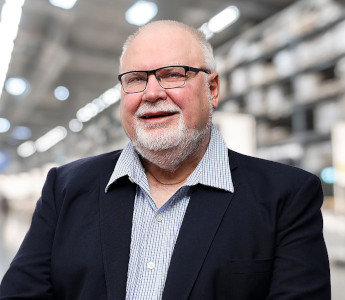
Quality sat down with John Vandenbemden, principal of Q-Met-Tech, LLC, as well as its 2022 Quality Professional of the Year to discuss his upcoming presentation at The Quality Show titled, “Inspection Versus Auditing.”
Listen to the podcast here.
John: Well, thank you for having me. I do appreciate the opportunity to speak at the show as well as present these topics to the audience and I welcome everybody to come join us on that Thursday morning.
Quality: So tell us a little bit about what people can expect from your session. In particular, why, it is important to distinguish between inspection and auditing.
John: Well, the two terms keep getting flip-flopped. People are using these two terms interchangeably. But what people need to really understand in the world of our quality and management tools is these two terms have really distinct differences and that is the most important part of all this.
Quality: How exactly did the concept of the need to separate these two first come about?
John: Well, as an auditor, it frustrates me a little bit to go into different organizations and see the two terms kind of get mixed in for different purposes and people not understanding what's associated when they use the term. And that's really the point. I'm trying to keep them separate. When you say the word audit, what does that mean when I say the word inspection? What can I expect out of this term? What's the end result that I should see? So that is the focus of what this sessions going to be about.
Quality: What would you say is the most important thing that you'd like the audience to take away from your upcoming session?
John: I want to have them come out of this session with an appreciation that both of these tools, or techniques, are very critical and there's a need for both. But there's also a proper application for both. When I use the term auditing, what do you have as an expectation? What's the output that should be there. And if I do an inspection, the same thing. What is it's intended output? And put in that separation of when should I use which tool or technique?
Quality: How did you first get interested in auditing and this need for it to be done well?
John: It goes way back to when I started my career. Really, one of the first tests when I entered the quality world in the early eighties was to go assess suppliers. We’d have problems with suppliers. Suppliers are not giving us what we need and building that technique and understanding of how to use auditing to help drive improvement, drive change. And then I became a corporate auditor and was auditing within our corporation at various sites, and that internal is external from there, and the rest is history.
Quality: So have you seen anything interesting, or any recent trends that you've been seeing in your work or your travels lately?
John: Well, I think the use of technology is starting to get acceptable. The pandemic brought us doing remote work and remote auditing. How to work smarter and how to be more efficient. It started driving different tools. I was doing an audit this past week and the company's maintenance people and their inspections are using tablets. It used to be done with all these paper check sheets, things of that nature. So I get a better response. I can analyze the data collected much easier…It's not replacing the person. It's enhancing the abilities of humans. They could get the attention the details. Still, somebody needs to train technology. Somebody still needs to evaluate when appropriate action needs to be done. But it's enhancing the abilities that we have and will help us to do a better job.
Quality: To learn more, attend John’s session at The Quality Show at the Donald Stephens Convention Center in Rosemont, Illinois. His presentation will take place on Thursday, October 26, at 11:30am.