The role of metrology is shifting.
This is especially true in modern industrial settings and for increasingly exacting applications. Once perceived as a necessary evil residing in the quality control department validating the integrity of finished parts and components, today metrology is viewed more as an enabling technology that truly adds value. This is increasingly leading to its deeper integration with the overall manufacturing process.
The move to the production floor is additionally accompanied by a paradigm shift from manual metrology solutions to automated solutions, and an overall move away from contact metrology systems to measurement using light, so called optical metrology solutions.
There is no doubt that industry’s perceptions of optical metrology systems have changed in recent years, and its uptake is growing substantially year-on-year. There are obvious reasons for this, key among which is its ability to measure without damaging surfaces or features on sometimes-delicate components. However, optical metrology also stimulates the move to greater automation in manufacturing due to its inherent speed when compared to contact systems, and also the fact that it can quickly undertake full-field measurement rather than focusing on specific part features one at a time.
Faster Time To Data
Ultimately, a key driver for these shifts is a desire for a “faster time to data,” and more importantly, the ability to make decisions as a result of that data faster.
Accelerating industry adoption of optical metrology solutions is in no small part due to the advances in optics, high-resolution sensors, and in the processing software and the hardware on which it runs, meaning that users can almost instantaneously access a clear visual representation of a part, which is easily interpreted, and therefore allows for agile and speedy problem solving. In a world where manufacturers increasingly require greater functionality with minimal cost and effort, 3D optical metrology solutions are critical to competitiveness.
For many manufacturers, quality control is key to cost-effective and efficient manufacturing, and sub-standard metrology solutions have real cost implications. Because of this, optimum quality management systems are key to competitive success.
Not only is the demand for automated, noncontact metrology systems as part of a production line where high frequency part inspection is required, but in addition, there is a growing emphasis on traceability, increased productivity, and global expansion which necessitates making important production decisions from geographically distributed manufacturing facilities.
Because of these demands, industry requires absolutely precise, accurate metrology on all parts produced. 3D optical metrology solutions provide the ability to fulfil such exacting process control requirements.
The days are receding when it was appropriate to collect a sampling from a manufacturing run and wait hours or even days for the data needed to adjust a process. Today through near-line and in-process optical metrology solutions, parts in production can be measured in near real time, building confidence in the quality of the manufacturing process. This ultimately delivers greater efficiencies and reduced failure rates from an optimized process and reduced downtime.
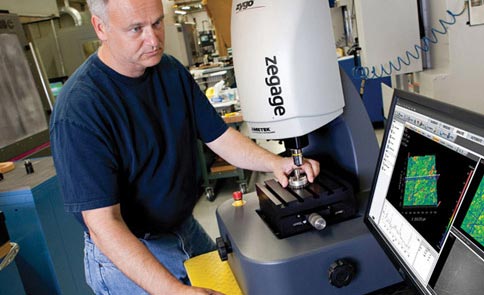
Data Driven Manufacturing
Effectively, what modern optical metrology solutions are supporting or even stimulating is the drive towards so-called smart manufacturing, Industry 4.0, or in other words data-driven manufacturing. As such, they need to evolve to fit in with the vagaries of a production floor setting as opposed to the tightly controlled quality control room environment. The ultimate goal is a product development process that seamlessly produces products that are not just right-first-time, but which exhibit zero failure rates.
Manufacturers want to produce highly innovative, cutting edge parts and components in the shortest possible time, one of the key drivers across all industrial settings being reduced design to market times. This can be stimulated by data driven manufacturing processes using the various data sets used in a product development process as efficiently as possible, these data sets critically including quality control / metrology data. The key is for this metrology data to influence manufacturing data and also to influence data upstream, allowing for optimization of design and machining protocols etc…which constantly update and optimize the overall manufacturing process. Only speedy in-process optical metrology solutions can support such initiatives.
Technology Developments
The journey towards the Industry 4.0 environment is still a work-in-progress, and ultimate success will depend upon the continued evolution of optical metrology solutions.
The key demand from users of optical metrology tools is for greater data density in applications that are often extremely complex. As the shift is towards in-process metrology, measurement is often to be undertaken in extremely difficult environments, which prohibits the use of some more conventional metrology solutions due to vibration or turbulence. In addition, extracting the maximum data possible from each scan is critical to enabling superior metrology on the widest range of samples.
Developments are constantly being made in the design and fabrication of profiler/lens objectives used in optical metrology systems. Profiler objectives are obviously a key influencer on the capability and performance of any solution when it comes to making field of view (FoV) larger, faster, and higher (key to efficiency and agility of in-process metrology solutions), and they also have a significant influence on other issues such as magnification and slope capability.
Vibration resistance, however, is perhaps the most important factor that influences the use of optical metrology in-process. Historically vibration has been one of the biggest challenges to getting robust metrology with 3D optical metrology instruments, vibration being seen as variations in the height surface.
To overcome this, very often the metrology tools had to be placed on heavy robust vibration isolation tables, or in a quiet metrology lab. Solutions today are being developed and evolved that through a combination of hardware and software address this issue by detecting and correcting for vibration during a measurement. This leads to lower measurement noise, more accurate measurements, and more freedom to place the metrology instrument where they are needed.
With the pressure on metrology solutions to maintain the integrity of measurement precision and flexibility in challenging environments, technologies have been developed for vibration robust metrology on optical metrology solutions. In addition, a host of capabilities such as oversampling, high dynamic range scans, and signal processing techniques that maximize the data quality and capability have been developed.
These technologies help to bring the instruments closer to the production floor and facilitate measurement of virtually any surface from the very smooth, to the very rough, and from very flat to highly sloped, stimulating in-process metrology applications.
Only through such technological advancements can optical metrology tools happily reside on the production floor providing data accurate and speedily enough to become a critical driver of Industry 4.0.
Summary
It is vital for industry that the efficiency of optical metrology systems continue to increase metrology in the manufacturing process. Good integrated metrology solutions tangibly boost efficiency gains, cost savings, and manufacturing process flexibility.
The shift towards in-process automated metrology is a key driver behind the uptake of optical metrology tools, but OEMs need to be aware that not all optical measurement solutions are the same. It is vital that any technology solution provider has the sophisticated hardware and software capabilities to maximize the potential for intelligent and in-depth data acquisition and analysis, and provides metrology tools that can fulfil the accuracy and repeatability requirements of today’s cutting edge industrial applications and to assist in the journey towards truly smart manufacturing.