Quite often in manufacturing, an inspection department is treated primarily as a necessary overhead expense required to assure compliance to customer specifications. Sometimes an inspection department may also be treated as a profit center for compliance to a variety of test protocols dictated by external agencies, or perhaps internal procedures to demonstrate traceability to certain quality standards.
However, for those of us who are practitioners of lean principles, we quite often discover rich sources of opportunities for reducing, if not eliminating, a variety of non-value activities in your inspection processes that ultimately not only improve customer satisfaction but also improve your company profitability by systematically identifying and addressing the eight wastes often encountered.
Having been in the trenches in many companies, I realize that most manufacturing facilities don’t really know how much profit is hidden in the inspection area of their company. Tasked with examining the processes for these “hidden in plain sight” opportunities, start by taking a closer look at the existing in-process and final inspection protocols being used, for things such as:
- the time it takes to verify a part or part family, and the spindle down-time,
- the cost of producing bad parts while the operator waits,
- the excessive movement of parts and personnel,
- the time it takes to build and rebuild fixtures, repair or replace damage
- to probes,
- the cost of machining simple fixtures internally, and the hourly rates for the lab and machine operators,
and so on...
But what if we mapped your inspection processes from beginning to end and systematically identified and addressed most of the eight wastes often encountered in the most critical steps in manufacturing?
While there may be some awareness of the process improvement opportunities, a clear picture of the magnitude of the potential savings may elude us. This article may help to raise that awareness with company owners, business and production managers, process and quality engineers, machine operators and inspectors alike.
Most solutions include the addition of new and more technologically advanced equipment. Whether placed in the metrology lab or in work cells on the shop floor, new machines offer faster and more accurate checking with easier and more robust software. Adding a shop floor CMM or vision system at the spindle or a work cell certainly expands the inspection department, speeding part verification.
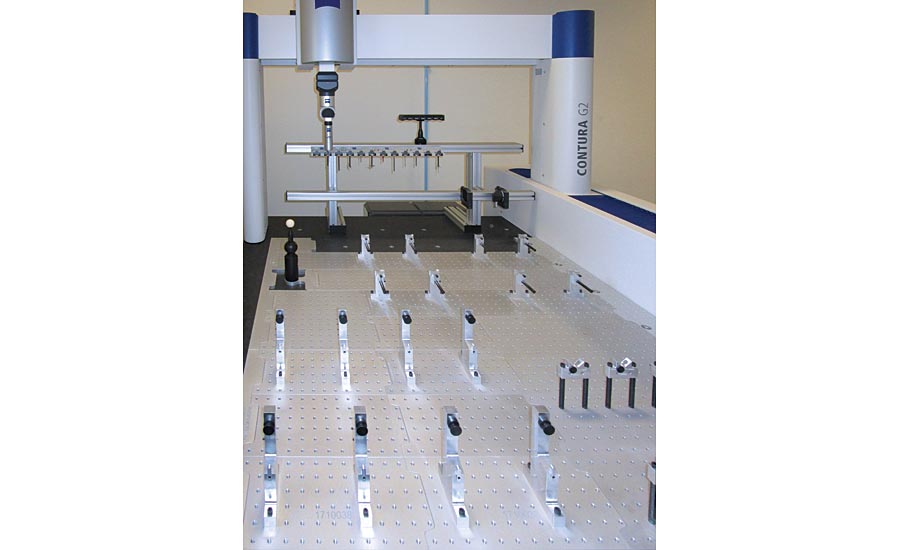
However, the addition of the equipment rarely includes effective fixturing. For example, many manufacturers that I visit forego fixturing due to the expense, lead times, or its functional limitations. In many cases, shops assume that they can make inspection fixtures for less money than purchasing a more readymade solution. This may not be the case with today’s world.
A few years ago I found a fixture system that I could recommend to resolve many of the eight (8) wastes. Let’s examine how a unique fixture solution that is both effective and affordable, can improve customer satisfaction and profitability from spindle to inspection and back again.
The Inspection Arsenal System and the Eight Wastes of Lean
Inspection Arsenal™ is the only Lean universal fixturing system that provides a complete line of tools simple enough to be used by both machine operators and inspectors anywhere in the manufacturing process.
Key features include a modular and magnetically interlocking quick-swap technique available with multiple sized docking rails and fixture plates that adapt to your equipment and unique applications. Many of the unique non-marring work holding components have a trigger-action or air-assist feature for quick-swap of parts. Machine operators and inspectors can quickly and easily be trained to use this simplified fixturing system that can be used across all inspection equipment.
Waste is any step or action in a process that is not required to complete a process (called “non-value added”) successfully. When waste is removed, only the steps that are required (called “value-added”) to deliver a satisfactory product or service to the customer remain in the process. To remember the eight wastes, use the acronym “DOWNTIME.” The inspection step of the process is considered “non-value added” unless a company negotiates reimbursement. Therefore, it is an important area for improvement to save money on jobs running through your company.
Looking at waste generally, there are a number of benefits of a system like Inspection Arsenal™ that blanket most of the eight wastes. This system offers the ability to adapt and reuse existing fixtures, is compatible with existing work holding, helps to create the redundancy of process for a short learning curve and start-up, fixturing can be ordered a-la-carte (as simple as a rail and plate to start).
Defects
Defects are reduced with faster inspection… it’s that simple. When parts are verified quickly operators run parts with confidence. If a spindle is stopped waiting for verification, there is an additional expense that needs to be factored.
Lincoln Tool & Machine of Hudson, MA, provides an example of how they reduce defects and optimize spindle-time.
“We have a bottleneck in our QC department because our new Palletech machine produces parts faster than we can inspect — even with our automated CMMs. The action of these new clamps helps us inspect parts faster — boosting productivity of both machines. We’re able to verify the quality of more parts early in production,” said Scott Ferrecchia, president of Lincoln Tool & Machine.
Overproduction, Inventory, and Extra Processing
Faster inspection can also reduce the need to produce more parts than the customer order requires. Good parts being produced more consistently reduces piece count. Outdated 1-piece grid plates require extra processing — the setup and breakdown of multiple part setups throughout a shift. Plates that can be swapped out quickly offer a new kind of flexibility for multiple setups and quickly exposes the granite to check large bulky parts or to use at datum. Companies who forgo fixturing altogether also face having to recreate time consuming setups with the use of rudimentary tools, such as blocks, tape, glue and putty. Customers do not want to pay for the extra processing time for inspection.
Even when CMMs are upgraded, or added, the Inspection Arsenal™ system can adapt. Simply add a locating rail on the new machines and fixtures can be moved from one machine to another. Fixture plates and work holding also work on or in conjunction with existing plates. Inspectors also find a plate especially designed for the qualifying ball bar allows operators to qualify the machine and move it out of the way to avoid expensive probe hits and free up the entire work envelope.
“We are very pleased with the reduction in set up times it offers us allowing quick changeovers between setup. The product is proving to be a great help. We now make our inspection fixtures to attach directly to the rail which allows us to automate more of our inspection programs as we are starting from known locations,” said Andrew Walmsley, president at Volo Aero MRO, Springfield, MA.
Triangle Manufacturing Company of New Jersey changed the technique used to check a large lot of complex parts using a simplified setup.
“The initial product launch of the implant consisted of 3,120 complex parts requiring 100% inspection. Previously, the time to inspect was nearly one hour per piece. The new leaner process now just takes 35 minutes,” said Ken Gredick, engineering manager of Southern Machine Work of Duncan, OK.
“We do both first part and in process inspections. Our table has to be flexible enough to adapt to a variety of parts and to adjust to part changes in quick notice. Inspection Arsenal’s interlocking system enables us to accomplish this goal. Because of its repeatability we have almost eliminated manual alignments after the initial setup. Its versatility has given us much greater latitude in our setups,” said Don Beasley, owner of Southern Machine Work.
Temco Tool Company understands that expensive inspection tooling is no longer necessary and at his shop rate it’s not cost effective to make fixtures in house.
Waiting
Manufacturers have perfected shop floor fixtures that cut machining time. Now, similar fixturing practices can be accomplished easily in inspection. Implementing a system that includes off-the-shelf, ready-made plates offers the ability to create simple and low-cost dedicated fixtures.
Fixtures can be checked on any inspection equipment that is available. Inspectors or operators can move fixtures from one machine to another, companies can employ CMM palletization features and set large part lot to run lights-out.
Linda Tool of New York makes use of inexpensive dedicated fixtures to swap setups quickly. “We create a simple fixture for each of our long-running jobs that we quickly swap in and out for a much faster inspection process. You’ll see several of our fixtures here — at least 35 unique fixtures — that are marked per the job to make retrieval and setup fast. We inspect the parts during the run. The machine operator will take the fixture, assemble the part and call the program up and inspect them. The learning curve was very fast, as well,” said Shlomo Mordechai, quality engineer.
Culver Tool and Engineering of Plymouth, IN, enhances the investment of their small CMM with quick change-overs and reduction of manual alignments.
“Our machines have a small table, so we keep a lot of fixtures mounted on these plates. They give us the capability to quickly swap fixtures and locate with accuracy so that we don’t have to do another manual alignment. Use of Loc-N-Load™ plates saves us a lot of valuable CMM time,” said Brandon Tanner, CMM programmer.
“Inspection Arsenal™ Loc-N-Load™ plates have been a key component in implementing new equipment. This is an all new implementation for our company so time studies are not complete. Like Brandon said though, the ability to just place a fixture and go has done wonders in taking the burden off of the CMM operator having to do manual alignments for each part we run,” said Deven Berger, continuous improvement manager.
Non-utilized Talent
The simplicity of the system increases the number of employees who can inspect effectively expanding the quality personnel. Operators can verify parts in the work cell on the shop floor. The number of parts inspected per shift increases dramatically.
Kennebec Technologies understands the need to expand quality personnel.
“We are always focused on lean activities and as we expand our use of CMMs on our shop floor this solution will be instrumental in our having a “self serve” inspection process,” said Harvey Smith, VP, operations.
Milwaukee Tool of Wisconsin is standardizing corporate-wide from the U.S. to China to reduce training time, increase the number of inspectors, and speed the overall process.
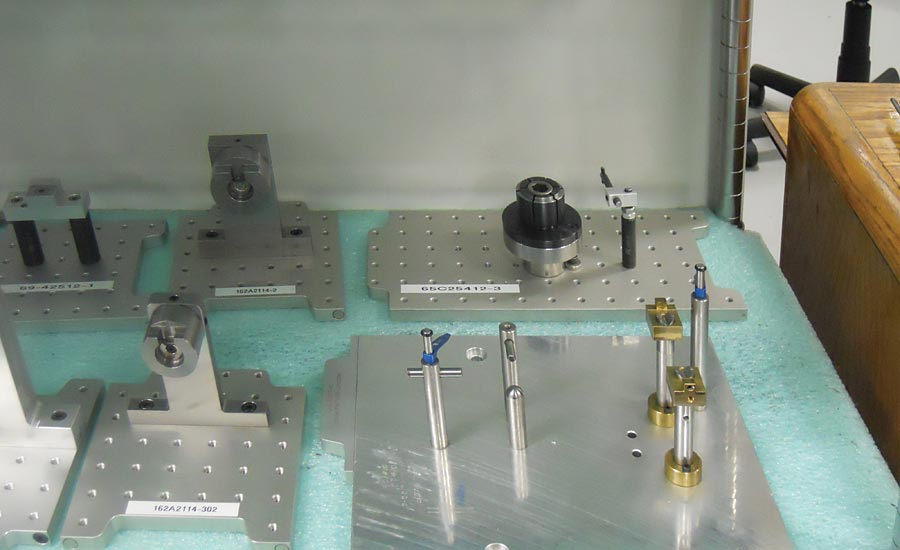
Transportation and Motion
Fixture system creates a standardized product/process across all inspection equipment, company-wide. For large part production the same part can be fixtured on more than one plate so that two or more operators can inspect on multiple CMMs. Fixtures can be run simultaneously.
As a reseller and training facility, Methods Machine Tool Sales of Sudbury, MA, saves time switching gears from training to test inspections for customers.
“We are constantly shuffling between CMM training classes, customer demos, and turnkey inspections. The quick-swap features of Loc-N-Load™ and Open Sight™ fixture systems from Inspection Arsenal™ make moving between these setups quite simple and efficient. Reducing the time it takes to build and break down inspection setups and faster recalibration means more time can be spent teaching about equipment features and programming techniques,” said Tom Oakes, quality applications engineer.
The above experiences provide real world examples of some of the opportunities that can be achieved through the use of a fixturing system when deployed with a conscious effort to mitigate, if not eliminate, the eight (8) wastes commonly found in today’s more complex manufacturing environment, whether on the shop floor or in an inspection department.
Improved customer satisfaction for increased revenue (top line growth)
Think about how your company can differentiate itself from your competitors via operational excellence by utilizing Inspection Arsenal™ and lean disciplines to address your quality (e.g., reducing defects by identifying issues earlier at the source), delivery (e.g., on time delivery, improved cycle times, reduced lead times), and cost (e.g., lower unit costs, lower overhead, improved margins) opportunities.
Improved ROI for increased profits (bottom line performance)
You don’t have to be a big company with deep pockets to make process improvements worthwhile. Smaller job shops with one or two CMMs can significantly improve throughput with a small investment.
“This system drastically reduces inspection setup time and cost. Imagine being able to replace a custom fixture block — one that you pay to have designed, material procured, machined and tested — with a couple of simple Loc-N-Load™ plates that are preset with trigger-action Inspection Arsenal™ work holding. Not only will you save a day or two of lead-time, but the cost will be significantly lower. Parts to be inspected can be set up by the machine operator and walked over to the inspector ready to go,” said Steve Phillips, inventor.
Now that you know that the ability to deploy a Lean process is readily available, take into account the following:
- Shop labor hourly rate
- Metrology lab hourly labor rate
- Value of rejected product in-process
- Value of rejected product in
- final inspection
- Value of rework incurred throughout
- Annual warranty returns in dollars or percentage of revenue
- Penalty for missed deadlines that could lead to a revoked contract
- Value of your reputation if impacted by unsatisfied customers
- Annual cost of quality overall
- Make (design, material, labor, machine time, etc.) versus Buy (purchase) decisions for fixturing costs
- Value of standardized and modular fixturing equipment and processes that minimize personnel training
Would you spend $1,000 to save $100,000?