Color is a determining factor in product acceptance or rejection. When a product doesn’t meet color specifications, it leads to rework, wasted materials, added costs, delays, and impatient customers. With a supply chain already stressed and materials costs rising and in short supply, manufacturers can’t risk incorrect color.
If your production color has started to drift or is causing problems, it might be time to evaluate your color workflow. Simple changes to how you use color measurement technology and the right training can significantly impact quality control and your bottom line.
Here are seven questions every quality control manager should be asking:
- Are you still using physical color standards? Traditional color workflows leverage physical standards for color communication and quality control. However, physical standards can fade and become dirty or damaged over time. It is hard to meet color requirements when comparing against an incorrect standard. A digital color standard removes subjectivity from color communication and sets clear expectations to minimize errors. A digital standard can include spectral data, tolerance data, measurement size and mode, device conditions, illuminant information, and much more in one file. This ensures everyone across the manufacturing process and supply chain is working with the same approved color standard. Digital standards also integrate with formulation and quality control software to help you begin color formulation immediately and quickly verify color accuracy throughout production.
- Are you taking advantage of ALL features in formulation software? Whether you work with inks, colorants, pigments, dyes, or resins, the wrong color formulation can easily lead to thousands of dollars in wasted material and time. Recent advances in formulation software can increase color match rates up to 50 percent. Using formulation software, ink rooms, masterbatchers, dye houses, and other formulators can accurately identify candidate formulas and cut the number of steps to get to an approved color match in half. Formulation software can also compare against digital standard data to verify accurate formulations and leverage features such as Batch Recycle and Waste Work-Off to reuse leftover materials. With ink/resin/colorant costs rising, formulation software can help you maximize inventories, reduce waste, and produce accurate color faster. Plus, some formulation software is now available as a subscription, making it easy and affordable to keep up with the latest enhancements.
-
Are you using the right color measurement device, and is it set up correctly? Spectrophotometers are used in most quality control processes to verify that color is within required tolerances. These color measurement instruments vary in size, geometry, functionality, and accuracy. Using the wrong device for your color measurement application can lead to inaccurate color. You should also use the same or a similar measurement device as specified in the digital standard, and ensure the device is set up using the same measurement conditions to capture similar spectral data. If you are not sure what type of spectrophotometer is best for your application or do not know which measurement conditions to use, talk with your customer or consult with an application specialist from the device manufacturer.
X-Rite Cup and Cylinder Fixture with the eXact spectrophotometer
If your sample is extremely large or small, liquid or powder, or an odd shape like a cylinder, a spectrophotometer accessory like an adjustable stand or sample holder can help. These accessories ensure the sample is held and positioned correctly for each measurement without damaging the device or sample, which can introduce errors into your process. By using the right device, accessories, and measurement conditions, you can truly compare “apples to apples.”
-
Is your spectrophotometer operating at peak performance? Like a car, spectrophotometers can drift over time due to age, wear, and environmental conditions. It’s essential to maintain your color measurement devices to ensure optimal performance. First, keep your device clean. It’s like looking through a dirty window; the aperture must be clean to capture accurate measurements. If you measure on a manufacturing floor or loading dock that has airborne contaminants, you should clean your device regularly, if not daily. Follow the instructions in your device manual for best practices to clean the aperture, white tile, and other components.
Next, follow the manufacturer’s guidelines for service and certification; generally once a year. Factory ISO certification provides quality control teams (and customers) the confidence that the instrument is capturing accurate spectral data. Most device manufacturers offer yearly service care plans that include annual maintenance and repairs.
-
If you have a fleet of measurement devices, are they measuring consistently? If you use more than one spectrophotometer across your workflow, you must validate they all continue to operate the same. If each spectrophotometer in your fleet measures a little differently, color data and production output will reflect this color difference. In addition to annual maintenance, tools can help validate instrument performance and reduce variation between devices. For example, these can check wavelength errors, make necessary adjustments to calibrate the instrument, and validate device performance for tight inter-instrument agreement across your fleet of devices.If your spectrophotometer manufacturer offers one, a cloud-based fleet management tool is another great way to maintain visibility into the health of all your color measurement devices. From one dashboard, you can see the location, monthly calibration reports, certification status, warranty information, and more for your fleet of instruments. For companies with multiple facilities, this real-time information makes it easy to identify devices that may cause color drift and require service.
The X-Rite Link dashboard shows the location and device health of all devices in a fleet.
-
How are you tracking and analyzing data? Many process variables, including raw material, supplier, operator, temperature, and humidity, can impact color and put you out of tolerance. Capturing and analyzing color data can help identify areas for improvement to gain efficiencies. For example, a fluctuation in temperature due to the change of season or a hot sample that was not cooled properly before measurement can affect the spectral data. Quality control and assurance software tracks and analyzes these variables to identify potential errors before they become a problem. Software can also track color and manufacturing data – from specification to material supplier to manufacturing and assembly. It works with digital standards for the most accurate spectral data and can provide an audit trail to improve communication and compliance across the supply chain.
-
Do your employees have the right training? Over the past year, we have all seen stories about the great resignation. As employees leave and new ones are hired, it is critical to educate anyone who works with or approves color. This includes a solid background in color science, an understanding of the fundamentals of color communication and evaluation, and training to properly use color measurement devices and software. There are several online and in-person color management trainings hosted by industry associations and vendors that are ideal for new employees as well as anyone who wants a refresher. Ensuring everyone has a base knowledge of color and follows the same best practices can improve your quality control program.
Online trainings
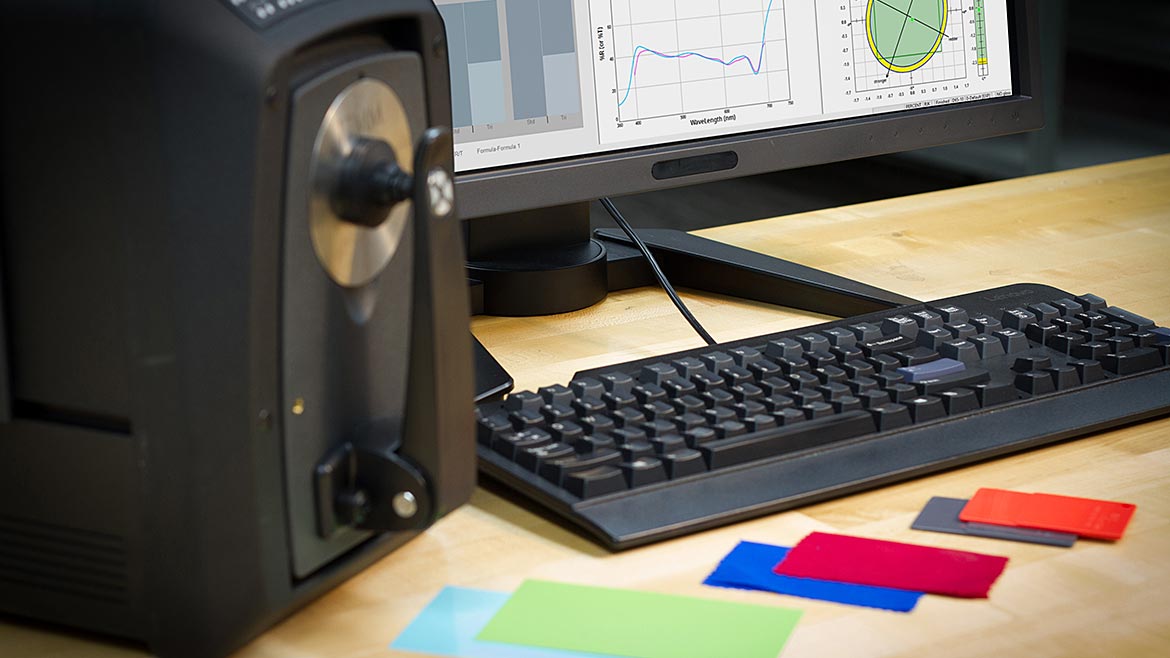
X-Rite Color iMatch formulation software
As manufacturers continue to work through ongoing supply chain challenges, consider whether there is room for improvement in your color workflow to maximize inventories and minimize waste. Even if you already have color tools and a quality control workflow in place, you can dramatically improve product quality and achieve more consistent color by maintaining your instruments, taking full advantage of technology features, and making minor adjustments to your workflow. The result is precise color the first time for a faster, more efficient, sustainable, and resilient manufacturing process.