In many industries, color stands for quality. Particularly in the case of consumer goods that reach the end customer, the exact color shade influences the value and identity of the product and the brand. Therefore, it is crucial to hit the right color tone in the production process and to produce it homogeneously across numerous batches. Color not only leaves an impression of quality, but can also be used as an indirect variable to control the process. For example, color sensors are used to monitor adhesive beads, sort parts or determine active ingredients. In most cases, color sensors are the more cost-effective solution because they offer higher precision than conventional switching sensors.
Various Sensor Types To Precisely Detect And Measure Colors
Color is (in physical terms) a reflected intensity spectrum in the visible wavelength range. This reflection spectrum depends on the object color and the illumination. Illumination is defined by different light sources, e.g. light bulbs, daylight, fluorescent lamps or cold white LEDs. A color sensor detects the reflected spectrum and imitates the principle of the human eye. Therefore, the reflected light is refracted into its spectral parts. The easiest method is to use filters where only one part of the spectrum can pass through. The following products have proven their worth in precise color recognition and measurement.
True Color Sensors For Precise Color Recognition
True Color sensors are based on an accurate color recognition principle. The specimen is illuminated by a light source, which in most cases is a white light LED, via fiber optics. The light reflected by the sample is transmitted via fiber optics to the controller where the light passes through three different filters and eventually reaches a light-sensitive sensor element. The filters divide the light into long-wave (X), medium-wave (Y) and short-wave (Z) parts. The individual signals are then transformed into L*a*b* color values. This is how measurement values are generated which enables the assignment of colors according to the color perception of the human eye. Therefore, we refer to these as perceptive color sensors or True Color sensors. They are ideally suitable to recognize deviations from a reference color. A teach-in function enables the user to program the desired color on the sensor and to define the maximum permissible color deviation. The sensor rapidly compares the color of the products during operation and sends for example a signal via a digital output if the color of the specimen is within the tolerance limits.
So-termed color groups imply another useful feature. The user can teach several color distances to the controller and group them. If the distance from the target changes and therefore also the recognized color, the latter may be contained in one of those groups and so is in the defined tolerance range.
Color Spectrometer For High Precision Color Measurement
Another functional principle is applied by color spectrometer measuring systems. This divides the spectrum of the incident light via a refraction on a grid into 256 parts, which are imaged behind the grid onto a CCD sensor line. This is how the complete visible spectrum can be accurately measured with a spectral resolution of 5nm. The color measuring system not only compares the colors to reference values, but also identifies and outputs individual colors as coordinates in the color space. As well as the sensor system, the white light LED is incorporated into the controller, enabling different sensor heads to be connected via optical-fiber cables.
For conventional measurement tasks, illumination and receiver are either arranged at an angle of 30°x:0° or 45°x:0°. This leads to observation distances of 50mm or 38mm respectively.
For more complex measurement tasks e.g. with structured, highly reflective or shiny metallic surfaces, a circular sensor with 24 circular arranged lighting optics at a measuring angle of 45°c:0° is used. This ensures continuous, homogeneous lighting for measurements, regardless of the angular position of the target object. Even with smaller measurement objects or on curved surfaces, reliable color measurements are possible.
For color measurements of transparent objects such as film or glass, a transmission sensor is required where illumination and receiver are arranged at an angle of 180°:0° to each other. This receiver sensor also measures colors of self-luminous objects. No lighting unit is required.
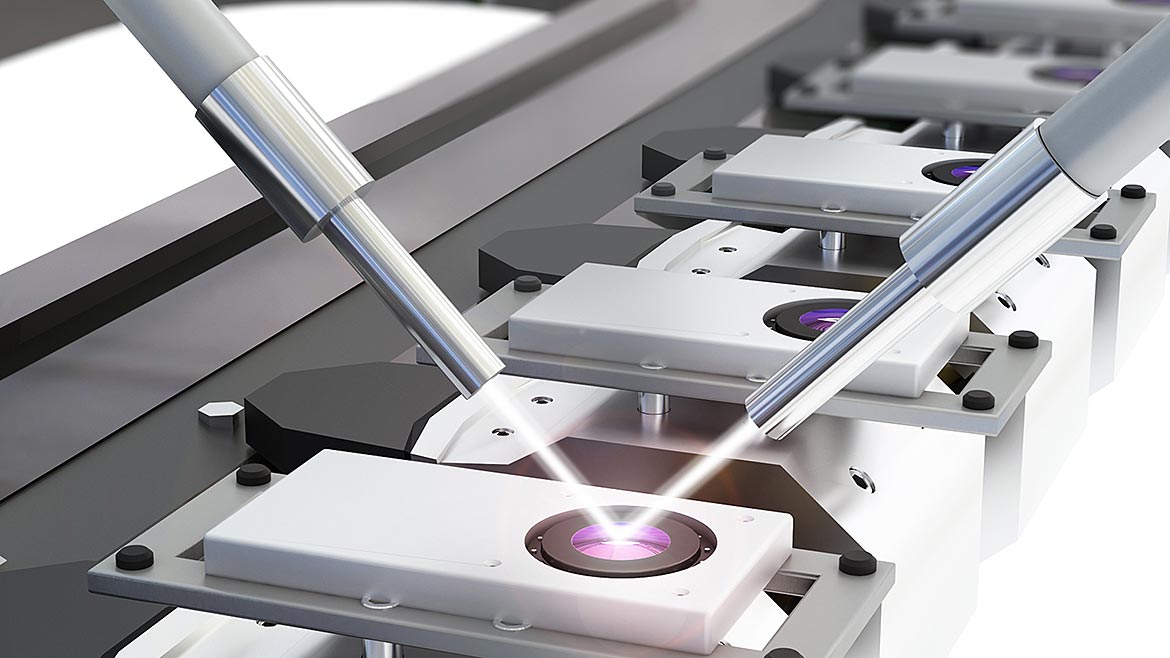
Detection of anti-reflective coating on lenses
Detection Of Anti-Reflective Coating On Lenses
The anti-reflective coatings of lenses and objectives must be applied evenly, otherwise color gradients can occur that impair their function. To check the visual color impression (green-blue for high-quality coatings) and thus the quality of the coating color sensors are used. The color sensors detect the color reflection of the lenses by means of the sensor head (total reflection; angle of incidence = angle of reflection). Due to the high resolution, even slight color variations are reliably detected.
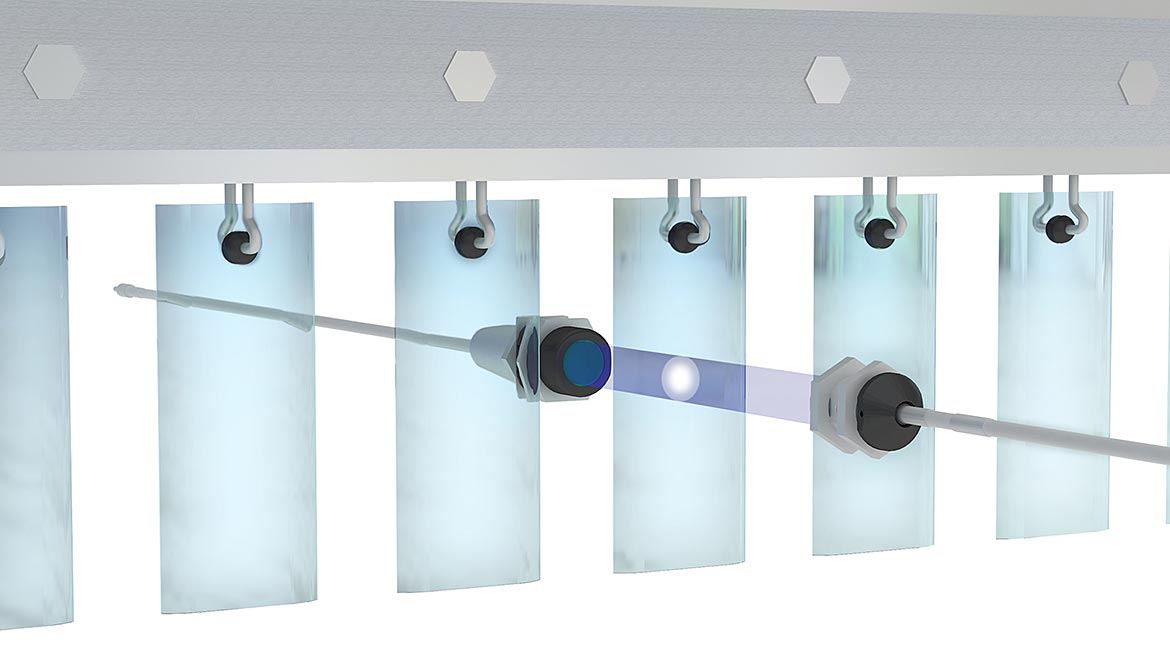
Control of the color tone of flat glass
Control Of The Color Tone Of Flat Glass
Color sensors measure glass color and glass tint in the manufacturing process. The color measurement system in combination with a transmitted light sensor head detects the exact color tone of flat and display glass and outputs the color values to the higher-level control system.
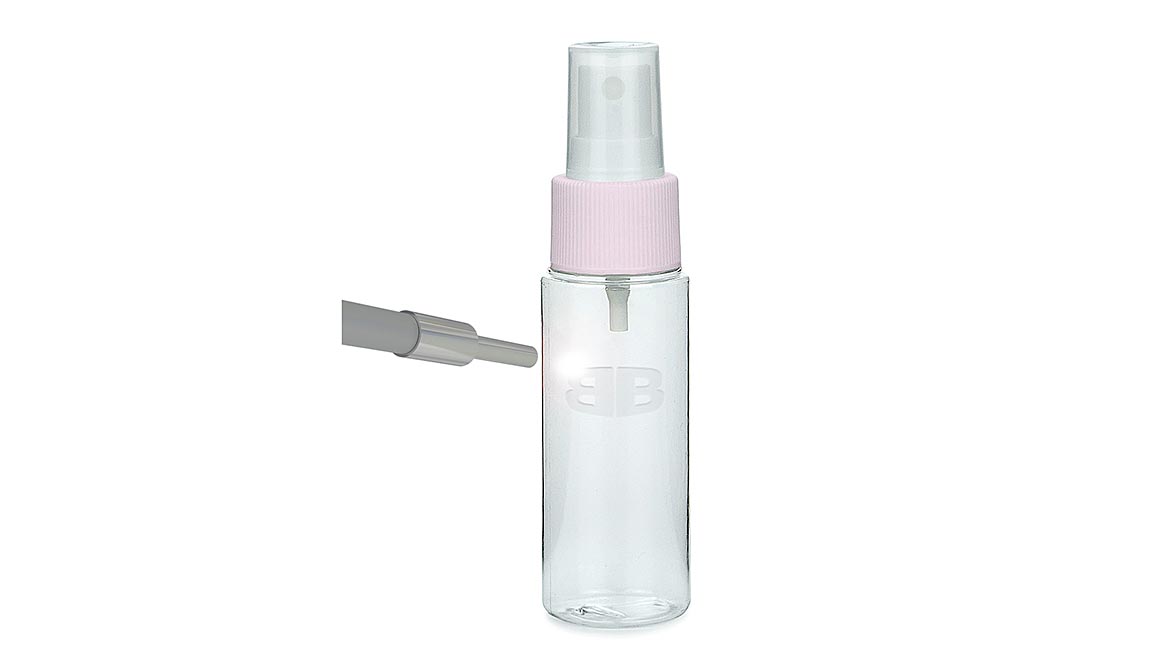
Marking detection on cosmetic bottles
Marking Detection On Cosmetic Bottles
Color sensors are also used for detection, inspection or positioning tasks. When printing semi-transparent glass ceramic bottles automatically, it is necessary to determine the exact position for printing. Before the printing process, a position mark is embossed into the bottles. The color of the embossing deviates slightly from the rest of the bottle surface. The sensor detects this color difference and thus enables the exact determination of the printing position. If the mark is missing, the bottle is considered faulty and is rejected immediately.
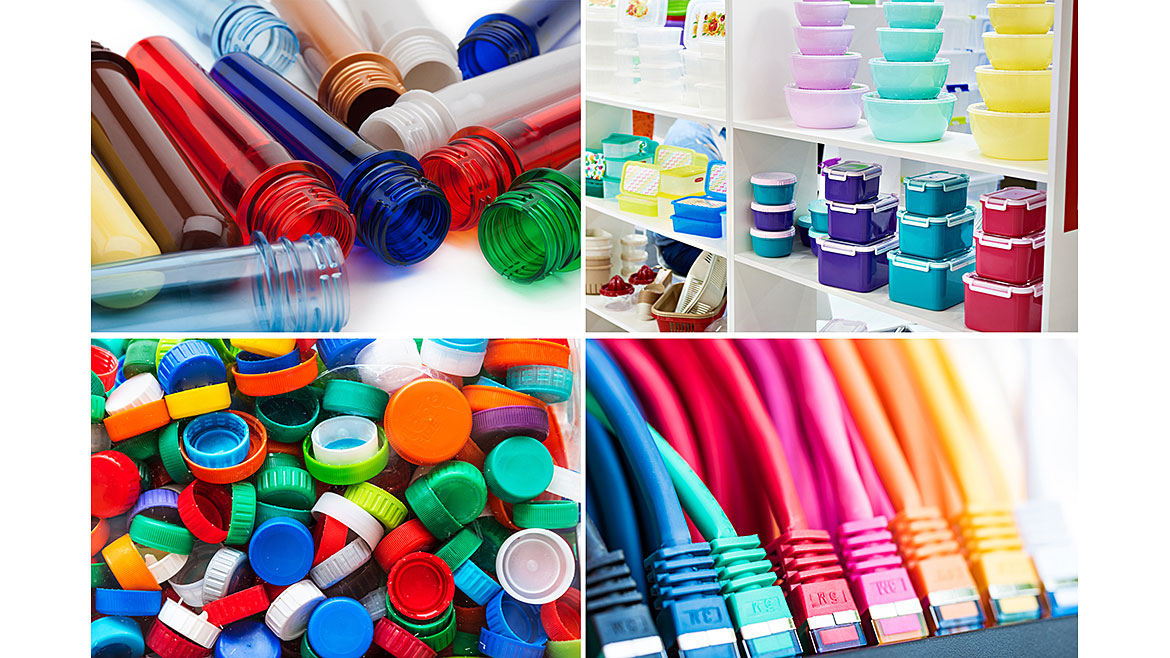
Sorting of plastic components
Sorting Of Plastic Components
Particularly with automated mounting, components must be sorted according to their color. With high measuring rates up to 30 kHz, smart color sensors are used for sorting different plastic components. Adjustable colors and tolerances enable high flexibility for the measurement task.
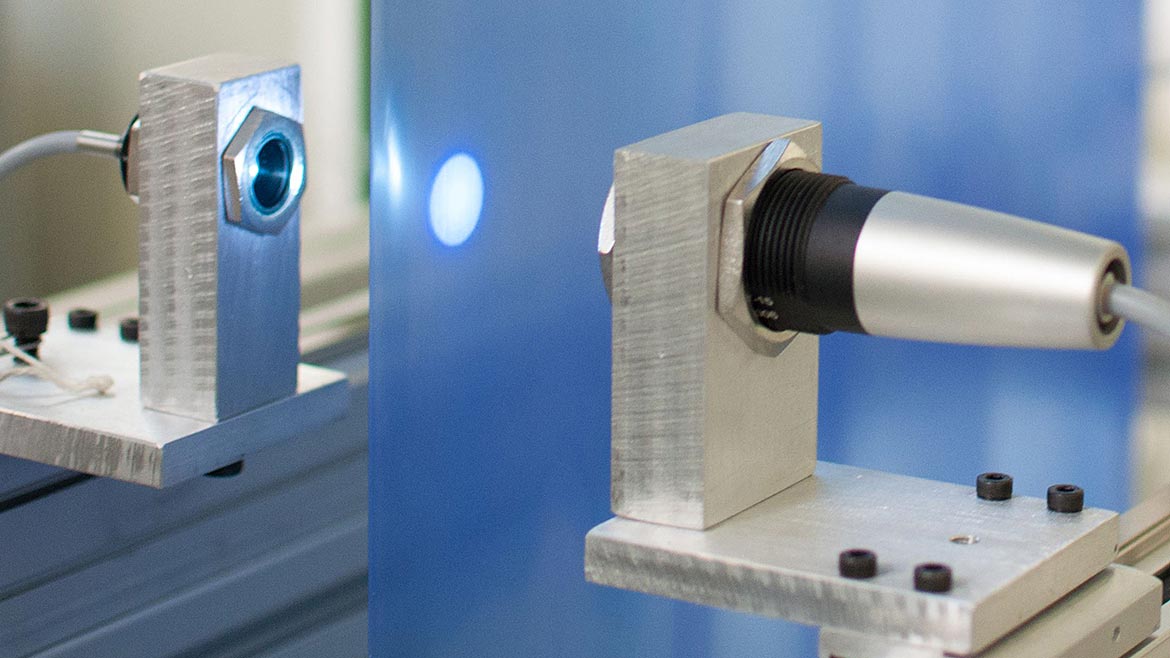
Inline color measurement of transparent films
Inline Color Measurement Of Transparent Films
In addition to color variations, streaks can also occur during production. The color homogeneity of transparent film strips is monitored inline without contact. Since transparent films are translucent, the color is measured in transmission, i.e. a transmitter illuminates the receiver and the film in between. This is measured with a high-precision inline color measuring system connected to a transmission measuring head consisting of a transmitter unit and a receiver unit. This system enables the early detection of slight color changes and streaks so that the production parameters can be adjusted accordingly.
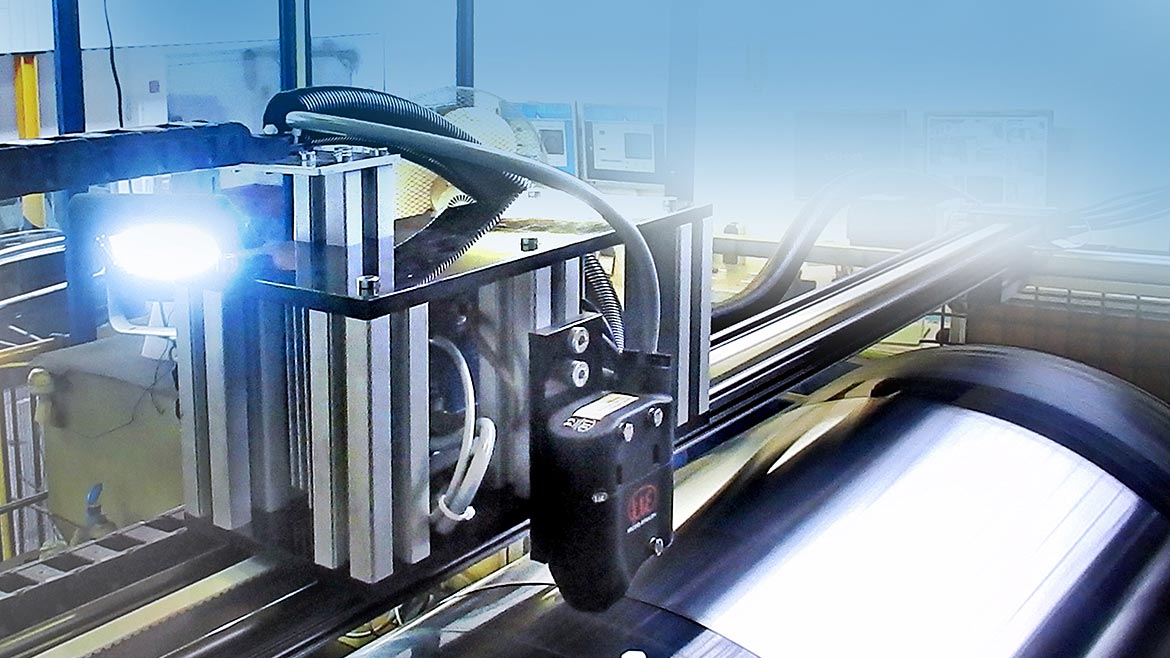
Measuring the zinc strip color in production
Measuring The Zinc Strip Color In Production
In the production of high-quality material strips and boards made out of titanium zinc, the surfaces receive specific treatment. So the strip receives defined coloring. For color inspection, color spectrometers are used to monitor the color shade in the running production line with high speed and high accuracy.
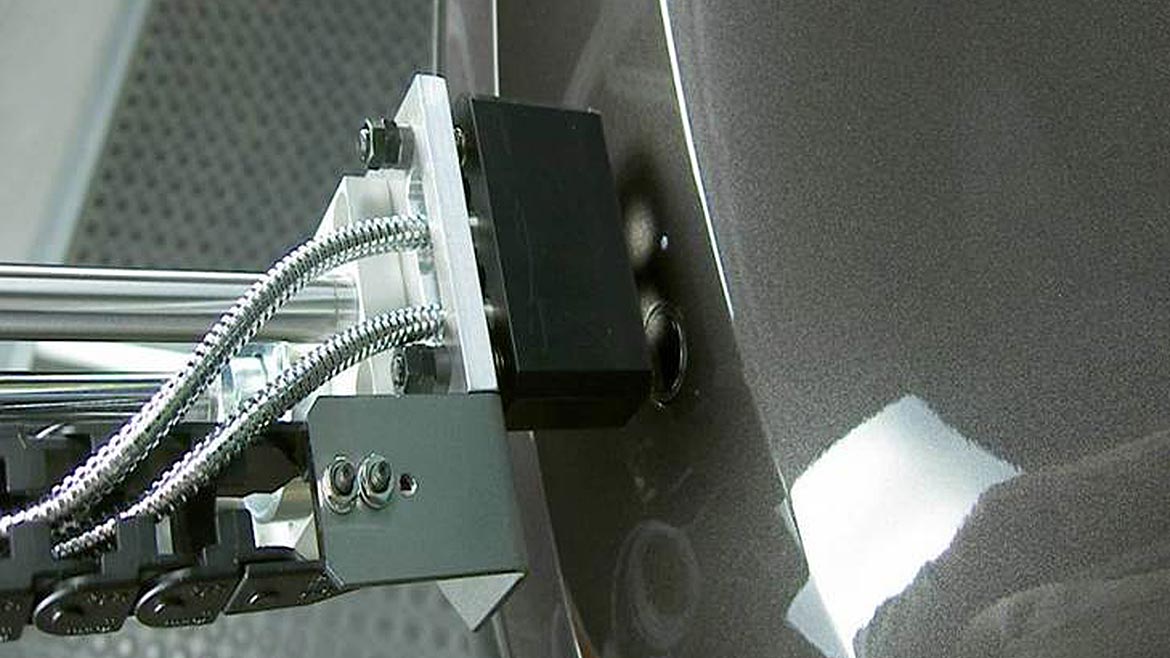
Comparing colors of parking sensor and car body
Comparing Colors Of Parking Sensor And Car Body
Car attachments such as parking sensors are painted separately. In the assembly, the color of the parking sensors must match the car body color, i.e. the color difference must be equal to zero. The True Color sensors enable a direct color comparison between the parking sensor and the rear bumper. The sensor issues a ‘NOK’ signal if the colors differ and an ‘OK’ signal if the colors are identical. The colors don’t have to be taught to the sensor. The user simply needs to define the maximum color difference between the two color channels.
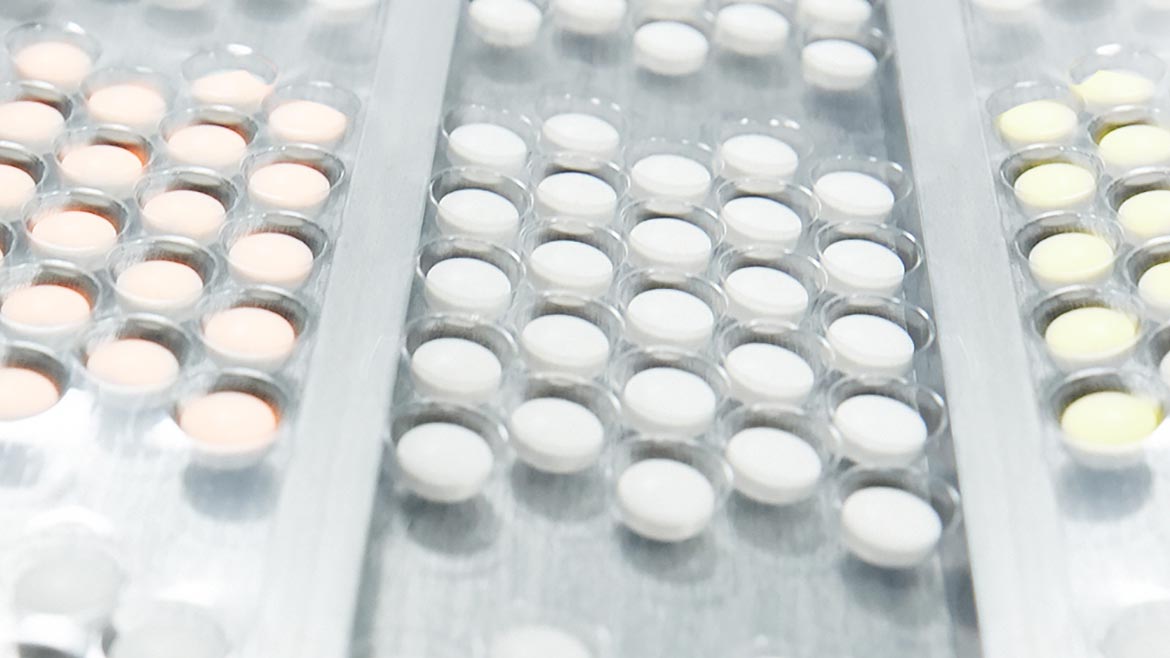
Color measurement of tablets in pharmaceutical production
Color Measurement Of Tablets In Pharmaceutical Production
In vitamin tablet production, different ingredients are used. The tablet color depends on the concentration of ingredients and might vary from pure white through to beige and yellow. An inline color measuring system with a 30° sensor head accurately measures the slightest color differences, particularly those finely-graded color shades between white and beige. This color information provides a statement about the quality of the ingredient composition.
How To Measure Colors Correctly?
In order to receive constant results, a reproducible measuring method with the following conditions is required:
- The sample surface must be as clean as possible. Fingerprints, scratches, dust and residues of cleaning agents distort the measured results.
- Curved surfaces: always measure at the same location on the target with the least amount of curvature to achieve a reproducible result.
- Make sure that the sample is optimally positioned. If the distance from the sample changes slightly the measurement results will be influenced.
- Constant surface temperature is important for comparable results as different temperatures can lead to deviations. Samples in best quality should be qualified as representative master.
- Regular calibration is a prerequisite for reproducible results and should be performed under the same ambient conditions prevailing during the subsequent measurement.