All quality professionals, regardless of educational background and/or experience, will at times find a need to consult their network of resources to get answers to questions, determine how best to collect and analyze data, or resolve different interpretations of a given analysis. Recognizing this need, Quality is launching a new column entitled “Ask the Expert: An Interactive Q&A Section” with topics that come from readers.
In their day to day work activities, both quality and manufacturing professionals are involved in conducting audits; collecting, analyzing, and interpreting data; and preparing a variety of reports and summaries of the data to document product quality. This work is critical to assuring that customers will receive products that meet their quality specifications as well as requirements for quantity, cost and delivery date.
The Context of Suppliers and Customers – The Supply Chain
In the manufacturing world the overarching question from customers centers on product quality requirements: “Can our suppliers deliver products that meet all specifications?”
Customers specify product quality requirements and suppliers must provide evidence that the products they ship actually meet these requirements. Such evidence typically comes from established final inspection activities or from capability analyses of critical product characteristics. Inspection results pertain to the quality of the particular shipment of product while the capability analysis describes not only the quality of the product in the shipment but also the behavior of the process that produced the product.
Ask the Expert will focus first on the various aspects of capability analysis. Product inspections—final or at intermediate steps—will be discussed in subsequent issues.
The Capability Analysis
The capability analysis is a formal, well documented technique that analyzes the particular production process and compares actual product quality with customer specifications for a given product characteristic. There is no lack of resources for conducting a capability analysis. Details can be found in texts, workshop handouts, YouTube videos and other sources easily found through internet searches.
A search for “capability analysis” using Google Chrome returned about 242,000,000 results. Links to quality organizations as well as software companies pop up immediately. These sites address questions including: What is Process Capability? What is the purpose of a process capability study? How to conduct a capability analysis? In addition, software providers make it easy for users to analyze their data and share these answers with customers.
Capability Analysis Examples from Manufacturing
Ignition Solenoid Housings
An automotive company recently changed to a new supplier for ignition solenoid housings. In the contract, the customer requires documentation of part quality for all critical characteristics be included with each shipment. One specific critical quality characteristic is the housing diameter. The supplier includes a capability analysis for the ignition solenoid housing diameter showing that all parts do meet the specifications. The capability analysis report for the diameter of the ignition solenoid housings in the most recent shipment is shown at the top of the previous page.
When the parts in this shipment were used on the production line in the automotive plant, some of the housings did not fit properly and others did not fit at all. Management’s question: “If the quality report shows the parts meet specifications, what happened?” Referring to the capability analysis provided with the shipment,
- How do you as a quality professional explain that the data provided show all parts meet specification?
- What questions should be asked about this analysis to understand how to interpret the information provided?
- How do you answer management’s question to their satisfaction?
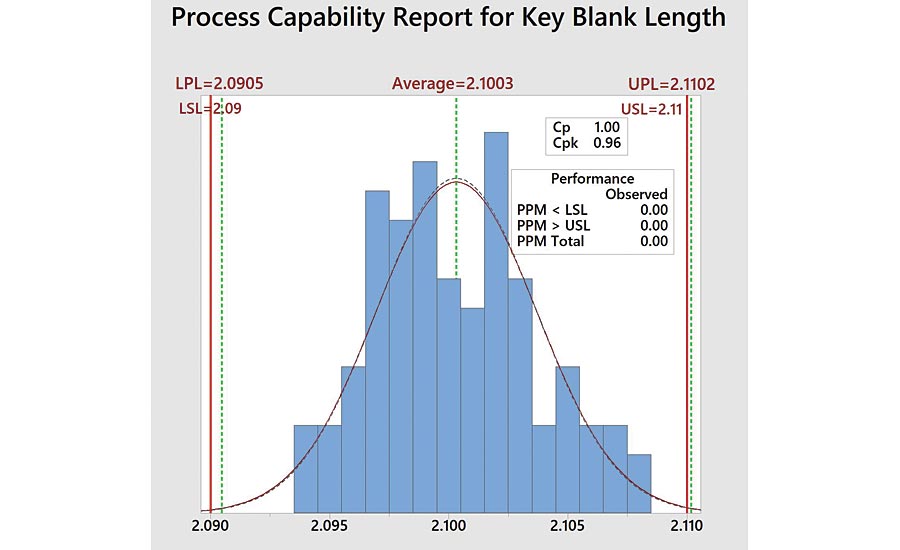
Process Capability Report for Key Blank Length
Length of Key Blanks
A nationwide hardware chain recently started ordering key blanks from a new supplier, Keys R Us, for all of their stores. According to the contract Keys R Us was required to supply evidence of product quality, including a Cpk of 1.33 or greater, with each shipment of keys. Several weeks later, employees in several of the stores noticed that they had difficulty fitting the new key blanks in the equipment to make duplicate keys. Many of the key blanks were too long or too short. Soon after, customers started complaining that their new keys didn’t work.
Even though the cost of the key blanks from Keys R Us was less, the buyer in the corporate purchasing department for the hardware chain reluctantly decided to cancel the business with Keys R Us. In response, Janet, the quality manager for Keys R Us, referred to evidence provided that the key blanks met the specifications for length set by the hardware chain and requested that the contract be reinstated. Her evidence is in the form of a capability analysis shown on this page for key blank length. The buyer set up a meeting with the corporate quality director and a representative of the stores to review the evidence.
- Is the evidence presented in this capability analysis sufficient to say Keys R Us met the customer’s requirements?
- How does the buyer interpret this capability analysis?
- What can be concluded about the length of key blanks from this analysis?
- What should be the corporate quality director’s next step?
Discussion
As a quality or manufacturing professional, what would you do? What additional information would you request? What questions do you have? Please post your answers/comments/ideas to the Quality website.
The next installment is dedicated to the specifics of a capability analysis with explanations about some of the common sticking points and discussing answers provided in this month’s column.