Artificial Intelligence, or AI, is being adopted across industries to harness the power of data and use it to make more informed decisions. We’ve previously written about how AI software enables more accurate quality inspection, and in this article, we’ll pick up on how you can identify opportunities for AI in your machine vision applications.
Business Requirements For AI Systems
Managing Expectations
AI methods have specific use cases. They are not one size fits all solutions, or “magic bullets” to solve all our problems. Some applications are better for traditional computer vision, some may need both, while others may only need AI. AI systems are expensive – both in terms of cost and the resources needed upfront. Open-source tools require a lot of development time, while external tools tend to be expensive. Also, a GPU is generally required to achieve sufficient performance on a system. Many manufacturers do not typically have a GPU or equivalent processing capability on the floor. Thus, it is important to identify applications that are a good fit for AI with a strong business need upfront.
Importance Of A Strong Vision Setup
Before getting into AI, it is recommended to have a strong foundation in the vision system setup. Although, it is less critical with AI because it can typically deal with poorer conditions than a traditional system. All regular machine vision system rules apply here – good lighting, camera resolution, focal length, etc. If any of these factors are not up to par, it may be worth going back and addressing these first before diving into AI. Ensuring a strong vision system setup is encouraged for best results.
Referencing Human Performance
AI systems are most successful where human performance is strong. Once the system is set up well, and an operator can easily identify/ classify images with their eye, then we can determine if it is a good fit for AI. However, if the human performance is insufficient, then the AI model will likely perform poorly. We can use a human’s performance as a reference point for what the AI model can achieve. That means if an operator only identifies images correctly 70% of the time, it is unlikely for the AI to perform a lot better than this. Thus, if human performance is not good enough for an application, we should first address that performance, and bring it up to an acceptable level. Once the desired performance is achieved by an operator, we can consider AI.
Time And Resources
Considerable effort is needed to gather images and train a model. Often gathering quality images is the hardest part, as many manufacturers have very low defect volumes. It can be hard to train a model with defective parts if they are lacking data. A training tool is helpful that provides pre-trained models which require fewer samples for training. Training is an iterative process spanning several steps to find out the ideal parameters to get a model to run. It often takes time and experimentation to optimize a model. Additionally, if new data arises in the field, the model will need to be trained and deployed again. Astrocyte saves time here with continual learning, as it allows models to learn in the field even after being deployed.
What To Look For In An Application
Generally, we are looking for problems that are difficult or impossible to solve with traditional image processing.
Sample Applications:
One sample application of AI in machine vision is for final assembly inspection, another is printed circuit board, or PCB, inspection.
Background
Final inspection of parts/products or assemblies is commonly done by operators or traditional machine vision systems (or both). Here we highlight a Teledyne camera as a sample product. A final inspection may look for bent pins, scratches on the surface, connectors in the right place, the sticker alignment, text printed correctly, the distance between mechanics, and more. Basically, we need to find any abnormalities that occurred during the build. The problem here is that the list of criteria to look for quickly becomes long. It is difficult to handle all the corner cases with a traditional rule-based system and tough to train new operators.
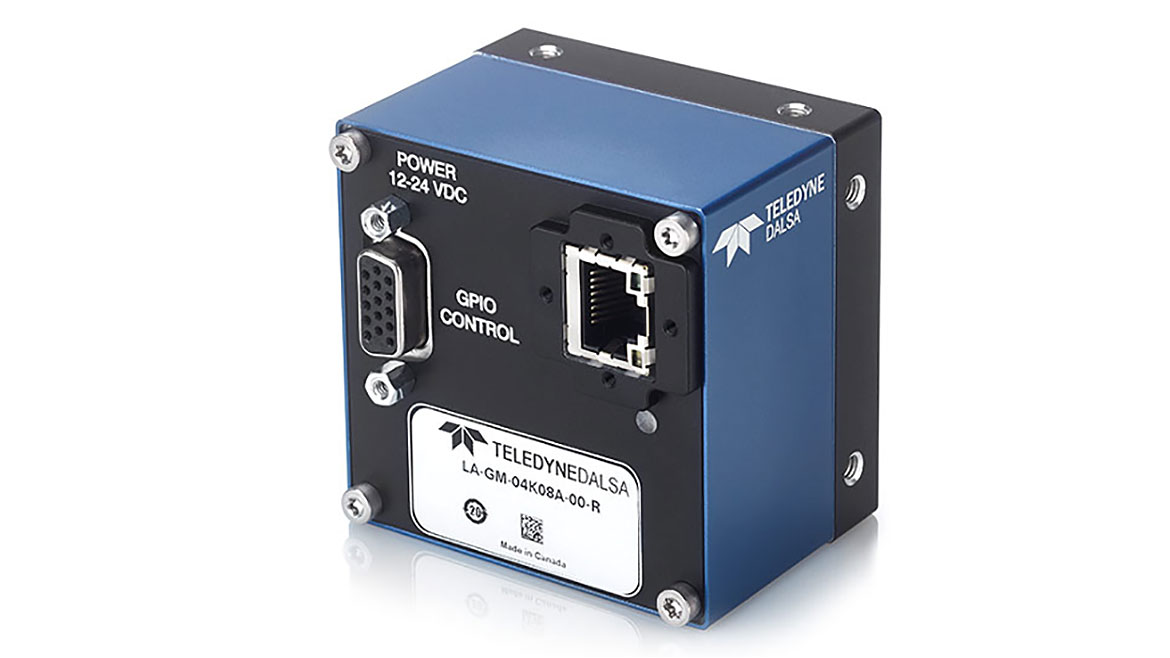
Final Assembly Inspection
Why AI?
There are often too many rules to identify what is “passed.” This makes it difficult for traditional machine vision systems to perform well. Another option, manual inspection is time-consuming for many companies, and it is tough for new operators to make some ambiguous calls. Often the traditional rule-based system does not have adequate performance and manufacturers rely on an operator’s judgment to assist. There may be varying light conditions, and high variation in defect location, shape, and texture. Usually, only a simple “good/bad” qualitative output is all that is required. However, this can also be combined with traditional rule-based algorithms if needed.
Benefits
With AI the setup is much easier. After a good number of images are gathered to train the model, there is usually a lot less development effort to get a system going than a rule-based system (especially with an AI tool). The inspection speed is usually much faster with an adequate system (usually with a GPU), on the order of milliseconds to inspect. An AI system should also perform more reliably than a human if given good data and is a good way to standardize inspection procedures. It can reduce human error as it is usually trained from data provided by several operators. This helps mitigate human bias or fatigue that may arise from a single operator. For this example, AI could help a manufacturer to reduce out-of-box failures and improve inspection quality and throughput.
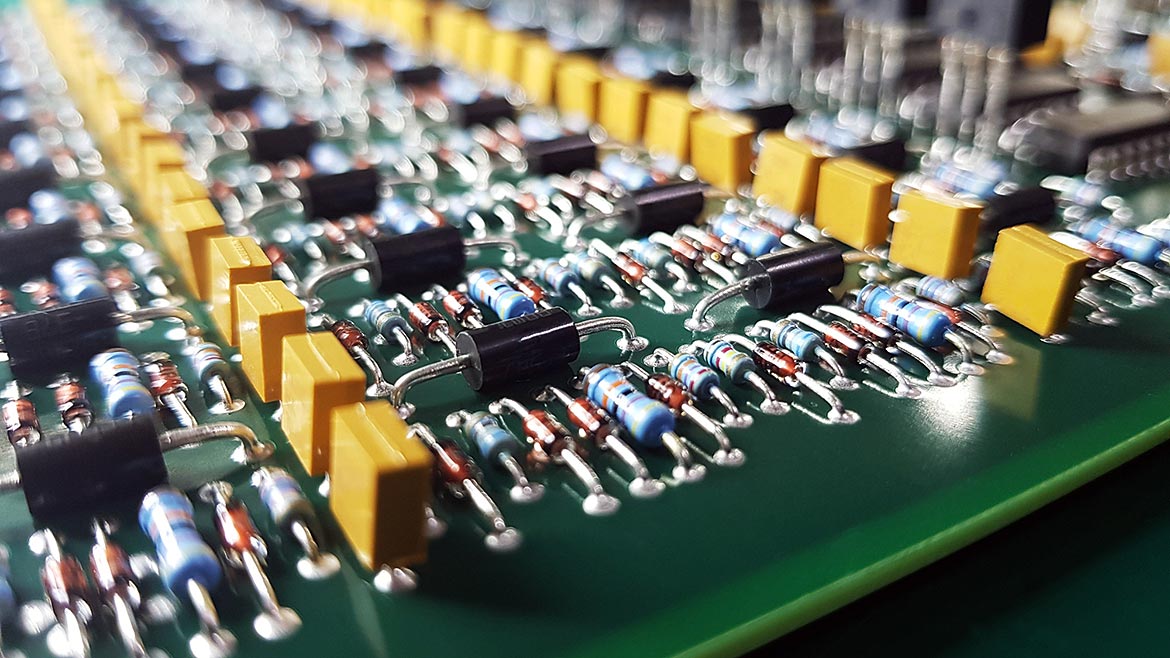
Source: PJ_joe / iStock / Getty Images Plus via Getty Images.
PCB Inspection:
Background
PCB manufacturers need to inspect their circuit boards for any kind of defects. This could be bad solder joints, shorts, or several other anomalies. Typically, they use AOI (Automated Optical Inspection) machines. However, it is difficult to handle all the edge cases as there are so many variations of defects. Often the performance of a rule-based system is not accurate enough, and manufacturers bring in operators for manual inspection, which is time-consuming and expensive.
Why AI?
The traditional AOI system has a hard time identifying the defects. It either overshoots or undershoots the performance, resulting in defective PCBs passing or good ones failing. Similar to the other case, there are often too many rules to identify a “good board.” Depending on the application, AI can also be used here to classify defects (i.e., short, open circuit, wrong component, solder defects, etc.) that may vary greatly in size and shape.
Benefits
With AI, the manufacturers get improved accuracy and better quality of inspection. This can help to reduce the number of defective PCBs passing inspection. They can also save on time and labor costs from any human-assisted inspection and increase their throughput by automating what an operator takes much longer to do.