Computed tomography (CT) scanning is one of the most advanced measurement technologies available today for medical device manufacturers and molders. This vital metrology asset captures data at a resolution of 5 to 7 microns and is capable of mapping a three-dimensional (3D) part in less than 30 minutes. Engineers, quality teams and project managers who use CT scanning can reduce time-to-market, project costs and risk. They can also increase medical industry compliance and improve the speed, accuracy and depth of their analytical capabilities.
Importantly, CT scanning also improves product manufacturability. Plastic injection molders who use this nondestructive testing (NDT) technique can perform first article inspection, assembly analysis and reverse engineering activities. Applications for CT scanning also include part-to-CAD and part-to-part comparisons, showing a 3D color map highlighting any and all form deviations. By accelerating projects and allowing plastic injection molders to literally see inside parts, CT scanning supports the rapid identification of design issues and the efficient resolution of production discrepancies.
Understanding CT Scanning
In medical diagnostics, where CT scanning can be used instead of exploratory surgery, the technology’s benefits are well-known. But this inspection technique is also highly valuable for industrial metrology. CT scanning is a nondestructive, noncontact technology that creates a virtual model at a resolution on par with a traditional coordinate measuring machine (CMM). X-ray measurements taken from many different angles create tomographic or cross-sectional images. These virtual slices represent specific areas of the scanned object.
Patient scanning differs from part scanning in several important ways. Medical CT scanning is limited to a few seconds to minimize a patient’s exposure to radiation. However, industrial CT scanning can take longer and usually lasts between four and 60 minutes, depending on the resolution. If a nanometer-level resolution is required, a 3D scan may even last several weeks.
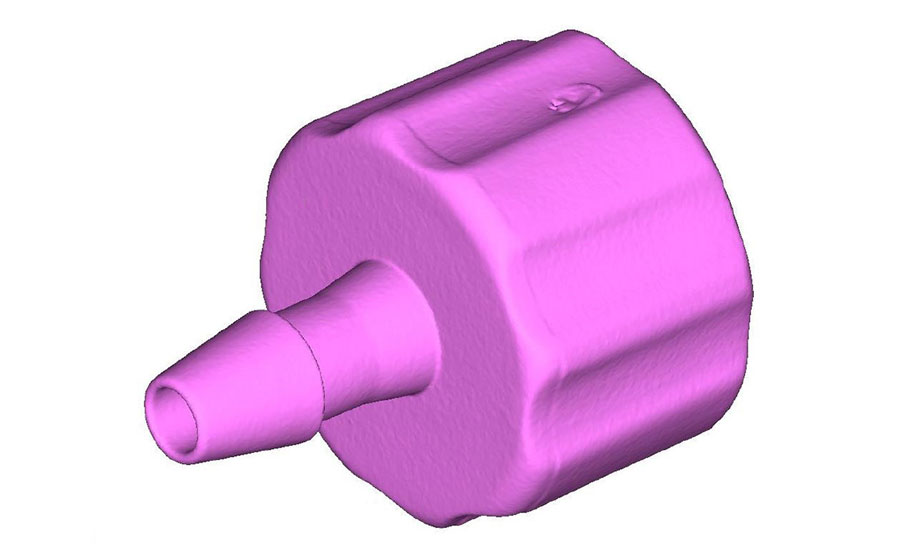
Reverse Engineering Actual Part
Industrial CT scanners also differ from medical CT scanners in that they have limitations with mixed material components that contain metals. Unlike polymers, metals tend to diffract X-rays and can contaminate the analytical data. Metal artifact reduction (MAR) algorithms can reduce this “noise” effect, but they also alter the detected boundary surface of the plastic. Therefore, MAR algorithms are recommended only for qualitative analysis.
For many manufacturing companies, equipment costs are a major consideration since a rapid industrial CT scanner can cost eight times more than a coordinate measuring machine (CMM). Part analysis can also take longer with CT scanning. Speeds are improving, however, and the per-part CT analysis will eventually cost less than traditional inspection methods. By partnering with an experienced provider of CT scanning services, medical designers and developers can realize CT’s benefits today while positioning themselves to benefit from future enhancements.
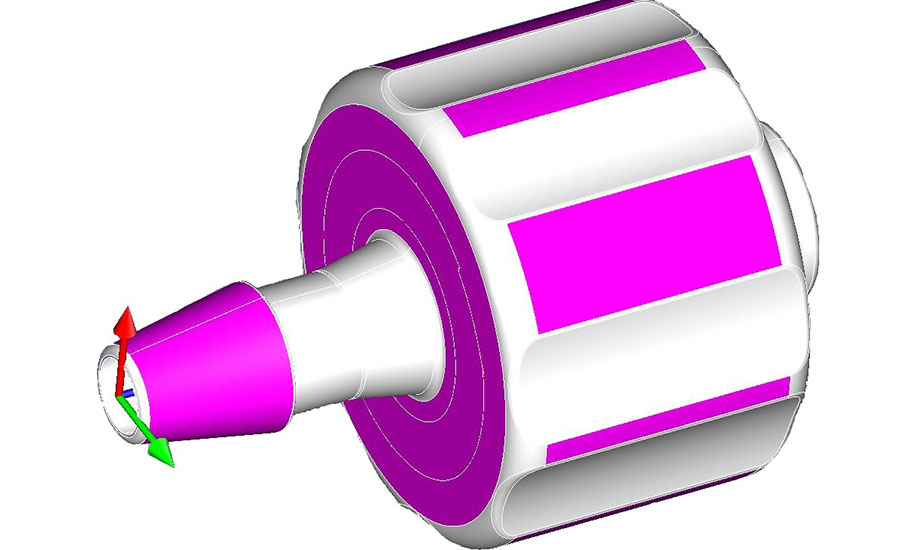
3D CAD
Comparing CT Scanning to Other Technologies
CT scanning is continuing to change how medical device manufacturers perform metrology and record the results in quality systems. By using CT scanning to solve a range of development and production challenges, users can gather inspection data that was previously unobtainable. For example, they can achieve:
- NDA inspection of assembly interiors for leaks prior, during and post activation
- Interference fitting of O-rings inside assembled devices
- Interference fitting for housing components and the ability to calculate steel modifications required to improve assembly
- Evaluation of ultrasonic weld integrity post welding and measurement of welding splash
- Mapping of tool wear from part-to-part variations
- Measuring dimensions inaccessible to a CMM probe or without a line of sight
- Component location post assembly
Engineers value this information, but they also prized CT scanning for its depth and accuracy.
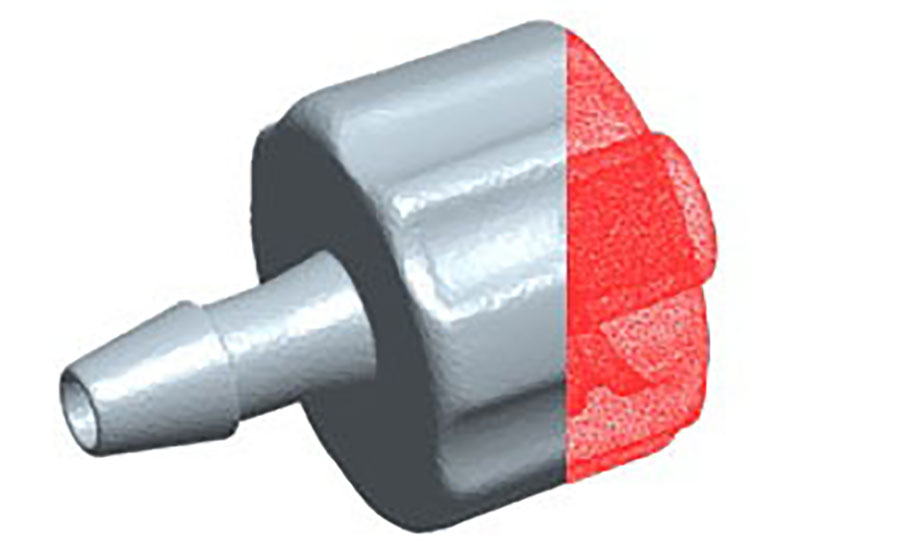
3D scan surfaces
Ultimately, switching to CT scanning involves calculations of cost and speed. CMMs and machine vision systems cost less but require time-consuming fixture validation with gage repeatability and reproducibility (R&R) activities. In contrast, CT scanning eliminates fixturing altogether. Instead of controlling a CMM or stage, a software layer controls a virtual machine. Then, instead of returning a single coordinate upon contact, CT instantaneously returns thousands of “pick points” for greater statistical confidence and little to no variation on repeat runs.
Yet CT scanning is more than just a fixture-free substitute for older inspection methods. CT can also discover part defects that are otherwise difficult to detect and even harder to quantify. There are cost savings, as well. For example, because molds can be validated and shipped without fixtures, project timelines can be reduced by an average of eight weeks. If the manufacturing runs are short then CT can eliminate the requirement for fixtures entirely, and further speed up the validation activities by four to six weeks.
CT scanning is ideal for the first article inspection of injection molded plastic components since it can detect, measure and monitor form errors such as warping, sinking and shrinking. CT can also detect “short shots” that occur when enough plastic isn’t injected. Additional applications include detecting voids inside the component, locating flashing and identifying the presence of foreign matter. Reporting follows the traditional structure of dimensional analysis, but also includes three-dimensional color mapping.
For example, 3D color maps can show an overlay of a plastic part atop the nominal 3D CAD file issued from the design team. For both plastic components and assembled devices, the scan can be rotated, zoomed, cropped, clipped, separated and explored in an intuitive 3D interface. Warmer colors indicate extra material, while colder colors signify missing material. This 3D analysis supports point-and-click manual measurements along with void/inclusion analysis so that users can see any unwanted form errors or voids inside the plastic.
For assemblies, CT scanning can determine how various components interact with each other. Design teams can then see how each component interacts under high or low temperatures while applying different forces. Designers can also assemble devices virtually and improve their overall accuracy based on improvements to the individual components. Enhanced simulations can also account for defects that are created during the manufacturing process.
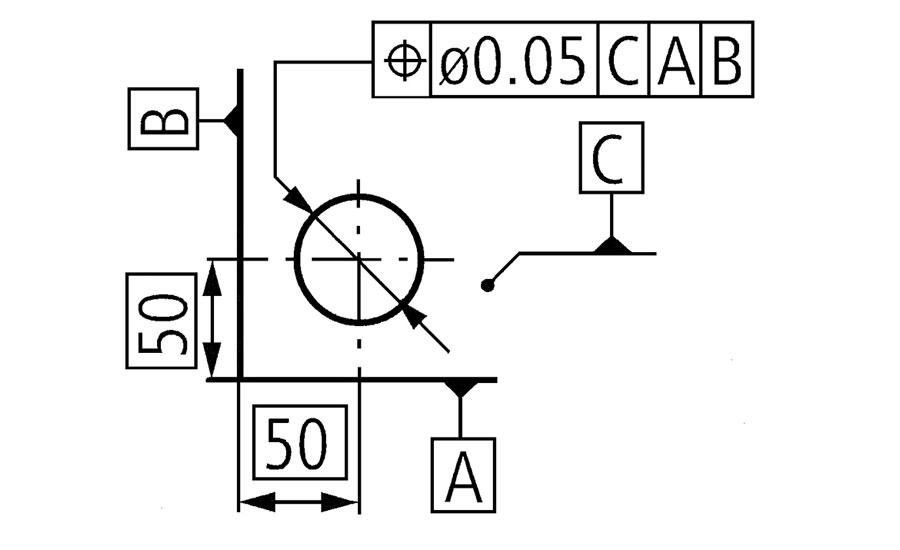
First Article Inspection (FAI) Reporting and Dimensional Analysis
Examples of CT Scanning’s Effectiveness
CT scanning has consistently been employed to successfully help companies with challenging device and component investigations. For example, one company reported interference issues with a device, in which a curved button somehow seemed to warp during assembly. Traditional dimensional analysis hadn’t revealed any defects and all the individual components met their metrology requirements. By scanning the assembled device, however, the interference became visible in a specific area. CT scanning provided proof of the problem’s source, allowing the company to resolve the issue promptly and continue development.
CT scanning also pinpointed leakage problems with a micro engine that was roughly the size of a small fingernail and that incorporated as many as seven micro-components. By recording videos of the device during operation one company was able to examine a piston seal inside a manifold without disassembling the engine. CT also supported the use of a high-contrast fluid for locating and measuring trapped air inside the device during its operation at different angles. By identifying form-related issues, CT scanning discovered defects in plastic molded components that could affect device operation.
CT even helped solve a stubborn defect in a part that had been manufactured for almost a decade. Despite numerous attempts to determine the source of the error, the manufacturer reported continuous changes in metrology data for a critical dimension. At most companies, engineering meetings about the same problem are time-consuming, frustrating, occasionally heated and very expensive. Thanks to CT scanning, however, a void was detected whose position and magnitude varied around a critical area that caused variable drift depending on where the void sat. A quick design of experiment on a process run solved the problem.
CT was also used to check the interference, fit and seal of an applicator device and cap. Scanning the fully assembled device allowed interference measurements to be taken for different sections. CT also supported correlating these results to data obtained from a tensile tester. This analytical loop fed back into a tolerance stack-up analysis that verified the acceptable deviation allowed during manufacturing. A full first article inspection was also performed on individual components prior to assembly.
After multiple actuations, CT scanning verified the dimensional and force results throughout the device’s life cycle. This helped to ensure that the device would perform to specifications over its entire life. Using CT scanning for this task enabled completion of an in-depth analysis in two days. Traditional inspection methods would have provided data with less confidence, requiring multiple fixtures and significant verification activities. Thanks to CT scanning, the development cycle was cut by eight weeks with a significant reduction in cost.
Validation and Compliance
CT scanning is enabling engineers, quality teams and project managers to reduce development times, project costs and risk. CT also supports increased medical industry compliance while improving the speed, accuracy and depth of a manufacturer’s metrology capabilities. Not all CT scanning services are internally-validated and 21 CFR Part 11 compliant, however, so it’s important for medical device designers and developers to understand a potential partner’s capabilities.
Experienced providers of CT scanning services can help medical device designers meet and exceed all required standards in device guidelines for metrology systems. This ensures that audits performed on metrology processes will prevent any findings that could result in a product recall or unplanned rework.
Importantly, CT scanning also improves overall product manufacturability. As per-part analytical costs continue to fall, this vital metrology technique will replace traditional inspection methods. As one of the most advanced industrial measurement technology available today, CT scanning will become an increasingly important part of injection molding. By leveraging computed tomography sooner rather than later, medical device designers and developers can position themselves to achieve the maximum benefits.