Software isn’t new to manufacturing, but as technical capabilities have evolved and matured, it’s becoming increasingly entrenched in processes that directly affect product quality. This means that quality professionals need to be concerned with software outside the realm of enterprise quality management systems (EQMS). Whether the manufacturing department uses a manufacturing execution system (MES), enterprise resource planning (ERP) system, or some combination thereof, how those systems affect quality and interact with each other is important to ensuring product quality. Providers of that software recognize it doesn’t operate in a vacuum and vendors need to consider how they can benefit their customers’ companies as a whole rather than focusing on a single department.
Keeping this in mind, software vendors are focusing on three trends to distinguish their offerings and better serve their customers.
#1: Built-In Artificial Intelligence (AI)
Very ambitious manufacturers are building their own artificial intelligence (AI) programs that connect and analyze data throughout the company. They’re hiring professionals that can design and train an AI algorithm specifically for them. That’s certainly one way to approach AI use. The other is to let software vendors do the heavy lifting for you. AI is popping up more frequently as functionality included in enterprise software. Of course, this brings up the problem of whether AI will take the place of humans. AI should augment, rather than replace employees. AI without humans leads to problems generally, but if you manufacture regulated products, the human element is vital. Software vendors know this and are working on AI that makes quality professionals’ jobs easier but won’t replace them.
Fortunately, AI can be used for work that humans either can’t do well or would rather not do. One example of this is detecting trends using data from free text fields. Natural language processing (NLP), a subset of AI, can understand the text much the same way that a human can but processes and analyzes the data more efficiently. That means complaints that are phrased differently but ultimately point to the same problem can be detected and categorized together. You could certainly have an employee read through the complaints and try to track common themes, but is that the best use of an employee’s time? By using an AI algorithm, your employee can focus on finding the cause of the problem and solving it, rather than manually tracking and trending data.
The holy grail for quality professionals would be AI that finds the root cause of a quality event and tells you the corrective action you need to take. Investigating corrective action/preventive action (CAPA), pinpointing the root cause, determining what corrective action needs to be taken, and monitoring to ensure it has the desired effect, is a headache. AI can do the bulk of the legwork for a quality professional and suggest the solution, reducing the number of CAPAs and the time it takes to resolve them. This again frees up time for quality professionals to focus on continuous improvement rather than constantly putting out fires.
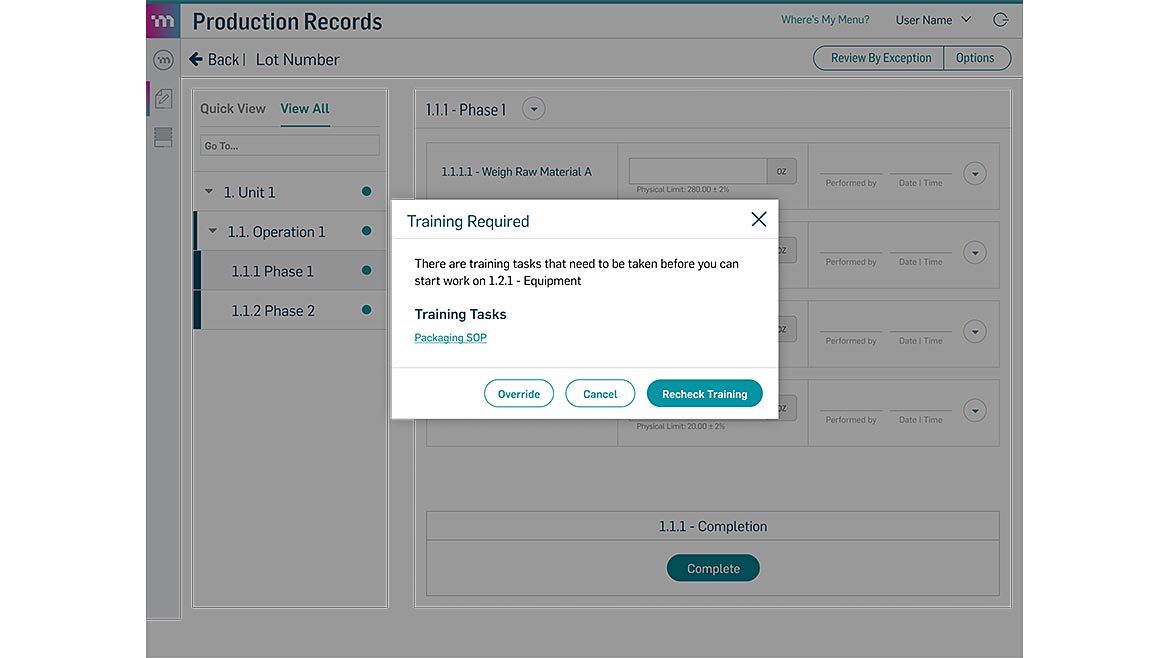
#2: No-Code Software
Customization sounds like a good thing until you apply it to software. Custom code hinders your ability to upgrade and any changes you want to make require more custom code. That’s not sustainable and software vendors know this. Hence the shift to no-code software. Software that users can configure to best fit their individual use cases can be updated more often without breaking anything and allows for flexibility in processes. Some EQMS vendors are already offering no-code options, but one area in which this proves difficult is forms for investigating quality events. Terminology for quality events and how they are investigated can vary widely. In regulated industries, there are also requirements for handling quality events and, if a digital system is used, software validation may be required. The complexity inherently makes it difficult to use an EQMS for quality event management (QEM).
Fortunately, the trend to no-code software applies to this category. Rather than being stuck with stringent forms provided by the software vendor, the newest QEM functionality gives users complete flexibility over how they handle quality events. The workflow can be changed on the fly with a simple, user-friendly interface. When this part of the QMS is natively connected to other aspects of quality management, the interconnectivity between QEM, training, documents, etc. ensures that nothing falls through the cracks and your company can follow its own processes for investigation without being stuck with a single option from a software vendor.
The idea of being able to change workflows so easily may make you nervous if you need to meet regulatory requirements for software validation. However, this is another area where vendors are trying to make things easier on users. There are multiple ways to handle software validation, but a valuable asset to any company is the validation work that the vendor performs on its own software. Vendors are every bit as concerned with their software’s performance as their customers are. Users can take advantage of the testing done by a vendor and ensure they don’t duplicate efforts. When this documentation is available to users, there is sometimes no cause for additional testing. Even when you do need to test more, the amount of testing and time required is greatly reduced.
#3: Connected Manufacturing Data
The trend of offering ways to connect data has multiple factors. The first deals primarily with analytics. As much as everyone loves exporting their data into a third-party application to analyze it, software vendors are getting the impression there might be some who prefer to analyze it within the software. Imagine having your quarterly reports for executives generated by software in near real time with your executive team having direct access to the information via dashboards. This is quite useful in an EQMS, but the use extends beyond that with solutions that are natively connected on the same platform.
For example, a manufacturing execution system (MES) that exchanges data with an EQMS is invaluable. That connection presents a new level of control in which you can prohibit someone not trained on a procedure from filling out a portion of a batch record. Not only that, but with that connectivity the employee could access the training document that is created and stored in the EQMS through the MES interface. This would let that person immediately complete the training, get access to the related section of the batch record, and keep the line moving with minimal interruption.
Analyzing your MES data from a quality point of view can provide further insight into ways to improve quality on the line. You may determine that a certain line has fewer quality events than another which can lead to improved quality on every line. You could also find the ideal group of employees to optimize output while maintaining quality. Manufacturing and quality both generate enormous amounts of data, but when they’re combined and analyzed together both groups benefit with increased efficiencies and less friction between the two departments.
Conclusion
Manufacturers are benefitting from increased functionality and flexibility from their software vendors. This certainly makes everyone’s job easier and provides more return on investment for the company. These trends are gaining traction and will continue to do so as manufacturers invest in software vendors that are dedicated to providing a better user experience for their customers. That better user experience will naturally bring together quality and manufacturing professionals as both groups benefit from increased functionality, connectivity, and more advanced technology such as AI.