Reliable measuring results from coordinate measuring machines (CMMs) are critical to monitoring manufacturing processes and delivering high-quality parts. Absolute confidence in part quality can only be achieved by keeping the measuring uncertainty at a minimum.
Styli and probe extensions can provide that certainty for most measurements. However, deep boreholes and hard-to-access features present challenges.
Don’t sacrifice quality by using the wrong styli and probe extensions. Find the right tools made from the right materials for your quality needs.
The Power Of Styli And Probe Extensions
Probe heads mount onto the arm and styli mount directly to the head of a CMM. As Matt Danford of Modern Machine Shop explains, some CMM scanning heads articulate on their own and some require extensions. Extensions can be found on all standard machines and come in a variety of types.
“Today, a wide selection of CMM probe heads are offered from fixed heads, indexing heads to continuous motion heads,” says Metrology News. “The fixed probe head is still used on extremely high accuracy CMMs and is also particularly useful for carrying long extension bars needed to probe and scan deep internal part features.”
These accessories increase the stylus range and enable optimal access to complex or large parts. Extensions are especially beneficial on fixed probe heads to access difficult-to-reach features deep into cavities or underneath parts.
Factors That Influence Extension Performance
Extensions have a direct influence on the measuring uncertainty of an overall metrology system. Consequently, the accuracy of what a CMM can achieve, according to specifications, will only worsen when using unsuitable extensions.
Extension performance can be challenged by three determining factors:
- Weight: The lighter and more rigid the stylus extension, the faster the machine can measure without negatively impacting the precision of the system through bending or centrifugal forces.
- Thermal expansion: Temperature fluctuations can cause significant CMM measurement errors. “The use of stylus extensions will reduce probe accuracy due to the loss of rigidity and susceptibility to temperature changes,” says the United Kingdom’s National Physical Laboratory.
- Static rigidity: The rigidity of the entire stylus system is significantly influenced by the type and design of the extension. Even slight extensions can lead to considerable fluctuations in reproducibility. The type and design of connection points also have a significant influence on measuring accuracy.
Operators should also be aware of best practices when using extensions for both styli and probes. As the National Physical Laboratory explains, “Manufacturers of probe heads and accessories generally specify maximum recommended lengths for probe extensions. Using extensions that exceed these lengths may seriously affect the accuracy and repeatability of the probe head readings.”
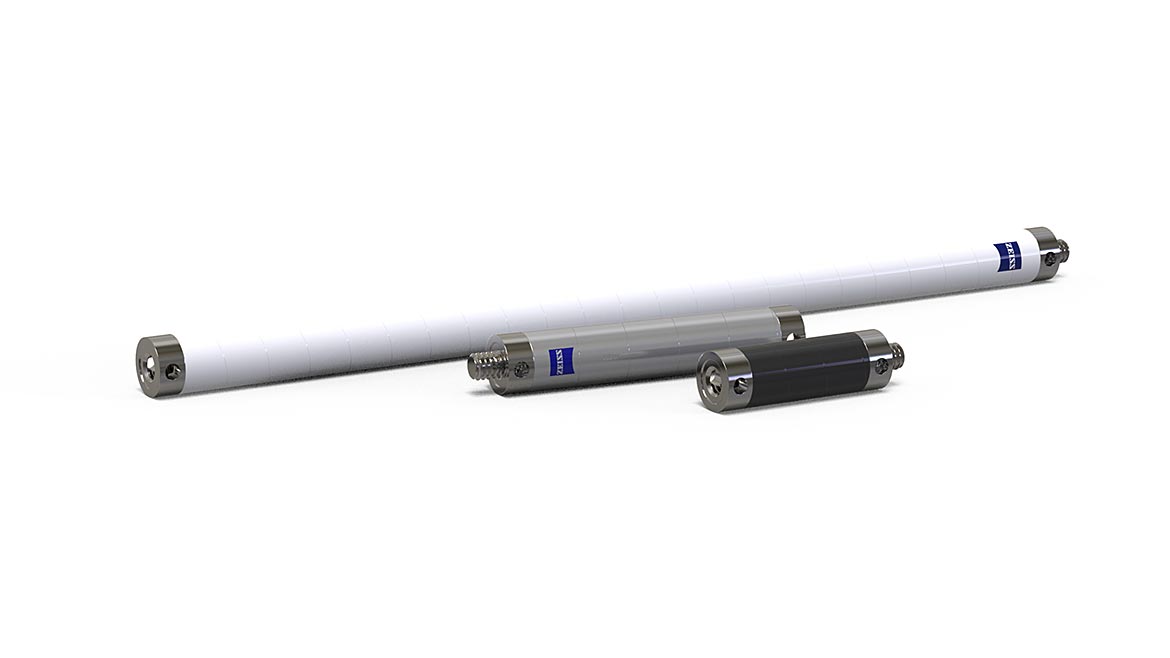
Choosing The Right Extensions
The desired result with any quality assurance solution is more consistent measurement results. Choosing the right material for stylus extensions can provide greater stability under changing conditions.
One quality that must be considered is a low coefficient of thermal expansion. Thermal growth is length-dependent, especially with long styli and extensions.
There are many choices for extension materials, and each option is affected by temperature changes in distinct ways. These materials include aluminum alloy, titanium and carbon fiber.
Aluminum was the dominant material decades ago when metrology was mostly conducted in quality labs. New materials were needed as quality assurance and control moved to the production line. Labs were temperature-controlled, but aluminum doesn’t handle temperature changes well and is ill-suited for production-line metrology.
Where metal is needed — for joints, knuckles and so on — titanium offers the best combination of light weight, strength, thermal and structural stability, and density. “But titanium extensions, for weight reasons, had to be reduced in diameter and wall thickness to be comparable to aluminum extensions,” says Jörg Esswein, head of product management for accessories at ZEISS Industrial Quality Solutions. “This reduction leads to loss of rigidity.”
Carbon fiber is the most common material and best option for long styli and extensions. The polymer is stiff, lightweight, has high flexural strength and, because of its thermal stability, the benefits eclipse other materials like aluminum, stainless steel, steel, titanium and ceramic.
Even with their unique advantages, all three materials — aluminum, titanium and even some carbon fiber — may not have the right combination of properties to guarantee the best results from extensions.
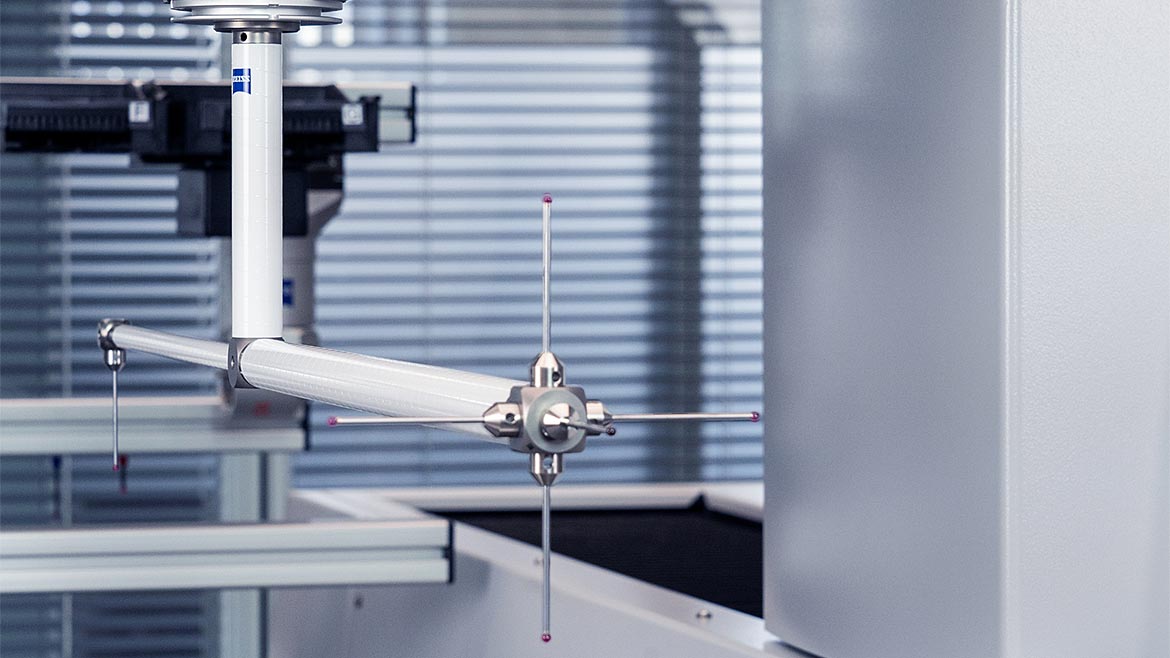
New Range Of Carbon Fiber Extensions Outperform Even Titanium
It’s important to find an extension portfolio that delivers the perfect combination of material factors. Extension suites should be customized for the varying accuracy requirements of different CMMs. These extensions would always keep accuracy at the highest possible level in combination with a very good price-performance ratio.
Using the right carbon fiber extensions can decrease the influence of the extension on the CMM measuring uncertainty by up to 5 times compared to titanium. Users would also gain increased productivity as significantly higher scanning speeds while maintaining the same level of accuracy are possible thanks to the increased static stiffness. As well, increased temperature resistance can make the extensions suitable for all measuring environments.
Ideally there would be three accuracy levels, based on requirements.
Conclusion
You need a complete carbon fiber extension portfolio that measures up to your accuracy requirements. Ideally, these would be tailored to fit your CMM. Get maximum accuracy and optimal performance without burdening your budget.