The push for increased fuel efficiencies has pushed the aerospace industry to develop stronger and lighter materials while simultaneously increasing component longevity. In turn, these new designs, materials, and processes require verification. X-ray diffraction residual stress measurements have been shown to add value to advanced designs and processing of aluminum alloys used by the aerospace community. This article provides a background in effectively using X-ray diffraction to improve the quality of manufactured aluminum alloys in aerospace applications.
Why Measure Stress?
Residual stresses can be beneficial (generally compressive stresses) or harmful (generally tensile stresses) and are fundamental to the useful lifetime of any component, particularly those subjected to fatigue and/or stress corrosion cracking environments. Identifying the types of stress in new designs or processes assist in manufacturing superior products. Luckily, stresses can be changed from harmful to beneficial in the manufacturing process (Noyan and Cohen, “Residual Stress Measurement by Diffraction and Interpretation,” Springer-Velag, New York, 1987).
The X-ray diffraction technique can be a nondestructive method for checking and comparing the stresses in a part. The measurements can be done at the beginning and end of processing as well as after each step. These measurements can also be made using portable equipment on the aircraft before, during, and after prescribed maintenance intervals.
Stress Generation during Processing
The final stress in a component is a compilation of the stresses from the initial material formation through all processing to the final product stage. Stresses must balance in a part at all stages of life. Any time there is plastic flow (plastic deformation), the residual stress state in the part will change. Plastic flow results from anything that is done to the part during manufacturing. Casting, machining, grinding, welding, thermal treatment, and surface enhancement are all examples of manufacturing processes that change the residual stress.
The parameters used at a specific manufacturing stage will also change the resultant stress. For example, abusive and conventional grinding may result in neutral to slightly tensile stresses at the surface (“Residual Stress Measurement by X-Ray Diffraction,” SAE HS-784, 2003, p. 1).
These low surface stresses may not adversely affect the part while in service. The problem is that both grinding scenarios will result in a high tensile stress just beneath the surface. If a high loading stress occurs at the subsurface tensile stress depth, the part may crack due to the loading and residual stress combination exceeding the yield of the material. Also, damage to the surface such as an inadvertent nick from a tool or FOD damage may expose the tensile stresses to the surface and also result in a failure. In aerospace components, a gentle grind is often preferred. The gentle grinding parameters typically will result in compressive stresses at the surface, and a slightly more compressive stress just beneath the surface. These compressive stresses at and just beneath the surface often protect the component during service, and improves the longevity of the part.
Welding during manufacturing can result in tensile stresses, especially at the toe of the weld, or heat affected zone (HAZ). The welding process joins two solid pieces of material by melting material and allowing the molten material to solidify. As the weld solidifies, it tries to shrink, but is restrained by the adjacent solid material. This restraint can result in tensile stresses in the weld or HAZ. When tensile stresses are produced, steps are needed to remove the detrimental stresses and replace them with good compressive stresses. Surface enhancement processes can be used for this transformation.
Surface enhancement processes are generally used during or after manufacturing to improve the residual stress state of an aluminum component. Rivet holes and access openings in bulkheads rely on coldworking processes to prevent cracking. For example, an oversized mandrel will be forced into a rivet hole to put the hole edge and surrounding material into a compressive stress state. After the rivet is installed, the hole will retain compressive stresses limiting crack formation under the rivet edge.
Other surface enhancements such as shot peening, ultrasonic impact treatment and laser shock peening will put compressive stresses in the surface and at varying depths beneath the surface. These processes have been shown to significantly improve component life, especially in fatigue and stress corrosion cracking environments.
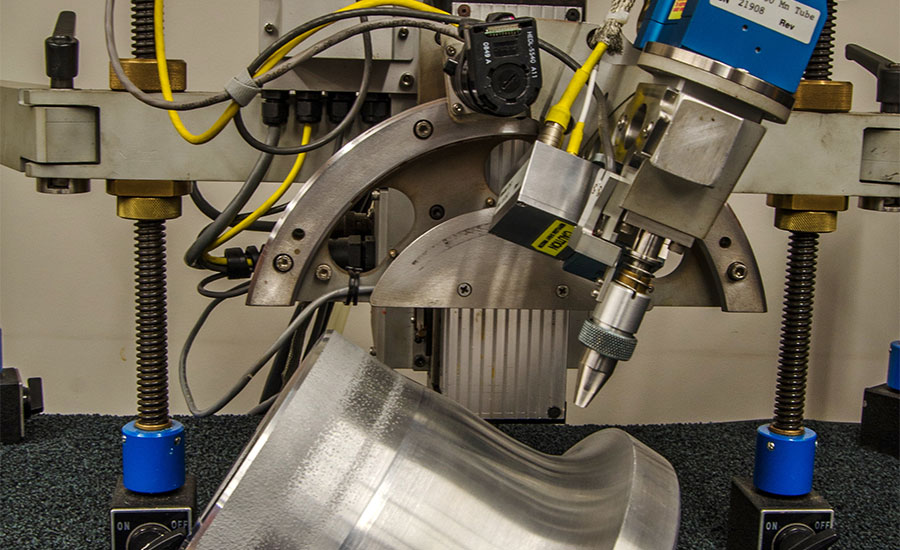
This instrument can quickly and easily measure residual stresses in a variety of materials, including measuring aluminum alloys using copper radiation. Advances in electronics have helped with making smaller, compact X-ray systems. Portable field application systems are now available that can be quickly set up on the manufacturing floor or used on aircraft. Measurement times of seconds to a few minutes are also possible.
Monitoring Stresses during and after the Manufacturing Process
Since X-ray diffraction was first used to measure residual stress (1925), advances in X-ray tubes and detectors have revolutionized the industry. The formerly lengthy, destructive process has been replaced by rapid nondestructive measurements that provide additional microstructural information.
Great strides were made in the technology in the 1970s with the advent and wide-spread use of position-sensitive detectors. These detectors allowed rapid data collection on large and complex geometry parts without sectioning. X-ray diffraction systems could be made compact and portable. X-ray tube technology also advanced to include small, low-powered tubes that could be used safely outside lead-shielded cabinets. Now aircraft parts could be measured at each step of the manufacturing process and before, during, and after service life.
It is now possible to determine at what stage in the manufacturing process that detrimental stresses are occurring. Also, if a problem occurs at a certain manufacturing step that normally produces beneficial stresses, the problem can be detected and corrected quickly. This innovation results in finding potentially defective parts early in the manufacturing process and reduces the time to identify the problem and cost of re-manufacturing the part. Innovative companies monitor stresses in components as a means of knowing when their manufacturing equipment require maintenance or even a change in a cutting tool. Again, the economic impact of identifying a potential problem early in the manufacturing process is immediate and significant.
Another benefit of measuring residual stresses during the manufacturing process is the ability to change the order of certain processes to have the optimal residual stresses in the finished part. Many thermal processes relax or remove stresses from a part. If a thermal process can be done prior to a high-stress operation, the resulting stress might be better for reducing or eliminating warpage in the part.
Finally, intelligent decisions can be made about using surface enhancement processes. If the manufacturing process results in neutral or tensile stresses, beneficial compressive stresses can be introduced in a part. The best surface enhancement treatment can also be selected based on the optimal stress state required. For example, relatively superficial compressive stresses can be induced using conventional shot peening. If compressive stresses are needed deep into the surface, ultrasonic impact treatment or laser shock peening techniques may be required.
Stresses can fade once a part goes into service. Using X-ray diffraction to measure the residual stresses can continue to have a large economic impact on aircraft. Parts that are subjected to high loading stresses can be checked during routine maintenance to see if beneficial stresses are still present. Since loading stresses and residual stresses are additive, parts can be checked in situ to assess the need for repair or replacement of the part. If a part still maintains beneficial stresses, the cost of removing the part from the aircraft, inspecting the part and re-installing the part is now no longer needed. Repaired parts can also be checked to insure beneficial stresses have been maintained.
Advances in Measurement Technology
Advances continue in measuring residual stresses in aluminum components. Newer techniques that use copper radiation (for deeper penetration) show better measurement precision compared to using chromium radiation (TEC Application Note, “Superior Stress Measurements on Aluminum and Its Alloys”). Limitations of X-ray diffraction residual stress measurements include large grain size and preferred grain orientation. Copper X-rays minimize these effects because of their deeper penetration in aluminum. The measurement angle is also higher when using copper radiation, which improves precision and allows measurement of more complex geometry parts.
The Bottom Line
Residual stresses can be controlled in the manufacturing process to produce a superior product that will last even in harsh environments. Technology advances in X-ray diffraction systems make it possible to measure residual stresses during manufacturing and during the service life of a part. Additionally, advances have been made to make superior measurements in aluminum alloys critical to the aerospace industry. Putting beneficial stresses in these parts and detecting potential detrimental stresses during manufacturing produces superior components while reducing costs. Even better, these parts can be monitored during service to improve safety and reliability.