Manufacturing automation is increasing and becoming easier to use, and experts say it gives quality control workers who adopt it a significant advantage in their careers.
Manufacturers’ use of automation is growing year-over-year, and every year automated systems become easier to use, making it easier for new quality control workers to learn how to use a robot or deploy new software, says Stefan Friedrich, marketing manager, New Scale Robotics.
“We help customers deploy robots to automate quality control, specifically dimensional gaging using collaborative robots. A cobot fundamentals course from Universal Robots only requires two days of training, so it’s becoming easier than ever to get up to speed on the latest technology and deploy it for your organization on your own,” Friedrich says.
Quality control workers that know how to apply automation have an up and are more likely to add value to their organization, Friedrich says. Because of this, they are more likely to get promoted and take on additional responsibilities.
“This could be anything from using a robot to physically manipulate and automate gaging processes, or even just automating data collection and/or statistical analysis to better monitor the quality of a production process,” he adds.
When automating gaging, the same metrology fundamentals still apply.
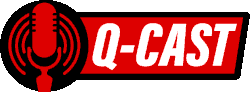
Consider What Automation Can Do For You
While companies may think automation is too cost-prohibitive or complicated, Martin Buena-Franco, automation products manager at The Raymond Corporation, says that is not the case. Here he dispels these myths and others and explains how automation could benefit your manufacturing process.
Listen to more Quality podcasts.
“The difference is that a robot is doing the work, instead of multiple inspectors. The manufacturer benefits from all of the obvious labor saving and capacity advantages automation brings, but also improved gage repeatability and reproducibility, improved yields and lower scrap, and fewer bad parts being shipped,” Friedrich says.
The workers also benefit from automating redundant tasks, he adds. “They can get rid of some dull and repetitive work, and move on to more complex and rewarding assignments,” Friedrich explains.
Automation can improve quality by reducing errors and boosting consistency, says Martin Buena-Franco, automation products marking manager, The Raymond Corporation.
“Real-time monitoring, made possible by automation, helps standardize processes,” Buena-Franco says, but it’s important to choose the right automation system and to have the right skills to use it.
“Quality control workers need to learn how to effectively use automation as a tool to establish standardized processes and achieve their goals,” Buena-Franco explains. “Integrating automation into existing quality control systems and training workers to identify and address errors is crucial.”
Gaining knowledge about new automation tools also helps. Vision technology can detect errors at the end of a manufacturing line, for example, but operators require training to understand its capabilities and requirements, such as proper lighting, object detection, data sampling, and more.
“It’s important to know how to apply it and maintain it in good working order to use it in quality control processes,” Buena-Franco says.
Enhancing Quality Control
Manufacturers are increasingly adopting robots for quality control and closed-loop production, using automation and interconnected systems to improve processes and monitor performance.
“Deployments of robots for QC tasks typically lag behind more production focused automation tasks, like machine tending, welding [and] packaging,” Friedrich explains. “We are seeing many more manufacturers adopting collaborative automation for quality control.”
Friedrich is also seeing a push to closed-loop production processes that combine an automated production task, alongside automated gaging to automatically correct the production process.
“A great example of this is lights-out machine tending. Many manufacturers have deployed robots for CNC machine tending, but an operator still has to come over periodically to gauge the parts and monitor wear on their machine tools,” he says. “You can use a robot to automatically load and unload parts from a CNC machine, then use another robot to clean and gauge the part, feeding that QC data back to the CNC machine to better control the process by applying automatic machine tool offsets, or alerting machinists to complete preventative maintenance on the machine, like swapping out a machine tool.”
Automation is being implemented more and more in facilities, with data coming from different systems throughout the facilities, Buena-Franco says.
“Because of this influx of data, interconnected systems like Labor Management Systems, Warehouse Management Systems and telematics are trending,” he explains. “Interconnected systems aggregate all the data, giving a more holistic picture of the facilities and helping to identify bottlenecks and fine-tune systems and processes.”
Process And Training Challenges
Choosing the right process and managing gradual change are key challenges in automating quality control, which improves accuracy but needs staff training and collaboration.
“Picking the right process to automate is often the biggest challenge we see when automating quality control,” says Friedrich. “This can be a struggle for anyone: automation pros that have deployed dozens of robots, or first-time robot users. With new collaborative technologies, automation is becoming more accessible to anyone, but you need to know how to define your scope of work and incrementally automate.”
When considering automating quality control, Friedrich advises manufacturers to treat it as they would any other automation project: pick the process that is the simplest and most time consuming, “not the hardest task that gives your team the biggest headache,” he says. “If a person cannot do the task, it will likely be difficult for a robot.”
Approaching automation incrementally is important, particularly if your team is just getting started with robot deployments, Friedrich adds.
“Many think automation must be an all or nothing task, thinking they need to automate the entire process to justify the investment. This is not necessarily true,” he says. “If you have a production process with a dozen steps, you may find that automating steps three and eight in that process will provide sufficient ROI and move you along the path of eventually automating the entire process.”
This incremental approach helps organizations divide the big goal into more manageable steps and costs, reducing the risk of the project, minimizing schedule and scope creep, and building momentum.
Keep in mind that staff may resist change, Buena-Franco says. Leaders may need to step up cross-department training and work on change management, he says.
As automation becomes increasingly promising, manufacturers must remain flexible and leverage their workforce to continuously improve their processes, says Michael Muldoon, director of sales and business development, AV&R.
“By working towards this you will be able to unlock the potential of an existing workforce to use their knowledge to realize quality and efficiency gains,” he says.