During the current artificial intelligence boom, businesses across every industry are leveraging powerful technology to make their operations and processes more efficient.
The manufacturing industry is no exception—from automating repetitive tasks, monitoring employee processes, predicting safety hazards, and more, AI can be used for many use cases on the shop floor and throughout the supply chain.
Manufacturing serves a vital role in the global economy. According to Statista, the industry accounts for about 11% of America’s total gross domestic product. As a primary driver of the economy, manufacturing leaders would be wise to realize the significant productivity gains and cost savings that can be achieved with AI.
AI can be customized to meet specific business needs and goals. With the proper solution, manufacturers can find an immediate return on investment in their organizations. In this article, we will explore a few specific ways manufacturing business leaders can benefit from AI by implementing it into their smart factories.
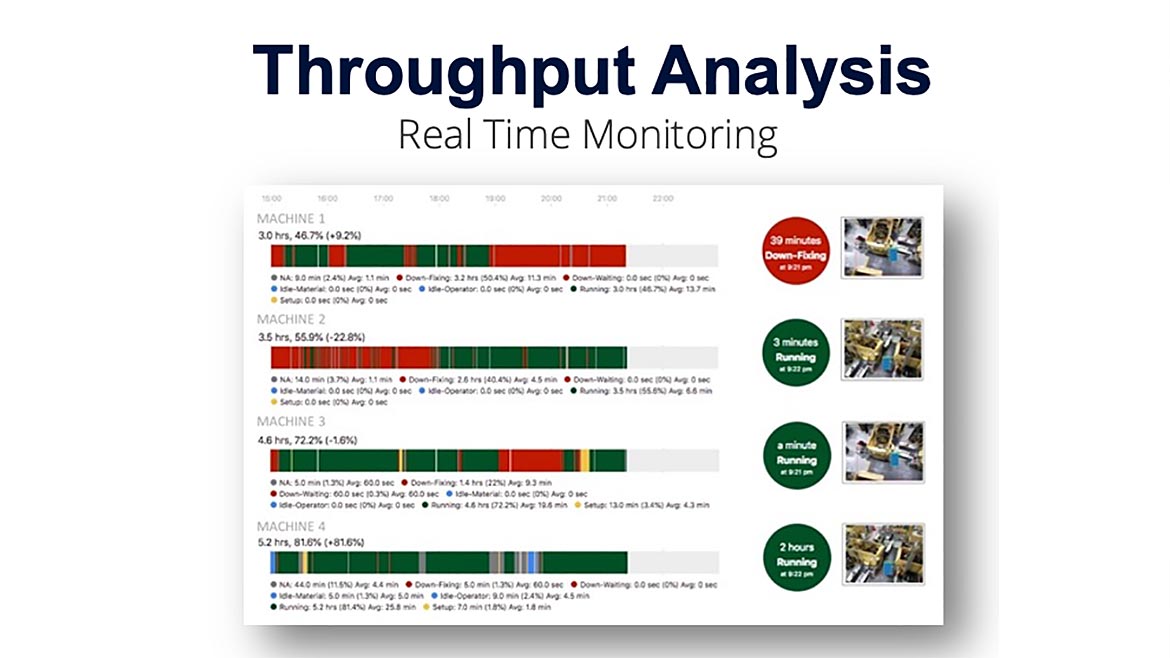
Automating Repetitive Tasks
The manufacturing industry functions on a routine cycle, similar to many other businesses. Various processes revolve around repetitive procedures, tasks, and work schedules. Although there are some variances, many business operations in the smart factory depend on a routine schedule.
These seemingly redundant manufacturing processes produce an overwhelming amount of valuable data that can be derived from many sources. These sources vary from sensor-equipped machines throughout the shop floor or the supply chain.
However, organizations must capture all this data to be able to extract value from it. Manufacturers generally use on-premise gateways and connectors alongside a system to integrate data into a single platform. The manual task of collecting and analyzing all this data throughout the enterprise can be automated with the help of AI.
AI can help supply chain leaders navigate mountains of data from various sources in real-time, keeping an already overworked staff informed, motivated, and better able to make the best decisions. Plus, with more free time back in their hands, employers can empower workers to work on more rewarding and creative tasks. In the long run, this will allow manufacturers to make their data collection processes more efficient and save time and money on hiring and training new employees.
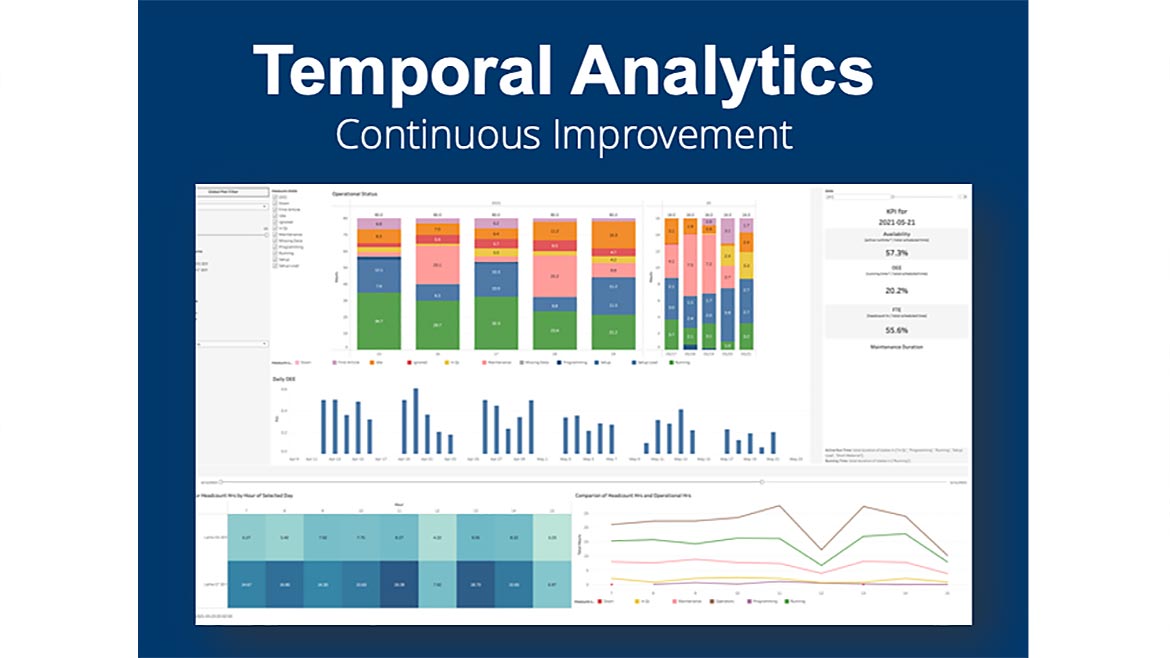
Generating Material-Centric Insights Anywhere
Data and analytics within smart factories can offer enterprise-level awareness and give valuable context that is crucial to decision-making. This data is collected through various sources, including IoT and IIoT devices, HMIs, PLCs, ERPs, CRMs, or manual data captures.
Once all the data is integrated into a single platform, business leaders can leverage AI to correlate the data and provide context automatically. AI can help find patterns in existing data and make predictions from new data. As a result, manufacturing leaders can create visualizations of the entire value chain and allow them to identify previously unseen blind spots within their factory. If implemented correctly, this can lead to proactive suggestions, predictions and warnings.
Additionally, through the cloud, businesses may interface with other logistics software and benefit from real-time results wherever they are. These platforms can immediately link to feed AI operations without the need for internal IT resources or challenging system integrations. This drastically reduces manufacturing bottlenecks and allows manufacturers to save time and money on hiring additional resources for generating material-centric insights from their data.
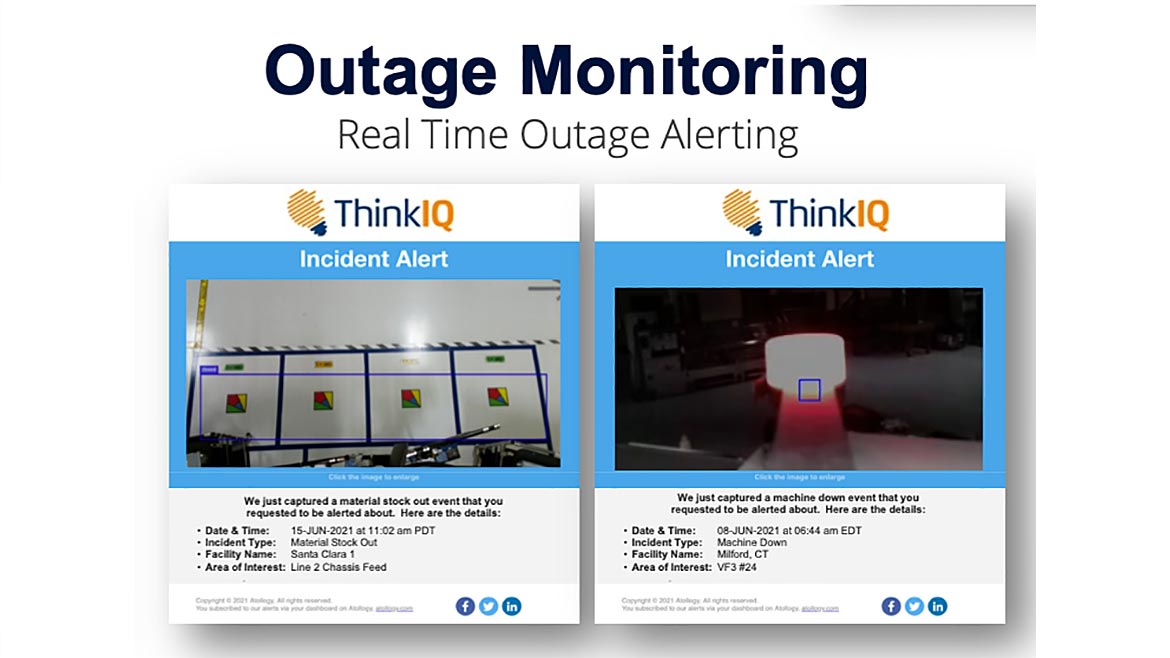
Predicting Safety Hazards
The manufacturing shop floor can pose many potential safety hazards for workers, including heavy machinery, rickety ladders, and dangerous hand tools. These machines and instruments can be potentially dangerous to employees if they are not properly trained or continuously monitored to ensure proper use.
With AI technology, camera sensors on the shop floor and manufacturing yard can continuously analyze video images to identify potential safety hazards to employees. The technology can be trained to look for employee errors, identify best practices to boost productivity and warn staff members of potential dangers.
For example, employees who fail to wear the appropriate protective equipment can pose a safety threat to themselves and others. With continuous monitoring powered by AI, managers can be warned of this and prevent a potential accident before it occurs.
Safety blind spots throughout the factory can take many forms, but with the help of AI, these previously unseen safety hazards can be exposed. This should be a high priority for all businesses, especially manufacturers since blind spots come with increased risk and cost for companies. Therefore, identifying errors in a factory and adjusting best practices based on this data will significantly benefit a company in the short and long term.
Monitoring Vehicles in the Yard
Another important AI manufacturing use case is monitoring vehicles entering and exiting the manufacturing yard. AI-powered yard management systems can now read license plates and container identifiers through sensor-equipped cameras. With this helpful information, managers can be notified when a vehicle enters and exits the yard and for how long they are present.
This information helps manufacturers to ensure that the correct containers are sent and that they are on a punctual schedule. As a result, supply chain leaders can ensure workstreams are efficient and timely, optimizing business operations and saving time and money.
The Journey Ahead
Efficient manufacturing businesses need an innovative solution to automate mundane tasks, generate contextual insights, and improve predictive maintenance and overall yield. As decision-makers look to continuously enhance operations, it is essential to recognize how AI can significantly build a successful smart factory. In addition, supply chain leaders should better understand how their factories operate by identifying weaknesses and implementing solutions to increase output.
Every manufacturing operation has different needs, but using technologies that offer a personalized approach while understanding broader business challenges can make a significant difference. Moreover, every advancement counts in today’s fiercely competitive economy.