Defined processes are critical to continuous improvement in manufacturing. Key measurement points are identified and metrics are put in place to measure processes. The resulting data is meant to be used for process improvement. It is in the evaluation of the data that bottlenecks can be discovered. In manufacturing, manual gaging is often responsible for bottlenecks.
Bottlenecks in manufacturing can be caused by labor shortages, which force employees to split time between processes. The resulting throughput irregularities negatively impact downstream processes. Technology can also cause bottlenecks if it is antiquated and slow, or improperly selected for the desired purpose.
In manufacturing, manual gaging is one of the processes that is often responsible for bottlenecks. Whether performed in-process or at incoming inspection, it is a slow but necessary task. Additionally, coordinate measuring machines (CMMs) or other specialty inspection systems in the quality control lab are often identified as significant process bottlenecks.
Here’s how automating manual gaging can reduce or even eliminate these bottlenecks.
In-Process Manual Gaging
A machine operator’s priority is to keep the machine running, producing parts that fall within specified tolerances. In addition to loading and unloading the machine, the operator is often tasked with gaging, per an inspection report, to ensure the parts are acceptable. Upon completion of a cycle, they may be required to make several manual measurements using instruments such as calipers, micrometers, and thread gages.
If the gaging process is longer than the machine cycle, then the machine will sit idle for a period after each cycle. In this case the inspection process is the bottleneck, and the cost is idle spindle time. That idle spindle time over one, two or three shifts adds up quickly and precludes optimal machine output.
An operator under pressure to keep production steady may inadvertently neglect the manual gaging process. There are multiple costs associated with this. Improperly measured parts, or parts not measured at all, do not yield the data required to make ideal machine adjustments. The result could be the production of parts that fall outside of acceptable tolerances.
Parts found to be unacceptable at a downstream manufacturing process could be scrapped or require re-work. Both are costly. If not caught in a downstream process, bad parts could cause a damaged customer relationship or worse. Think implantable medical devices or aerospace components.
Adding an automated gaging system to the process could eliminate these risks.
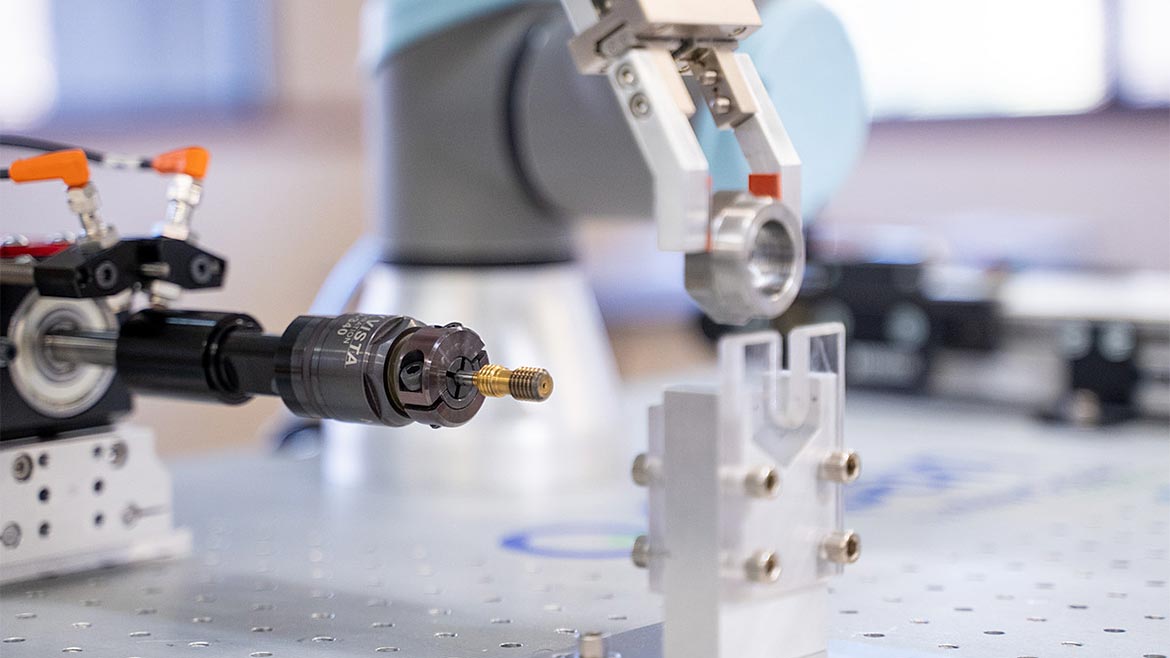
Incoming Inspection
Outsourcing parts production by manufacturers is very common. There are shops that specialize in different types of parts production. For example, a Swiss machine shop can offer high mix/low volume and high volume/low mix production of parts from standard bar stock. Consequently, a manufacturer with the need for a part suited for a Swiss machine will outsource the work because they do not have the capability or the capacity themselves.
The manufacturer that has hired the Swiss shop to produce those parts will require some level of inspection by the Swiss shop to avoid buying non-conforming parts. When these parts are critical, the manufacturer may choose to perform an incoming inspection upon receipt of the parts to ensure conformance.
In some shops, the delivery of these types of parts is not so frequent as to warrant a dedicated, full-time inspector. Incoming parts will sit in a staging area until they can be inspected. The inspector is likely an employee with primary responsibilities elsewhere in the organization. When they are taken away from their regular role, that process is temporarily put on hold and can result in a bottleneck. Incoming parts awaiting inspection can slow or stop downstream processes where they are needed, creating an additional bottleneck.
An automated gaging system designed for the inspection of incoming parts can relieve both of these bottlenecks. As an additional benefit of automation, in some instances, the manufacturer could choose to do 100% inspection on incoming parts and only pay for those within acceptable tolerance.
At The CMM
Most manufacturing facilities have a quality control lab that contains more accurate, specialized measuring systems. Systems like CMMs are used because they can accurately measure many features that cannot be captured accurately by handheld instruments. Although CMMs can be automated, the inspection cycle times can sometimes exceed optimal time due to the number of features being measured per program. This can slow shipments of final products or additional downstream manufacturing processes. The result is a bottleneck at the CMM.
The CMM is often programmed to check all the features of a part. Instead, many of the less complicated part features could be measured on an automated gaging system before the part is loaded into the CMM. The CMM program can then be shortened to only measure those features that cannot be captured via other means, leading to a reduced cycle time. Additionally, this could disqualify parts from being loaded onto the CMM if they are found to be out of tolerance based on the initial inspection.
In either case, the bottleneck at the CMM could be reduced.
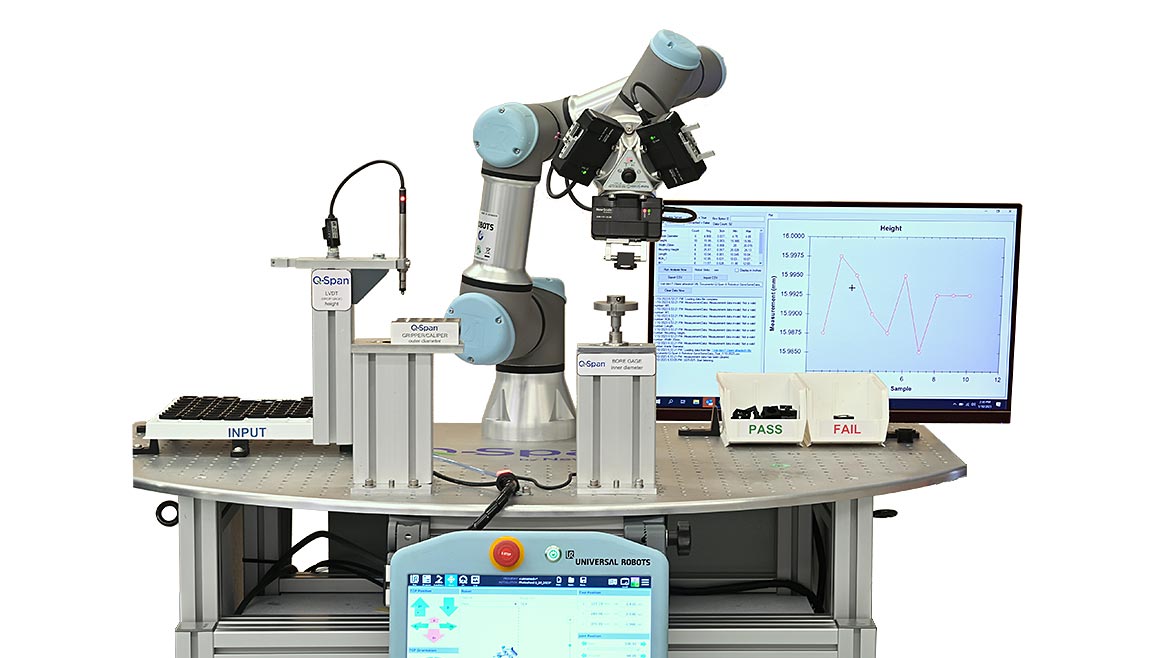
The Benefits Of Automation
An automated gaging system in precision manufacturing is a technology that uses automated equipment and software to measure and inspect manufactured parts with high accuracy and efficiency. Here's how it improves productivity and relieves bottlenecks:
- Accuracy and Consistency: Automated gaging ensures precise and consistent measurements, reducing errors caused by manual inspection.
- Increased Speed: It accelerates the throughput of your inspection process, allowing faster feedback and quicker decision-making in production lines, improving process control.
- Bottleneck Alleviation: By automating measurements, it streamlines the inspection process, preventing bottlenecks caused by manual inspection or slower measurement methods.
- Improved Production Efficiency: Reducing the time spent on inspection allows for more efficient use of resources, enabling higher production capacities and reducing overall costs. For example, allowing machinists to spend more time running machines and less time on inspection.
- Employee Retention, Less Manual Labor: Automation reduces the need for tedious manual labor in measurement processes, freeing up human resources for other critical tasks that are more appealing to people with a variety of skills.
- Integrated Data: Software systems work with the automation platform to measure data which can then be exported in a number of formats allowing for importation into an existing Quality Management System (QMS) or Statistical Process Control (SPC) software system for analysis and storage. Measurement data can also be sent back to your CNC machine to set automatic tooling offsets, creating a closed-loop, lights-out machining process.
Overall, an automated gaging system not only ensures accuracy but also helps streamline production processes, speeding up operations, improving process control, and mitigating potential bottlenecks, leading to increased productivity in precision manufacturing.