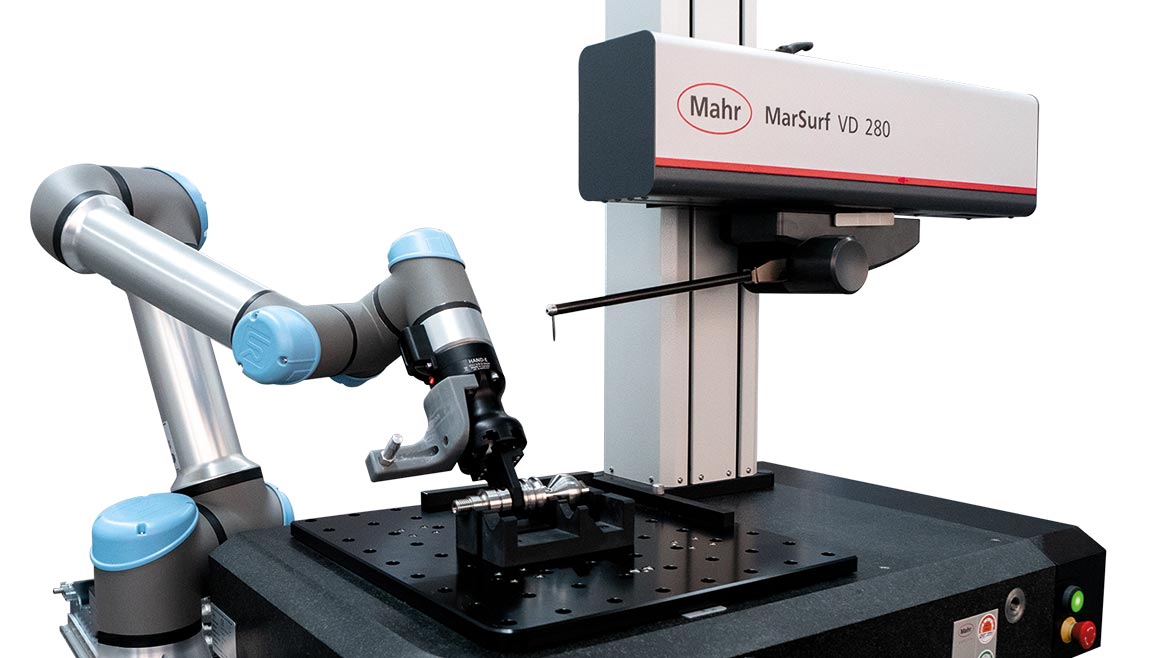
The Importance Of Data Integrity In Quality 4.0
Quality 4.0 places a strong emphasis on leveraging data for decision-making. It involves collecting and analyzing vast amounts of data from various sources, including gages, machines, sensors, and quality control systems. This data is used to identify trends, deviations, and opportunities for improvement.
Ensuring data integrity is crucial. In Quality 4.0, it is becoming increasingly important not only to collect measured results but also to know when and where the data came from. With the integration of digital technologies, Quality 4.0 enables enhanced traceability throughout the production process. Manufacturers can track the history and origin of each product or component, which is vital for quality assurance and compliance.
For example, standards are being implemented in the automotive industry with requirements regarding documented information vital to the success of the quality management system itself. In addition, there are requirements concerning the verification of processes being carried out as intended, the fitness for monitoring and measurement equipment, and the documentation of monitoring and measurement activities and their results.
To ensure enhanced traceability, it is crucial to ensure that when collecting measurement data from precision gaging tools, the measurement was made on equipment dedicated to that purpose. This can be achieved by having the gage send a unique identification number, the part number it is measuring, and a date and time stamp to the data collection system. This enables documentation of the measuring device used, ensuring traceability of measurement results and providing essential data integrity.
Often, this can be easily implemented with software that enables the user to add information concerning the unique gage identifier, part number, and setup parameters for the measuring system. This allows a controlled and calibrated measuring instrument to be used with the parameters set up for that particular part.
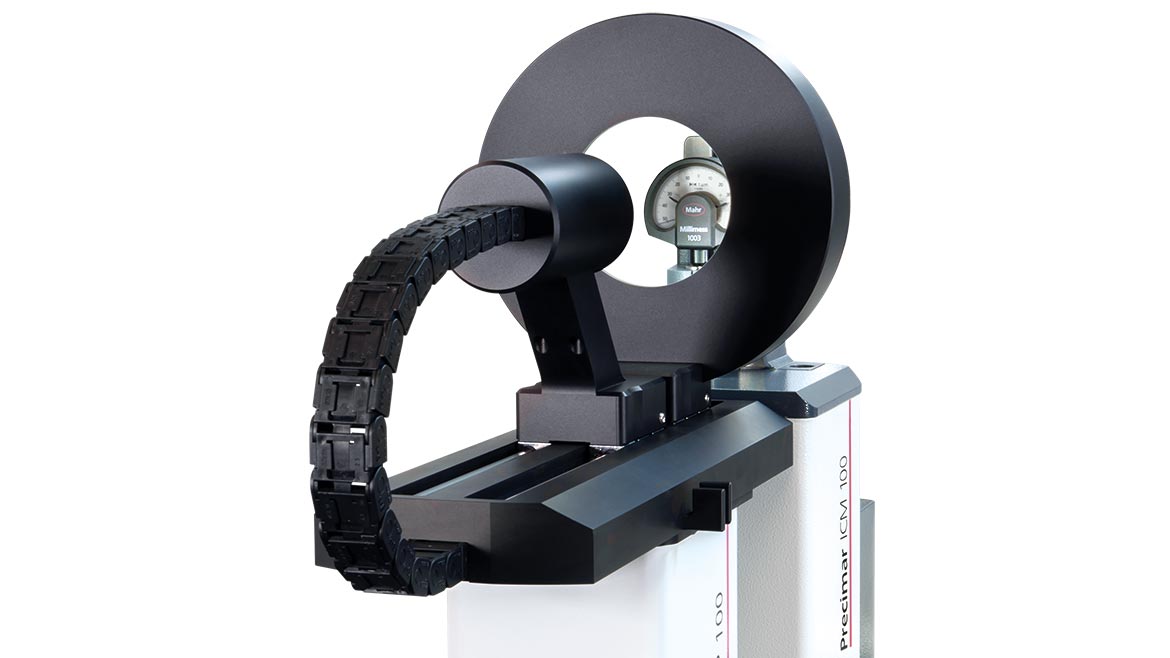
How AI And Automation Aids Productivity In Quality 4.0
Quality 4.0 tools will increasingly leverage automation and artificial intelligence (AI) to streamline quality control processes and help augment human capabilities with data-driven insights. For example, they help with automated monitoring and data analysis, making the job more efficient and focused on value-added tasks.
Precision gaging data is often processed and analyzed automatically using advanced analytics and machine learning algorithms. This can identify trends, anomalies, and potential quality issues that may not be apparent through manual inspection. Data is shared in real-time, allowing quicker responses to quality issues to adjust to maintain quality standards and create more effective communication between departments.
AI software can monitor trends, identify deviations, and flag critical issues, allowing engineers to take corrective actions swiftly. It can also automate routine tasks like machine adjustments or scheduling maintenance. This increases productivity and ensures that the best products leave the manufacturing floor.
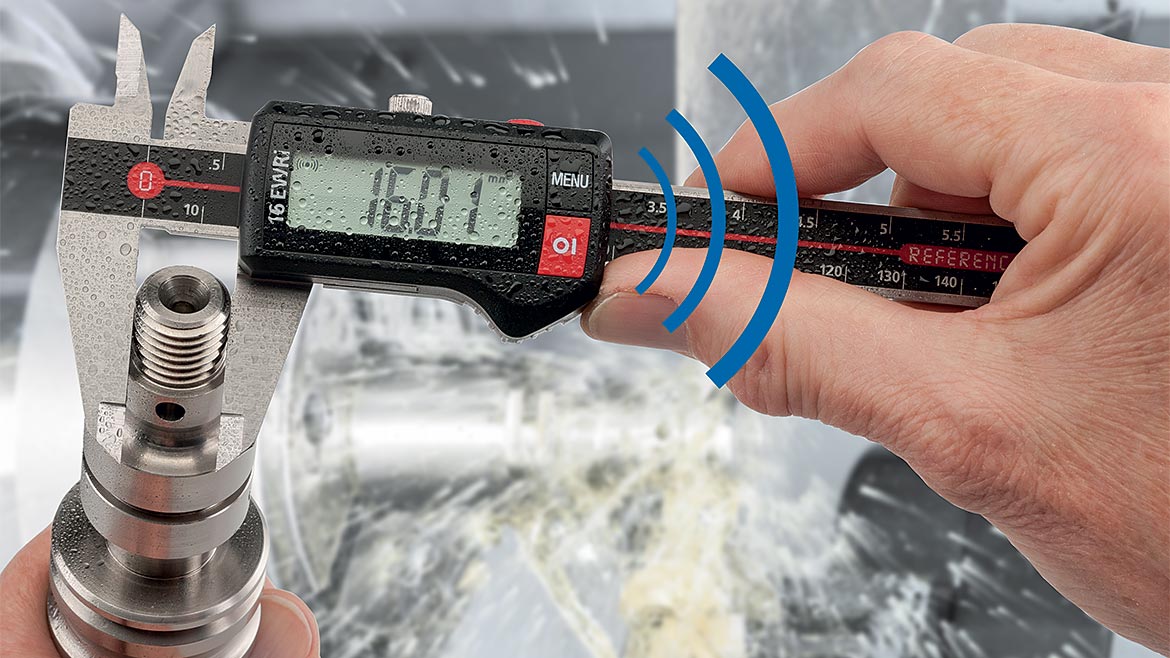
Precision Gaging Tools Enabling Quality 4.0
Precision gaging plays a crucial role in Quality 4.0 by enabling accurate measurement and control of manufacturing processes. Integrating digital gaging tools minimizes the risk of measurement mistakes and ensures consistency in data collection. It ensures that products meet specific quality standards and tolerances, essential in industries where even minor variations can lead to product defects, safety issues, or compliance problems.
Some of the precision gaging technologies that play a pivotal role in enabling Quality 4.0 include:
Integrated Wireless Gages: Precision gaging tools, such as calipers, micrometers, and digital indicators, are used to measure the dimensions and features of manufactured parts with high accuracy. These gages can be equipped with digital interfaces and data output capabilities that enable wireless data transmission from other gages for seamless integration with digital quality control systems, transforming analog measurements into digital data. Furthermore, investing in wireless digital indicators has an even higher ROI in enabling a transition to Quality 4.0 as they can be used to adapt existing gages rather than investing in all new gaging.
Universal Interface Software Tools: Smart and fully universal interface software systems integrate gaging modules into a computer, allowing seamless data collection and analysis. This type of software provides a powerful tool for upgrading analog systems to digital. Furthermore, it can enable users to seamlessly access previously saved programs, enabling a measurement to be started without inputting the settings. This saves time while avoiding potential sources of error encountered when carrying out the settings manually.
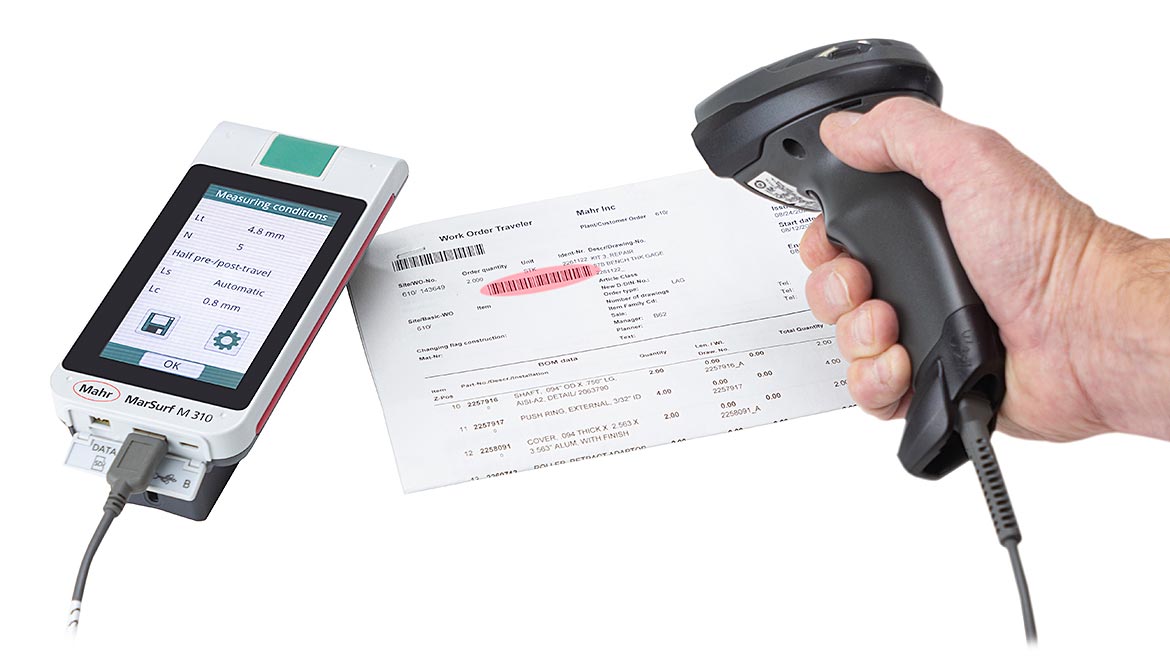
Practical Steps To Begin Implementing Quality 4.0 Now
For quality professionals and manufacturers, practical steps are essential to adopting Quality 4.0 and preparing for a data-driven future. Here are three key strategies to consider for beginning or strengthening Quality 4.0 practices:
Go Digital: Quality 4.0 involves the digital transformation of quality management processes. Upgrade existing analog equipment in gaging and machining processes to digital counterparts and ensure that all equipment is compatible with modern computing technology. This sets the foundation for data collection and analysis.
This process can start slowly when new equipment purchases are evaluated. Traditionally, quality engineers look at two things: performance and price. In the shift to Quality 4.0, more weight should be given to factors such as ease of integration and digital communication when assessing new gaging tools or making a purchasing decision.
Invest in IT Knowledge: Understanding how devices connect and share data is crucial for implementing Quality 4.0 effectively. Collaborate with IT departments to ensure that gages can communicate properly with the network and that all the permissions are intact. Quality professionals should also consider continuing education on networking and data communication to understand the enabling technologies behind Quality 4.0 more thoroughly.
Prioritize Data Collection: Start collecting data even if there are no plans to utilize it immediately. Building a repository of historical data is invaluable for future analysis and decision-making. Many gages on the shop floor already have digital capabilities. If those existing gages can communicate with a network, set up the digital infrastructure to collect and store the data.
Parting Words
In conclusion, Quality 4.0 is not just a buzzword; it's a transformational approach to manufacturing that leverages data to improve quality, productivity, and risk management. By embracing digitization, investing in IT knowledge, and collecting data, quality professionals can adapt to the changing landscape—leveraging precision gaging technology for new data-driven insights to create a more efficient, reliable, and innovative future in manufacturing.