In the middle of the most chaotic, uncertain months of 2020, manufacturers discovered that the perfect antidote was to double down on quality and reliable delivery—turning to their enterprise resource planning (ERP) systems for the timely insights needed to navigate rapid changes in market demand and resources across their supply chains. The increased agility has not only enabled business continuity; it also has served as a competitive advantage in attracting and retaining customers. And it has set the stage for manufacturers’ growth in 2021.
“For us, it’s simple: can our ERP system help us keep our word to customers and retain their trust? That’s the goal of quality and business continuity,” one manufacturing founder and CEO recently told me, We have to do everything we can to keep customers’ trust, and ERP systems make that happen by having a view across every production process and how it impacts our financials.”
Notably, ERP systems are not being used in isolation. The past year has seen an acceleration in manufacturers adopting non-compliance/corrective action (NC/CA), corrective and preventative action (CAPA), and advanced product quality planning (APQP) APQP techniques while sharpening their focus on statistical process control (SPC), inbound quality management, and supplier quality management. ERP systems provide the guardrails that give manufacturers the data they need to trade off supplier quality, the optimal mix of machinery, and right worker teams to deliver excellent quality, gauge calibration and compliance to customer and industry quality standards, and more.
Let’s look at how ERP systems are helping to ensure business continuity through quality, as well as review best practices for aligning quality with business continuity.
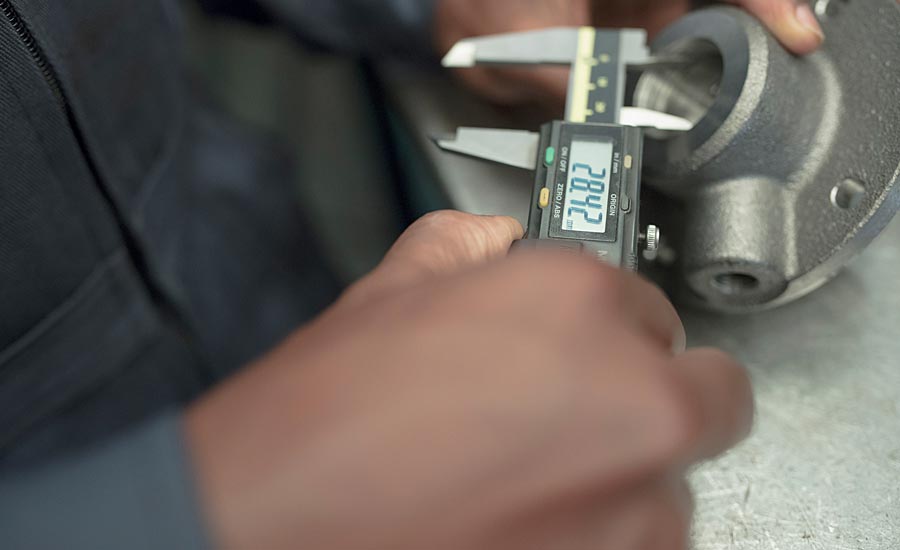
A measurement check is performed during the manufacturing process. Source: DELMIAworks
Using ERP Systems To Ensure Better Business Continuity Through Quality
At some of the fastest growing manufacturers, ERP typically works in concert with a manufacturing execution system (MES) to enable supplier quality management, production quality management, and real-time manufacturing process and production monitoring, along with financial reporting. The real time insights and ability to drill down into data are empowering these companies to reliably meet customers’ demands—even during rapidly changing market conditions.
As the COO of a plastics extrusion manufacturer noted, “ERP systems and the quality management metrics they deliver along with real-time process and production monitoring mean our word is good as gold. We keep more commitments when we use ERP to manage quality.”
Here are four key areas where ERP systems help manufacturers to delve beyond the first level of analysis across their manufacturing operations and understand how decisions affect product quality and related performance metrics.
Track and traceability. The consensus among manufacturers I have interviewed is that track and traceability in their ERP systems helped stabilize quality and reduce operating costs while providing much-needed compliance data required to meet a range of industry standards and government regulations. For executives at these companies, deploying track and traceability proved to be one of the most effective strategies in 2020 that they have carried into this year.
RMA Insights. Return material authorizations (RMAs) are a direct measure of product quality and a product’s nonconformance to customers’ specifications and requirements. ERP system databases with quality management modules can do real-time Pareto Analysis and vary the sampling frequency of data easily to uncover sources of RMA variation problems. For example, sometimes RMA rates vary drastically even when product quality remains consistently high. Using an ERP system to troubleshoot the issue often finds that a new customer is using the product in an edge case—or an application area that is tangential to its core designed use.
Understanding CAPA events. CAPA, also known as a corrective action request (CAR), is a measure of how well the initial engineering specifications combined with build instructions on the shop floor reflect customer requirements. ERP systems that have an integrated data platform can provide these metrics in real-time and at whatever frequency manufacturing quality engineers need.
SQA rate. The supplier quality assurance (SQA) rate is an excellent indicator of how effective SQA systems and processes are in a manufacturer, and SQA metrics are an integral part of any ERP system’s quality management reporting system. The goal of an SQA is to help manufacturers provide suppliers with an accurate, reliable framework for delivering the highest quality raw materials, components, subassemblies and assemblies used in production. Many manufacturers evaluate this metric every 90 days with all suppliers to understand relative quality levels by product and sourcing area.
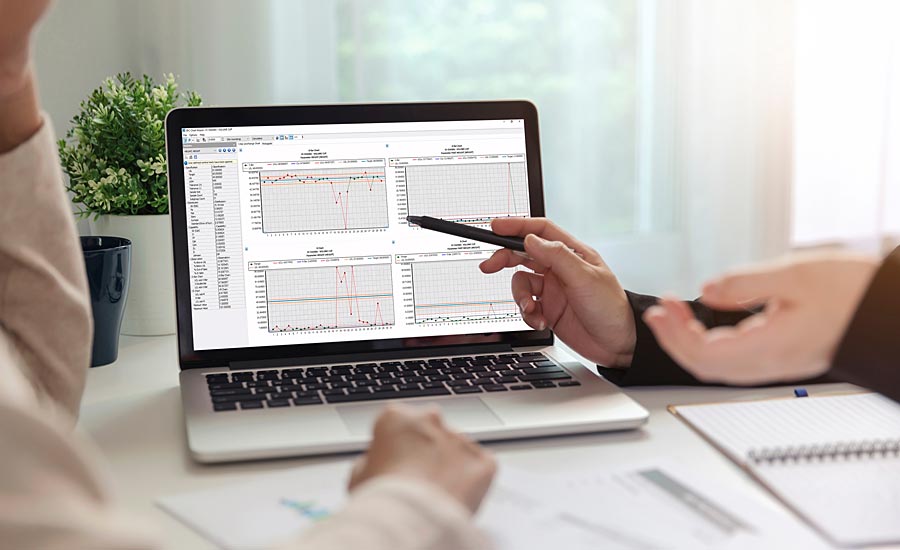
Statistical process control (SPC) charts. Source: DELMIAworks
Best Practices For Aligning Quality With Business Continuity
In 2020, all manufacturers had to take a hard line on anything that didn’t contribute to quality or keep their business operations running so they could accept orders and fulfill them. Throughout the year and into 2021, four best practices have emerged to address these priorities.
Using quality management and compliance to guide business continuity. All the manufacturers I have spoken with agree that the practice of relying on quality management and compliance to guide their business continuity planning has provided the perfect training to meet rigorous Defense Production Act (DPA) requirements for personal protective equipment (PPE), COVID-19 testing kits, and vaccine vials and syringes. The more integrated quality, supply chain management, production scheduling, logistics, finance and service are, the more effective a given manufacturer's contributions will be to the program.
Increasing collaboration with customers. Competing on price in 2020 was a losing strategy, while higher quality guarantees and committed-to delivery dates were considered the two most highly valued services among manufacturing customers. The most successful manufacturers have also been achieving greater compliance by anticipating further customer-driven audit needs.
Understanding the cost of good quality. Manufacturers increasingly recognize the value of having insights into how much the cost of good quality contributes to higher margin and recurring customer purchases, particularly when viewed against the costs of bad quality in the form of sales and revenue declines. When financial reporting, quality management, compliance, supplier quality, MES and ERP are all part of the same platform, tracking the cost of good versus bad quality becomes an automated workflow.
Following a roadmap to value. When management teams build business continuity on quality first, they are better equipped to define a roadmap to value company-wide. This makes it possible to see where and how product quality is making an impact on revenue, costs and financial performance. Following is a diagram of what such a road to value looks like.
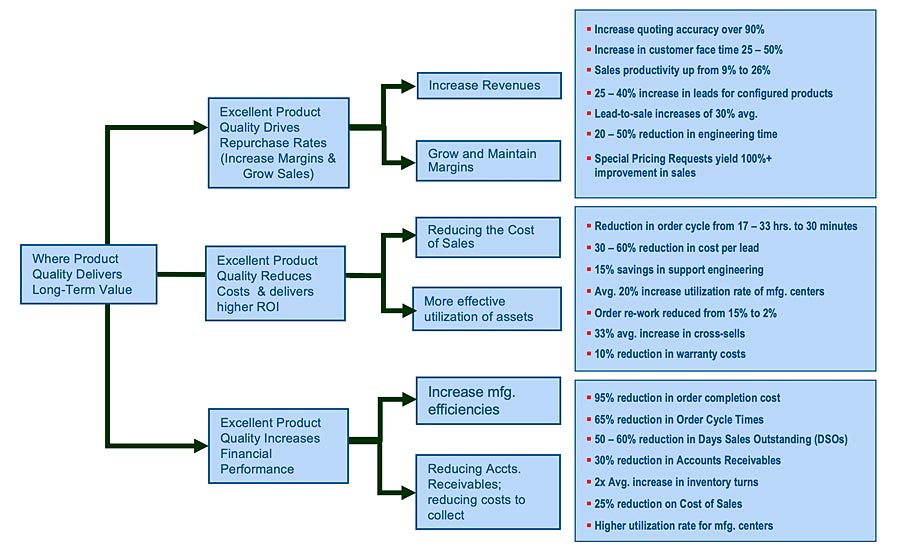
Roadmap to value. Sources: DELMIAworks Research, LWC Research
*Click the image to see a larger version
Quality makes the continuous operation of a business possible, and quantifying its revenue contributions in a roadmap to value is the cornerstone of business continuity strategies today. When business continuity is based on revenue alone, or worse, simply on forecasts, there is too much room for variation in performance. By leveraging their ERP systems to help take control of quality—and sell on its value first, including commitments to quality levels, delivery dates, and custom configurations—manufacturers can compete on by becoming customers’ trusted partners in navigating uncertain times.