It all starts with the question, "How can we clearly see what is going on inside our product without damaging it?" In certain cases, the answer is an industrial x-ray (2D) or computed tomography (3D) system that can evaluate, analyze, and inspect internal and external features while preserving product integrity.
These essential tools supply a wide range of benefits, from first article inspection through quality assurance. The technology, when operated correctly, can ensure products meet or exceed quality expectations in industries with exacting specifications, including aerospace, automotive / e-mobility, electronics, additive manufacturing, science/research, and more. However, these inspection systems need to be operated by trained operators to optimize the benefits and supply the return on investment (ROI) companies anticipate.
This technology has created a nondestructive way to detect defects or anomalies within a product’s interior not visible from the outside. When products must meet precise dimensions or tight tolerances, nondestructive testing imaging provides accurate measurements of the product’s internal features for verification purposes. CT images can even be compared to the original CAD drawing. Most importantly, these technologies offer the ability to detect internal defects such as cracks, voids, wall thicknesses, etc. and thereby improving product safety.
The value of proper training in industrial imaging equipment
The system’s potential remains locked inside the machine unless employees are properly trained to operate it. Even operators of an automated or semi-automated X-ray/CT system cannot reach the system’s full potential without proper training. In-depth training is what turns that lead box filled with an x-ray tube, generator, manipulator, operating controller, and cooling system into a functioning asset of the quality control department, R&D laboratory, or production floor. Imaging and the data it provides can release the product’s full potential, thus transforming the expected potential into actualization.
Budgeting for operator training
The cost of operator training can vary greatly depending on the level of expertise required and the system’s complexity. The budget for operator training should start with an assessment of the amount of time needed for comprehensive training. This should include both the hours spent in a classroom environment along with hands-on experience with the planned system you are purchasing. It is also important to factor in additional costs such as travel expenses, instructor fees, or any other related costs associated with an onsite visit.
These training details are discussed with the system supplier and included in the initial budget request for the system, with an option for additional professional training in the short term as an added expense. Companies who fail to take training into consideration may find instead of a useful investment supplying a sophisticated level of quality control, they wind up with an installed system simply taking up space on the production or lab floor instead of remaining unused, slightly used, or used improperly due to the lack of investment in training.
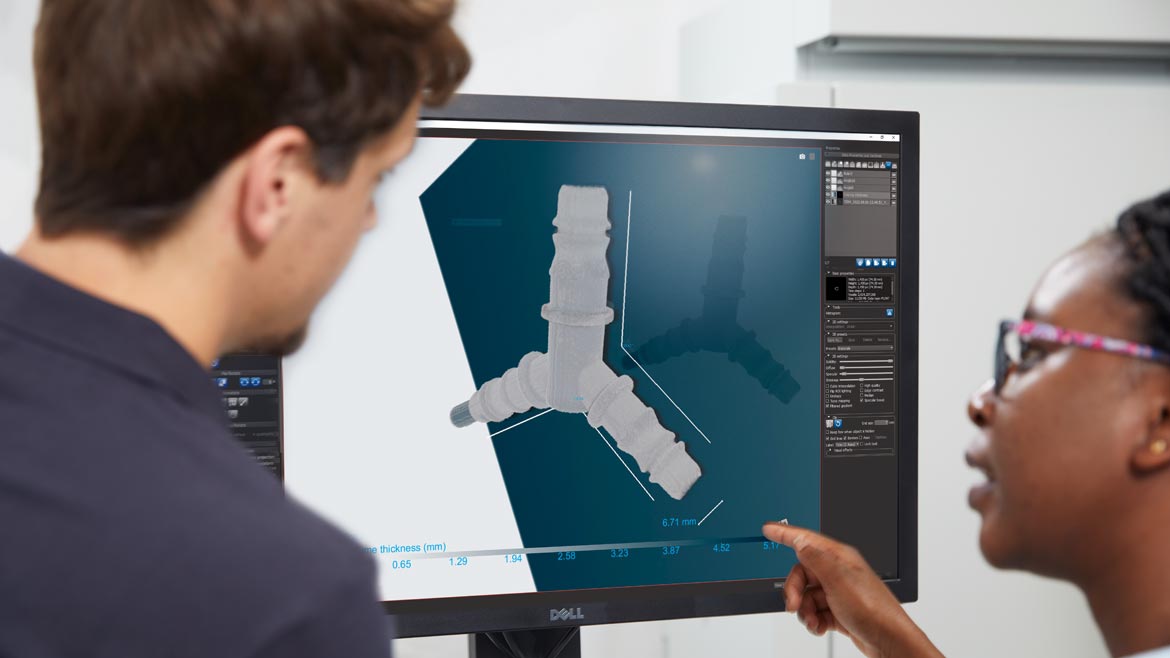
Onsite operator training with a professional is essential. | Image source: Comet Yxlon GmbH
Budget an adequate amount of time for training
A training budget involves more than a capital expenditure; it also includes time. Be realistic about the time involved for operator(s) to be trained. Previous experience does not necessarily mean the learning curve is shortened, especially if the experience was gained on a different manufacturer’s system using different software or with different materials or parts. Keeping in mind that not all operators start from the same level of expertise, it is best if the operators and the trainer can determine in advance the depth of training required to develop and learn a new technology or system and the fitting technique(s) for the application. This discussion is the basis for a timeline and lines up expectations.
The most important training topics to cover
When it comes to operator training topics, there are several areas that must be addressed before anyone can safely operate an industrial x-ray or CT machine. These include radiation safety, operational ease-of-use, production downtime considerations, depth of training needed for specific applications, and professional training performed by system manufacturers.
Radiation safety is obviously one of the most important topics when it comes to operating these machines; operators must understand the risks associated with radiation exposure to stay safe while working around hazardous materials. Systems today are designed with a lead radiation-tight enclosure or are installed in a radiation protection bunker. Special fuse circuits prevent the system from being opened while x-ray is active. Despite these safeguards, safety training is vital.
Never assume that because your operators have previous industrial x-ray or computed tomography experience, it will ensure immediate success. Understanding the technology, learning application expertise with in-depth direct experience directly with the system, and specific attention to the applications are the building blocks of success for your operators and your system choice.
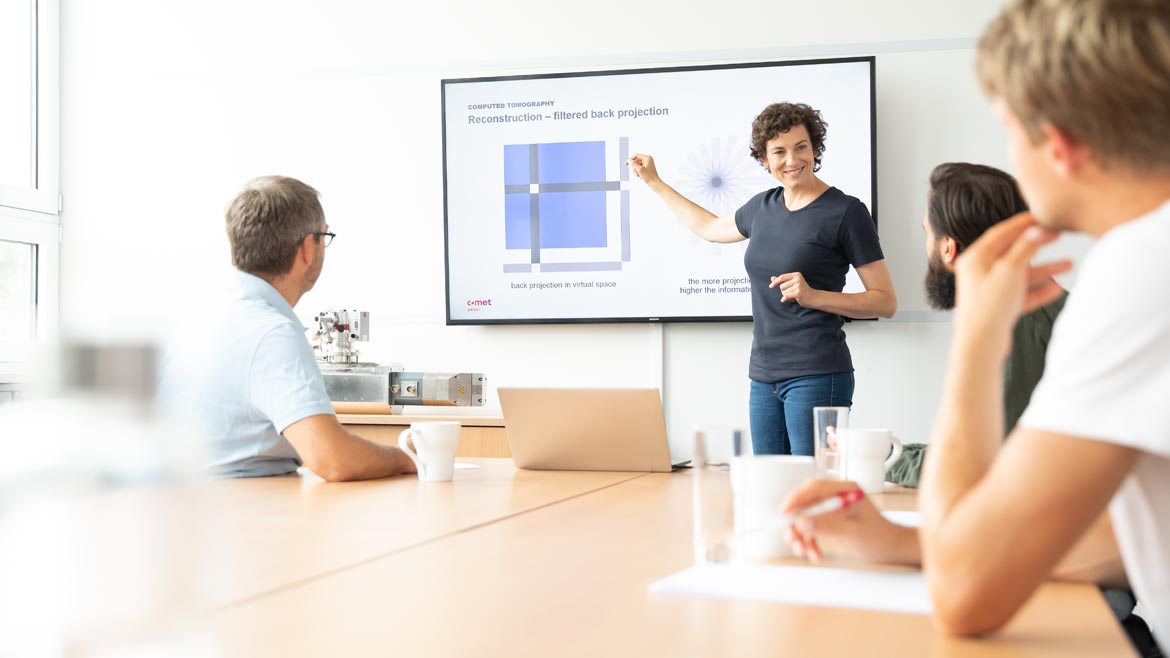
When planning, make sure to include onsite or online classroom training time. | Image source: Comet Yxlon GmbH
Today, user-friendly systems are a must; operators should be able to easily navigate through menus to quickly get their job done. What works in the new operator’s favor is that newer systems are no longer designed by experts for experts. User-friendly features include touchscreens, intuitive drag-and-drop functions, and a clear layout matrix saving time, effort, and labor costs. Systems are less complex to operate due to modular software options and customer-focused software platforms. Quality managers should be sure to ask about these improvements when evaluating a system and make sure they are given a complete demonstration to ensure that what the manufacturer considers user-friendly and your idea of user-friendly are one-and-the-same.
Minimize downtime with proper scheduling
For the future, make sure additional training for new hire(s) can be easily scheduled with the manufacturer you choose so you do not have extended downtime when a new employee is onboarded. Although you might be tempted to have the current operators train the new hire, this is should be left to a professional trainer for proper and thorough training. This gives the new hire the best possible chance to succeed and not learn any existing shortcuts or poor habits.
Other things to consider when incorporating training into the budget and schedule are to choose a date for installation well in advance, then properly adjust your production requirements to consider downtime of the production line or lab during the installation and the training of the operator(s).
Consider all the other specific internal and external people or departments involved which will be affected by the addition x-ray/CT to the process. Don’t forget to include training samples in the conversation. A trainer may suggest using samples with known flaws to begin the training and, at some point, switch to the actual products of the system’s new owner. Confirm the benefits of inspection requirements before training begins.
According to Joscha Malin, director product marketing software solutions at Comet Yxlon, Hamburg, Germany, "Additional advanced training should be scheduled a couple of weeks after the initial training that is immediately following system delivery and installation. This is especially valuable for highly complex systems with new imaging technologies. This delayed additional training solves the information overload which is common for new users. It is unrealistic for new users to absorb everything in the training over two to three days. A short delay in additional training cements operator success, which is truly a benefit for all."
Depending on your specific x-ray and/or CT needs and system, there are a wide range of applications and techniques which could be taught. Provided below is a short description of main technologies and the popular applications for each to provide an idea of the depth of the training possible:
Industrial X-ray (2D)
Because the human eye can only distinguish about two hundred gray levels, but modern X-ray detectors deliver about 65,000 X-ray images that must be processed. Depending on the inspection task, operators can use simple procedures to adjust contrast and brightness in the image, representing a portion of gray values. Advanced methods to filter the whole image with e.g. a high-pass filter to highlight intense gray value changes are applied.
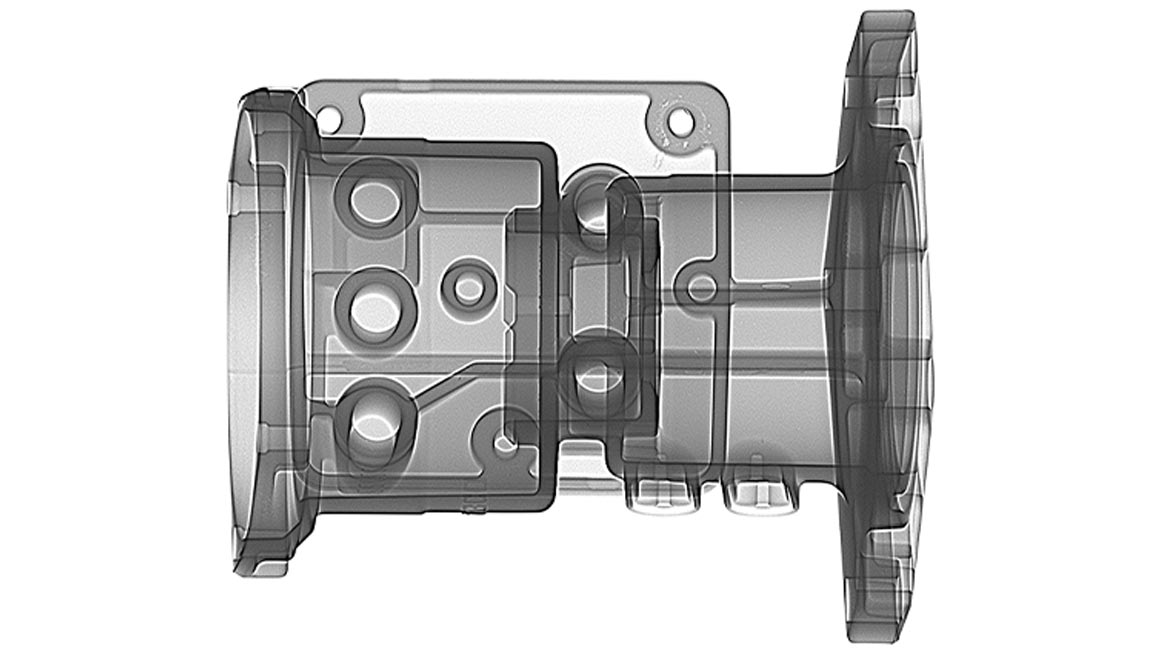
X-ray image of an aluminum cast part | Image source: Comet Yxlon GmbH
Popular applications for industrial x-ray include:
- First article inspection
- Quality assurance and material analyses
- Failure analyses, e.g., flaws, porosities, cracks, inclusions
- Assembly checking
- Measurements of outer and inner structures
- Inspection of samples, small serial productions, and 100% inspection
- Process control
Computed Tomography (3D)
To generate the 3D representation of an object under inspection, an industrial CT scanner system first creates a series of 2D X-ray images at different rotational angles, so-called projections. As the 2D images are captured, the reconstruction can begin, e.g., by a back-projection algorithm. For each row of pixels, the system creates tomograms – virtual slices through the three-dimensional object. These tomograms are then joined together by software to produce the final 3D data of the object.
Different shades of gray correspond to different density values of the material, so flaws or irregularities can be spatially localized with the greatest accuracy. When describing image sizes, industrial CT speaks of voxels (volume pixels), which are the 3D equivalents of pixels.
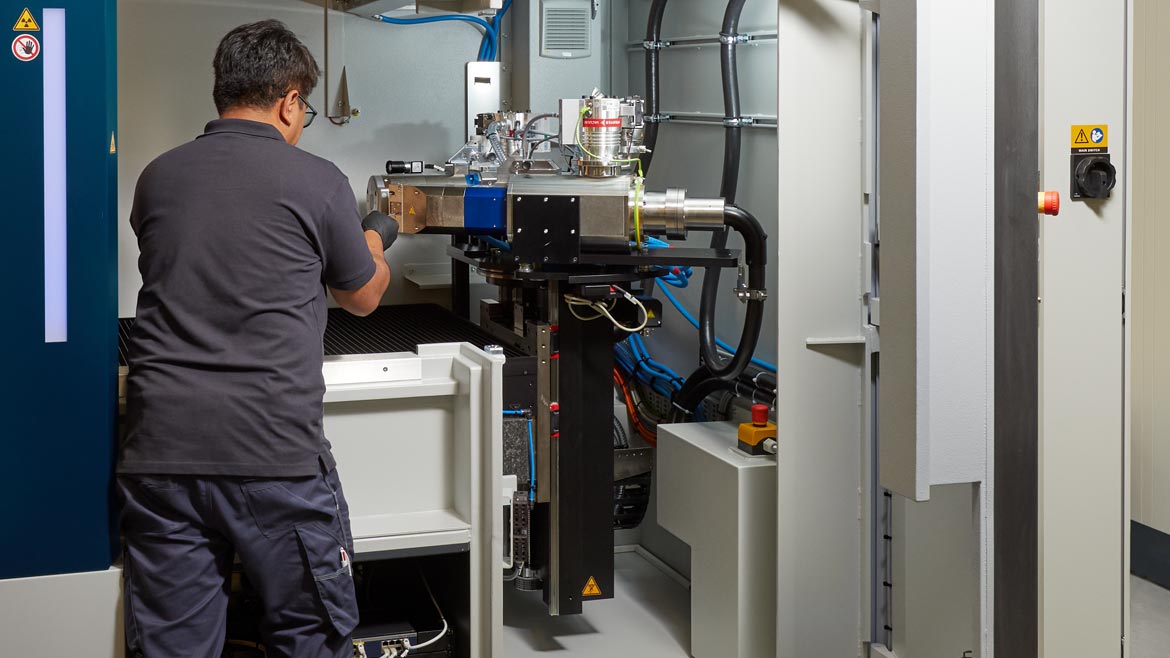
Example of the interior of a CT Inspection System, in this case Comet Yxlon FF35 CT | Image source: Comet Yxlon GmbH
Operators can be trained on basic CT scanning techniques such as fan-beam CT, cone-beam CT, helical CT and computed laminography.
Popular applications for computed tomography include:
- Identification of porosity and inclusions
- Metrology
- Structural analysis in AM
- Analysis of composite materials
- Assembly analysis
Laminography
In between 2D X-ray radioscopy and 3D computed tomography (CT), laminography is sometimes referred to as "2.5D inspection." Laminography addresses the specific challenges of inspecting flat components, such as printed circuit boards (PCB), microchips (IC), entire cell phones, tablets, laptops, and more. As we have learned above, 2D X-ray inspection provides high resolution but does not give spatial information, and 3D CT supplies good spatial information but can lack resolution. Laminography adds depth information to high-resolution 2D images so defects can be reliably detected and spatially located in a plane object.
Unlike computed tomography, laminography does not record 360-degree projection to generate spatial information but instead scans objects from a limited angular range. The limited angle allows moving the x-ray tube closer to the flat inspection object for higher resolution. The inspection system generates high-resolution slice images in the lateral plane of the object.
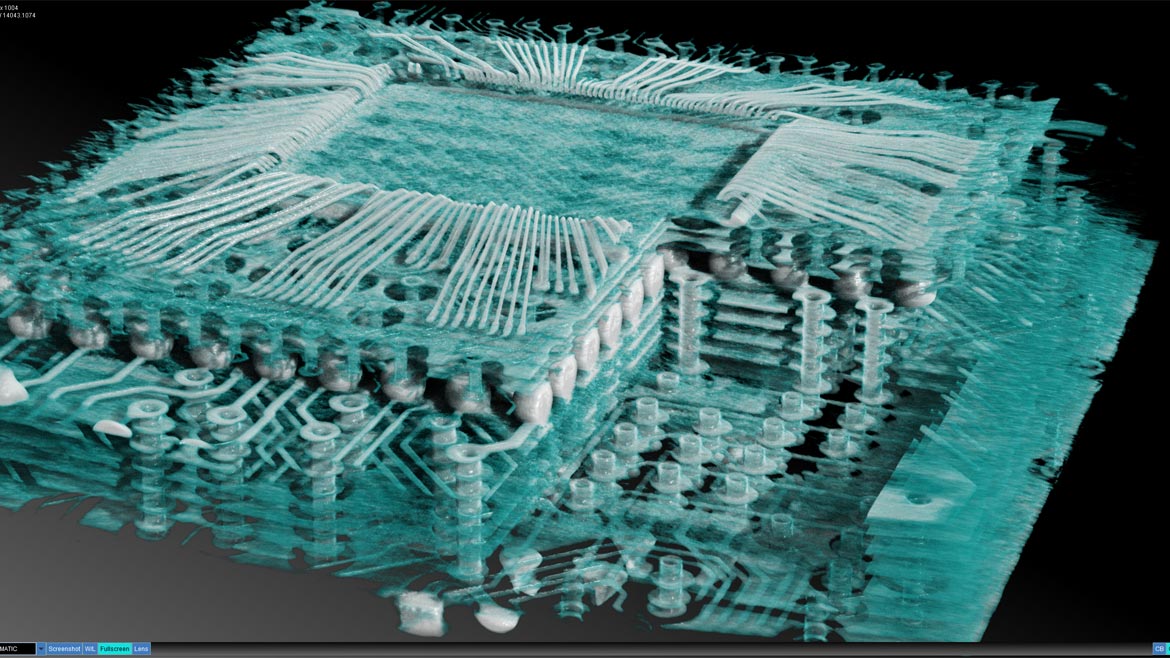
Laminography scan of a CPU. | Image source: Comet Yxlon GmbH
Popular applications for laminography include:
- Quality assurance of solder joints
- Advanced packaging inspection
- Flat electronics device inspection
CT Metrology
Analyses and measurements of the internal structures have become particularly important, especially in the context of new additive manufacturing methods. Nondestructive testing produces volume data containing comprehensive geometrical information. With an almost unlimited number of reference points, a complete part can be measured, and high-resolution dimensional measurement delivers precise data for an in-depth analysis of cavities and material interfaces, even in hybrids.
Popular applications for CT Metrology include:
- Injection molding in the automotive industry
- INCONEL cast part inspection for the aerospace industry
- Actual/nominal comparison
- Geometric dimensioning
- Wall thickness measurements
- Edge distance calculation
Data analytics related to X-ray and CT systems
X-ray and CT systems are sensors providing rich data that can be used for quality assurance and product optimization. Among optimization objectives, manufacturers can leverage statistical information to improve the process, keep an eye on adverse production trends and counteract them at an early stage. This avoids waste to increase efficiencies and cost-effectiveness. Make sure the operator learns data analytics as part of the training process.
Operator Attentiveness to Preventative Maintenance
Preventative maintenance is another must. The installed system should have sensors and image data that identify preventive services or worn components. This knowledge can help to avoid downtimes and extend the life of the system.
Industry Standards and Certifications
Applicable industry standards and certifications are an additional consideration. Here is a list of just some of the organizations that set these industry standards:
- ASTM International
- IPC
- NADCAP
- VDE/VDI
- EN
- ISO
- AS
Summary
Achieve training goals by cementing expectations as part of the purchase process for advanced scanning technology. The result? Operators will be able to complete a scan in the time expected, using the manufacturer’s own product, collect and analyze the required data, and meet or exceed specification and quality standards. Then a quality manager can truly say their industrial x-ray or computed tomography purchase has turned from expectation into actualization.