Modern engineering quality software must have its foundations in fundamental software best practice. For solutions in the realm of quality assurance, the software component of a hardware system is becoming the enabler, and as such should be carefully considered when initiating or adding to an organization’s toolset. Here we review essential software specifications and cover how those attributes can be leveraged when considering computer-controlled physical product testing equipment in the lab or on the shop floor.
In today’s market, the manufacturing sector is becoming increasingly data-driven and digitized. Even the smallest, specialist organizations are having to embrace the principles of Industry 4.0 to remain agile and competitive. No matter how experienced a business is in its unique sector, it must evolve to keep its reputation and ensure its survival. Software is often the enabler in meeting this challenge—either in enhancing existing tools or extending the connectivity and communication of data to other areas within its business or external supply chain.
Software Quality Fundamentals
There are several established standards for ensuring the definition of a piece of software is ultimately fit for purpose. A set of core attributes are used to verify a software design workflow from specification to delivery. A selection of those are as follows:
Functionality — Features which guarantee the software functions to predefined specifications. This is the basic requirement that it meets the needs of the business and does what it says on the tin (or the installer).
Usability — Attributes geared to aspects ranging from operability to error protection to UI and aesthetics. The target audience’s abilities and needs must be explicitly met to eliminate user error, the one aspect beyond the software’s direct control.
Compatibility — The degree to which a software system or its component can exchange data with other systems or perform while sharing the same hardware or software environment.
Flexibility — The ability to adapt to future changes—future-proofing—whether that’s user behavior, technology trends or any other external factor that may be reasonably predicted to have an impact. Scalability, maintainability and modifiability are closely related terms.
Security — Encompassing confidentiality, accountability and integrity; in its purest form, this covers internal application elements such as users, admins, permissions, audit trail and events logging. This capability is gaining importance nowadays with the need to be secure against malicious viruses and users.
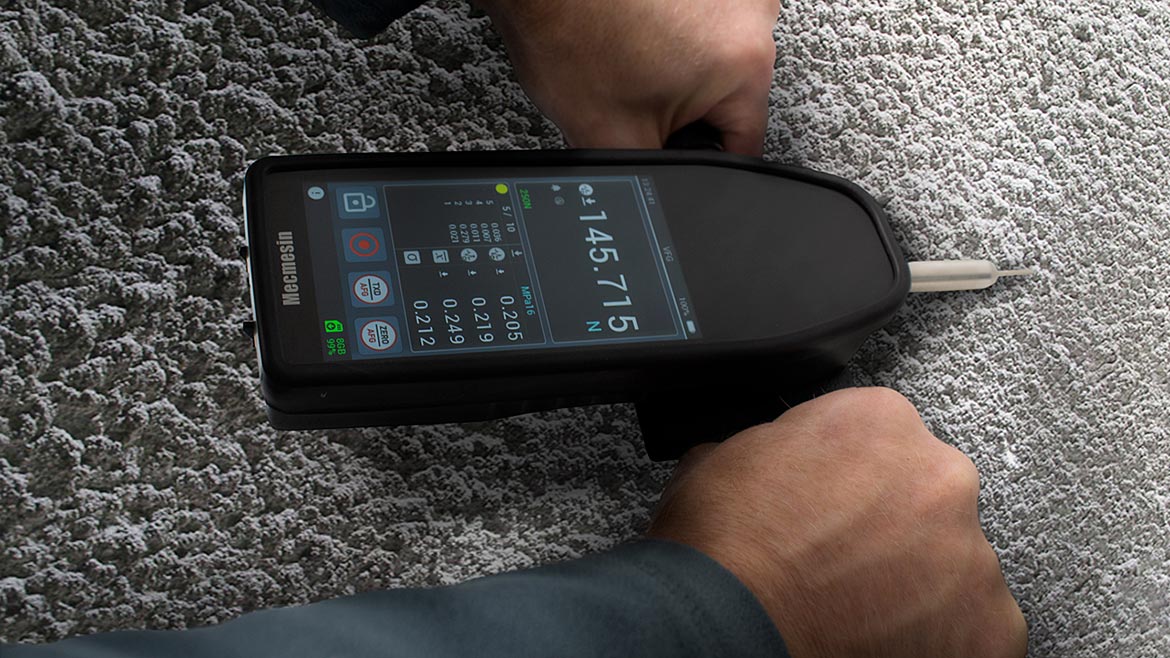
Quality testing may need to be performed in the field. A VFG Shotcrete Penetrometer is used at concrete spraying construction sites and its in-built software performs industry standard calculations from measured data—just the specific functionality required. In a rugged instrument, a modern touchscreen interface and UI maximizes efficiency. | Image Source: Mecmesin, a PPTGroup company
Developing Beyond The Basics
For any organization to implement a software solution to the benefit of their business, the specification and purpose (functionality) is the unique element that defines the job to be done. Internal and external factors can drive these requirements. In-house expertise and the desire to automate USPs protects and enhances what a company already does. Certain industries, however, have external demands that may be crucial for operating in those industries; compliance drives the software specification. Safety-critical sectors and those dealing with cutting edge technological challenges are prime examples—aerospace, defense and the medical markets.
One mandatory regulation is FDA 21 CFR Part 11, dictating compliance to supply medical devices and pharmaceutical products into the U.S. Part 11 of this Food and Drug Administration’s Code of Federal Regulation relates to electronic records and signatures, implemented via a software solution. This level of compliance builds on the security and integrity attributes of a software quality system, by adhering to a well-established ALCOA set of principles. This acronym stands for:
Attributable — Data should clearly state who performed the action and when.
Legible — Data should be easy to understand, recorded permanently and preserved in its original form.
Contemporaneous — The data should be recorded at the time the work is performed.
Original — Data should be preserved in its original form or a certified true copy.
Accurate — Data should be free from error.
Metrology Instrumentation
Any organization implementing a controlled Quality Management System (QMS) within an FDA-regulated industry will need to be cognizant of selecting equipment to support these requirements. Also relevant to R&D laboratories, the prime context for this situation is the QC lab in a manufacturing environment. The checking of physical attributes is a universal method for evaluating the quality of products. Measurement of force and torque as an indicator of functional integrity, through destructive or nondestructive testing, with metrological equipment such as UTMs, torque testers, gages and other instruments is commonplace. Software will be an intrinsic part of such equipment and how it builds on and implements the fundamental quality attributes to deliver its specialized functionality will be critical to the delivery of compliant products.
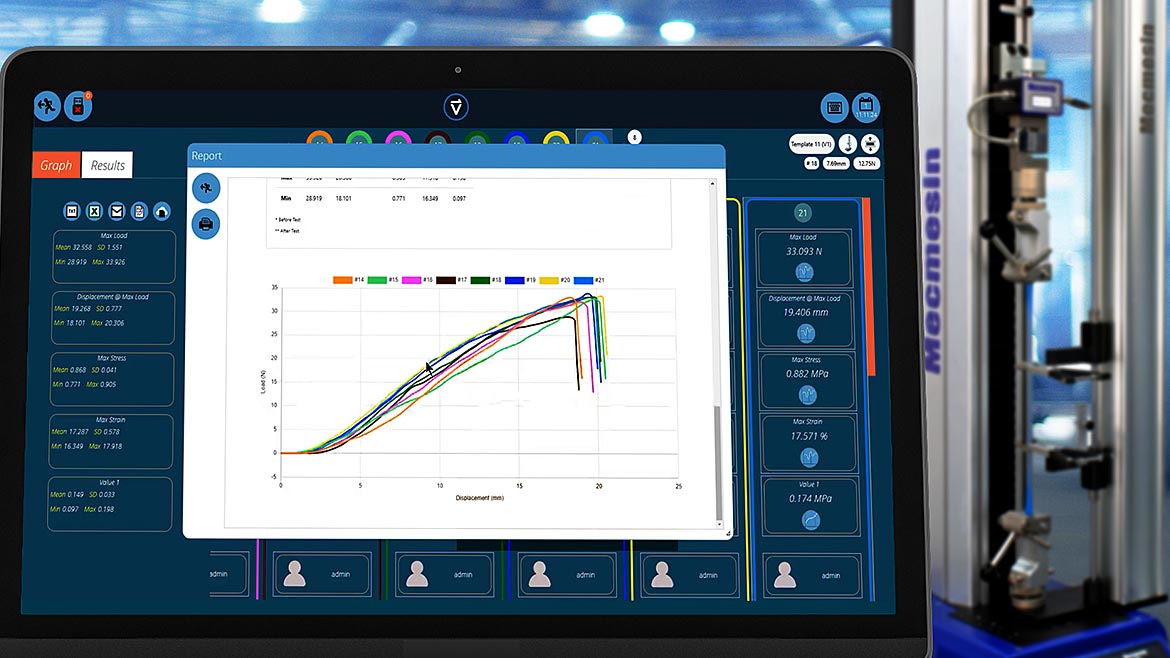
Traceability, compatibility and automation: Recalling versions of QC tests into VectorPro software that detects connected instrumentation, runs the program and then produces reports from a database of templates. | Image Source: Mecmesin, a PPTGroup company
Quality Software Attributes
With reference back to our core quality attributes, dedicated quality control metrology software should parallel these fundamentals:
Functionality — In-house USP knowledge from industry experience will give confidence that the equipment can perform simple or complex test routines to cover any required methods. The end user should be able to create their own checking workflow and any strictly defined industry standards (ASTM, DIN, etc.). Having the flexibility to perform stress-strain calculations from data is a must for a materials testing lab. A touchscreen-enabled interface may also be essential.
Usability — Modern software will implement an effective and intuitive UI. Users have interactions with software in many aspects of their lives and well-understood ergonomics maximizes efficiency and accuracy in using similar tools in the workplace. Building operations from basic modules via drag-and-drop is an efficient and innovative feature, in conjunction with icon-driven (and therefore language-independent) graphics.
Compatibility — To integrate with a complete QMS, metrology software should integrate well. This requires good interfaces to and from other tools. With a hardware-based system that relies on dedicated attachments (fixturing or other connected instrumentation) to perform custom testing, the software should support a range of industry-standard, OEM-independent accessories. Established protocols and file types, like CSV and PDF, facilitate information sharing and enable data to be transferred to other tools, utilizing their strengths. Reporting templates eliminate errors in presenting results.
Flexibility — Software built on a modern architecture that allows updates, bug fixes and the efficient addition of other features will optimize longevity of the toolset. End users can request features, and the likelihood of their implementation is greatly enhanced, enabling responsiveness to changes in external factors. Well-architected software can easily be offered with levels of features—fully featured or “lite” versions—to meet end customer needs.
Security — This is the crucial consideration. Software that ensures data is attributable will securely handle multiple user groups and types—enforce best practice password strategies; ring fence access to functions and data based on operator role; maintain time-stamped event logs; preserve test versioning for comprehensive traceability and audit trails. Integrating benchmark applications from developers well-established in IT security, such as Active Directory and SQL Server to maintain the data are worthwhile considerations.
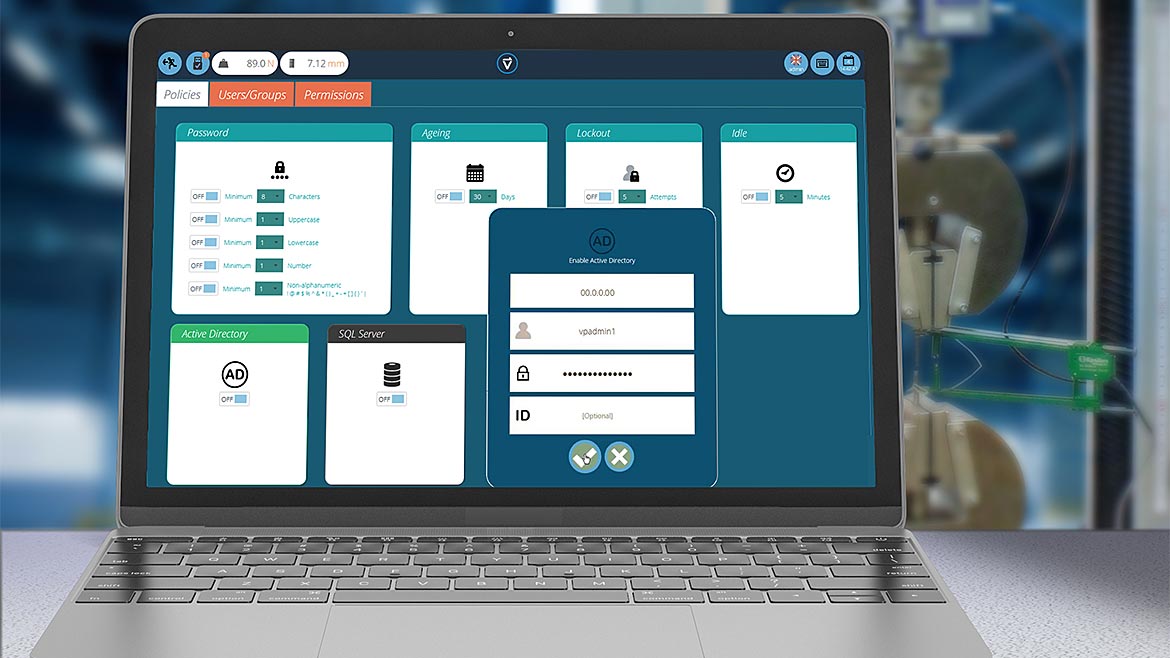
Security is crucial in an enterprise software-driven application. VectorPro Policies, Users/Groups and Permissions screens implement password rules, Active Directory and SQL database access. | Image Source: Mecmesin, a PPTGroup company
Conclusions
Quality assurance testing software for products, components and materials is key for any manufacturing organization, irrespective of size. Manual operations cannot fully meet the challenges of a competitive and increasingly digitized industry. However, initiating a more automated QMS strategy or upgrading existing tools to meet changing regulations can be done relatively painlessly by selecting solutions that build upon robust and well-established software quality principles that can do the heavy lifting.