A number of measurement devices come equipped with internal or user calibration functions. Allowing the user to calibrate their measurement equipment on a more frequent basis gives greater control over the quality process; however, with great control comes great responsibility. There are a number of considerations that must be taken into account to ensure that the operator is not invalidating the certified calibration of their equipment by utilizing such functions.
Before going further, it is important to note that calibration does not mean verification. There is no issue with a user regularly verifying the operation of their equipment, as long as no adjustments are made. An example of verification would be placing test weights on a balance before using it daily, in order to ensure the scale is functioning correctly and reading within tolerance.
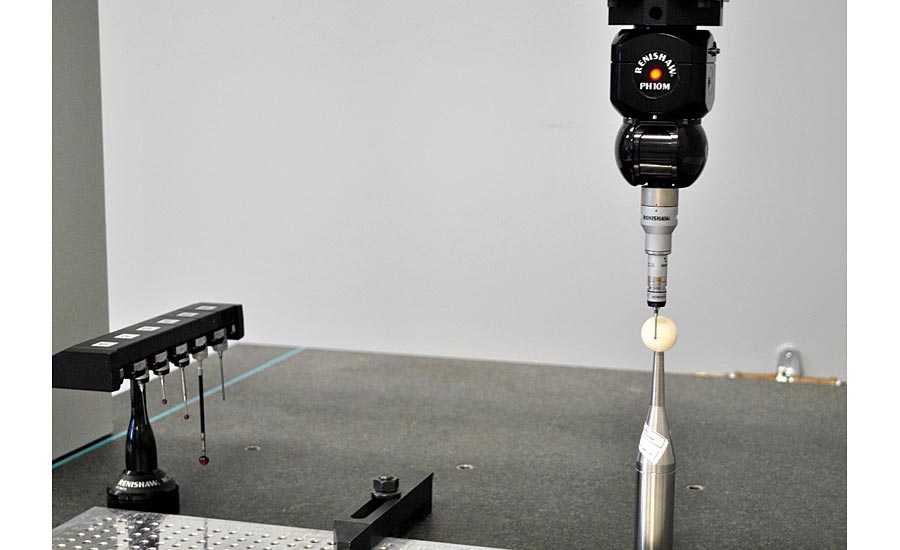
Using proper protocols when calibrating equipment with multiple probes will help ensure accurate and repeatable measurements.
Calibration, on the other hand, involves not only checking the function and readings of equipment, but also making adjustments to bring it back into tolerance if necessary. This is what inherently makes the user calibration function so risky. With the push of a button, any user can alter the accuracy of their equipment without necessarily knowing or understanding the standard to which the equipment is calibrating. When a user takes on the responsibility of calibrating their equipment with a user calibration function, they are opening the door to a variety of traceability issues which they may not be aware of, or fully equipped to address.
When used properly, however, user calibration can be a valuable component of your quality system. Precision balances, for instance, often need to be regularly calibrated due to the sensitivity of the equipment and level of precision needed for the application. Devices that utilize multiple probes such as CMMs or roughness testers should be recalibrated every time the probe or stylus is changed. Following the correct protocols for these types of calibrations will ensure accurate and repeatable readings, but should be done in coordination with periodic certified calibration to ensure proper functionality. Beyond that, there are a number of things to consider before pushing the user calibration button.
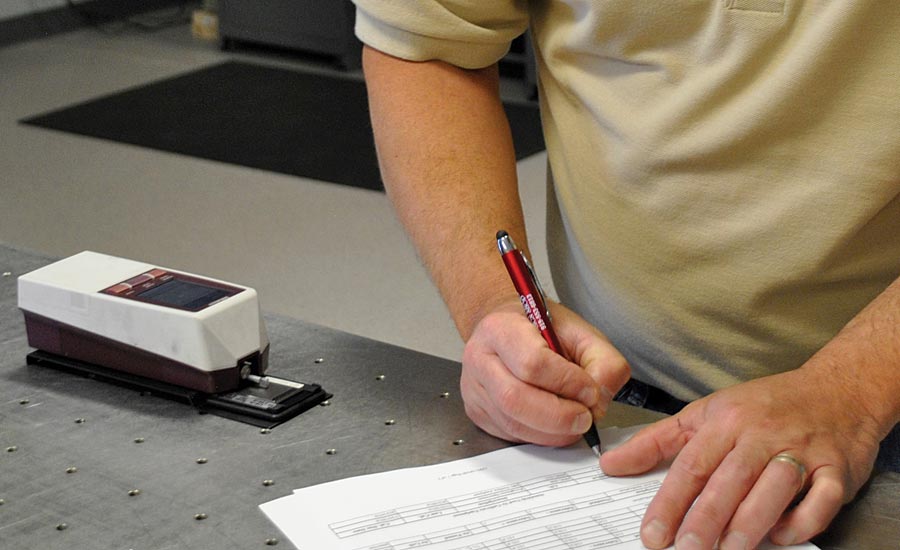
Proper record keeping of all calibrations, including user calibrations, is a critical part of your quality process.
Reference Materials
When performing any type of user calibration function it is critical to know that the reference materials being used are traceable and otherwise acceptable for the application. Regardless of the type of equipment being calibrated, there must by definition be a standard to which it is referencing. Certified Reference Materials (CRMs) are available for purchase from a variety of sources including directly from NIST. These materials used for instrument calibration have well-characterized composition and/or properties, which ensure the validity of your quality process. Additionally, knowing and understanding the uncertainty of your CRM is critical, as this can impact your calibration process. You should not be using a standard with an uncertainty larger than the allowed tolerance for your quality system. External calibration providers closely manage the traceability of their standards to ensure that they are calibrating equipment to the appropriate reference material.
Coating thickness gages, for instance, come with shims used to calibrate the equipment. Often users do not realize that these shims also require regular calibration. In the case of items such as roughness or surface finish testers, the standard roughness specimen used to calibrate the probe or stylus should also be calibrated in order to ensure traceability.
Special attention must be paid when calibrating equipment that requires the use of consumable standards. A great example would be the solutions used to calibrate pH meters. These standard solutions often have expiration dates and are susceptible to cross-contamination. Checking that the solution or other consumable CRM being used is both within its useable window and not otherwise compromised is critical for maintaining the integrity of the quality process.
Even when using scales and balances that feature internal calibration capability, there are standard-related considerations. The highly convenient internal calibration feature can be run on a daily or even hourly basis. On many models it can be set to calibrate without the user needing to even push a button. Unfortunately, this automation can easily lull the user into a false sense of security. If the internal test weights are not checked on a regular basis by a trained scale calibration technician, using the function could be doing more harm than good.
Scales and balances calibrate themselves to a set of internally mounted test weights, which like any other test weights are at risk of being damaged or changed in a way that could alter their mass. For this reason, it is critical that when the scale as a whole is calibrated by a qualified service provider, the operation of the entire scale system (including the internal calibration function) is validated. If not regularly checked, the feature should be locked to prevent use. You should communicate with your service provider and let them know if you plan to use the internal calibration function on your balance. If the scale is externally calibrated without checking the internal calibration, subsequent use of the function would invalidate the external calibration.
Record Keeping
Thorough record keeping is critical to your quality system. Certificates of calibration serve as proof that your equipment is providing you with accurate and repeatable measurements. While it may be obvious to track certified calibration events, recording user calibrations is equally important. If a coating thickness gage is calibrated daily by the user on the floor, recording the date and time of those user calibrations, as well as the CRM used is critical. When a technician calibrates a piece of equipment and provides a certificate of calibration, it only documents the condition of the equipment at that exact moment. It cannot guarantee that the equipment will stay within tolerance if the operator performs a user calibration using reference material that isn’t traceable or has an uncertainty too large for the application. To avoid potential audit findings, it is crucial that user calibrations and the CRMs used are correctly documented.

Checking that the solution or other consumable CRM being used is both within its useable window and not otherwise compromised is critical for maintaining the integrity of the quality process.
Mechanical Issues
There are two ways that mechanical issues can pose a problem for user calibration type devices. The first, and most obvious, occurs when there is a mechanical problem directly associated with the function. For instance, if the internal calibration weights in a balance were to be shifted in such a way that would prevent them from properly loading, the scale would not calibrate to the correct weight. Were the scale not regularly checked by a trained technician, it could be out of specification without anyone realizing there was an issue.
The second complication that can occur is general mechanical failure of the equipment. Though not directly related to user calibration, the practice of handling calibration by someone who has less experience with equipment increases the chances of unexpected failure. A proper calibration not only includes checking that the equipment reads as expected; a trained technician also checks the overall functionality of the device. A technician who is calibrating equipment on a regular basis knows what to look for, and can often catch major failures before they cause serious problems. Preventative maintenance is key to ensuring that measurement equipment provides repeatable and accurate measurement for years to come.
In the end, whether or not you utilize the internal or user calibration feature on your device will depend on the specific requirements of your quality system. When used properly, it can give you added control over your measurement process. However, you can cause more harm than good by failing to take responsibility for the risks associated with its use. Using reference materials that aren’t traceable, using CRMs that are expired or have uncertainties greater than the allowed tolerance, not keeping proper records, and not verifying the overall functionality of the device can all derail your quality system. Even taking these things into account, it would however be highly inadvisable to solely use an internal or user calibration function without regular calibrations from a certified provider.