In today’s manufacturing landscape, efficiency, safety, and skills training are critical to success. But these elements often exist in a delicate balance, especially on the shop floor. These challenges are being addressed by machine trainers, a robust virtual solution for training machine operators and programmers.
In this article, we’ll take a closer look at what a machine trainer simulator is, how it works, and the benefits it provides. We’ll also explore how a machine trainer integrates into the smart manufacturing workflow and presents actionable solutions to today’s most pressing shop floor challenges.
What Is A Machine Trainer?
A machine trainer is an innovative solution for training operators/programmers for CNC machines/CMMs, in an efficient, cost-effective, and safe manner. Connecting the real world and the digital world, a machine trainer offers integrated teaching, practical training, program verification, and safety simulation for CMMs and CNC machines.
Running on designated software, these simulators are perfect for both novice and experienced operators. A machine trainer allows users to train using different types of controls, often including programs such as Siemens, Heidenhain, and Fanuc. Users can easily select the exact control panel that mimics the one on the actual machine they need to train for.
Machine trainers are extremely flexible; manufacturers can use it for production, train people on a machine trainer through simulation while using their real machines for production or use it in a classroom setting where they can have multiple inputs or controllers within a single unit.
About CNC Simulation Software
The brains behind a machine trainer is the CNC simulation software. Standard machine projects are usually included right out of the box, or manufacturers can perform an end-to-end process, requesting a specific digital twin to train users. In essence, the CNC simulation software allows a machine trainer to mimic all real machine motions with greater visibility and freedom.
This software gathers data from across the CAM system — including cutting tools, stock parts, designed parts, fixture models, and G-code — and then applies those features to the digital twin environment, a replica of the machine on the shop floor. Next, it runs it through a quick, three-step process:
- It looks at the entire G-code and determines if anything will alarm out the real machine
- It runs the actual simulation, removing all the material and detecting any crashes
- Finally, it performs a part inspection, identifying the difference between the original part and the part resulting from the G-code
Users can optimize the tool and the cut path beforehand either in the air — reducing any air-cutting time and overall cycle time — or in material, standardizing chip thickness or flow and automatically rewriting any feed rates. Users can automatically generate documentation for the shop floor, meaning that anything they change in the CNC simulation software environment will also automatically be changed in the setup sheets, ensuring machinists always have the most up-to-date information.
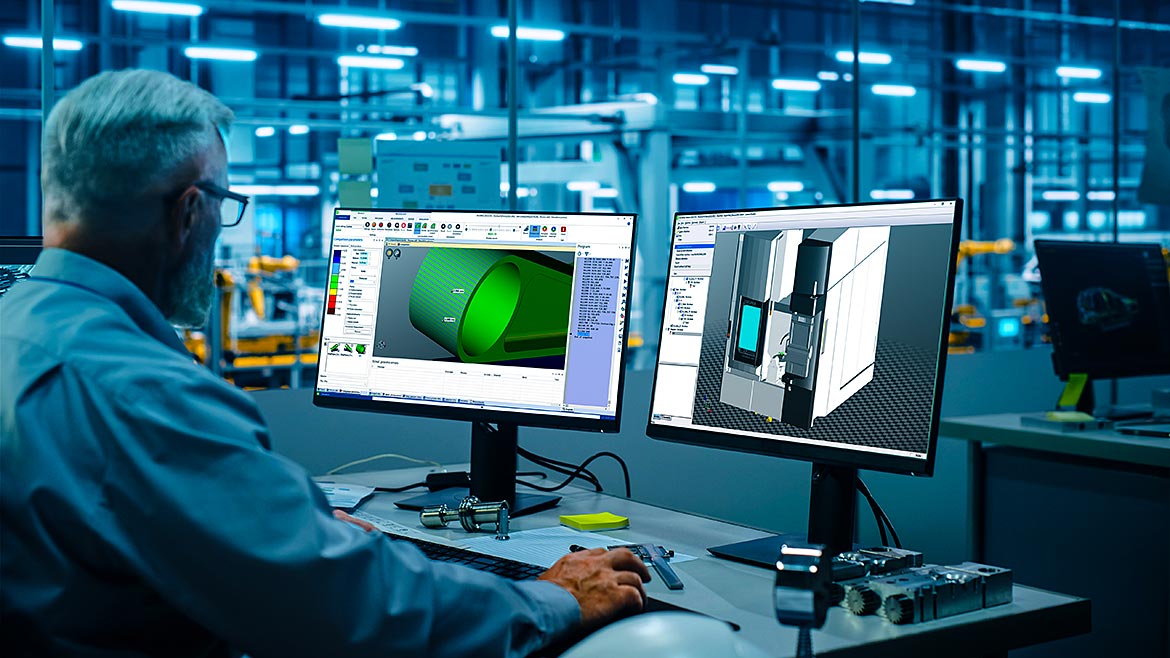
A Machine Trainer’s Place In The Workflow
In the smart manufacturing workflow, a machine trainer fits within Process Certification, aligned between machine programming and manufacturing. This helps ensure that everything is good on both the programming and the machinist side.
How To Use A Machine Trainer
Working with a machine trainer is a user-friendly, straightforward process. The operator sets it up for training just like they would on the shop floor — by getting a setup sheet or producing one as an output from the CNC simulation software program. On the screen, the user ensures that the Work Coordinate System (e.g., G54, P3) location on the corner of the part is set up the same way as in the real machine. The user accesses a machine trainer’s manual mode using the control panel, then accesses preset management and checks their offset list, ensuring that parameters match exactly.
Next, the operator ensures that all the same Z gages or tooling lengths offsets mimic precisely what is seen on the real machine. Once they’ve verified input, they can go to the next step, ensuring their program is ready. The user can easily switch from manual to automatic mode, and a machine trainer will display the G-code, which will be the same that runs on the real machine. If the user needs to reset the simulation, they can easily do that.
A machine trainer allows users to access all of the inputs, allowing them to override the spindle speed or feed rates or even perform an emergency stop. And if the user wants to modify the G-code, they can do so directly from the panel.
Once a machine trainer starts, the user observes the process, watching as it starts to remove the first initial (virtual) cut. At this point, the user can re-verify that their offsets are good before allowing the machine to take one initial slim cut around the entire part.
From there, the user takes measurements — zooming in the view just like leaning in to take a closer look at a real machine — ensuring that the offsets on the initial cut are as desired. Users can also perform a point-to-plane measurement or back out of the zoomed view to access one of their predefined views to observe the whole machining environment again. Users can also control the speed of automatic overrides, allowing them to get through more of the machining material more quickly.
If the user anticipates something going wrong (or sees something go wrong), they can stop the simulation and retract to a safe distance, using either the Z-plus or the jogging wheel on the side of the machine. The user can reset the program, put the stock back on the material, and change their G-code if necessary — then continue the program.
A machine trainer allows users to see the final piece taking shape. As a user zooms in on the material removal process, they can observe the simulation of the chip flow, the coolants, and even the sound of the machine running in the background. Additionally, at the top of the machine, the user can easily see its status: red if it’s alarming, orange if the machine is being powered up, or green if things are running smoothly. And the CNC simulation software dynamic status window displays the same current conditions as status as they will see on the real machine.
Operators can pause the process at any point — for example, they can pause to take an in-process measurement of something that’s already been machined, zooming in to perform diameter or radius measurements to ensure the part is up to snuff before going to the QC room.
The Benefits Of Using A Machine Trainer
Using a machine trainer will help manufacturers in numerous ways:
- Minimize machine footprint, investment, and operating costs: A machine trainer allows manufacturers to perform important training tasks without taking a machine out of production. And because a machine trainer effectively contains multiple machines in one footprint, manufacturers can keep costs down without sacrificing more space; users can simply flip the arm around to use the language they need, with its corresponding control panel and keypad. Additionally, because the training happens virtually, manufacturers can save money on raw material stock, tooling, fixtures, etc., required for training purposes.
- Scalable with a large variety of machines: Machine trainers currently run on a range of controls and will likely expand to include more in the future.
- Training on critical solutions without destruction: Operators can practice critical solutions without wasting materials or causing potentially expensive harm to the machine — which could cause downtime, product delays, and frustrated customers. Additionally, manufacturers can effectively evaluate the operator’s understanding of the training process to measure their training effectiveness.
- CNC simulation software connection: Because CNC simulation software usually powers a machine trainer, manufacturers can train on preset projects or create customized projects, allowing operators to train on the real project they’ll be using at the real machine.
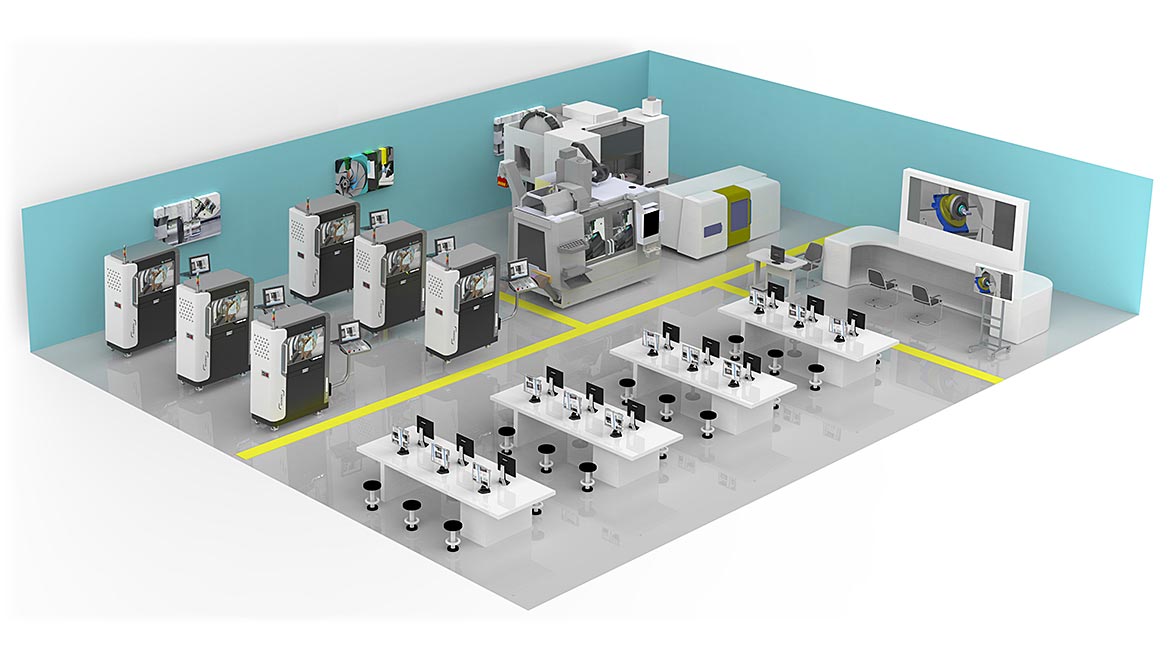
Current Shop Floor Challenges And How A Machine Trainer Solves Them
A machine trainer helps manufacturers overcome many of the challenges currently facing shops today, including:
Machine time and safety
- Separate production from training: Using an expensive CNC/CMM machine for training puts it at risk of a breakdown due to human error, which can lead to customer delivery delays. By allowing users to train on a machine trainer, real machines can stay in production, allowing the manufacturer to support training without stopping (or jeopardizing) the production process.
- Eliminate risks before implementation: Because a machine trainer runs the program virtually, users can identify potential issues or problems before working on the real machine.
- Reduce delays and rework: A machine trainer’s virtual environment also helps reduce the need for rework — and because it’s on a completely separate, non-production machine, manufacturers don’t need to be concerned about training activities leading to production delays.
Transfer of knowledge
- Skilled workforce set to retire: Many seasoned machinists are set to retire; a machine trainer allows the company to capture their knowledge and share it with future employees.
- High job turnover rate: High turnover means that manufacturers constantly need to train operators and programmers. A machine trainer helps streamline that process even as the company grows and brings in new machines.
- Attract talent with technology: Manufacturing companies work with colleges and universities to include machine trainers in manufacturing programs; because users have the opportunity to become familiar with the technology while in college, it may boost their interest in the field and in working with companies that use this technology.
A Future-Proof Solution For Today’s Manufacturing Challenges
Machine trainers offer a game-changing approach to training tasks with its capacity to enhance safety, boost efficiency, and significantly mitigate operational costs. This training platform alleviates the pressure on real machines by providing a controlled yet realistic environment, allowing them to continue with production tasks. Its scalability, backed by the power of CNC simulation software, makes it a versatile tool compatible with multiple machine controls, suitable for both small and large manufacturing setups.
As manufacturing enterprises navigate complex modern production demands, embracing solutions like machine trainers demonstrates a strategic, long-term investment for building a more skilled, efficient, and safer workforce.