Ensuring the color enhances the design, conveys the right message, and resonates with consumers can make the color selection process challenging but it is only half the battle. Achieving and consistently reproducing the intended color across materials requires expertise and the right tools to aid in the process.
Across design industries, visual checks and balances are often the first step in assessing or measuring color at a basic level. To communicate color across the supply chain, designers should leverage universal color systems and identifiers to specify the color they intend. Manufacturers will then use color references specific to the substrate to visually evaluate how closely the resulting color is to the standard. For example, when assessing textile samples, suppliers will use tools such as color swatch cards to compare against the sample. If the sample is far off from the standard visually, that is an immediate indicator that either the color formulation or the material should be adjusted. While this visual approach provides a basic level of color control that is easy and affordable mostly for simple supply chains, it does not scale up effectively for complex workflows with many participants in various continents making the same product.
Whenever accurate and consistent color is critical, or to simply provide assurances beyond the visual assessment, brands and their suppliers rely on color measurement hardware. One of the most common and widely used color measurement tools in the industry is a spectrophotometer. A spectrophotometer is a device used to capture and objectively evaluate color. Brand owners and designers require their use by the manufacturers to monitor color accuracy during pre-production and production. Measuring color during a production run helps manufacturers manage color in real-time, catching potential errors early so that adjustments can be made before additional resources are wasted.
There are three main types of spectrophotometers and choosing one over another is largely based on the type of surface that needs to be measured. Ranging in size from portable devices to benchtop instruments, each one offers varying functionality intended to ensure color is consistent across materials.
- Single Angle or 0º/45º (or 45º/0º): This device measures light at a fixed 45 degree angle, and is the most common because it closely replicates how the human eye sees color. They are commonly used for measuring color on flat, smooth or matte surfaces, particularly in the printing industry. These devices are mostly used to calibrate monitors and screens, and are used for print and packaging.
- Sphere: Spherical instruments can measure light reflected at all angles to calculate color measurements that closely match what the human eye can see. These instruments are commonly used for measuring color on textured surfaces such as textiles and plastics, as well as shiny or reflective surfaces such as metallic inks and other glossy surfaces.
- Multi-Angle: Multi-angle spectrophotometers evaluate the color of a sample as if it is being moved back and forth. These instruments are best-suited to measure color on specially coated pigments and special effect colors with additives such as mica and pearlescents, commonly used for the automotive industry for the exterior of cars. However, these special effects coatings are also moving more into apparel and footwear.
Measuring color both visually and spectrally throughout the production workflow helps to ensure that colors remain within tolerance and that the end result closely matches the brand design intent. As color can appear differently under various light sources, a critical, yet often overlooked, step in the color measurement process is evaluating color with respect to lighting. As a consumer, have you ever purchased a product based on how it looked on-shelf, only to take the item home and feel dissatisfied because it seemed different than what you saw in the store?
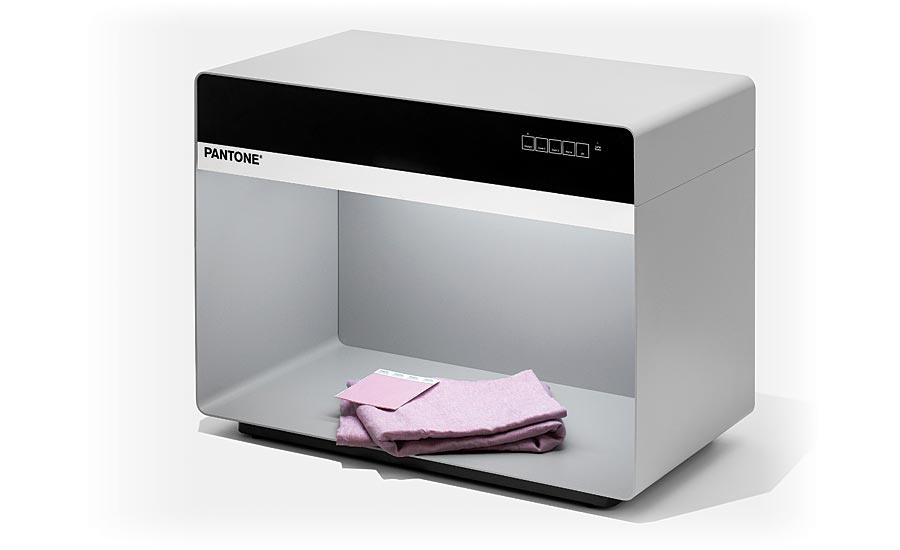
Effectively incorporating proper color measurement and management processes into the workflow helps reduce the amount of time spent on rework and resources.
Comprehensive color measurement processes should include proper evaluation of the material under various light sources. For example, home furnishings manufacturers should anticipate how their products might appear in store or showroom lighting to incite a purchase, as well as in common home lighting to prevent a return. The best way to do this is by using a light booth, which can simulate colors under lighting that represents different environments.
Similar to spectrophotometers, light booths are available in various sizes and with a range of light sources, depending on the materials you are assessing. Some of the more common lamps and use-cases include:
- D65: ideal for reviewing hard and soft goods, textiles and coatings or industrial applications.
- D50 (also known as Daylight): ideal for reviewing color on printed materials or packaging
- “A” Tungsten (also known as Home): ideal for simulating halogen home lighting
- Cool White Fluorescent: ideal for simulating store and office environments
Throughout the design process, time is money. Effectively incorporating proper color measurement and management processes into the workflow helps reduce the amount of time spent on rework and resources. In turn, a more efficient process helps accelerate speed to market, which is a major differentiator in today’s evolving marketplace.