Leak testing, which has always been essential in the automotive industry for ensuring the manufacture of quality parts and components, is taking on added importance in the mobility age. The automotive industry continues to move at a rapid pace to keep up with the growing demand for electric vehicles (EVs). Assemblies for Li-ion traction batteries and battery packs, as well as hydrogen fuel cells and fuel cell packs, each have their own special considerations for leak testing, from the component to the system level. However, engineering and product development are experiencing immense pressure to get products out of the door and into EVs. Concurrent with battery manufacturers’ racing forward to meet traction battery production demands, standards for leak testing Li-ion battery cells and packs, as well as hydrogen fuel cell batteries and packs, are in development.
It is critical to understand the leak-testing imperative for Li-ion traction batteries and fuel cell batteries, and how leak testing impacts product quality, performance, battery longevity and vehicle safety. Also critical is the need to define leak tightness testing standards specifically for leak testing Li-ion battery cells and packs, as well as fuel cells and the onboard hydrogen storage tanks and hydrogen delivery system. In the absence of specific leak-testing standards for these crucial electric propulsion power sources, elements of traction batteries and fuel cells, best practices based on what is already known can guide leak testing.
EVs can be powered by two different sources of energy: Li-ion batteries and hydrogen fuel cells. The chemistries for each power generation mode are quite different. Each traction battery is composed of numerous individual Li-ion battery cells to form a battery pack and numerous individual fuel cell assemblies form a fuel cell stack. At every juncture of manufacturing each cell, where two pieces are joined together, an opportunity for a leak is created. Similarly, when cells are assembled into traction battery packs, there are opportunities for leaks at every point where one part is joined to another.
There are thousands of places where a battery pack or fuel cell pack can leak. From the cell to the pack assembly, every joint, weld, screw, bolt, gasket, etc., presents the opportunity for medium leakage (or ingress of medium from the environment) and diminished performance. To conduct comprehensive leak testing, a best practice is to leak test each structure at the joining seams or fasteners at each added section to ensure quality, safety and battery longevity.
Leak testing for both Li-ion batteries and fuel cells is conducted with a proactive approach to evaluation – from the perspective of what needs to be prevented – or the nature of the failure that needs to be averted.
Each Li-ion battery cell and battery pack, as well as each hydrogen fuel cell and onboard hydrogen delivery system, including hydrogen fuel storage tanks, has its own leak testing considerations based on the individual structures and specific chemical mediums used. Any change in the medium in which a chemical reaction takes place, even at the micron level, would have a negative impact on traction battery performance and, by extension, vehicle safety.
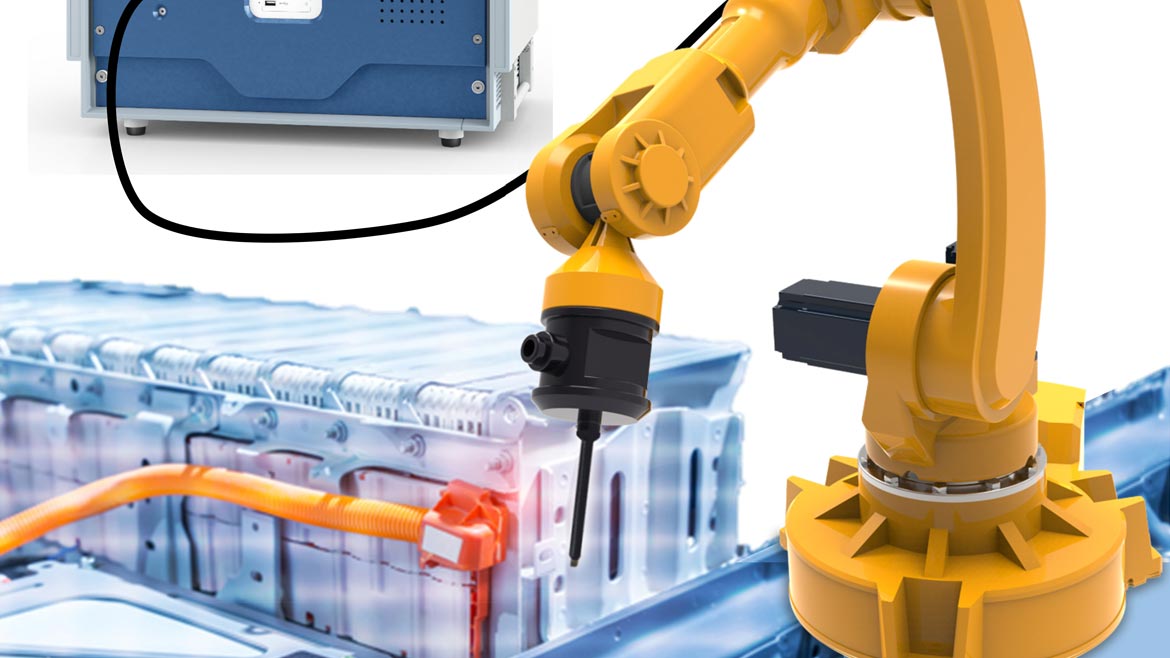
Robotic sniffing battery pack with XL3000flex
When testing for leak tightness, clear standards for leak testing to determine a “go” or “no-go” scenario are crucial. Occasionally, Simplifying Tables are used to show which leak rates to apply to each medium. However, the broad categories used in these tables can be misleading. For example, leak tightness needs to be measured differently for water loss at a power plant versus water ingress into an electronic component. That’s akin to using a bathroom scale to measure the weight of a feather, when a kitchen scale, designed and calibrated to weigh smaller things, is available.
The right tools calibrated to test a specific medium in a defined environment can obtain accurate leakage information to ensure a quality component. In the case of humidity ingress into a battery cell, a vacuum test using the electrolyte as a tracer gas can detect a leak down to a few microns.
THREE LEAK SCENARIOS
While there are hundreds of places where Li-ion batteries and fuel cells can leak, there are three leak scenarios that are essential to protect against. Each considers the type of medium important for the energy generation of each Li-ion battery and fuel cell structure. In the first leak scenario, the medium needs to be contained within a specific part or system. The second measures the ingress of a different medium into a part of the system that does not require it to function properly. In the third, the crossover of one medium into the loop where a distinctly different medium is operating is measured.
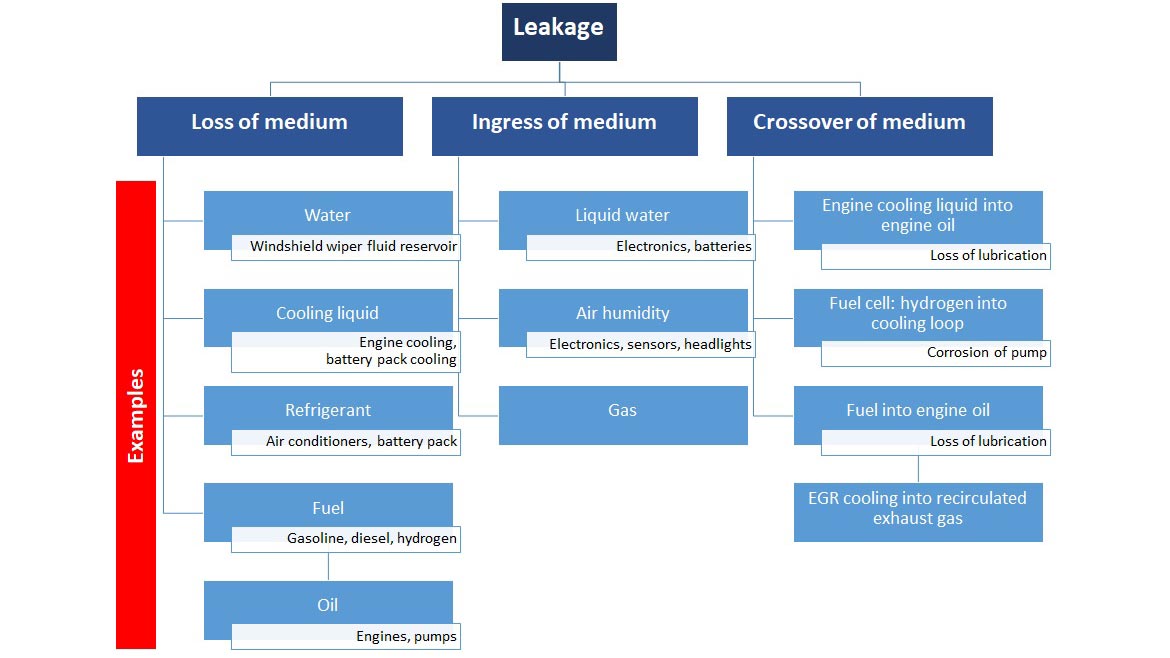
Examples of leakage scenarios in the automotive industry and failures to prevent
Loss of medium can occur with the cooling liquid used in battery trays for Li-ion battery packs. The cooling liquid is typically a water-glycol mix that, if leaked from the cooling tray could cause short circuits in electrical connections to the battery management system. For fuel cells, loss of medium can mean loss of hydrogen to power the cell. Not only can that result in a fire if hydrogen mixes with air, loss of hydrogen in a fuel cell will diminish its power output because the hydrogen is the cell’s fuel source.
Ingress of medium can occur with liquid water and air humidity. Both liquid water and air humidity ingress can cause damage to the battery cell by short-circuiting electronics and causing fires. If any form of water mixes with the electrolyte, hydrofluoric acid is formed and will cause the battery to decay over the short- or long-term.
Crossover of medium can be seen in fuel cells, where the hydrogen crosses over into the cooling loop and mixes with the water-glycol cooling solution causing loss of power, corrosion in the pump within the cooling loop and the potential for hydrogen to ignite when exposed to air.
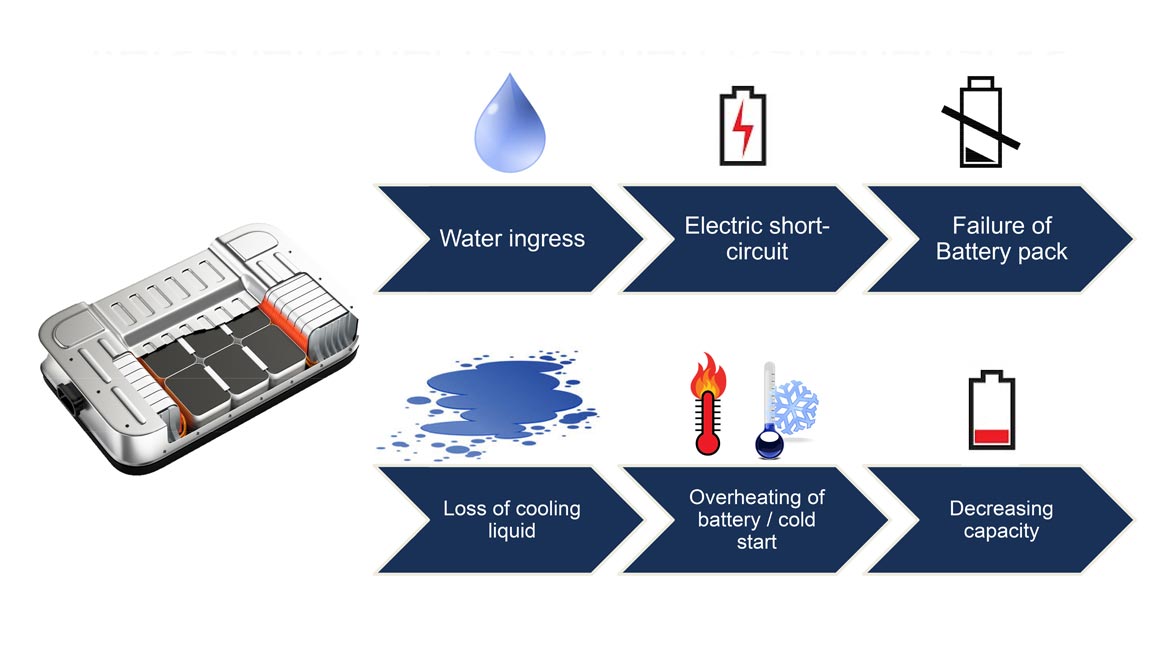
Battery pack failure mode
Li-ion batteries and fuel cell stacks typically use water-glycol cooling loops to regulate battery temperature. Very small amounts of water-glycol loss can enable the liquid to come into contact with electronics in the battery pack and may cause an electric short. Therefore, the allowable amount of water-glycol leakage needs to be set low. Considering the operating pressure of the cooling loop system, it needs to be tested for leak rates in the 10-4 to 10-5mbar.I/s range.
LEAK TESTING CONSIDERATIONS
For EV traction batteries to function at optimal levels of power generation and safety, it is imperative that each Li-ion battery cell and hydrogen fuel call, and their corresponding pack assemblies, be leak tested in efficient, effective and cost-saving ways to ensure quality, performance and safety.
Factors affecting leak tightness testing include temperature, operating pressure and material combinations. When developing best practices for leak detection, it is wise to consider these elements.
Operating pressure in Li-ion batteries and hydrogen fuel cells is a systems factor that can have an extensive impact on the amount of medium leakage. In the water-glycol cooling plate example, as the operating pressure increases, the leak rate caused by any defect will also increase, albeit not in a linear fashion. The leak rate rises with the pressure to the second power (q~ p2).
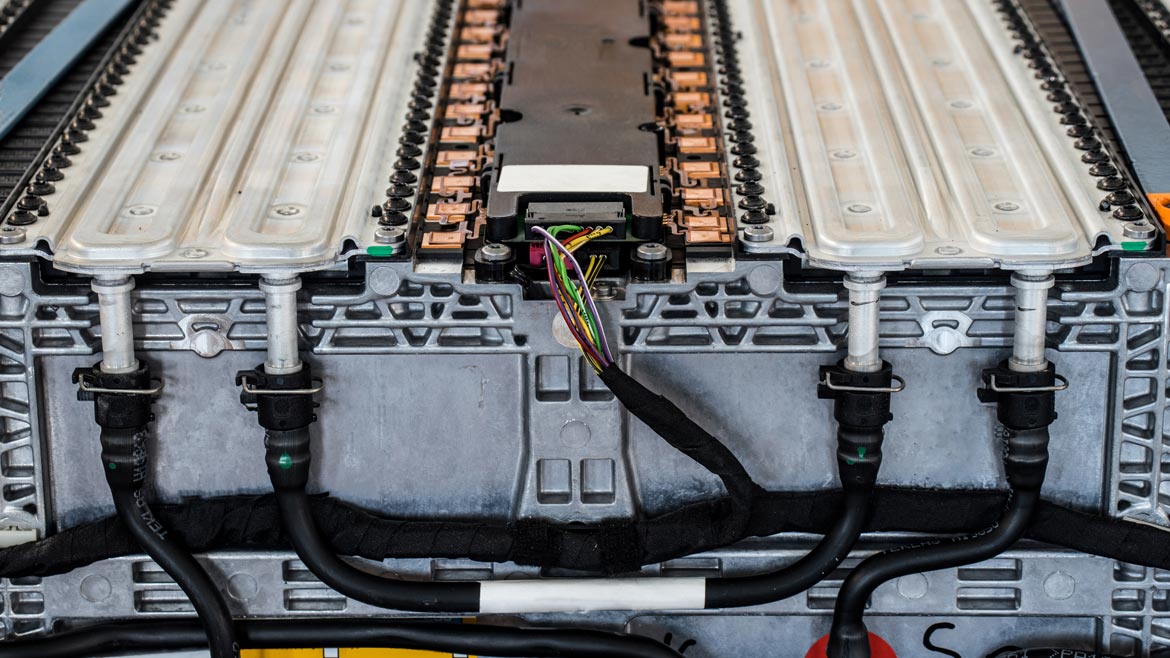
Cooling system of a car battery pack
Likewise, water ingress prevention has its own complications, because when an electrolyte reacts with any form of water that has entered the battery cell, it forms hydrofluoric acid, which destroys the battery. There are specific tests for liquid water and humid air ingress depending upon which type of water you’re trying to prevent from entering the cell or pack. Tolerable leak rates for battery cells range in the 10-6 mbar·l/s area. For liquid water ingress into battery packs, leak rates in the range of 10-5…10-3 mbar·l/s range need to be considered, in which the housing material and thickness are also variables.
LI-ION BATTERY LEAK TEST CONSIDERATIONS
There are several types of Li-ion battery cells in use in the automotive industry: prismatic, round and pouch cells with or without a solid housing. The exact level of acceptable leak rates is dependent upon several variables, including the pressure conditions inside the battery cell, the required service life of the cell and its volume.
FUEL CELL LEAK TESTING
Leak testing for fuel cells has added complexity because the fuel cells generate the power for vehicle propulsion. Since hydrogen is ignitable over a wide range of concentrations – between 4 and 73% hydrogen in the air – a best practice would be to test for hydrogen leak rates as low as possible and to set the leak limit rate one degree of magnitude lower than typical leak rate range of 10-4to 10-6mbar.I/s, using vacuum testing with tracer helium gas to test for 10-7 mbar.I/s.
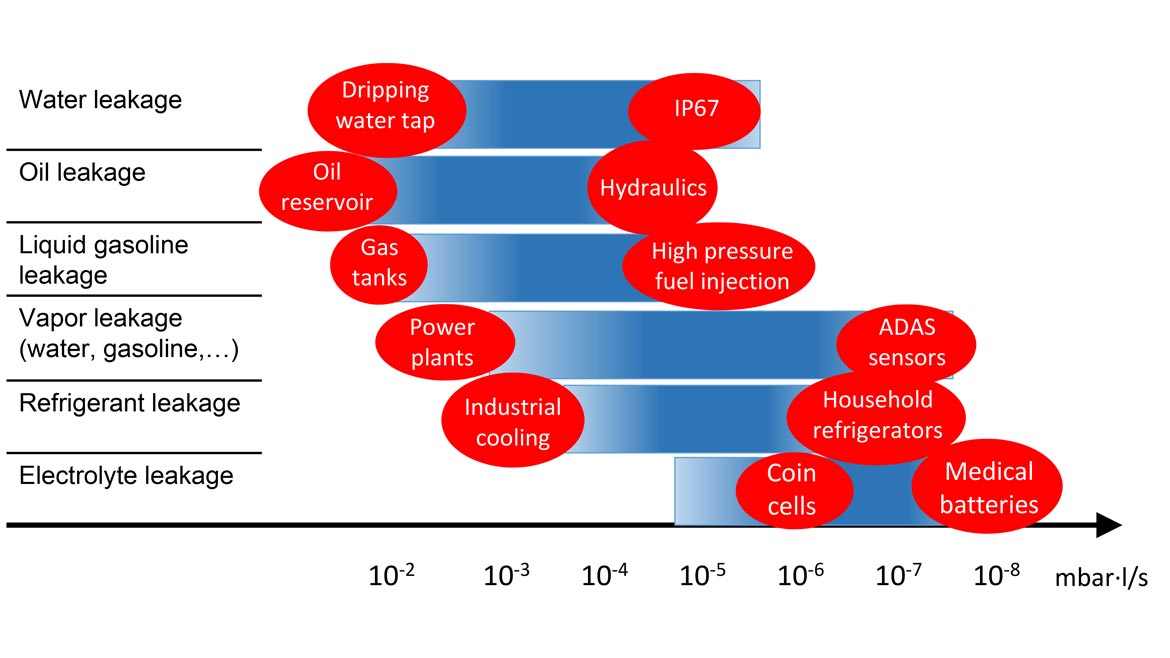
Examples of leak rate ranges
TESTING BIPOLAR PLATES FOR HYDROGEN LEAKAGE
The bipolar plates in a fuel cell provide the electrical conductivity between cells and serve as the backbone for the fuel cell stack. For leak testing, the vacuum method is also used with helium as a tracer gas. Testing with hydrogen carries the risk that the fuel cell will start inadvertently and produce electricity.
LEAK TESTING AND THE FUTURE OF MOBILITY
The above discussion of leak testing for Li-ion battery cells and packs, as well as hydrogen fuel cells and packs, just scratches the surface of the complexities, and the necessities, of leak testing for traction batteries. Knowing the three leak prevention scenarios is the first step in a marathon to implementing leak testing at every stage of Li-ion battery and fuel cell manufacturing, especially end-of-line testing. The future of mobility demands leak testing tools that do the job with speed, efficiency and exceptional accuracy to ensure quality, performance and safety.