When an engineer begins the process of specifying a new machine vision system, they will often think very carefully about the line speed, the optics, and the image processing software. Lighting is often the next consideration because appropriate lighting can significantly reduce software development time and can even be critical to the success or failure of the project. The aim of the lighting will be to project a uniform area of light over the field of view so that a sharp image is obtained and the desired feature can be separated from the background, regardless of any ambient light that may be present. Lighting may have other goals, for example to minimize the effects of motion by strobing the light, or in a more complex implementation lighting may be used to combine data from different lighting schemes.
The lighting controller is frequently only considered towards the end of the project. Frequently, a dedicated machine vision equipment supplier will remind the customer about the lighting controller in a vital “do you want fries with that?” moment. However, the lighting controller is far more than an accompaniment to the main dish. Machine vision experts have learned that a great image is essential for reliable machine vision systems because no amount of software processing can recreate data that is absent at the image sensor. Getting that great image, time after time, needs consistent illumination and accurate, dependable control of that lighting. Lighting equipment vendors will willingly provide consultation on how to properly light an inspection scene and a good one will also understand the different types of lighting controller and be able to guide you to the best choice for your particular application.
In making the choice of lighting controller, an engineer should consider the voltage and power rating of the light or lights, whether the application is pulsed or continuous, and the number of lighting channels required. If the application is pulsed, several additional parameters define the average and peak power that the controller needs to supply, including the pulse frequency and the maximum and minimum pulse widths. If the light is strobed then it can be overdriven to obtain a brighter illumination than the manufacturer’s maximum, but this must be done within safe parameters for the particular light and application to avoid damage to the light. It’s clear that the choice of lighting controller is an important consideration that requires careful consideration. However, before reaching for the calculator, there is one consideration that should come first: whether a voltage drive controller or a current drive controller is the best choice.
Types of Machine Vision Lighting Control
Most machine vision systems use LED illumination with one of three drivers: voltage drive, voltage-drive with pulse width modulation (PWM) or constant-current drive. The earliest LED lighting controllers were voltage drive and this technique can still be adequate for some applications. However, driving an LED light with a voltage source can have significant practical disadvantages. Lighting manufacturers often specify LED lights by supply voltage, but it is the current flowing through the light that dictates the brightness obtained and not the voltage. As LED die temperatures change during start up or with use, the same voltage will result in different brightness levels.
Diagram 1 demonstrates the linear relationship between illuminance and forward current for a typical LED. It shows that the relationship between forward current and voltage is very non-linear and a tiny change in supply voltage will create a large change in the current flowing which creates a big change in brightness. This effect means that voltage drive cannot create precise and accurate adjustments in lighting intensity. Voltage drivers are also susceptible to small fluctuations in system supply voltage which may cause lighting levels to vary significantly.
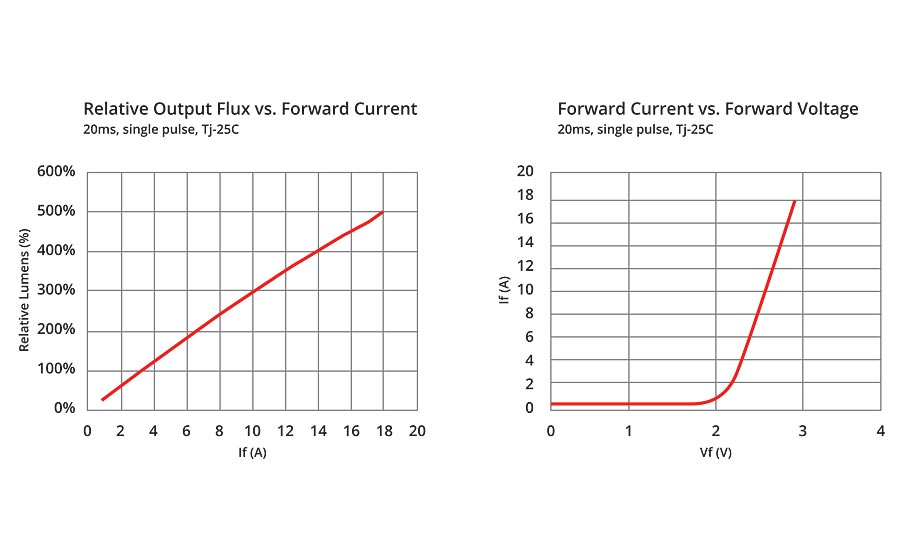
Despite the limitations of voltage drive, some lighting controllers utilize this type of supply to save costs. Because voltage drive cannot directly control lighting brightness, pulse width modulation (PWM) can be used instead. PWM switches the light on and off several times per exposure to obtain an average brightness that is approximately the required level. This can be adequate in some situations, particularly with area scan cameras running on a slow system. The PWM pulses are controlled by an internal clock and to obtain fine control of brightness, a faster internal clock is required. The clock puts a limit on the number of illumination levels that PWM can provide. A typical voltage-drive lighting controller provides 100 intensity steps, whereas a typical current-based controller will typically provide several thousand steps and a much better level of control.
Constant current lighting controllers are designed to directly control illumination intensity with a steady, controllable current flow through the light. Constant current drive is likely to be the most accurate and reliable choice for LED lighting control because the illumination intensity is directly proportional to the current flowing and current drive is not susceptible to variations in power supply. Constant current controllers also have significant benefits with high-speed systems and where a pulsed light is needed.
High-Speed Current Control
An important challenge of lighting control is to create repeatable lighting levels for every exposure. This benefits from accurate, square pulses with rapid rising and falling edges. Sharp pulse edges are difficult to achieve with a voltage drive, particularly when the cable between the lighting controller and the light is long. The result can be that brightness varies between exposures and with time. Constant current lighting controllers are able to utilize higher voltage levels to quickly establish an accurate illumination level without causing EMC interference. This makes constant current drive up to ten times faster than voltage drive.
Accuracy of lighting intensity in PWM systems relies on having a large number of voltage pulses for each exposure. Very high-speed systems may have exposure times in the order of a few microseconds and only a few PWM pulses will occur per exposure. In very fast systems, the exact timing of the PWM cycle relative to the exposure cycle can have a measurable effect on illumination intensity. Diagram 2 shows an example where the timing of the camera exposure and PWM pulses results in the first exposure receiving over 30% more light than the second exposure. A faster internal PWM clock can reduce this effect but these high-speed voltage pulses can cause EMC interference in neighboring systems. More advanced PWM systems may offer the ability to synchronize the PWM cycle with the camera shutter, but this can be difficult to implement, particularly with rolling shutter camera systems.
The Value of Overdrive
An important benefit of modern LED lighting is that LEDs can produce much brighter illumination than the maximum specified by the device manufacturer. This is achieved by driving a brief but high current through the light in a technique known as overdrive. Overdrive will not damage LEDs when heat dissipation within the diodes is carefully managed so that it never exceeds safe levels, and this is done with a careful, real-time calculation based on the LED light rating, the current flowing through the light and the duty cycle. Voltage-based lighting controllers that supply 24V to an LED light cannot create a controllable level of overdrive and those that offer dual voltages suffer from an unpredictable discontinuity in brightness between the two voltage levels. Only constant current controllers can safely and accurately control overdrive.
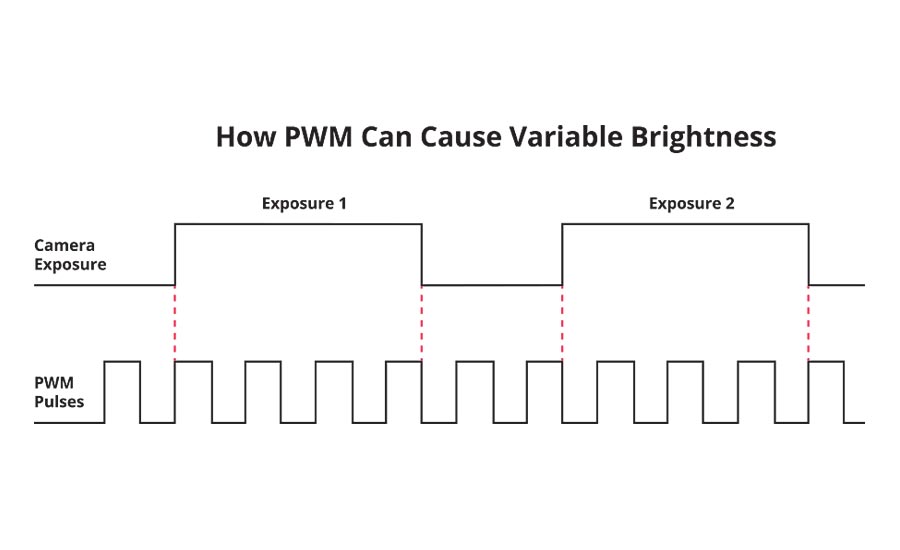
Choosing the Best Lighting Control For Your System
The best choice of lighting controller for a system depends on many factors, including budget, speed of the line and whether it’s wise to build in flexibility for future expansion and change. The reliability and flexibility of current control lighting controllers make them the best choice for many machine vision systems. V&S