Measurement
The new VDA Volume 5 – Obligation and Opportunity
Too much measurement uncertainty leads to incorrect conformity decisions, incorrect assessment of machines and production processes, poorer process quality and thus, increased production and testing effort.

The third edition of VDA Volume 5 was published in July 2021, and the associated Practical Guide was published in April 2022. The 3rd edition is much more than an editorial revision, as the project group, formed from automotive manufacturers and suppliers, incorporates all practical experience since the introduction of the first VDA Volume 5 in 2003 into the redesign. Chapters on the planning and management of measurement and inspection processes have also been included.
What’s new in the 3rd edition?
-
Expansion of the scope
- Integration of test process planning and test equipment management
- Expansion from geometric features to other measured quantities
- Integration of product development
-
Risk-based assurance
- For optimal and as well economical safeguarding of product and process quality.
-
Solution approaches for many practical topics such as
- Transferability of proof of capability
- Dealing with measurement and inspection process capability that has not been achieved
- Handling small tolerances (fine tolerances)
- Implicit proof of capability
- Calculation of the capability ratios for one-sided specification limits
- Specific requirements for the documentation
- Proof of capability for small test sample sizes
- Consideration of measurement uncertainty in R&D
-
Dealing with attributive inspection processes
- Distinction between “discretized characteristics” and “discrete characteristics”
- Complete overview of common methods (signal detection, effectiveness, Kappa methods, concordance coefficient, ...)
-
Specification of the procedures for verifying ongoing capability
- Application of measurement stability charts (control charts for stability measurements)
- Selective repeated assessment of individual uncertainty components
- Further organizational measures
- Supplementary Practical Guide with case examples
Measurement and inspection process management – backbone of quality assurance
There are very good reasons for good measurement and inspection processes, because too much measurement uncertainty leads to:
- incorrect conformity decisions,
- incorrect assessment of machines and production processes,
- poorer process quality and thus
- increased production and testing effort.
It is therefore important to organize inspection process management so that product and process quality are ensured and unnecessary costs are avoided.
Risk-based assurance
The focus of risk-based assurance is on the characteristics that are of particular importance for the quality of the final product. Assessment is made of the consequences and the probability of an incorrect test decision. In the example, the clearance test in assembly and the ACC distance check as part of homologation are compared.
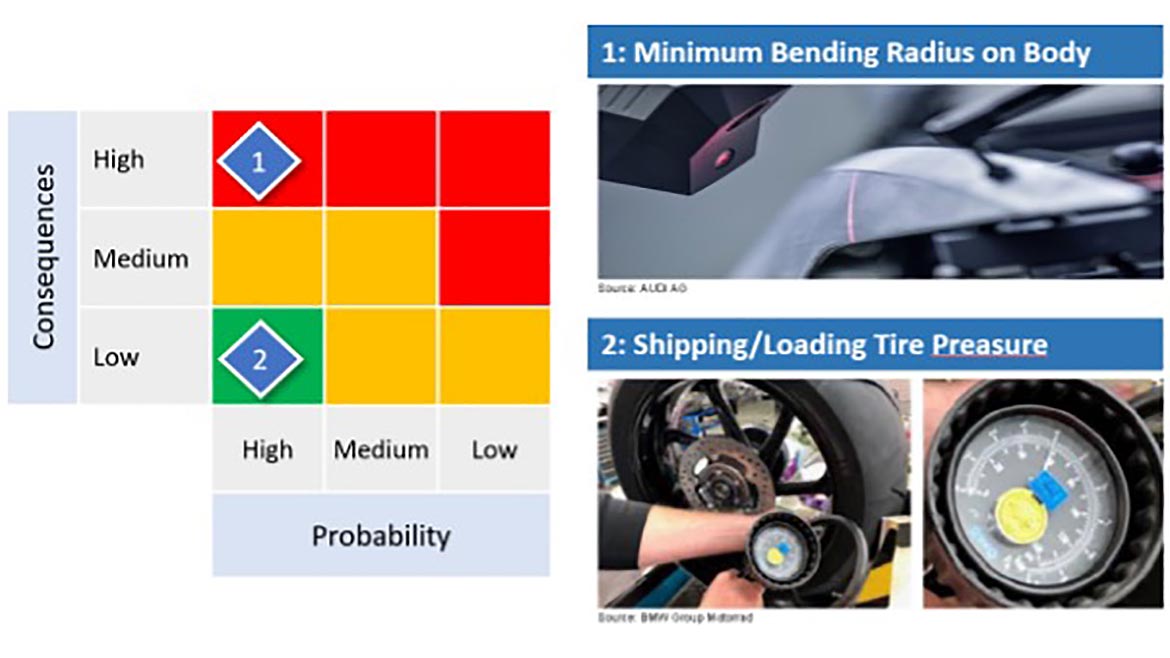
Figure 2: Consequences and probability of incorrect test decisions of different characteristics
Test equipment management
The following two tables show the validation of measurement and inspection processes in test equipment management and during verification of measurement and inspection process capability.
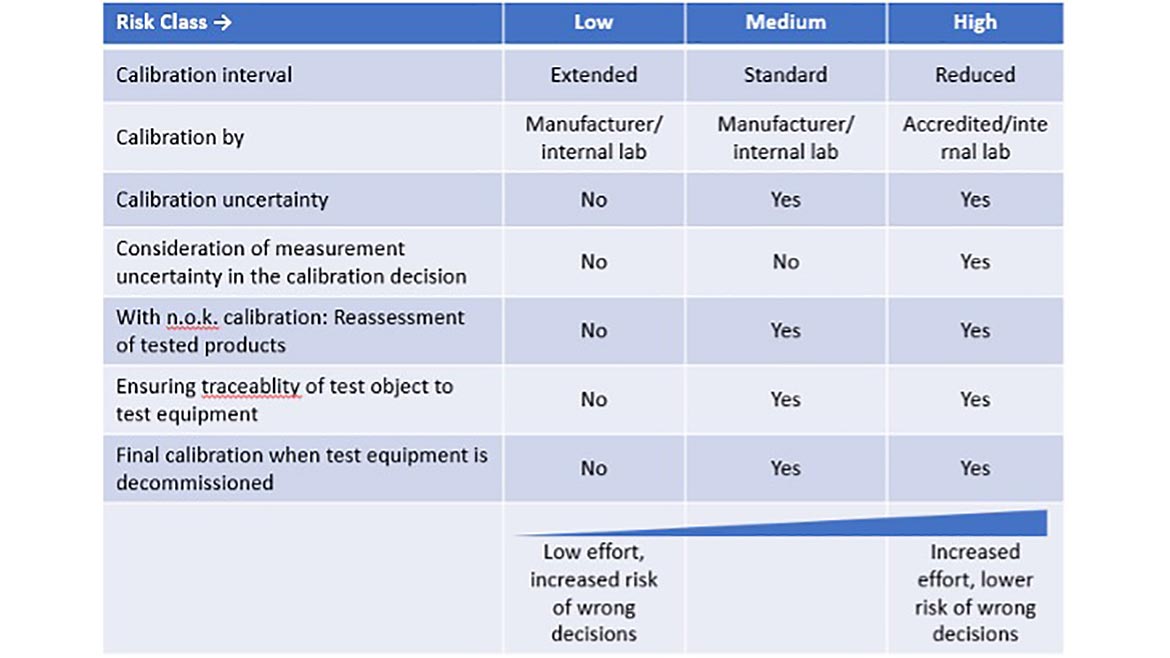
Table 1 Risk-based assurance by test equipment management (based on VDA Volume 5)
NOTE: Traceability is misspelled in this graphic. Can this be fixed?
A laser section sensor used for inspection of the legal minimum bending radius should therefore be calibrated at relatively short intervals according to a procedure that has been accredited by a National Accreditation Body in accordance with ISO/IEC 17025:2017. Calibration in an in-house laboratory that meets the requirements of IATF 16949 is still permitted. This measurement uncertainty of the calibration procedure should be considered in the conformity statement referring to ISO 14253-1. Manufacturers must ensure traceability, so that measurements that have already been carried out during a NOK calibration can be checked again. The validity of the measurement results must be proven by a final calibration until decommissioning. In contrast, the gage which is used to measure shipping tire pressure can be calibrated at relatively long intervals.
Proof of capability
The proof of capability for measurement and inspection processes is carried out analogously. The measurement uncertainty of the measurement process used in design and development of the assistance systems must be explicitly and individually defined for the measuring system used (i.e. mostly experimentally).
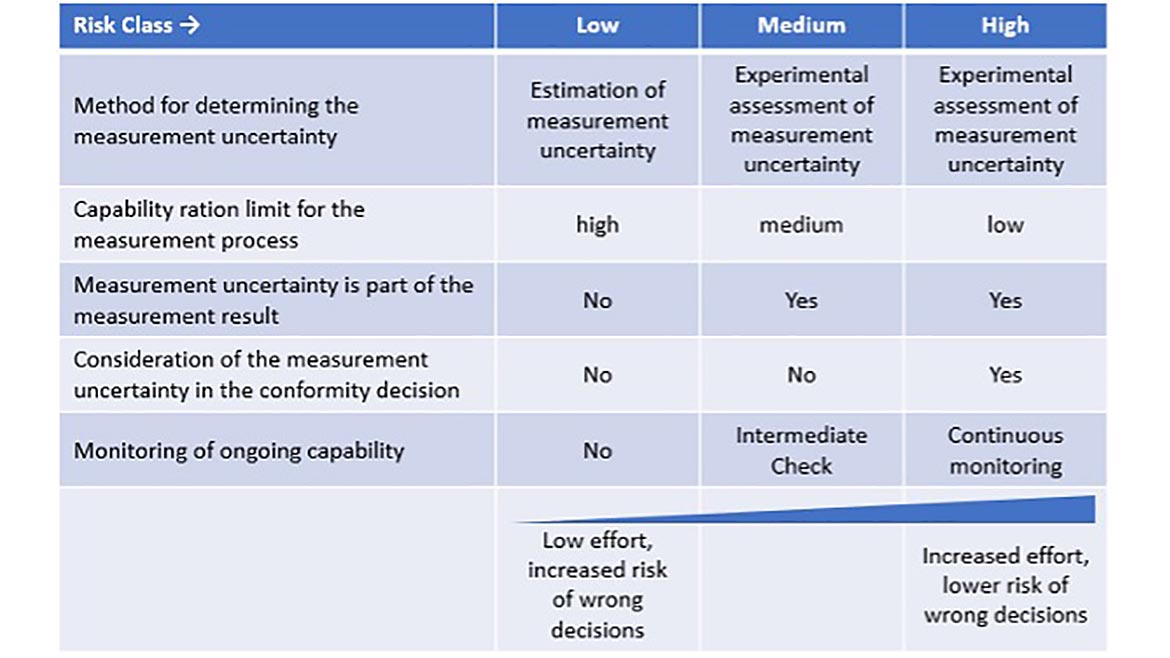
Table 2 Risk based proof of capability (based on VDA Volume 5)
For the first time, VDA 5 defines requirements graded according to risk classes. For example, the measurement uncertainty for the risk class “high” must be shown as a component of the measurement result and considered as guard band in the test decision to reduce the risk of an incorrect acceptance of a test object! Finally, as required in ISO 9001:2015, it must be continuously monitored that the measurement uncertainty of the inspection process does not change and that the proof of capability is therefore permanently valid.
In contrast, no experimental proof of capability has to be carried out for the tire shipping pressure test. An estimation of the measurement uncertainty based on the MPE value of the test equipment (MPE: Maximum Permissible Error) is sufficient here.
Procedure for proof of capability
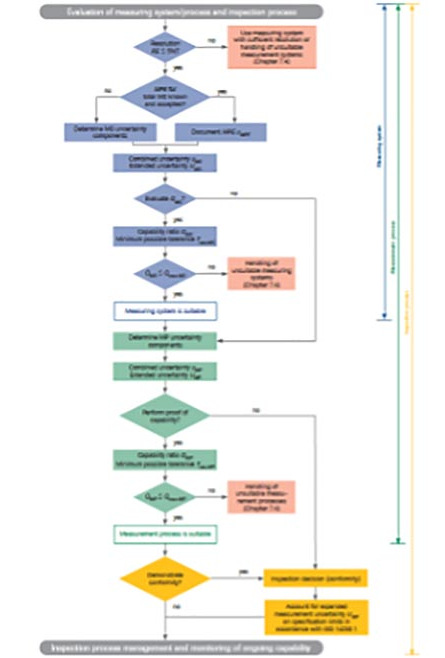
Figure 3 Flow chart according to VDA 5 (2021)
Although no significant changes have been made to the basic concept of proof of capability in accordance with VDA Volume 5, many improvements have been incorporated in detail. The determination of the influence of linearity deviations was completely revised and a new calculation method presented.
It was also clearly highlighted how the assessment of the uncertainty components is managed by the planning of the measurement tests.
If an MPE is used for verification, VDA Volume 5 now explains in detail under which conditions an MPE is considered trustworthy and thus suitable for use. This also applies to the use of key values for the pre-selection of measuring systems.
The measurement uncertainty budget to be presented contains additional columns according to the new edition, so that the entire measurement uncertainty determination becomes more comprehensible. The analysis is completed by rankings and their percentage contribution to the measurement process uncertainty. With this potential for optimisation can be very easily determined.
Last but not least, there are rules on when the proof of the QMS, can be omitted in order to resolve any contradictory evaluations of QMS and QMP still possible referring to the 2nd edition.
New, practice-oriented solutions
An important goal of the new VDA 5 is the inclusion of solutions for practical challenges during the verification of capability. This includes questions such as:
- When can the proof of capability or parts thereof be transferred to other studies?
- What are the possible actions if the capability ratio target is not met?
- How is proof of capability achieved if only small test sample sizes can be measured?
- How often does the proof of capability have to be repeated?
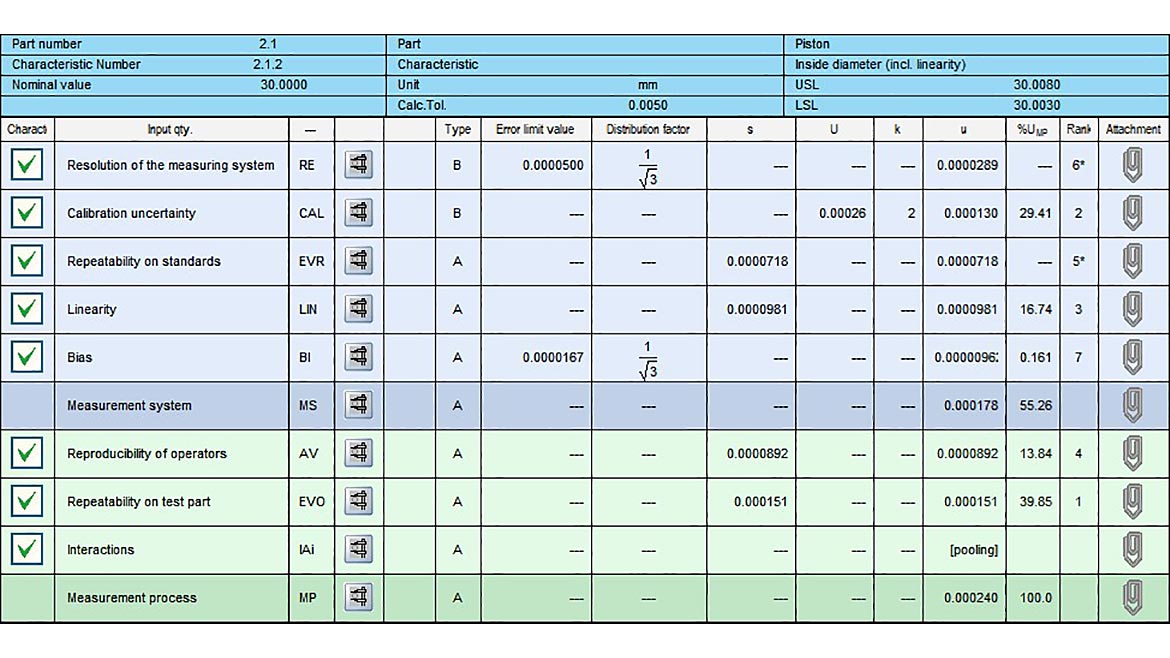
Figure 4 Measurement uncertainty budget from Q-DAS solara.MP V14
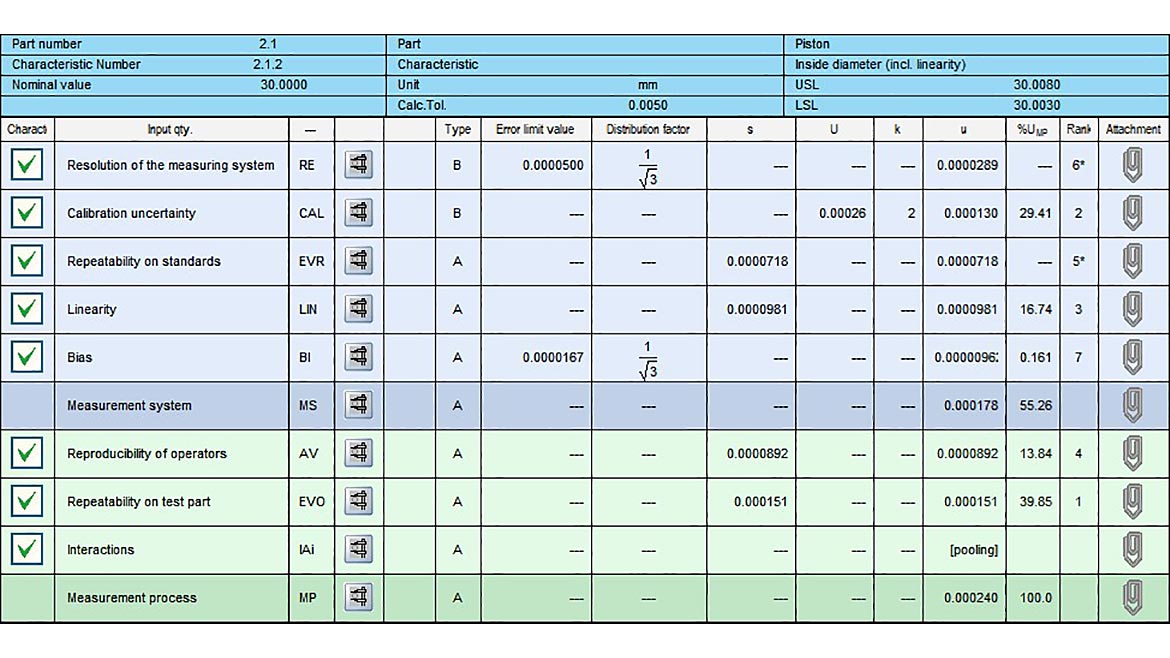
Figure 4 Measurement uncertainty budget from Q-DAS solara.MP V14
Dealing with unachieved capability
In the new VDA 5, there are two sections for dealing with measurement and inspection process capability that has not been achieved. The order of the possible actions was deliberately chosen:
- Optimization of the measuring system and the measuring process should always be the first option. As an attempt is made to pass the capability test after all, no involvement of the customer is required.
- Risk analysis with conditional release as a second option, whereby the involvement of the customer is essential.
The new method of fine tolerances is particularly noteworthy. In some areas, tolerances in the range of what is technologically only just feasible are common. Measuring systems must often be evaluated then via special approvals. To reduce the organizational effort, a “fine tolerances” method can be introduced in which approval limits are adjusted automatically if the characteristic tolerance is below an agreed fine tolerance limit.
Capability ratios for one-sided specification limits
There are many features with one-sided specification limits, such as pull-off forces or measures of form and location. Added to this are process ratios that have a defined operating point (setpoint value) but are limited to only one direction. A distinction is made in VDA 5 between three cases:
- Characteristics with a process-relevant technical/physical/natural limitthat corresponds to the target value, such as form and position dimensions (GD&T) or the maximum water content in the brake fluid. In this case, proof of capability can be carried out as usual.
- Characteristics with defined operating pointsuch as the object temperature of a component in the combustion engine (coolant temperature).
- Features without defined operating point and without additional process-relevant technical/physical/natural limitsuch as tensile strength.
Proof of capability for small test sample sizes
Another known problem from practice is the verification of capability for small test sample sizes. It often happens that not at least 30 measurements can be carried out, e.g., due to too long measuring time or lack of parts availability. In this case, it is permissible to carry out less than 30 measurements if the k-factor of the normal distribution is replaced by the k-factor of the student t-distribution. A clearly regulated procedure for this is described in the new VDA Volume 5.
Assessment of ongoing capability
DIN EN ISO 9001, Chap. 7.1.5.1, requires ongoing capability to be ensured (“… resources … are maintained to ensure their continuing fitness for their purpose”). This means that the validity of the proof of capability must be monitored continuously depending on the relevance of the characteristic and the stability of the boundary conditions. Various methods are proposed in VDA 5:
- Regular calibration with shorter calibration intervals
- For special consideration of selected influencing factors, proofs of capability can be repeated periodically in part or in full.
- Continuous monitoring based on a stability chart.
This last approach is given priority due to the effectiveness and relevance of stability charts.
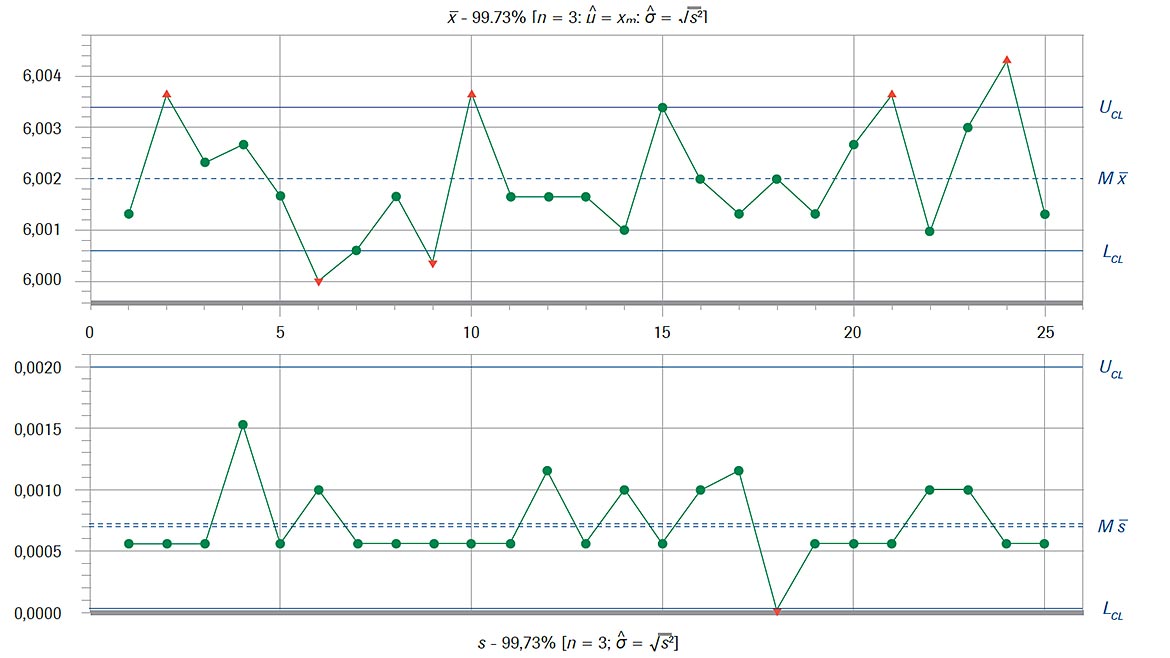
Figure 5 Stability chart according to VDA Volume 5 (2021)
Harmonization with ISO 22514-7 and other ISO standards
When developing VDA Volume 5, the working group paid close attention to ISO-compliant terminology so that internationally unambiguous terms are used. The proof of capability in accordance with VDA Volume 5 is harmonized with ISO 22514-7 “Statistical Procedures in Process Management - Capability and Performance - Part 7: Capability of measurement Processes” so that companies outside the automotive industry can reference an industry-neutral standard.
Summary
With the third edition of VDA Volume 5, answers to many questions and challenges in practical application are provided. The expansion of the scope to non-geometric characteristics and the introduction of risk-based assurance have resulted in guidelines for ensuring product and process quality and the focused use of resources in quality assurance.
The application of the new VDA Volume 5 is therefore mandatory and an opportunity for many suppliers in the automotive industry. Some specifications in the new VDA Volume 5 are formulated more explicitly, the regulations are clearer and more unambiguous. At the same time, there is an opportunity to better understand the interaction between test planning, test equipment management and proof of capability and thus improve overall quality and the quality management system. Last but not least, VDA 5 offers the possibility of fulfilling the requirements of ISO 14253-1, JCGM 106 and ISO/IEC Guide 98-4 for taking measurement uncertainty into account during conformity testing. This means that the user is always on the safe side, in the truest sense of the word, even in the event of product liability.
Looking for a reprint of this article?
From high-res PDFs to custom plaques, order your copy today!