Positive material identification, or PMI, is a method of nondestructive testing (NDT). It is as critical for quality control and assurance as it is for safety, says Matt Kreiner, head of global product management, Hitachi High-Tech.
The ability for producers to manufacture quality goods starts with having safe, reliable operations, and PMI is central to any mechanical integrity program, providing a quick way for inspectors to identify risk factors within the facility and avoid potentially hazardous situations, Kreiner says.
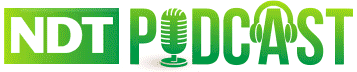
Positive Material Identification Made Easy
Matt Kreiner, the head of Global Product Management at Hitachi High-Tech, discusses trends with PMI, how it can help manufacturers improve quality, and the benefits of on-site PMI.
“The materials comprising production equipment are carefully selected and specified to handle the process streams flowing through them at given temperatures and pressures,” Kreiner explains. “When there are mismatches between materials and chemicals, or when mistakes are made when replacing components, there is potential for accelerated corrosion and unintended chemical interactions that can result in physical or chemical properties being out of specification, or more violent reactions.”
Therefore, quality teams must establish a baseline of safety, using the right materials so that plant operators are able to run their processes as designed and produce goods to specifications at the expected volumes, with lower risk for unexpected failures, Kreiner adds.
PMI is employed in industries using metals and alloys to rapidly verify raw materials or check finished products, “ensuring materials comply with the specified grade or composition,” says Mathieu Bauer, senior application scientist and associate product manager for handheld XRF analyzers, Thermo Fisher Scientific.
PMI is essential in many industries where mission-critical metal alloys are used, such as in the power generation, oil and gas, aerospace and automotive industries, and the requirement for PMI of alloy materials has grown steadily. Today, PMI is a standard procedure in many industries for incoming inspections, material verification during manufacturing, and quality control of final products, says Esa Nummi, vice president, X-ray Mobile and Portable Analyzers, Bruker Nano GmbH.
There are several different techniques for the positive material identification (PMI) of metal alloys, with the most common being Handheld XRF (X-ray fluorescence), Optical Emission Spectroscopy (OES) and Laser Induced Breakdown Spectroscopy (LIBS), Nummi says.
The most widely used of these is XRF. Modern handheld XRF instruments are easy to use, provide fast and accurate analysis, and designed to withstand challenging industrial environments, Nummi says.
PMI using handheld XRF is critical for quality control, because it helps ensure that the correct alloys and grades are used. “PMI plays a critical role in quality control by verifying a material’s composition and ensuring product consistency,” Nummi says. “By confirmation of the desired material properties, PMI helps to guarantee product quality and reduce defects, rejections, and customer complaints.”
The absence of PMI in mission-critical industries can lead to several potential risks and consequences. These include safety, compliance, quality, reputation, and financial risks, experts say.
Omitting PMI can lead to the manufacture of parts comprised of inappropriate metals and alloys that could later fail, typically because they have lower corrosion resistance or inadequate physical properties, says Bauer. “This can result in serious consequences, especially when these parts are used in aircrafts or facilities such as nuclear power plants,” he says.
If you do not perform PMI, you are effectively flying blind, says Kreiner. “There may be hidden dangers directly in front of you and you wouldn’t even suspect it. Using the wrong material in the wrong place in an operation could result in premature failure of process equipment, products being out of specification, and safety hazards.”
The first two situations mostly carry monetary risks, but they are disruptive, slow down or stop production, and waste valuable resources in finding a resolution. And while it is easy to be alarmist about safety hazards, Kreiner says, material compatibility issues have been attributed to injuries, property damage, environmental impact and even death.
Depending on where in the world you operate, there are regulatory agencies – including OSHA– that establish behavioral requirements for plants to minimize these risks, he says. Not performing PMI risks non-conformance fines or other punishments.
NDT Series
Positive Material Identification
Although they make look visually identical, different alloy grades can have significantly distinct properties, such as hardness, thermal differences, or corrosion resistance. This makes it, in many cases, impossible to differentiate between them without PMI, says Nummi.
“Using incorrect materials can pose significant risks in industries where safety is paramount,” Nummi says. “For example, in sectors such as aerospace, petrochemical and energy, the use of improper materials can compromise the structural integrity or functionality of components. This can result in catastrophic failures, accidents, or injuries. PMI helps ensure the right materials are used, minimizing these safety concerns.”
Without PMI, there is a higher risk of using incorrect or substandard materials in manufacturing processes. This can result in products not meeting the required quality standards, leading to performance issues, premature failure, or reduced durability. Quality control may be compromised, leading to product recalls or potential safety hazards. Implementing a PMI program helps mitigate these risks and ensures the use of correct and compliant materials.