Additive manufacturing (AM) is a much-heralded technology, but it, like all other technologies, comes with its risks and challenges. It is not a push-button process that delivers perfect parts on each try; many factors can contribute to flawed parts. Strict quality control measures prevent these parts from ending up in, for example, an aircraft, but methods also exist to detect errors during manufacturing, saving time and money.
In-situ monitoring (ISM) employs cameras and sensors (to name a few) to monitor additively manufactured parts as they are being built. As parts become more complex and are used in more critical applications, the need for ISM grows. The technology has plenty of room for growth and maturation, and thus in June 2022, ASTM International and NASA sponsored an ISM workshop. The intention of the workshop was to bring together representatives from government, industry, and academia to assess ISM technologies and their application in qualification and certification, and have discussions on what research and development is still needed.
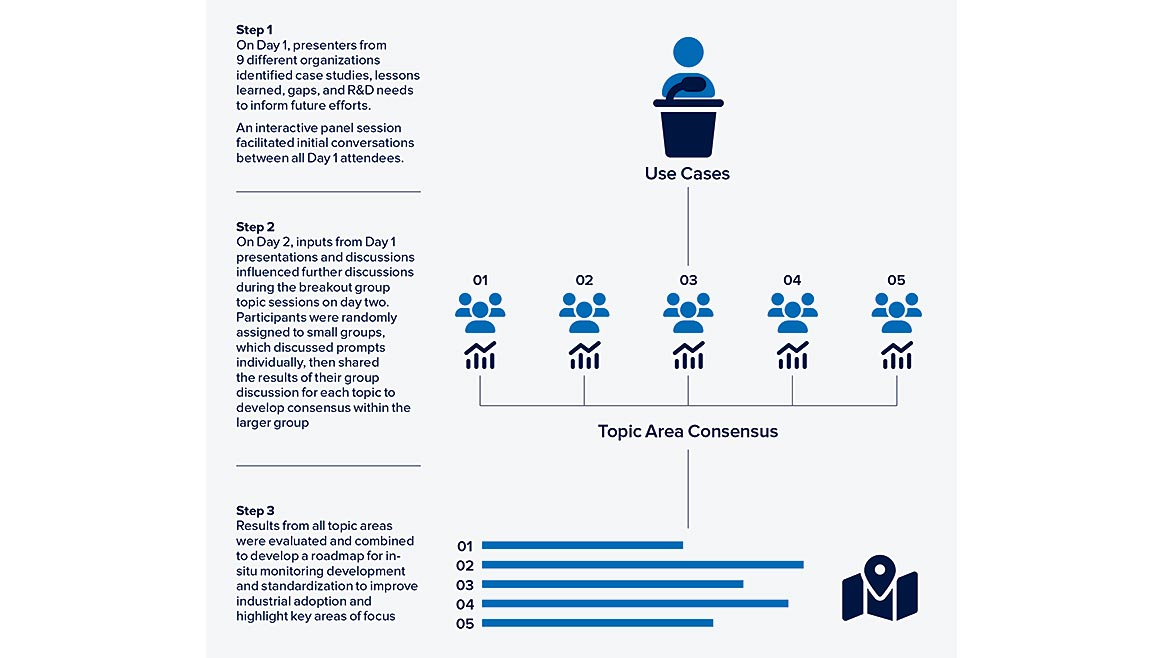
The participants discussed the different types of ISM in practice to determine which methods are the most mature. The first was AM Machine Condition Monitoring, which involves models and methods to monitor the health of the printer. These tools ensure that the machine is operating normally and alert the user to conditions that are outside the window of acceptable operation. These conditions could involve the beam health, feedstock interactions, and build chamber conditions, etc.
Layer imaging is another highly mature ISM method. This method, used in laser powder bed fusion and directed energy deposition processes, involves off-axis cameras that image and assess the top layer of the powder bed. It allows for the entire build area to be monitored for anomalies. The third ISM method that the workshop participants determined to be the most mature is residual stress and distortion modeling. These models and systems, included in many commercial software packages, predict and monitor distortion effects caused by residual stress.
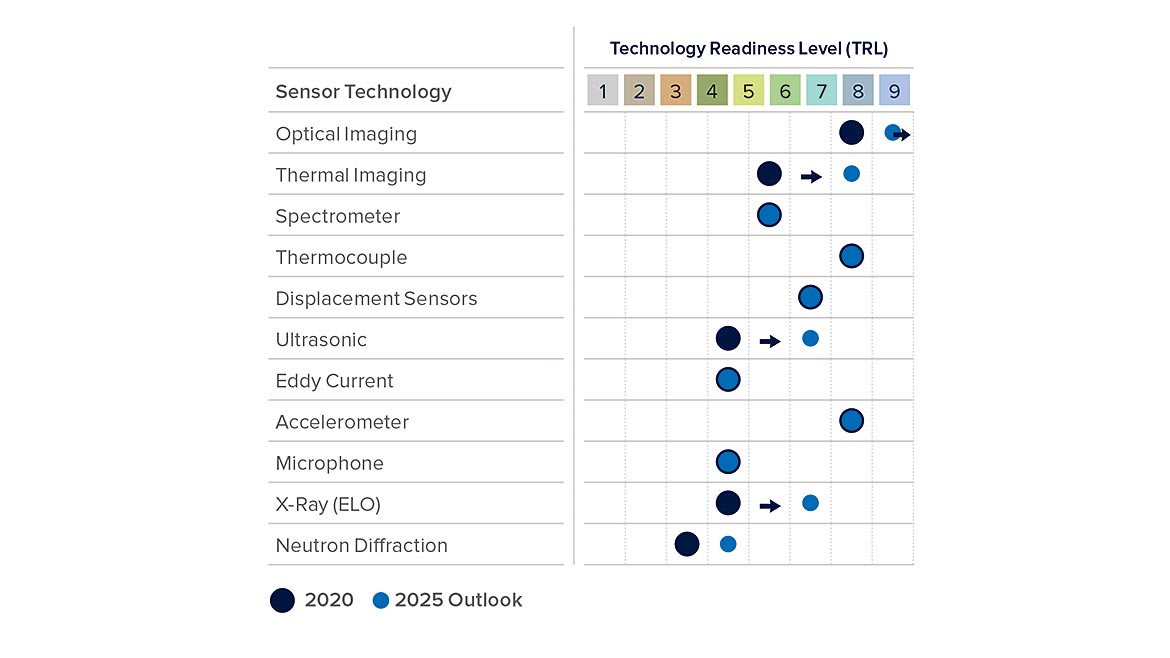
The participants also assessed ISM methods with low levels of maturity but high levels of potential for future impact with more development. Data analysis and interpretation of flaws and defects was one method lacking maturity currently, due to challenges involving registration and false indications. These challenges have led to a lack of consensus on best practices and consistency across the AM industry. Consensus on this method is needed for industry acceptance and widespread adoption.
Another less-mature method is probabilistic analysis, which predicts the probability of occurrence and detection of various potential flaws, along with the likelihood of those flaws remaining in the final parts. Probabilistic analysis methods have a great deal of potential to reduce the impact of flaws as well as reducing the need for computational power. Like data analysis and interpretation, however, probabilistic analysis methods suffer from a lack of industry consensus on the best approaches. These methods also need more data and use cases to demonstrate their reliability.
Finally, melt pool-scale simulation models, which include thermal and fluid simulation models, are currently at low maturity. These have seen some success with OEMs and research institutions, but they require additional development, testing, and standardization before they can achieve widespread implementation. To bring these methods to greater maturity and wider use, machine learning holds a lot of potential.
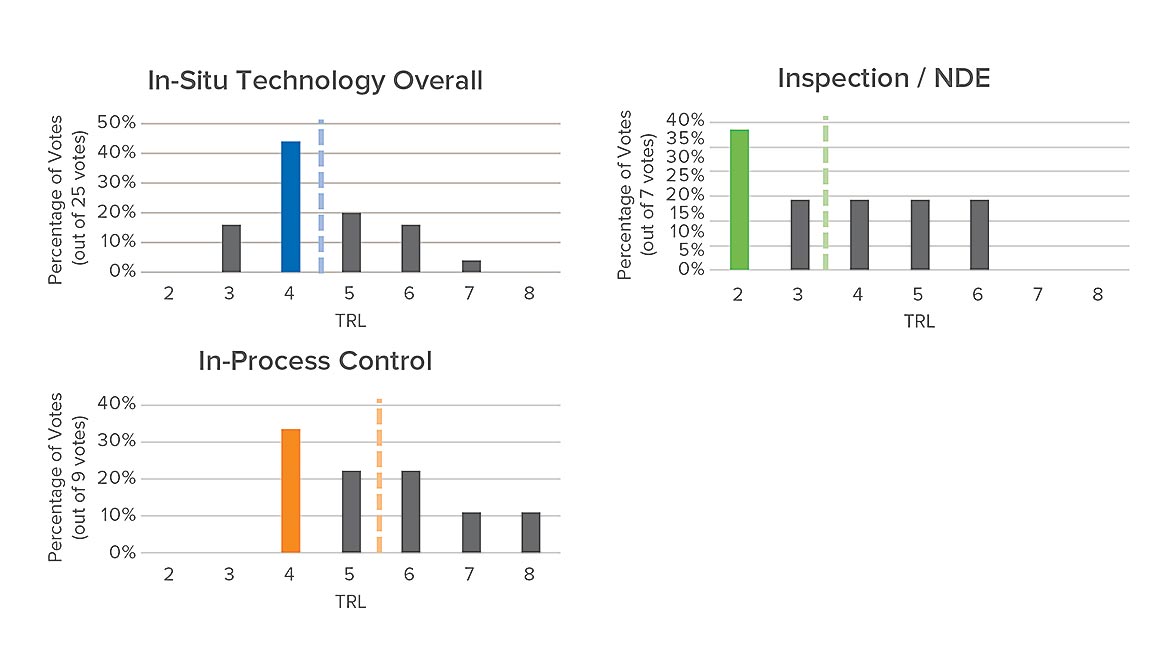
The workshop participants also identified technical gaps limiting the full implementation of ISM for AM qualification. One of those gaps is the lack of causal correlation between signals and actual flaws. To address this issue, new models need to be developed, and data-driven algorithms need to be integrated with physics-based models. Testing should be implemented across different machines, materials, and monitoring technologies. Widespread data sharing and collaboration will also be necessary across the AM industry.
Another gap in ISM readiness is the limited availability of baseline datasets. While many machine suppliers have databases of historical data, testing and verification of the models and techniques used to acquire that data is needed before it can be used by the wider AM community. To speed the process of more widespread adoption, quality, reliable standardized datasets need to be generated. Industry and academic partnerships can be leveraged to create open-source databases.
A lack of standard artifacts or benchmark models is another issue. Testing and standardization of defect formation approaches and artifacts will be helpful for the development, setup, calibration, qualification, and ongoing use of ISM systems.
What types of flaws can be detected using ISM? Highly detectable flaws, as identified by the workshop participants, include lack of fusion (surface and subsurface LOF), spatter, geometric and dimensional defects, powder spreading quality, and melt pool dynamics metrics such as spot size and shape. Flaws with moderate detectability include keyhole porosity, internal stress-induced cracks, and delamination above a certain threshold. Defects with the lowest detectability include contamination and subsurface defects, as well as defects related to variation in microstructure and chemical composition.
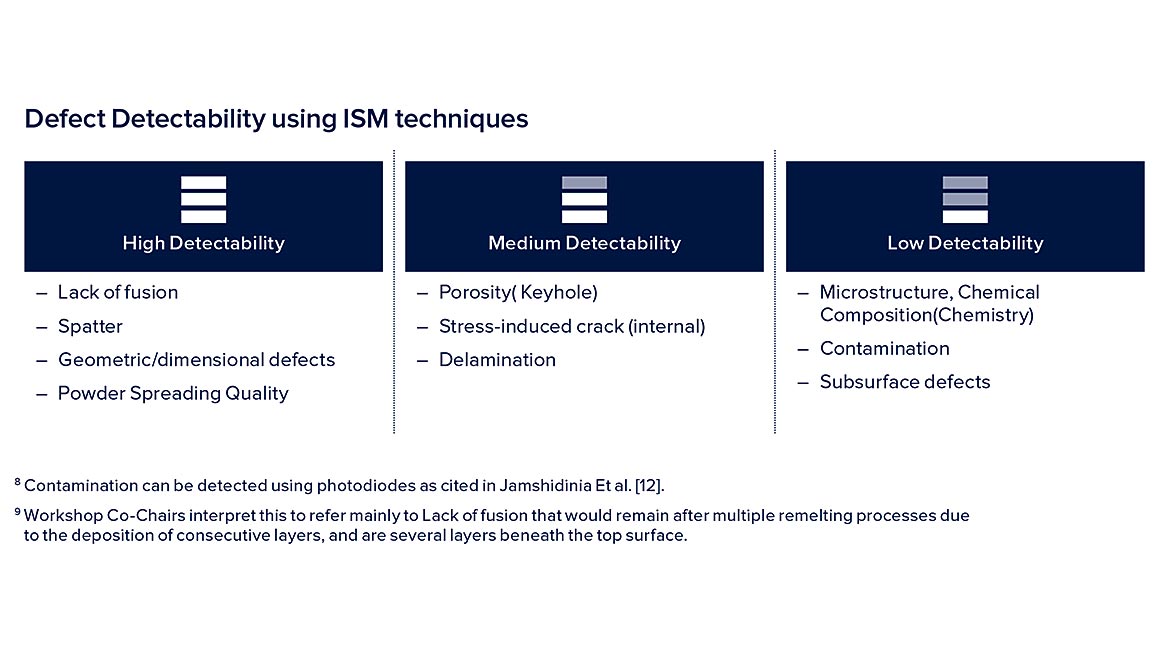
Flaw detectability is currently limited by several factors including slow measurement speed, cost, lack of causal correlation, sensor resolution, and interactions with the previous layers. The AM community needs to define the critical flaw size for different types of flaws, which will help determine the computational power required and support corrective action. Determining what size flaws can be reliably detected across machines and materials could also go a long way toward addressing this challenge.
ISM presents several opportunities for standardization. Establishing a common file format for ISM data is one example, as are standardizing the transfer and exchange format and developing an overall data management schema. Standards can also be developed for setup, calibration, and maintenance of systems. While systems created by different OEMs will have different requirements, certain areas can potentially be standardized. These include frame rate and wavelength being captured, as well as some other parameters.
The standardization of terminology is especially important. Terms such as anomaly, flaw, and defect, for example, need to be uniform across the AM industry for the purpose of consistent documentation and communication. Terminology also needs to be re-evaluated as ISM technology progresses.
Acceptance criteria should be established for defect detection and process control. A standardized approach to qualification of ISM systems must also be created for these systems to be fully implemented in production.
Standards in general can help to set expectations for users considering implementing ISM and to identify the best applications of the technology. As AM continues to mature, ISM needs to mature alongside it. ISM has the potential to be a valuable tool for qualifying AM parts, but the industry must form stronger consensus on best practices and terminology. If time and effort are directed at growing and developing the various methods of ISM, it could lead to stronger AM parts, reduction in time and cost, and wider acceptance of AM.