Every business or service today has some form of quality control or quality assurance. With such high market competition, quality has become the market differentiator for almost all products and services.
With new technologies such as additive manufacturing being introduced more and more into different industries, it becomes harder and harder to qualify the parts for quality due to its geometric complexity. Time is another factor that manufacturers must consider, as an increase in quality also leads to slower production times.
How then, do manufacturers assure the quality of their part in a way that is accurate, reliable and fast?
One industry that has grown alongside every manufacturing industry from aerospace, castings, automobile, to now additive manufacturing is the nondestructive testing industry, mainly digital X-ray. Digital X-ray is sought after by many manufacturers today due to its versatility and provides more capabilities than any other type of nondestructive testing. It has live viewing capabilities, can store images and provides fast and accurate inspection capabilities, all in real time.
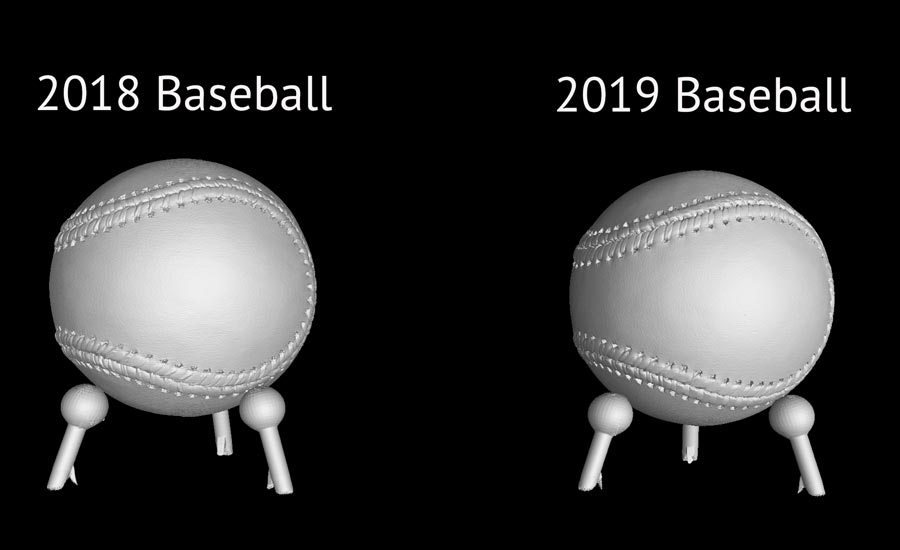
Digital X-ray can provide 2D scans (digital radiography) as well as 3D reconstructions (computed tomography) of a part. Depending on a manufacturer’s part and preferences, digital radiography or computed tomography is used. If a manufacturer wants to see exactly where the defect is in the part, computed tomography is the right method to use.
Computed tomography is unique because it provides a user a way to inspect the part without destroying it. Just like with medical CT, industrial CT works in a similar fashion. By utilizing the penetration capabilities of X-rays, the technology generates cross-sectional images of the object for detailed analysis. Because industrial CT is digital and is done on the computer, it can provide the inspection specialist with a wide variety of tools to inspect the part. The specialist can look for defects and voids, measure distances, and locate the problem areas in hard-to-access components.
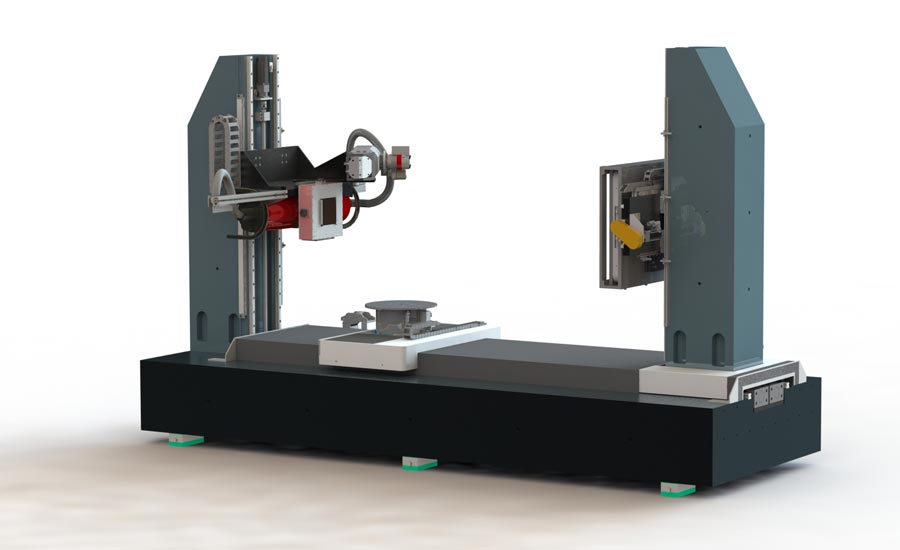
In order to conduct a computed tomography scan, a trained NDT radiographer must be present to prepare the object for scanning and calibrate the system in accordance to the purpose of the scan.
2D vs 3D imaging. What’s the difference?
Traditional 2D imaging produces X-ray images where all the internal components overlap. In comparison, computed tomography provides clearer images without the internal structure overlapping. The overlapping can be confusing, and the operator may confuse an overlapping area for a defect. By being able to view each individual slice, defects can be spotted much more accurately. In addition, computed tomography allows the user to view the part at any angle in the system, as well as remove certain areas to expose areas of interest.
How does Computed Tomography work?
In order to conduct a computed tomography scan, a trained NDT radiographer must be present to prepare the object for scanning and calibrate the system in accordance to the purpose of the scan. Each unique part that is scanned generally will have its own imaging technique.
Although the technique varies from part to part, generally there are common steps a radiographer takes to conduct a CT X-ray scan:
First, the radiographer will match the part size and material to the appropriate X-ray source with high or low energy levels depending on the purpose of the scan. Being able to adjust the power and visually see how it penetrates the part in real time is a tremendous time and cost saver. Based upon the counts which displays the gray values, the radiographer can increase the X-ray so that it penetrates the part fully and reveals the internal components. Just like with cameras, one can expose the part for a certain period to allow the X-rays to penetrate more, even if the energy level is low. This is known as the integration time.

Computed tomography is an extremely powerful nondestructive testing method because it gives you the ability to visually inspect parts, automate the process and provides more than just a pass or fail qualification.
The radiographer needs to make sure that the X-ray level is not too high, otherwise there is a risk of oversaturating the flat panel detector (the device that converts X-rays into digital signals and thus into an image). If the panel is oversaturated, the screen will be white or overblown. Just like with a camera, if the shutter is exposed for too long, the highlights are overblown.
Once the right energy level is acquired for the application, the part is placed on a rotary table which is located between the digital detector panel and X-ray source.
This technique comprises of part or source orientation, energy level and/or filters to only allow only the high energy X-rays through.
CT imaging begins with the acquisition of projections, X-ray images captured by the image detector during X-ray generation. The most popular way computed tomography is done now is something called cone beam CT.
The way computed tomography works is by hitting the object with X-ray beams from an X-ray source. The power level needed depends upon the part thickness and density. As the X-ray penetrates the object, the object rotates on the rotary table—located between the digital detector panel and X-ray radiation source. The varying density of the part absorbs varying amounts of radiation. The remaining radiation travels to the detector panel, which captures a 2D X-ray image. The imaging detectors can be configured to capture images at various frames per second as well as synchronize with the rotational stage motion control unit.
This allows for various configurations of the number of acquired 360-degree rotations (360 projections, 720 projections…). Generally, a faster acquisition frame rate results in reduced image quality. Ultimately it depends on the user and what level of detail they want to see.
The captured images are reconstructed mathematically to develop a 3D model of the part. This model is used for further internal and external analysis of the part, whether it is to identify internal defects or to conduct dimensional analysis.
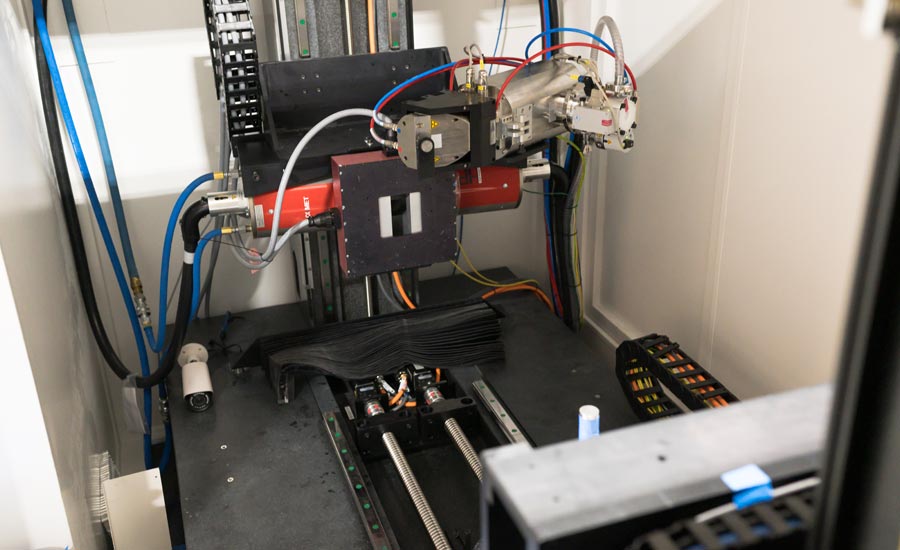
What determines X-ray Computed Tomography image quality
In order to achieve the highest quality and sharpness, a few things need to be considered:
The size and shape of the part being tested – If the object being scanned does not fit in the detector panel, the resulting image will not reflect the object in its entirety. In that case, this will mean more projections are needed to capture the entire object or a larger detector is needed. On the other hand, if only a certain area of interest is needed, it may not be necessary for the subject to fit the detector panel size range.
Orientation of the X-ray source subject to the part – The distance of the X-ray source and the part plays a significant role in determining the accuracy and the quality of the image. The closer the object is to the detector, the sharper it is.
Material of the part being scanned – Density of a part determines the quality of the resulting scan. The higher the density, the more exposure of radiation is required to evaluate internal features. With a lower density object, less exposure is needed. If too much exposure is passed through a low-density material, the resulting effect will show scatter marks on the image. If the exposure that is passed through the material is not adequate enough, viewers will not acquire accurate data.
Length of Scan - Depending on the purpose of the scan, the amount of 2D cross sectional slices can be determined. If not enough slices are captured, the resulting image or reconstruction will not display a highly accurate result. The radiographer must factor in how much time can be allocated towards the scan.
Other factors – Other factors that are crucial in determining image quality are corrections (scatter correction, artefact reduction, etc.), calibration and precision of mechanical subsystems, focal spot size, pixel pitch, among several others.
Computed Tomography Reconstruction and Visualization
Once the technique is found, the CT reconstruction requires powerful computing power. The acquired projections are processed with special software algorithms in order to reconstruct these cross-sectional images. The benefits of being able to reconstruct parts on a computer is that it can be stored and transferred to a database where a visualization software can analyze it. The visualization software enables you to view the reconstruction slice by slice, segment out areas of interest, and perform different analysis and metrology. These kinds of tools that enable you to view parts to such a degree helps make the entire manufacturing process more efficient. Parts can be sent out knowing there is no internal defect with pass and fail algorithms.
Computed tomography is an extremely powerful nondestructive testing method because it gives you the ability to visually inspect parts, automate the process and provides more than just a pass or fail qualification. It provides deep insight not only into your part but also the entire manufacturing process. Q