3D printing, or additive manufacturing, is an umbrella term for manufacturing technologies that can generate parts by growing them out of base material. This differs from subtractive manufacturing, such as CNC machining, where a bulk material is reduced to its final shape through cutting or forming. Additive manufacturing is a powerful tool for generating custom parts, often with complex geometries, and serves industries from aerospace & defense, to automotive, to medical and dental, and beyond. We have incorporated a variety of metal and plastic additive manufacturing options across our portfolio of over 20 processes and have worked to build tools to manage and understand the nuances of qualifying 3D printed components over those that are traditionally manufactured.
In the realm of manufacturing, the evolution from traditional methods to additive manufacturing (AM) represents a paradigm shift, bending some of the rules and preconceptions behind the design and qualification of parts. Additive manufacturing typically has benefits for low-volume manufacturing where value can be added at a reduced cost for similar results. This can be for applications like prototyping as well as functional, end-use parts that incorporate more features without assembly, generated organic geometries, and purpose-driven lightweight structures. However, this transition is not without its intricacies, especially when it comes to ensuring quality and consistency. In this article, we’ll delve into the complex world of additive manufacturing inspection, exploring the challenges and considerations unique to parts that are grown versus cut.
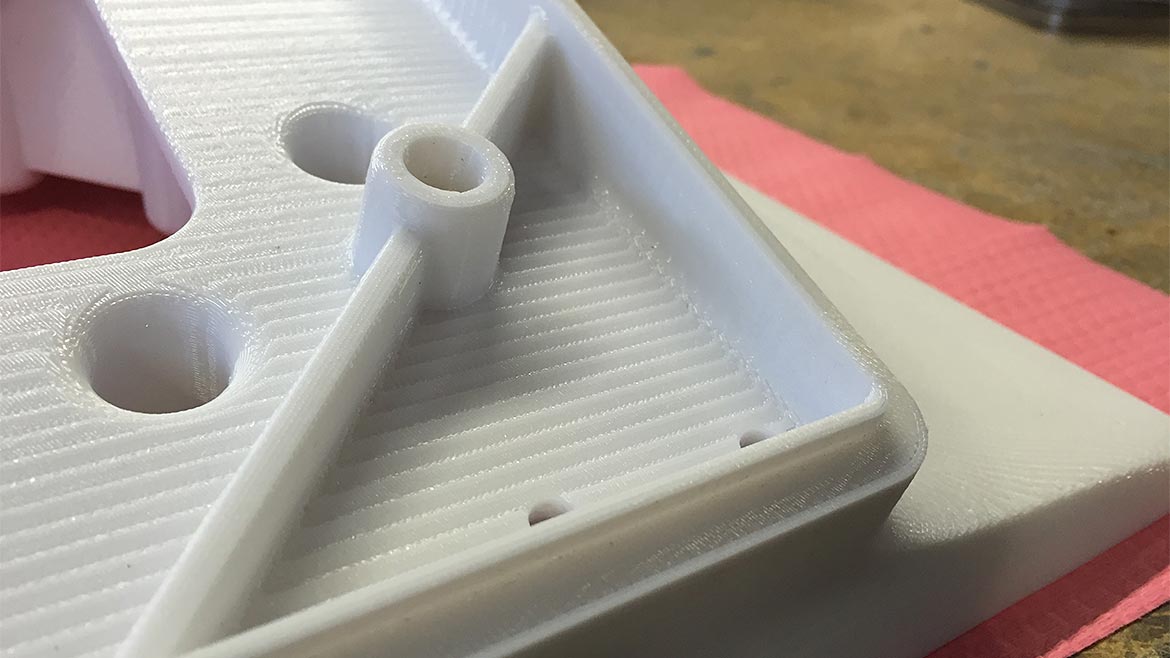
Thinking in Near-Net-Shape: Additive vs. Traditional Manufacturing
In CNC machining, a digital design is programmed using CAM and executed through a series of operations on the platform. Operators can incrementally stop, measure in process, and adjust their program and offsets to hit the desired tolerances. A technical print can dictate the inspection requirements of a directly manufactured part with this level of interaction, giving highly precise components and repeatability.
When parts are manufactured with 3D printing there is no ability to pause and adjust during building, which is typically done in a thermal and even gas-controlled build chamber. Additive manufacturing success is highly dependent on the geometry, build setup software and realistic expectations of the process. Build preparation software interprets the 3D model and may dictate the orientation, build parameters, sacrificial support generation (if necessary), and slice data exported and fed to the machine. Automation is important in this software, but manual intervention is common for orientation and part arrangement.
Successful additive manufacturing is heavily dependent on the software input to build its part and the outcome is the combination of the slice input, the machine, the build parameters, the supporting structure, the equipment, and the material used. Any part built using any additive manufacturing technology will produce a near-net shape driven by the CAD input. Tuning critical features in additive manufacturing may require an iterative approach. This is often accomplished by printing, measuring, and offsetting the original model to print again.
General tolerances vary between manufacturing equipment and the material used for 3D printing. Dimensioning a print for additive manufacturing should reflect these considerations and reference dimensions are very common for spot-checking without pass/fail (e.g., for general XYZ dimensions).
Managing Expectations from Design to End Product
Additive manufactured designs for production parts should begin with the end in mind. This process is often referred to as DfAM or design for additive manufacturing. This differs from traditional DFM, where it looks at design characteristics for successful manufacturing within a given process, because DfAM incorporates a holistic approach to design from software setup, to the process, the material used, and secondary operations to bring it into its needed specifications.
Plastic 3D printed parts DfAM considerations may consider the following criteria:
- Orientation-specific features that mitigate support (if required) or achieve the needed mechanical requirements. Orientation is more critical for performance on printer platforms that have anisotropic properties, where the XY planar face is stronger than the Z direction. This is a common consideration with filament-based printing methods like fused deposition modeling (FDM). Additionally, vertically grown surfaces and top/bottom planes tend to look smoother than gradual transitions due to discrete layer sizes depending on the platforms used.
- Secondary processing such as tapping or reaming, installing inserts, milling, and other surface treatments. Coatings like paint or sealant will add thickness to the part, which may require CAD offsets during build preparation to accommodate any critical fits.
On top of the features above, metal 3D printed parts usually have more stringent requirements around critical tolerances, surfaces, heat treatments, and features. In this manner, metal 3D prints, such as direct metal laser sintered (DMLS), can be compared to secondary processes for die casting.
- Heat treatment may be as simple as annealing, or as complex as hot isostatic pressing (HIP), to achieve the needed characteristics of the metal. Heat treatments can cause deflection of the material and should be considered when preparing a print – especially for post-machining.
- Secondary machining is typical with metal-printed production pieces. Post-machined parts benefit from improved mechanical properties due to a continuously smooth surface with reduced micro-stress points. However, post-machining is often expensive, requiring custom setups and test runs as well as anticipatory features for indicating, workholding, and thickening features that will be cut. Post-machined 3D printed components require upfront CAD design work to achieve the best results and should have two file sets for the net shape and the finished product. This would be a similar approach to processes like investment or die casting.
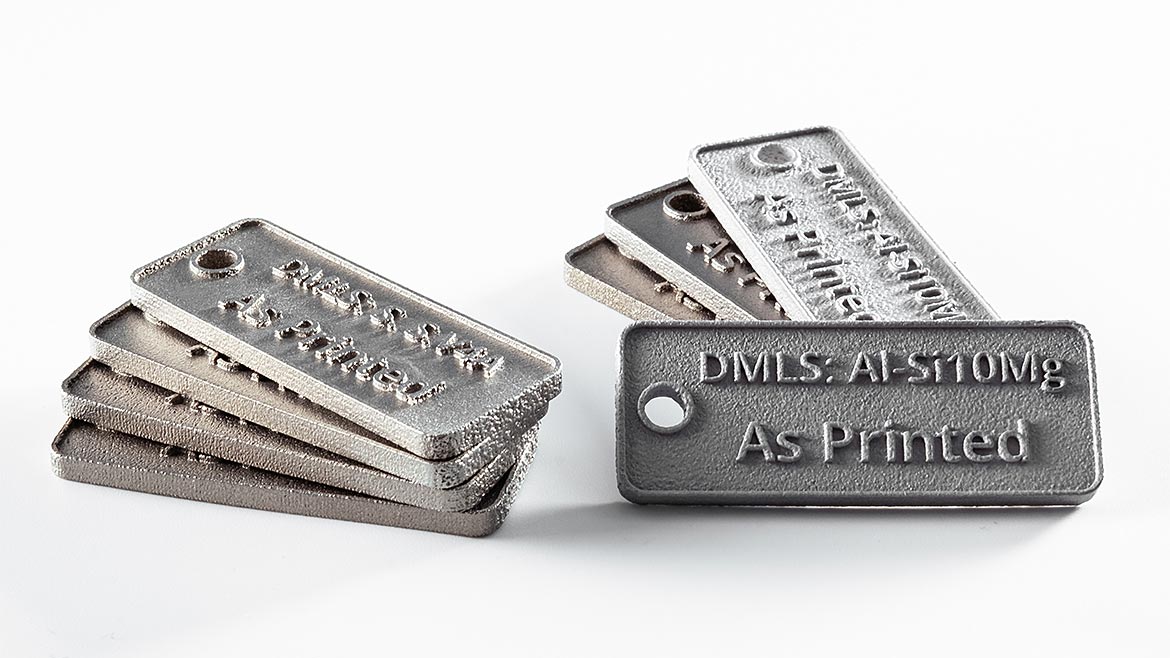
Additionally, surface finishes of 3D printed parts vary by process and material. They are coarser than traditionally manufactured surfaces like machined parts because they represent their raw stock material:
- Filaments (FDM, FFF) may show coarse zigzag and layering on the part.
- Powder bed (SLS, HP MJF, DMLS, Binder Jetting) has a sugar-cube finish from the raw powder stock.
- Resin printing (SLA, DLS, LSPc, DLP) shows smoother surfaces from the liquid photopolymer stock.
Surfaces can be treated and smoothed after printing if required but should be considered standard for any as-printed features.
Measurement and Inspection of Additive Manufactured Components
As-built 3D prints should have standard inspections applied after they are cleaned, and supports are removed. This includes general size measurements to ensure proper scale (e.g., XYZ) and that all features are resolved to the extent of the equipment and material selected. Technical drawings should only highlight what is critical for the part function and must be considerate of the processes’ general manufacturing standards. This may affect general tolerances on the title block. For cases like rapid prototyping, this general inspection is usually sufficient for shipping.
Once the near-net shape has passed preliminary inspection, the secondary processes can be applied, and a separate print may dictate the final product’s needs. It is important to understand that any features in contact with sacrificial supporting structures or, in some instances, the build plate may need looser tolerance requirements than other grown features. This helps accommodate for surface deviations after part and support removal.
Parts can be inspected with manual tools, gages, vision systems, or CMM. One major difference in inspecting additive manufactured components is how cantilevered features, such as on a manifold, should be toleranced. Minor deflections from printing and secondary processes can affect these features and may require their datums for machining. Internal structures are difficult to measure with manual tools or gages and nondestructive methods like CT scanning become useful.
In metal production cases, tensile bars and other accompanying pieces are printed simultaneously for testing and inspection of material properties without directly testing the printed component. These test items are printed with every new part to ensure consistent passable results for mechanical validation.
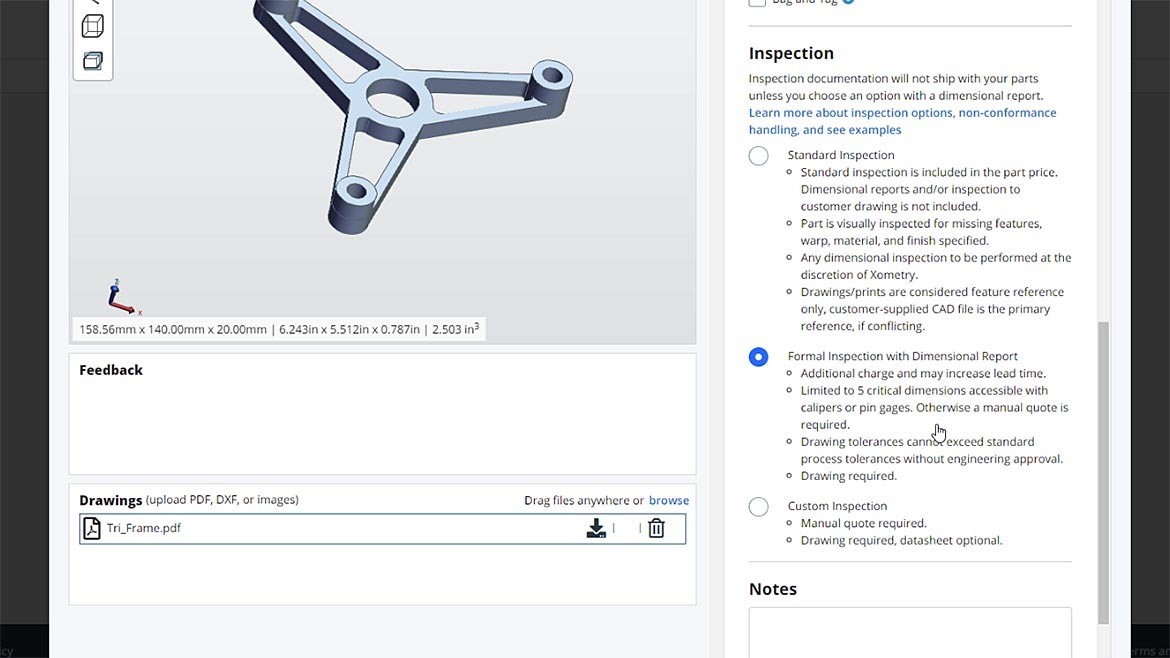
Embracing Additive Manufacturing
Additive manufacturing signifies more than just an advancement in production capabilities; it heralds a fundamental transformation in the manufacturing ethos. This technology isn’t just about adopting new tools; it’s about reimagining the paradigms of design, production, and problem-solving. With its ability to create complex structures and innovative solutions, additive manufacturing is reshaping critical industries from aerospace to medical, pushing the boundaries of what's feasible.
Here we recognize and embrace the dynamic and evolving landscape of additive manufacturing. We are committed to exploring and realizing the vast potential of this technology. As the industry progresses, the expanding role of 3D printing in production scenarios becomes increasingly evident. For manufacturers, designers, and engineers, this is a pivotal moment to delve into the possibilities that additive manufacturing unlocks. By mastering its unique strengths and addressing its challenges, we are not just adapting to a new manufacturing era; we are actively shaping it. This journey into the advanced terrain of additive manufacturing is set to redefine our understanding of quality, precision, and innovation in the manufacturing world.