The COVID-19 pandemic has created an unprecedented surge in demand for healthcare and consumer products. This crisis has demanded stockpiles of supplies and has shifted the supply chain to local production. Manufacturers of masks, ventilators, sanitizer, wipes and other essentials have ramped up production to meet an overwhelming demand. Manufacturers that typically make other products have stepped in to help with the crisis.
It is important not to overlook the quality assurance (QA) process to ensure that these essential products comply with all specifications and standards prior to delivery to the customer. Force measurement is an important characteristic in meeting the requirements of a quality product. A universal tester can produce a force measurement that will determine whether the product is acceptable. Let’s take a look at some applications related to product testing of essential goods and supplies:
Tensile Testing
Many materials need to be tested for tensile strength. A tensile test involves stretching or pulling a material apart. The results of a tensile test will ensure product quality. Disinfecting wipes are a popular product that can be tested for sheet strength. Consumers and medical personnel want wipes that tear easily before they are properly removed from their container, but still maintain enough strength not to fall apart during use. The strength of a wipe can be assessed by gripping the product on the top and bottom edges and pulled to failure. The fabric of hospital gowns and scrubs can be testing in a similar manner. The elastic bands for masks continue to be tested for tensile strength. Sanitizer is often sold in a flip cap bottle, which includes a small tab that must be flipped up to dispense the product. The force to move the tab up and down must be measured to ensure that the cap is not too difficult to open, or too loose where it might cause a spill. Additionally, nasal swab sticks, ventilator tubing, sutures, packaging films, and medical packaging boxes require tensile tests.
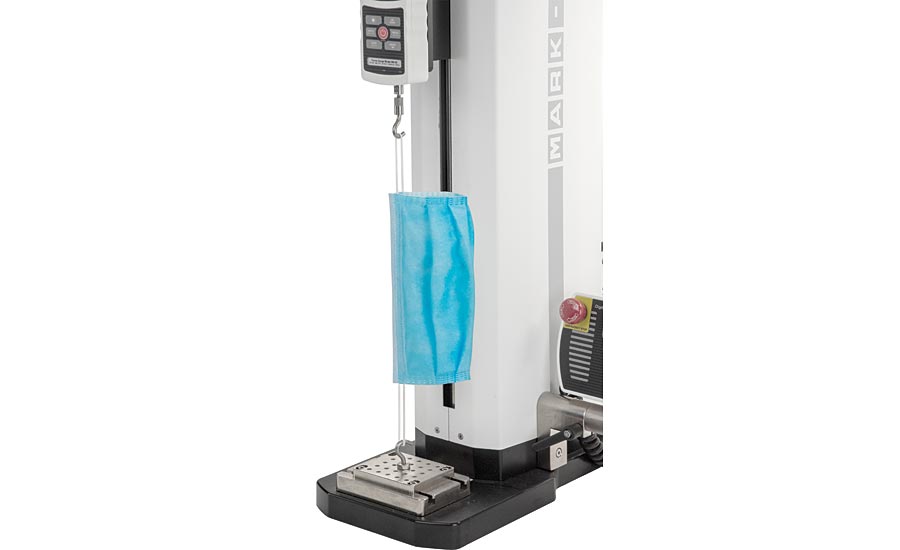
A medical-grade surgical mask is tested using hooks.
Compression Testing
Compression tests are conducted to evaluate specimens by crushing, pressing, squashing, or flattening them. These tests are often conducted to establish a breaking force or limit. Needle syringes are tested for compression force using specialized fixtures. A compression plate presses down on the plunger of a hypodermic syringe. With an appropriate testing system, initial and secondary peaks can be measured. Soaps and sanitizers are often packaged with a pump dispenser. The compression force of such a dispenser needs to be tested to ensure it is suitable for human use. The downward force needed to press the pump is measured to ensure that the liquid can be pumped properly.
A Universal Test Machine (UTM)
Measuring force in either tension or compression is achieved with a universal test machine and force measurement instrumentation. A complete system consists of a force gage or load cell, test stand, grips and/or fixtures, analysis software, and a safety shield. A UTM will allow a material or component to be tested to determine if the sample meets acceptable force limits, consistency in manufacture, and design criteria. Conducting these tests can also reduce costs and ensure compliance to industry standards, which is especially important in the medical industry. The equipment needed to conduct these tests is made up of the following components.
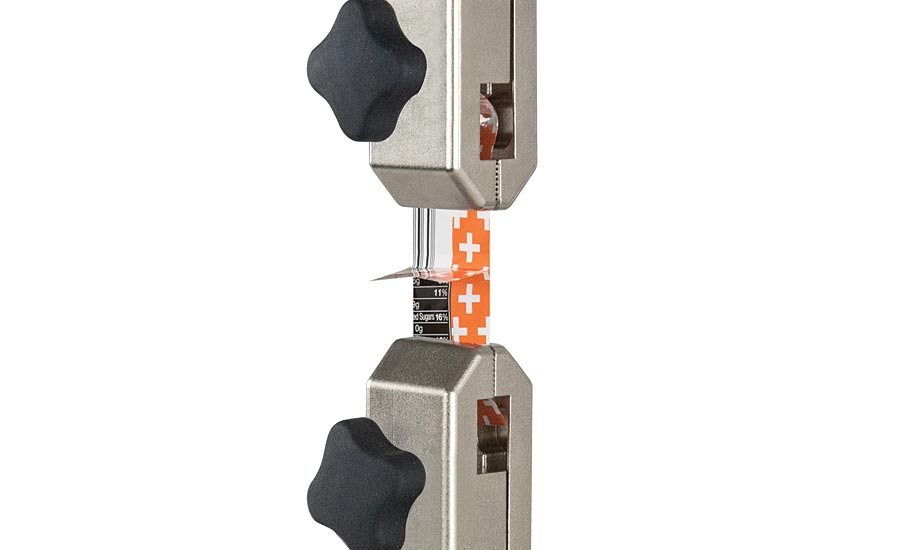
An example of peel testing with manual grips.
Force Gage
As the heart of every measurement system, the force gage or load cell translates force into an electrical signal. Strain-gage based load cells utilize the Wheatstone bridge concept, which consists of a network of four resistive legs. When a change in strain occurs, a change is resistance will result, producing a signal that can be processed and converted into digital form. The result is displayed in force units such as lbF, kgF, N, or kN. A load cell can be used in conjunction with an indicator to display the measurement reading. Load cells are frequently integrated into a force gage in many UTMs. It is best to choose a force gage between 10% and 90% of its range to optimize its accuracy.
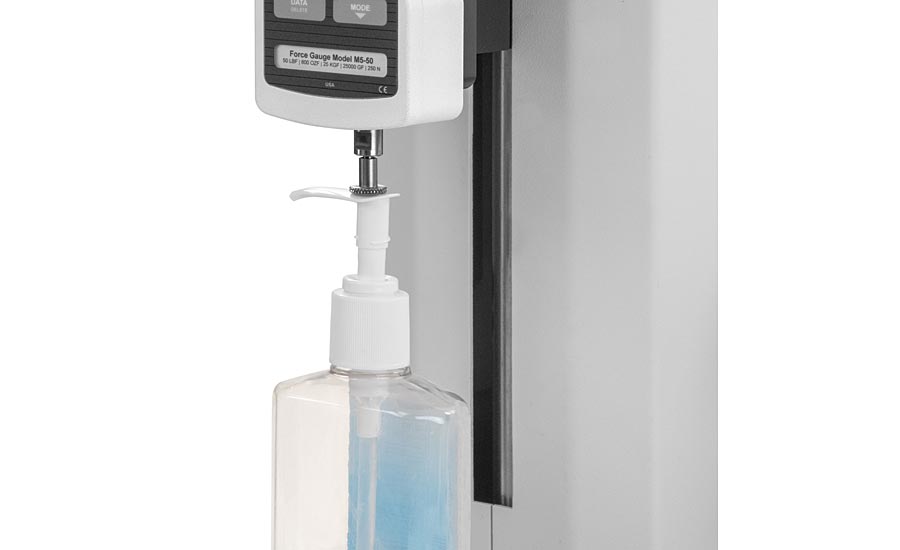
A sanitizer pump dispenser is tested in compression.
Test Stand
A test stand produces the force necessary to test a specimen in tension, compression, or bend. A motorized test stand offers ease of use and repeatability. Test stands are offered in either single or double column configurations. A single column tester is most often utilized for low force application, generally up to 2000 lbF. Single column UTMs are often used in a lab or production environment.
High force applications require the use of a double-column UTM. A double-column UTM can be floor mounted for heavy duty testing or bench-mounted for lab use. Heavy duty machines are actuated hydraulically, while standard UTMs are driven by one or two lead screws. If samples are tall or have high elongation properties, a custom test frame might be required.

A syringe is tested to determine plunger force activation.
Distance Measurement
An integrated encoder or linear scale is used to measure stress, strain, and percent elongation. It is also necessary to measure the travel or sample elongation when creating force-distance plots and stress-strain curves. When there is a small deflection, an extensometer is used to produce accurate measurement and better resolution by clipping onto the specimen. Dynamic and static extensometers are available for different applications. Hydraulic test systems often an employ a linear variable differential transformer (LVDT) displacement transducer to measure displacement.
Grips/Fixtures
A wide range of grips and fixtures is available for testing a plethora of materials, but choosing the correct grip is of utmost importance. If the grip is not suitable for the material undergoing testing, the material will slip and testing will be unsuccessful. It is also important to estimate the maximum force capacity for your test before choosing a grip, as each grip has a specified use capacity. Wedge grips are generally used for rigid metal or plastic samples. Parallel jaw grips are versatile and can be used to test fabrics, films, and semi-rigid materials. Wedge and parallel jaw grips can be fitted with various surfaces: plain jaws, serrated jaws, interlocking wave jaws, and rubber jaws. Wire and rope grips are available to test wire, rope, yarn, tubing, and elastics. Specialty opening force fixtures enable to the opening force of box cartons to be measured. A flip cap grip can be used to engage a flip cap tab for pull testing. Specialty fixtures such as a syringe compression fixture conform to relevant ISO standards to allow for medical testing of a syringe plunger. Basic attachments such a simple flat attachment, a compression plate, or a hook enable a variety of material and product tests.
Enclosure/Safety Shield
It is not only good practice to use a protective device such as a safety shield during force testing, it is often required by safety guidelines. A safety shield will provide pinch and sample debris protection for the operator, as well as protecting limbs, hair and clothing from entanglement. Some UTMs feature environmental chambers that are used for testing materials throughout a wide range of temperature and humidity requirements.
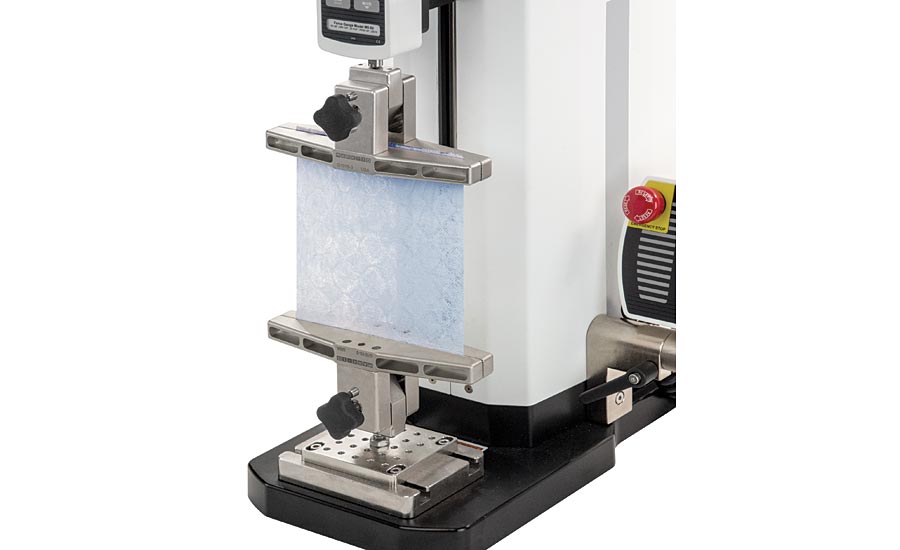
A tensile test is performed on a disinfecting wipe.
Analysis Software
With increased production demands and validation needs, recording data is becoming more important than ever. Today’s force measurement systems allow results to be sent to a PC for analysis and reporting. Tables and charts can be provided as well as graphs representing stress vs. strain and force vs. distance or force vs. time. Additionally, spring rates, Young’s Modulus, and other calculations can be performed allowing for discernable results.
Conclusion
The new normal has created demand for an adequate stockpile of healthcare and consumer goods as well as a focus on product testing. Accurate force measurement provides the quality assurance team with the data they need to ensure a supply of high-quality products that can go to market quickly. Q