More than ever before, plastics are being used to manufacture consumer and commercial goods across the world. From medical devices to automotive fasteners, plastics have made their way into nearly every industry. In order to confirm that the plastics used are appropriate for the application, both the raw material and finished goods must undergo quality control testing to ensure critical properties, such as tensile and flexural strength, meet industry standards.
Physical testing of plastics has been around for decades. However, as new polymers and processing techniques are developed, the standards for physical properties have also adapted to the ever-changing landscape. If you’re testing plastics, whether for research and development or quality control purposes, it’s critical to keep up to date on your standards to ensure the most accurate and reliable results.
An update to ASTM D790 was released last year, changing verification requirements. To help illustrate potential compliance issues, let’s take a look at a few of the most common mistakes that occur when testing either the tensile or flexural properties of plastics according to ASTM or ISO.
1. Getting the Correct Verifications
With the latest update to ASTM D790, there were significant changes to the verification requirements for strain measurement. Previously, the standard called for deflectometers to be verified in accordance with ASTM E2309. This standard is typically reserved for the verification of crosshead indicating systems. Now, deflectometers must be verified according to ASTM E83. This change more closely aligns ASTM D790 with ISO 178, though they are still not identical.
So what does the change mean for you? When requesting your yearly verifications, be sure to ask for the appropriate verification type. The different methods require different verification equipment. While ASTM E83 is typically used for extensometers with a defined gage length, ASTM D790 allows for the assumption of 50 mm as the gage length in verification calculations.
Despite the changes to verification requirements, a deflectometer is still not mandatory for testing according to ASTM D790. Crosshead position indication is still a valid means of flexural strain measurement. However, the standard adds an additional note pointing to the procedure for performing a compliance correction. This correction provides a means of eliminating the lost motion and deflection from the system, including the load frame, load cell, and testing fixtures. Advanced testing software packages can provide this calculation, ensuring operators have the most precise strain measurement.
2. Choosing the Right Strain Measurement Device
When calculating strain throughout testing, it’s critical that you report strain from the appropriate device. In addition to verification requirements, standards also have stringent requirements as to how you report the results and what equipment you use.
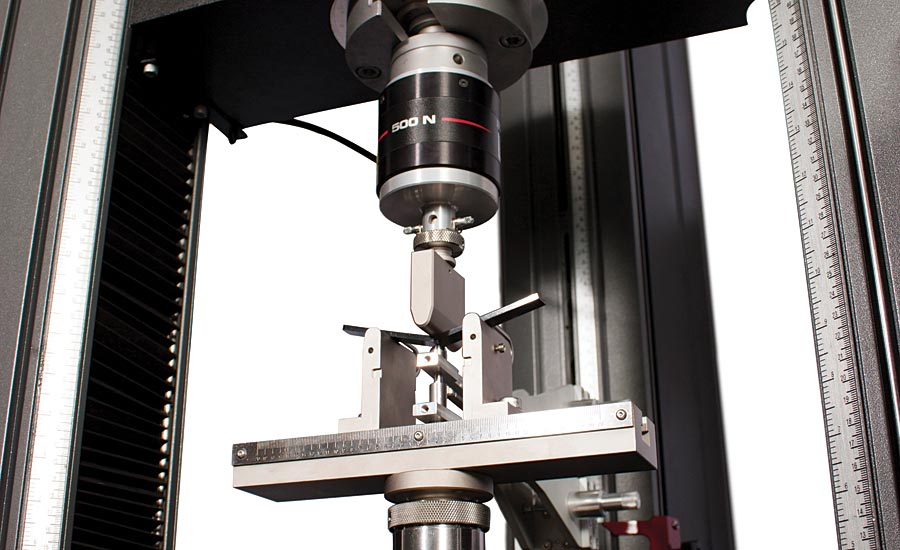
Flexural testing according to ASTM D790 with a deflectometer.
After almost 20 years of calling for a 50 mm gage length, the 2012 update to ISO 527-2 introduced a change that now requires a 75 mm gage length extensometer be used for type 1A specimens, with a 50 mm gage length only being acceptable in quality control applications. The extensometer must conform to be an ISO 9513:1999 class 1 device, resulting in an absolute accuracy requirement of 1.5 microns for a 75 mm gage length. With such high accuracy requirements, reporting the modulus of sub-sized specimens may not be possible due to the unavailability of devices with sufficient accuracy.
The latest version of ASTM D638, however, continues to call for a 50 mm gage length for the most preferred size of test specimen. To make sure you always have an appropriate device on hand, the use of automatic contacting extensometers or non-contacting video extensometers can provide a means of changing the gage length without having to buy a new device. These devices also allow you to test to multiple standards and offer the flexibility to adjust to continual changes in test standards.
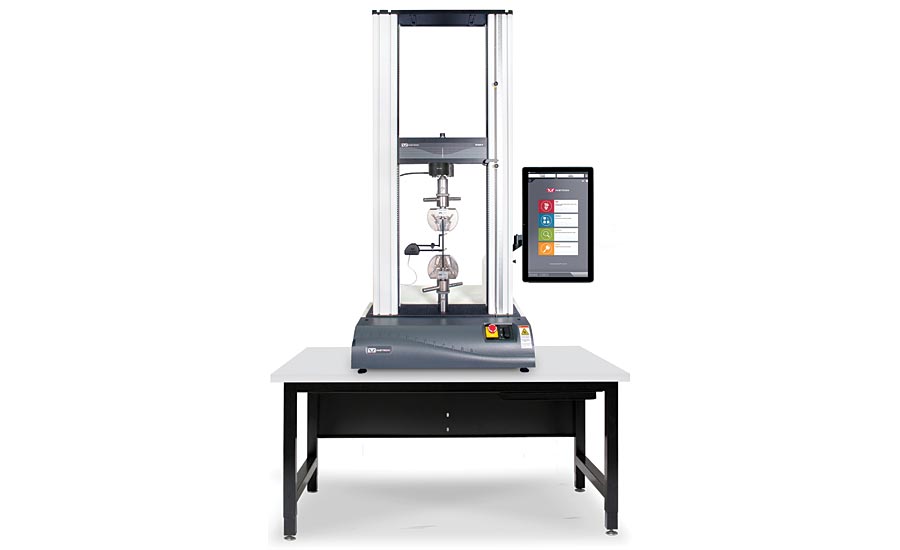
ISO 527-2 tensile testing with a clip-on extensometer.
3. Reporting the Correct Strain at Break
Even after choosing the correct strain device, users must ensure that they report strain appropriately. Oftentimes, when using an advanced extensometer, like one mentioned earlier, the device can be left on through specimen failure without being damaged. While it may be tempting to report strain at break as the strain from the extensometer, both ASTM and ISO require strain at break to be reported as nominal strain. Crosshead and extensometer strain can differ as localized necking may occur outside of the extensometer gage length.
Nominal strain has a slightly different definition depending on which standard you are testing to. For ASTM D638-14, the nominal strain is defined as the change in length based on the original grip separation measured using the crosshead of a system. A common mistake is to calculate nominal strain based on the parallel length of the narrow portion of the specimen, instead of the distance between the grips. This may result in an artificially higher strain at break.
The 2012 update to ISO 527-1/2 introduced an alternative method for determining strain in addition to the one used by ASTM D638, now called Method A in ISO 527. Now, the preferred means for measuring nominal strain is through Method B, which calls for the use of strain measured by the extensometer up until the yield point, and then you switch to crosshead strain for the remainder of the test. The two strains are then added together.
The use of advanced materials testing software can ensure you always have the means to change these calculations, even after testing.
Any departures from the standards can result in unexpected findings at an audit, or unreliable results. While these are just three of the most common sources of non-compliance, many other sources are possible within these two standards. Staying up to date with your equipment suppliers and verification labs can help to highlight ongoing changes and offerings to meet the constantly changing industry requirements.