Why test for top-load strength?
Packaging for consumable goods has several purposes. Not only must it have an optimal design and attractive looks to grab the attention of a prospective purchaser, but it must also provide ample protection for the product inside. Plastic, metal and glass bottles, aluminum cans, and cardboard cartons must all stand up to the forces encountered during handling, transportation, and storage. Manufacturers of both flexible and rigid packaging, which are fitted with closures, face the additional challenge of ensuring that their containers have sufficient strength to withstand the loads applied during the capping process.
Key to quantifying the design and quality of containers is measuring resistance to top-loading. Top-load testing – also known as crush strength, axial strength or compressive strength – evaluates a packaging material’s structural resistance under a compressive load, usually to the point of deformation or collapse of the packaging. Manufacturers and their customers use top-load testing to ensure that they have the right balance between ensuring packaging integrity and eliminating any excess material – a process known as “downgauging” or “light-weighting.” Downgauging has high environmental and business significance, since packaging soon becomes waste material and, when produced in huge volumes, it is clear that excess material has powerful cost ramifications.
Compliance with environmental regulations is a serious business concern and current regulations enforce strict limitations on the volume of primary resource material that can be used in single-use containers. Several international standards (e.g., ASTM D2659 and DIN 55440) and industry guidelines (e.g., PTC002 by the ISBT) clearly define top-load testing methods that can be followed to enable optimal downgauging of containers. Carrying out testing in accordance with these methods requires accurate top-load testing equipment to reliably determine the performance limitations of packaging materials.
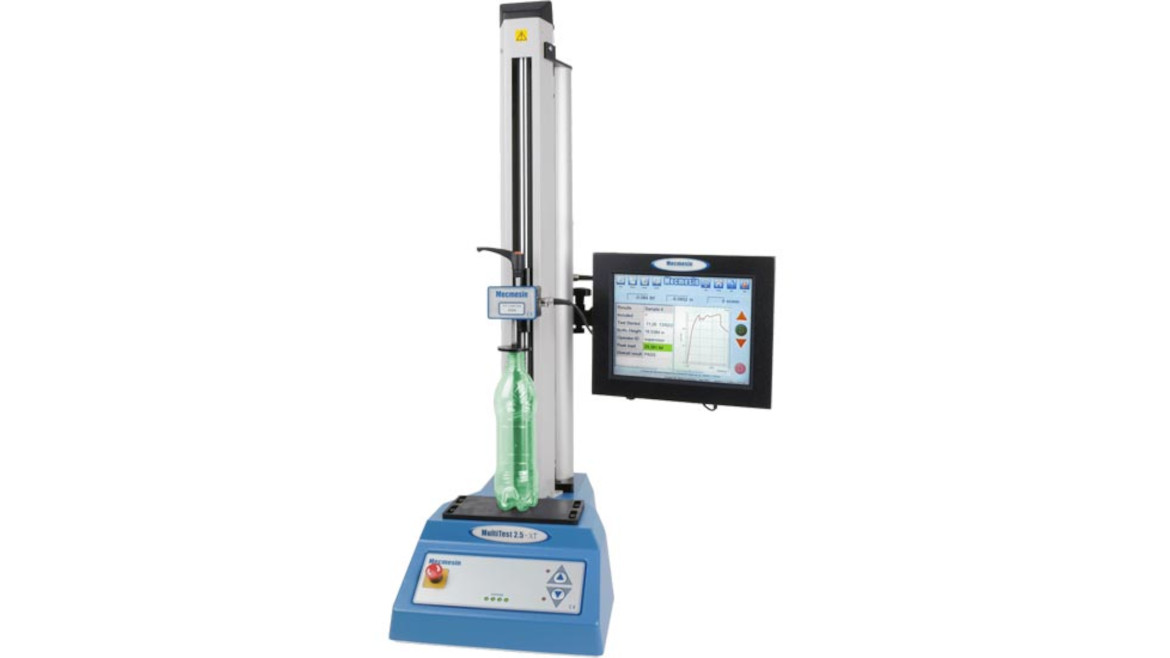
Single-column, Software-driven Materials Tester. Image source: PPT Group (Click on the image to enlarge.)
Industries that Benefit from Top-Load Testing
Beverage Industry
Plastic bottles used for drinks are commonly made from PET and PE (HDPE and LDPE) and are regulated by strict environmental standards limiting use of material. Milk and juice bottles tend to be made from HDPE due to it being widely recyclable and lower cost to produce. Still and carbonated beverages tend to come in PET bottles because the material is both strong and light. For standards compliance and business economy, both volume of original material and the number of production line rejects must be minimized.
Production of PET bottles is a long and involved process that begins with the bottle as a 4” pre-form.
These tiny half-formed bottles are blow molded then sized and shaped. After cooling they are placed on the filling line, where they are then capped and finally boxed. A capping machine pushes the cap down onto the bottle with a significant axial load before it twists the cap to tighten. Testing that PET bottles can withstand this axial load without collapsing and spilling all their contents onto a fast-moving production line is an essential quality-control check.
PET bottles tend to exhibit weak spots around their base and/or neck and deformation typically occurs at these areas when under compression. Not only does top-load testing reduce the possibility of “light-weighted” PET bottles experiencing crush failure during capping, but it also serves to verify the strength characteristics required for the onward journey of the bottle during the handling and storage phases of the supply chain.
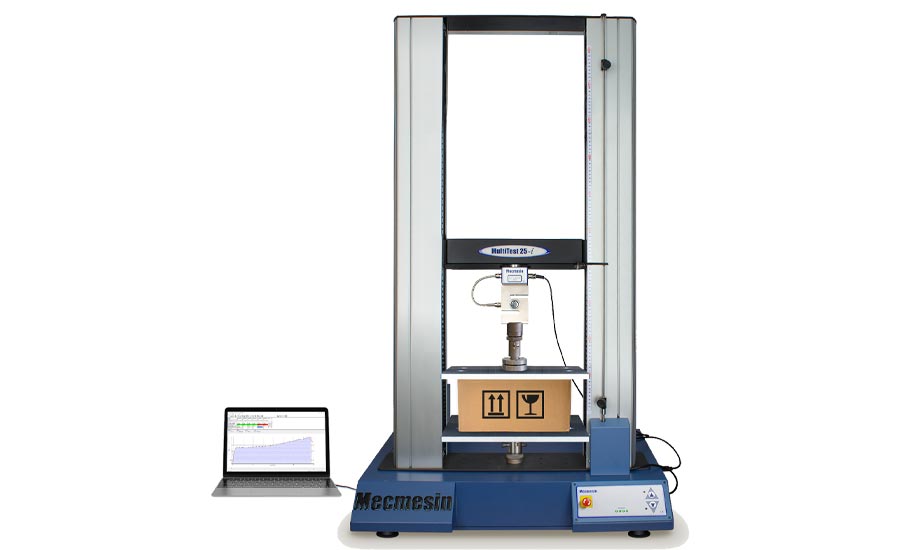
Twin-column, Software-driven Materials Tester. Image source: PPT Group (Click on the image to enlarge.)
Packaging Industry
The range of materials used in general packaging is extremely broad and covers many varieties of plastics, cardboard, and metal. Consider the material used to create a basic cookie carton – at the very least, manufacturers require certainty of the cardboard quality so that product will reach consumer in saleable form. First, material structure must support all processes, which include production, palletization, and stretch wrapping. Second, handling activities are critical considerations – possibility of material distortion is high during pallet stacking and storage. Other factors include humidity resistance and shelf-life longevity.
The design of a cookie carton will consider such environmental conditions. Realizing economy of raw materials, determining material limitations, ascertaining packaging strength, and protecting product are the essential goals of packaging industry processes, where achievement of greatest consistency in quality and reliability is of critical importance.
That’s where top-load testing comes in - it is performed on production shop floors to measure the structural strength and stability of the assembled carton. Operators perform regular spot-checks at line-side, assessing multiple samples per batch to obtain accurate measurements with minimal impact on production throughput.
If more comprehensive results are required, further analytical tests can be performed in QC laboratories. For most applications, a stand-alone, touchscreen top-load tester is ideal. These testers provide a robust platform for accurate testing of samples in environments unsuitable for computer usage, such as the production shop floor. Computer-controlled testers, on the other hand, are most commonly used for more detailed tests in laboratory environments.
Choosing a Test System
The business advantages of top-load testing are already clear, but the choice of test system can be a challenge. Testing standards stipulate top-loading should be applied under controlled conditions at a fixed speed, so this requires a motor-driven test system not a manual tester.
If the tester is located in a production area where the use of a PC is not ideal, it is often better to use a touchscreen-driven top-load tester. If more complex test routines in the QC or R&D labs are required, then a PC-driven tester is preferable.
How the tester works
Touchscreen-controlled top-load testers are suited to production floor usage, where they facilitate improved control over the molding process with minimal disruption to daily manufacturing flow, saving both time and cost.
To perform a top-load test, a bottle, taken from a batch at regular intervals from each production line, is placed on the base of the test stand. The test method is selected using the five icons on the touchscreen’s console. When the ‘start’ button on the touch screen is pressed, the crosshead descends at a fixed speed. When the top of the sample is reached, a touch is registered, the free height of the bottle is captured, and compression begins. Load is applied until deformation is detected, at which point the maximum force (top-load strength) is captured.
The results of the test appear on the touch screen in tabular or graphic format, peak load and free height is recorded, and a color-coded “pass” or “fail” result is reported. When the test finishes, the crosshead returns to its home position, ready for the next test. Results can be stored internally, on the touch screen’s hard drive, or exported to a statistical process control (SPC) or other quality monitoring systems.
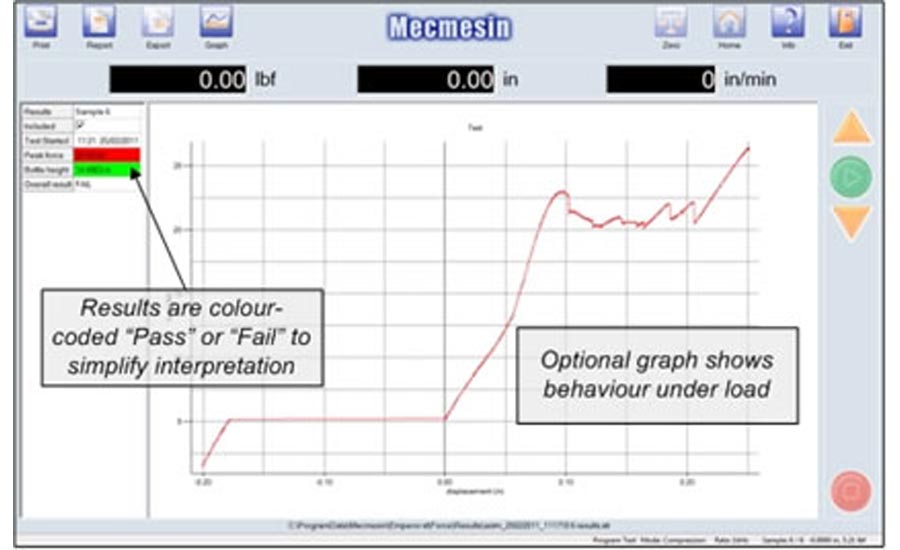
Computer-controlled systems are the superior option for advanced test measurement. Fully programmable, these systems are operated from a computer running software. Test results are displayed graphically in real-time and enable automatic calculations to be performed on top-load test parameters. Image source: PPT Group (Click on the image to enlarge.)
Accessories
Compression plates are the most common contact fixtures used in top-load testing and it is important to select the correct plate for your application.
Vented plates are used for testing empty containers as they allow any air trapped inside the container to be released. Vented plates with nose cones are useful to help center the bottle by inserting the nose cone inside the opening. Flat compression plates with self-adjustment are used for testing filled containers and boxes, where keeping the plate parallel to the container across its whole surface is critical.
Implementing a top-load tester as part of the quality control regime is a cost-effective way for packaging manufacturers to ensure their products are resilient to the rigors of production, distribution, and storage. At the same time, cost savings can be achieved through top-load testing by identifying where lower volumes of material can provide sufficient strength. Reduction of material volume, lower reject counts, and maintenance and improvement of batch consistency all become achievable with effective top-load testing.