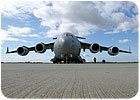
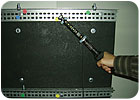
Inertial motion-sensing technology enables the real-time tracking of position, orientation and movement of objects, bringing higher speed and quality to industrial control applications. A key feature of the system is the inclusion of inertial sensors, which are immune to interference from ferrous or electromagnetic sources. Source: InterSense
To meet the challenge of producing quality products at a competitive cost, manufacturers long ago began automating as many of their manufacturing processes as they could, with the payoff coming from producing better products, cheaper and faster than their competitors.
The primary objective of automating a process is to reduce, or even eliminate, the manual or “touch” labor involved in a manufacturing process. The utopian vision is fully automated factories that would use intelligent robots and sophisticated machines to fabricate a variety of customized products quickly, inexpensively and without defects.
In businesses that produce a high volume of standardized products, automation can approach that vision. However, industries such as aerospace typically produce relatively small volumes of complex assemblies, in which the manufacturing process simply does not lend itself to fixed automation. Fixed automation systems have yet to reach the level of sophistication and flexibility of the trained human technician so, for example, jet engines are still assembled mostly by hand.
As sophisticated as humans are, they are prone to human error. Distraction, fatigue, illness and interruption, not to mention worker substitution because of absence, can all lead to mistakes. As a result, the most sophisticated assembly resource can be the most vulnerable to inaccuracies.
In spite of the fact that as much as 40% of manufacturing processes occur beyond the limitations of a fixed automation system, manufacturers can still realize benefits from automation in these manual environments. These benefits are derived not from replacing people with machines but from providing workers with right-on-time information that helps them accomplish their jobs accurately the first time, every time.
Simply put, right-on-time information augments human performance. Just as just-in-time inventory control avoids receiving material earlier than needed, providing right-on-time information avoids an operator receiving feedback too late to correct an error as it occurs.
Technologies such as augmented assembly and verification, for example, combine motion tracking, process tracking and real-time feedback to monitor assembly accuracy, detect mistakes and provide the operator with the feedback needed to immediately correct those errors. If the system also can document the resulting assembly accuracy, manufacturers can avoid duplicative manual verification processes.
This blend of man and machine enables the implementation of semi-automated manufacturing processes that leverage the best elements of both manual and fully automated approaches, while protecting against their respective weaknesses.
Moving Beyond Traditional Control Processes
The accuracy of traditional manufacturing processes often varies with the amount of manual labor involved. Take the example of an assembly procedure where human operators are applying fixture bolts with the use of a manual torque wrench. The first element of control is feedback. Manual torque wrenches are fitted with adjustable torque meters that emit an audible click when a preset torque threshold is achieved. This sound tells the operator that the bolt on which he is now operating is correctly torqued.
Adding external monitoring to this process provides the second element of a manufacturing control system because the system can now be used to automatically verify that the procedure took place. As useful as external monitoring may be, it is not enough.
Assume that the procedure at this assembly station calls for the operator to tighten five bolts in a specific sequence. The system detects that five bolts were tightened to the threshold torque value. However, if the operator tightened the bolts in the wrong sequence, or tightened the wrong five bolts, potentially missing one of the target bolts in the process, the monitoring system determines that five bolts were tightened but is unaware of the mistake in pattern sequence or bolt selection. Without accurate bolt identification, an inspector must still check the completed work using today’s manual technique of duplicating the procedure several times, thus increasing assembly costs and manufacturing lead times. Moreover, the accuracy of the original pattern sequence can never be verified.
As a result of an incomplete monitoring system, this fully manual torquing procedure can release defective product to the next station in the assembly process and ultimately to the customer, despite costly duplicative quality checking steps intended to prevent such errors.
Ironically, manual errors can occur even in highly automated environments. In-line rejects are typically routed to repair stations where the defective work is reworked manually. Because rework and repair is performed “outside” the inline manufacturing process, its effectiveness depends completely on the operator knowing how to conduct the operation correctly. Visual inspection is often the only quality safeguard at these stations. In many manufacturing operations, more than 50% of defective production is generated at manual or semiautomatic repair stations, critically impacting competitiveness in the areas of cost, quality and productivity.
Machine vision is frequently used for the inspection of manufactured goods such as semiconductor chips, automobiles, food and pharmaceuticals to detect production defects. These systems are programmed to perform narrowly defined tasks such as counting objects on a conveyor, reading serial numbers and searching for surface defects.
Contrary to what the term machine vision suggests, the computer cannot “see” what is happening on the plant floor. Rather, machine vision systems look for differences between a preprogrammed ideal image and images taken during actual production. For defined, repetitive production, machine vision has proven to be an effective inspection approach. However, vision systems by definition can only detect visible flaws and they only identify flaws, not their source. They also have proven impractical in monitoring large, complex assembly tasks, and therefore are not well suited to real-time touch manufacturing process improvement or control.
Augmented Assembly and Verification Systems
Motion sensing and tracking is a technology that is well proven in the flight simulation side of aerospace as well as in weapons trainers, sports training, ergonomic design and motion capture.
Adding motion-sensing technology to the manual assembly process enables technicians to check their own work, detecting and correcting errors before they are “baked in” to an assembly. Operators are able to document the accuracy of their work, provide a quality assurance (QA) audit trail and eliminate the costly process of inspection by duplication.
This is achieved by accurately locating and tracking an assembly tool relative to the fixture during the performance of an assembly procedure. By matching the exact position of the tool to that of the object to which it is affixed, an assembly control system can determine that a scheduled task was successfully completed by capturing relevant data, such as the position and motion of the tool, torque threshold achieved and part identification, with a time stamp of the event. In turn, an electronic QA log can be updated to record the successful completion of the task.
In the event an error is detected by the system, the technician can be directly alerted to allow immediate self-correction and verification. This spatial confirmation dramatically reduces the number of visual and “repeat procedure” quality checks required before the technician can move to the next task, speeding workflow while improving quality.
This innovative combination of “soft automation” and human augmentation enables the deployment of augmented assembly and verification systems which can reduce or eliminate errors at assembly and repair stations by tracking and verifying manual and semiautomatic assembly procedures in real-time using precision motion-sensing technology.
Until now, this capability has been difficult to deploy in highly dimensional environments such as the assembly of jet engines, aircraft and construction equipment. The traditional means of tracking tool motion has required mechanical arms, magnetic sensors or continuous visibility of the tool, each of which is impractical in assembling such complex equipment. However, recent advances in the miniaturization of inertial sensing technology now allow the deployment of operator-friendly systems in environments long thought impossible to address.
These new augmented assembly and verification systems are made up of four elements:
1. Miniature inertial sensors and LEDs that are built into or affixed to the assembly tool-for example torque wrench, rivet gun, air gun, drill-along with a small wireless transmitter.
2. Small cameras mounted around the work station that track the position of the LEDs in real-time as the operator performs an assembly procedure.
3. Motion fusion software that captures the wireless data and processes this data to determine the exact position, orientation and movement of the tool during the procedure.
4. A workstation computer that compares the actual tool movement against a correct procedure template to detect errors or confirm accurate completion, provide real-time feedback to the technician and generate QA audit trails and reports.
Inertial motion-sensing technology enables the real-time tracking of position, orientation and movement of objects, bringing higher speed and quality to industrial control applications. A key feature of the system is the inclusion of inertial sensors, which are immune to interference from ferrous or electromagnetic sources-an essential characteristic for environments where complex machinery is manufactured. They provide a smaller, more ergonomically correct form factor for the tool than do mechanical tracking systems and they provide faster detection of angular motion or orientation than do purely optical systems.
Furthermore, the use of an inertial sensor allows for a reduction in the number of cameras required to accurately track the sensor and eliminates data losses due to occlusion. As a result, the overall cost of the system is reduced and its accuracy maximized.
Key attributes of such a system include:
• Right-on-time information to the assembly technician.
• No mechanical arms or constraints on operator movement.
• Continuous tracking immune to acoustic, magnetic or visual interference.
• Full data capture for quality documentation and performance tracking or retraining.
While most quality assurance manufacturing solutions in use today, such as digital manufacturing, vision systems and radio frequency identification systems, are focused on monitoring fully automated production processes, augmented assembly and verification systems address the remaining 40% of manufacturing that happens outside of a fixed automation environment. Integrating inertial technology into the manual assembly process provides a new error-proofing and verification functionality that can proactively reduce production errors and eliminate redundant inspections.
The business result is reduced cost, improved quality and accelerated throughput, any of which can increase company profitability and market share.
Tech Tips
- To meet the challenge of producing quality products, manufacturers long ago began automating as many of their manufacturing processes as they could.- Technologies such as augmented assembly and verification combine motion tracking, process tracking and real-time feedback to monitor assembly accuracy, detect mistakes and provide the operator with the feedback needed to immediately correct those errors.
- Adding motion-sensing technology to the manual assembly process enables technicians to check their own work, detecting and correcting errors before they are “baked in” to an assembly.
Mike Donfrancesco is the vice president of sales for InterSense (Bedford, MA). He can be reached at [email protected] or (781) 541-7606. T.C. Browne is the chief executive officer and president of InterSense. He can be reached at [email protected] or (781) 541-7601. For more information, visit www.intersense.com.