Since its early days, machine vision has been primarily used to check the liquid level in a bottle, or verify if a packaging label is applied correctly. A computer was able to compare a known good image to what the camera was currently “seeing” and then executed an action based on the Go/No-Go argument, therefore preventing items that had failed the test from moving further along the assembly line. In short, an important yet limited manufacturing function.
Today, however, even a cursory review of the trade press shows that machine vision has greatly expanded its horizons beyond the assembly line. While not as numerous as the omnipresent security cameras in our everyday lives, applications where machine vision cameras are being deployed have grown exponentially. For example, consider such diverse uses as the remote monitoring of hazardous locations, 3D mapping, agriculture, automated retail, or genome sequencing.
Machine vision companies that have ventured into these new markets have encountered different interface standards to what they are accustomed to. For example, consider the broadcasting industry where things like video quality, durability, speed, time code, and flexibility are all must haves. Professional videographers have long focused on Serial Digital Interface (SDI or HD-SDI) as their main high-speed interfaces. Yet several broadcasting companies are now taking a hard look at CoaXPress (CXP), a similar standard to SDI. This is because of CoaXPress’s use of the ubiquitous coaxial cable and the ability of the protocol to transmit zero-latency uncompressed high-resolution video, while supplying power and controlling the camera. Simultaneously, working groups with the CoaXPress Committee are researching SDI companies and seeing how faster data rates can be achieved by modifying equipment. Besides broadcasting, there are a number of other parallel industries that have their own data transfer interfaces, such as HDMI 1.3 in microscopy, 3G-SDI in defense, LVDS in traffic imaging, and GMSL in automobiles.
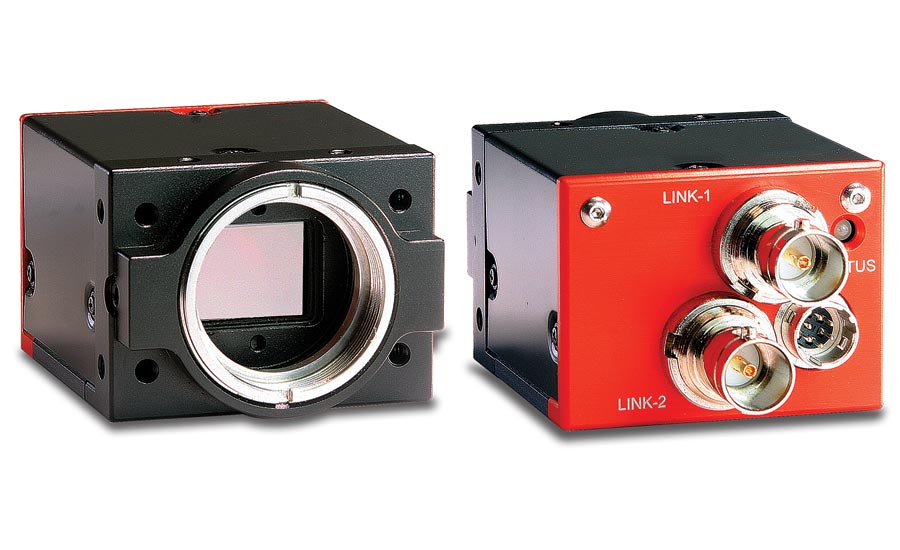
Small form factor industrial cameras with single/dual-link CoaXPress output. Courtesy of IO Industries Inc.
Obviously, it best serves all parties if the machine vision industry collaborated with these various industries to share expertise on how best to get the data from a camera’s sensor to the PC memory for processing. While some machine vision companies have adapted their equipment to industry-specific standards rather than CXP, USB, GigE or Camera Link, for the most part these emerging markets could be best served with the available technology that the machine vision industry has spent the last 30 years developing, improving and perfecting.

This is a 48-Megapixel 30fps camera with quad-link CoaXPress interface. Courtesy of IO Industries Inc.
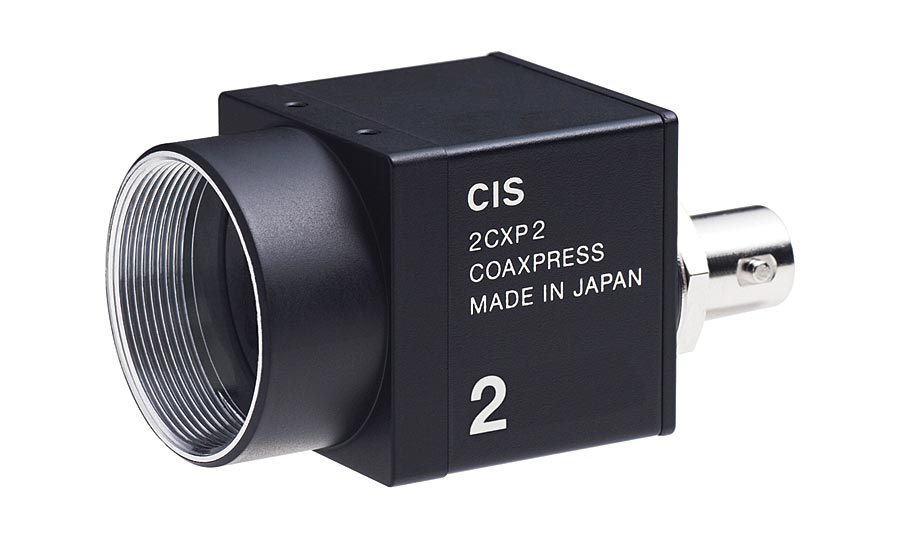
The current trend in the CXP world is the introduction of single-link CXP cameras and frame grabbers. Source: CIS Corp.
MANY INTERFACES, ONE GOAL
Since the 1980s, the machine vision industry has migrated successfully from analog to FireWire, Camera Link, GigE, CXP, USB and other different digital options that enable system integrators to engineer the optimal solution, whether it is a requirement for a large image over a long distance, or the focus is on a small region of interest (ROI) running as quickly as the camera can capture. No matter what the need, there is a common goal: an accurate, reliable and cost-effective solution. Therefore it only makes sense to hand this responsibility over to machine vision experts with decades of experience on getting the first pixel out of a camera all the way to the decision making process on the computer. When you think about it, it’s like hiring a plumber when you have a leaky pipe, or an accountant when you need your taxes prepared. Working with a machine vision company makes perfect sense when trying to integrate or refine the vision options in a system.
THE GROWTH OF CXP
A lesson in this style of collaboration is CoaXPress (CXP), the brainchild of several machine vision companies that, while competitive in some respects, have also joined forces to encourage the widespread adoption of this interface. Back in 2009, CXP was developed to confront the ever growing size of camera sensors and their increasing speeds. As sensors grew in size, so too did the customer’s thirst to deploy them to create a better, bigger and faster system than current technology. Customers in the semi-conductor industry were especially interested in developing faster, more efficient methods of streamlining their production for an enhanced competitive position.
Today, there are over fifty different companies working with CoaXPress. Market research suggests this interface will soon double in size. The current version of CXP is 1.1.1, which was adopted in late 2015. The next reiteration is CXP 2.0, and it promises much more. The final draft of CoaXPress 2.0 was anticipated to be ready towards the end of 2017 with the first certified products expected in 2018. Central to this updated standard is an unprecedented speed boost to achieve lightning fast data rates. CoaXPress 2.0 will extend data transfer rates to a new machine vision highest data rate of 12.5 Gb/S (CXP-12) per link. Greater speed translates into enhanced flexibility in system design, and in the reduction of total system costs. In recognition of the global trend and increasing adoption of 3D vision techniques, CXP 2.0 also is expected to have extensions for 3D imaging. This addition to the standard is especially timely given the increasing use of 3D machine vision in the automotive and electronics industries.
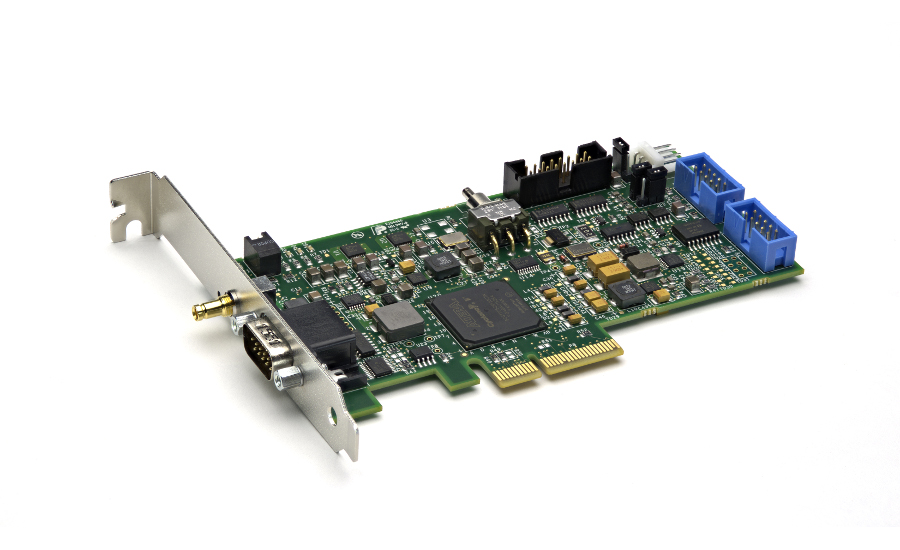
A single link CXP frame grabber (Aon CXP). Source: BitFlow
The current trend in the CXP world is the introduction of single-link CXP cameras and frame grabbers, a combo that is now challenging the USB3 market. A winner in both cable length and increased bandwidth, single-link CXP is causing USB3 users to step up and take notice. Customers using FireWire and GigE Vision solutions are also considering this new solution in traditional and emerging markets.
THE ROLE OF COST
In the automotive industry, the data transmission standard can be GMSL or FPD-Link, amongst others. In the datacom transmission market—think internet and phone—the transfer is DSL/T-1 or Fiber. In most cases, these standards are driven by the current technology available and connector costs. If twelve cameras are installed in a car, for instance, the cost of each connector is multiplied 12 fold. So the difference between a $2 and a $15 connector becomes a major determining factor in the manufacturing decision making. Therefore it is unlikely these industries will be interested in converting to machine vision standards anytime in the near future. All that said, there’s a lot to be learned from looking at automotive, data communications and other industries and seeing what and why they use certain technologies, besides costs.
CONCLUSION
Vision is an important part of industry and, ultimately, our lives, from security cameras in banks and backup cameras in our cars to the cameras used in quality inspections of our food, electronics and pharmaceuticals. There is a responsibility for all shareholders to ensure the best, most efficient systems are moved forward. Progress to this end can be achieved with improved cross industry research and development. While machine vision companies best operate within the comfortable confines of the standards that they are experts in, with the growth of vision into other industries, there’s a two-fold solution: either resolve the challenge of these newer markets with existing tools, or create brand new tools that meet the acceptable standards in that industry.