On a recent manufacturing plant tour, I came across that stack of paper that seems to be ubiquitous on make to order manufacturing lines. The hard card, or traveler or build book, has many names. And while computerizing quality management is no longer news, spending on eQMS was almost $10 billion last year and is forecast to grow at a rate of over 10% annually, that stack of papers always seems to be hanging around.
That paper is a stark contrast to the digital focus of Industry 4.0 initiatives. A Boston Consulting Group studied the use of Industry 4.0 digital technologies to transform traditional quality programs. They referred to this as Quality 4.0. Highlighting technologies such as digital twins, predictive analytics, sensors, vision and electronic feedback loops, the study showed the emerging connection between quality processes and manufacturing automation. But the study also emphasized the growing need to include a focus on frontline workers and their skills.
Quality 4.0 is emerging on the frontline for human powered processes where digital technologies are replacing those paper checklists and forms. For companies that depend on skilled workers to carry out complex and often varying tasks in the production process, digitalizing the frontline can be a game changer. There are a variety of digital technologies that are currently available as next steps to start to deliver Quality 4.0 to the frontline.
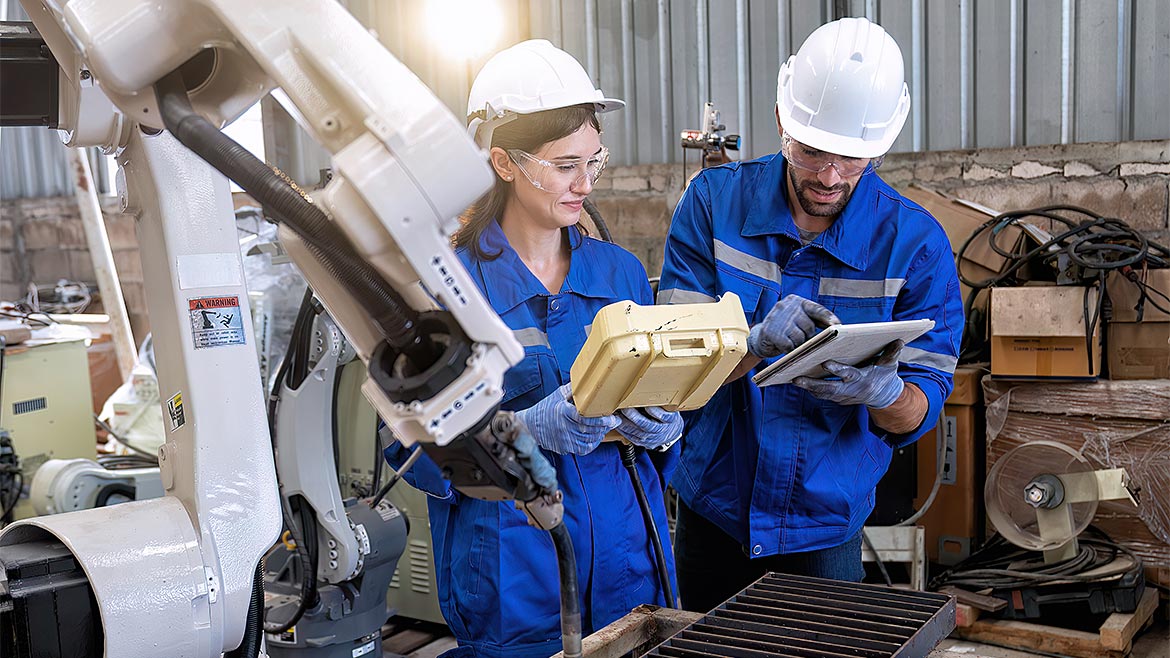
On The Spot Information And Training
A persistent challenge that impacts quality for manufacturing organizations is the recruitment and retention of skilled workers. This issue has been heightened by the pandemic’s “great resignation” and the fact that a quarter of manufacturing employees are approaching retirement. Replacing paper checklists and work instruction with digital workflows on mobile devices can transform the onboarding and upskilling process, providing immediate access to information and short, targeted bits of training often referred to as microlearning.
With today’s digital technologies, microlearning can be delivered on demand and personalized based on the process, worker activity or experience level. A study from Training Magazine found that organizations using microlearning saw a 20% increase in employee productivity and a 23% increase in employee satisfaction. Josh Bersin, a Deloitte Partner and head of their corporate learning practice, wrote an interesting article where he coins the phrase “Learning in the flow of work.” He sees the future of training as fusing microlearning into the digital platforms that workers use to get their jobs done. And he points to studies showing that 49% of workers want to consume training at the point of need.
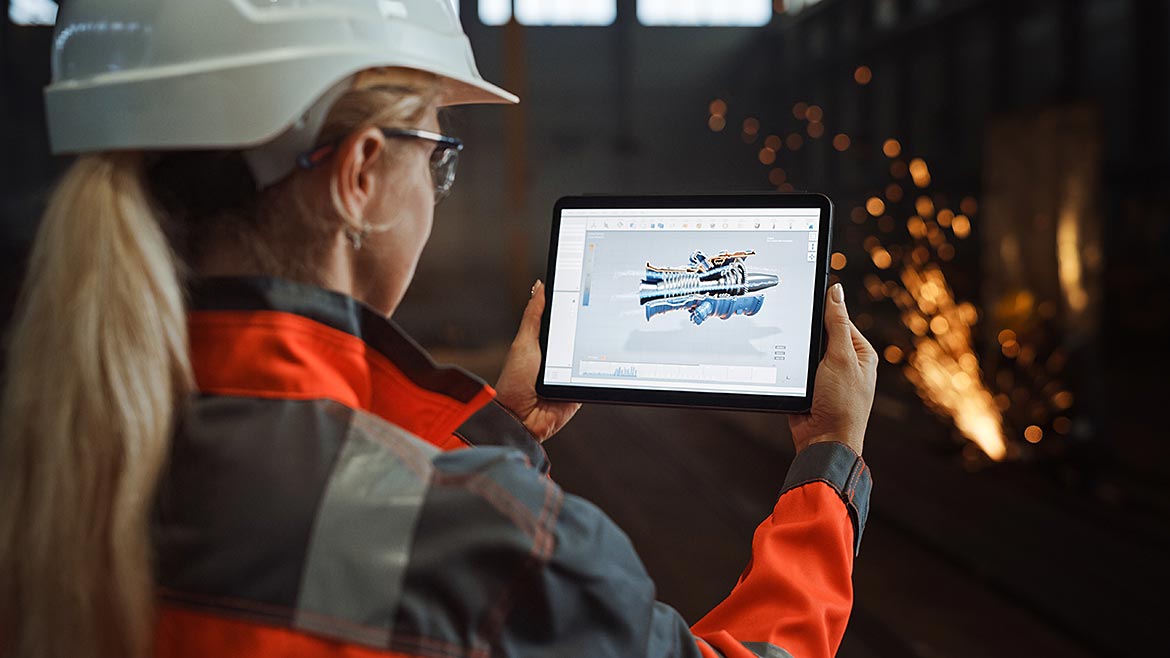
Empowering Workers Through Visualization
A McKinsey study on connected worker technologies in manufacturing found that 64% of companies implementing digital technologies on the frontline were stuck in what they called “pilot purgatory.” The major challenge to any technology on the frontline is adoption and usability. Unfortunately, most current eQMS solutions adopted designs typically used for office workers: text-based forms and PDFs. This digitized paper ignores the fact that the frontline worker and work environment are very different.
The majority of the information that a person processes - 90% of the information we send to the brain - is visual information. People process visuals 63,000 faster than text and retain 83% more information compared to text alone. Advances in visualization technology for the frontline are becoming much more accessible, whether that’s a commonly available tablet or advanced visual headset.
According to a study by PWC, one third of industrial companies surveyed planned to use Augmented Reality (AR) or Virtual Reality (VR) technologies in the next three years. Related to quality processes, visualization technologies like VR can be used for training and to simulate manufacturing processes to diagnose root cause issues or test processes before release into production.
On the frontline, AR technologies blend digital data and instruction with the actual visual to guide and direct workers, providing greater consistently and accuracy in quality processes. VR/AR are expensive and still in the early stages, but new visual interfaces on mobile devices are also able to deliver similar benefits at much lower price points. The ability to show workers the standard process and exactly how to complete the process not only supports quality staff, but also empowers workers to provide more effective self-inspections.
Delivering Remote Assistance And Collaboration
With a digitalized frontline comes the opportunity to connect workers with each other and expert assistance. Early frontline digital tools introduced chat streams where workers could share information and ask questions. The ability to share images and video is also a tremendous benefit in identifying issues and addressing corrective actions. Experienced workers can share best practices and quality teams can see issues as they are developing.
Technologies have evolved to provide more workflow specific messaging and to enable remote assistance which is facilitated through the native functions of the mobile devices. A McKinsey study pointed directly to the potential benefits of digital collaboration and remote assistance, showing an improvement in quality with the potential to reduce scrap up to 25%.
Closing The Loop On Defect To Repair
Those paper travelers have a double downside. They are a challenge to the collection and analysis of quality data, and they are also a speed bump in the production processes required to repair that defect. Days can go by while defect information is manually entered, and work lists are created. For a fast-moving MTO manufacturing line like the one I toured, phone calls and notes taped to the asset were used. They also had to employ “fixers” at the end of the line that could handle any type of defect which added cost. They also mentioned that finding skilled workers for that type of role was extremely difficult.
New solutions that digitalize the frontline are extending the capabilities of digital QMS to deliver real-time visibility to defects for product teams. Digitalized defect information can be made immediately visible to product teams, and repair and verification processes initiated through a series of digital alerts. Enhancing QMS with the new digital frontline platforms can close the loop between defect and repairs to improve production time and quality of finished product. This type of automation, enabling quality and production teams to collaborate on defect and repair, is particularly valuable in MTO manufacturing where inspection of each unit is the norm.
Bringing AI To The Frontline
AI is often spoken about as a job replacement technology. A Goldman study estimated that AI could automate up to 25% of all work tasks and eliminate up to the equivalent 300 million jobs. Yet, despite the apprehension that many frontline workers may have regarding AI technology, for workforces in manufacturing environments where variability is high and the process depends on human powered activities, AI can provide guidance and assistance in the flow of work.
Digitalizing frontline quality inspections and processes creates the opportunity to use prior inspection data to apply AI-driven predictive analytics that guide quality inspections on the frontline. Integrated with a digital platform for inspections, AI can direct attention to specific defect areas and types ensuring more effective inspections. This AI guidance also upskills the workforce, taking the place of time on the production line, enabling new workers to benefit from the experience of thousands of inspections for on-the-spot insights.
Take The Leap To Digitalizing Quality On The Frontline
Manufacturers looking at replacing paper-based quality processes are being presented with a much broader and more effective set of technologies than ever before. While digital tools are still not that common in the hands of frontline workers for quality processes, manufacturers today can look past the simple digitization of a paper inspection form and start to make bigger impacts on quality.
Digitalizing frontline quality can shorten onboarding time and upskill workforces with embedded microlearning. Next generation visualization technologies can improve accuracy and consistency with inspections and enable the decentralization of quality processes to less skilled workers. Digitally enabled collaboration helps capture “tribal knowledge” and leverages expert resources more effectively across the workforce.
And with a digitalized frontline, manufacturers can leverage the power of man and machine data for predictive issue identification and work guidance. Digitalizing frontline quality can also create closed-loop workflows that align quality and production teams to shorten production times for defect less products.
Making changes on the frontline with workers that are not daily computer users requires significant planning and change management. However, most workers are already adept users of modern mobile devices and given the benefits that can be gained in digitalizing frontline quality processes it makes more and more sense to bid farewell to those paper travelers we’ve all been accustomed to seeing.