Driven by the need to make parts faster, better, and for less, manufacturers of all sizes are embracing various forms of automation in the quest to lower costs, increase production, and reduce response times. From large manufacturing plants that are run almost entirely by robots to small job shops looking to improve a few key production processes, automation is changing the face of manufacturing in ways that were previously unimaginable. Totally self-operating plants are a long way off for most manufacturers. But more and more are adopting automation on a smaller scale in ways that make sense for their businesses.
For example, CNC machines, a mainstay of the manufacturing industry for decades, have always required highly skilled operators to run them. Thanks to new technologies, many CNCs can now make parts without having an operator present or with only minimal human interaction. Automated CNCs not only lower production costs, they also eliminate waste, improve quality and safety, and speed up turnaround times.
This automation is especially useful in areas where manufacturers struggle to find enough skilled machinists to grow their business. As machines and humans get better at talking to each other via advances in software and the Internet of Things (IoT), production lines will become increasingly automated.
“Lights Out” Manufacturing
Automating CNCs has led to the development of “lights out” manufacturing, the ability to operate 24 hours a day with minimal staff for the second and third shifts. Normally, running extra shifts takes a lot of time to plan and schedule. It also incurs additional labor costs, whether in the form of overtime, extra personnel or both. Automated CNCs make it possible to build parts all night long without needing anyone to clock in or out of the job.
CNC automation generally requires a programmable logic controller (PLC) to run an assembly line, robotic device, or process that requires high reliability. The PLC tells the CNC how to run the process, and sends the job data to the company’s ERP system when the job is complete. Spindle time, number of finished parts, how long it took to make them—it’s all there in the ERP system for quick review.
Manufacturers will still need skilled CNC operators for the more complex parts. But automating production of other CNC parts enables increased production and lower costs without sacrificing quality.
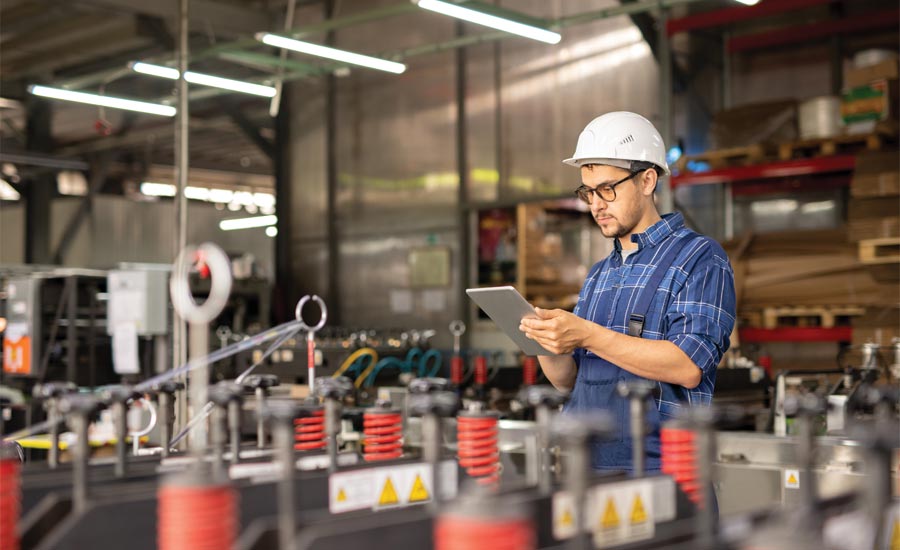
Router Automation with Nesting Software
If you make different parts out of large pieces of material, you know the importance of using nesting to lower costs by making more efficient use of the material. Typically, manufacturers used a third-party nesting software to determine how to cut each piece of material, but they still have to manually enter the data into their ERP system. Automating the router with the nesting program, using a nesting interface, dramatically reduces the time and expense of this critical step. Here’s how it works.
Start by flagging all workcenters used for the nesting interface and send open work order sequences from your ERP to the nesting program. The nesting program then calculates the optimal size and usage for each piece of material, and sends this data back to the ERP system as a flex schedule. This enables the capture of labor time and number of parts for each specific job with only one login. The nesting software also returns the following information related to each job/work order on each nest: labor time, pieces and material usage posted to the job, as well as usable remnants and drops to be inventoried.
Advantages of this router/nesting automation include:
- More efficient material utilization
- Optimized production and labor efficiency
- Increased programming capacity without adding personnel or machinery
- Reduced setup times and tool changes
- Faster migration of geometry, material, quantity, and other part parameters
- Real-time information (based on cycle changes) to operations, material management, engineering and sales departments
Third-Party Software Integration
Today’s ERP systems are remarkably sophisticated and robust, but they can’t do everything. Hence, the continued growth of third-party applications to help manufacturers simplify specific production processes. CAD software offers a good example of how automation can make an already good process even better.
For companies that make complex products, especially those that use sophisticated CNC machines, the design and engineering process has always been one of the more time-consuming steps in the production process. CAD software provided a big step forward by making it quicker and easier to visualize, design, evaluate, modify and share drawings and other specs required to make a part. But it didn’t address the time required to build lengthy bill of materials (BOMs) in the ERP software.
CAD interface software takes the value of CAD software to another level by importing the design data to the ERP system with just a few keystrokes. It then automatically builds the BOM, saving expensive engineering time by eliminating the mistakes that can occur with manual data entry. Having the BOM in the ERP system also gets jobs to the shop floor faster, thereby reducing cycle times.
A similar automation, called a “configurator,” addresses the needs of manufacturers that make products with a wide variety of customizable options. This software allows for highly efficient creation of large BOMs that involve selection of many different options. When entering an order, the options are selected in the configurator and the ERP creates the material list, generates the work order, and schedules production—all in a matter of minutes.
A configurator is a popular automation tool for furniture manufacturers and other companies that allow customers to select options and order online. It shaves time off the order process by creating assemblies of common options and order requests. Once created, an option is available for all future quotes. When used in this manner, a configurator:
- Allows self-service styling, pricing and ordering online
- Enables customers to quickly choose predefined options
- Improves speed and accuracy of quoting and pricing
- Automatically updates pricing throughout the ERP software
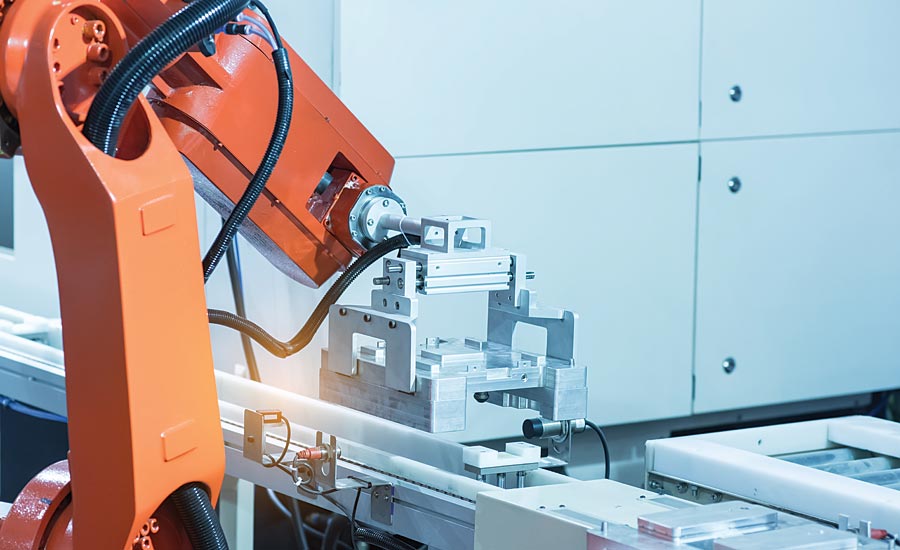
Getting Automation Right
Despite the many benefits, automation should not be deployed as a quick fix for ongoing production problems. A poorly designed process is still a bad process even if you do it faster. Fix the process first, then use automation to make it cheaper and more efficient. Automation also typically requires a significant investment in software and/or machinery. Therefore, it should be approached from both a strategic and operational perspective, with an eye toward how it can improve your business today and in the future.
To get the best return on your investment, start by selecting one problem that slows down your manufacturing process. Define it, then analyze how automation can solve it and identify the expected return on investment. Know what improvements the automation will offer and how it will benefit your business and your customers. To justify the cost, automation should be able to meet current needs while offering the flexibility to adapt to foreseeable future needs.
Most of all, make sure all automation aligns with your business and operational strategies. Every automation should have a specific purpose and desired outcome that supports your long-term business goals. Today’s manufacturing markets move faster all the time. Going forward, automation offers a powerful tool for staying one step ahead of your customers and your competition. Q