Vision & Sensors | Automation
Metrology Automation Finally Arrives
The smart start to metrology.

All Images Source: Hexagon Manufacturing Intelligence
We often use buzzwords in the manufacturing business such as Industry 4.0 and digital twin as if there were clear definitions of what these terms encompass. I am often in meetings with customers who state they are trying to “automate production” or are looking for an “Industry 4.0 showcase installation.” However, as you drive deep into the specifics of the implementation plan, I frequently walk away with the feeling they have not mapped out their own manufacturing process. And in many cases, they do not fully understand how to leverage new metrology technology and the impactful data immediately available for analysis and decision-making.
Manufacturers are now embracing the move to the digitization of their production processes. Many initial project goals are very narrowly focused around removing manpower, manual errors, and running 24/7 to improve total output. These are all worthy goals for sure. Yet, this approach leaves many facets in their overall process often overlooked. There are critical questions that must be asked. How can the upfront programming and integration effort be reduced? How can downstream quality data be leveraged to react more quickly and efficiently in the manufacturing process? What method can be used to make production turnover between products easier and more efficient? How can part design changes or manufacturing process changes be easier to implement? How can overall equipment effectiveness (OEE) data be used to improve production workflow or predict hardware downtime?
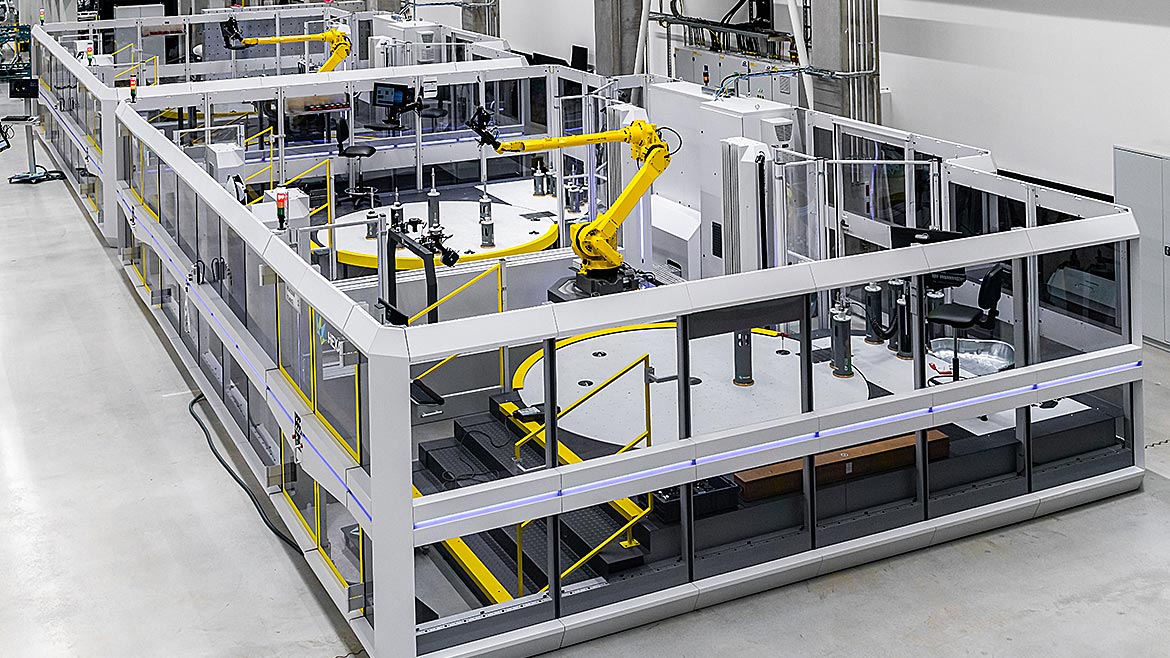
Portable measurement combined with automation solutions enables lab-grade metrology technology on the shop floor in-line, near-line, and off-line.
Metrology, A Good Place To Start
These questions are all challenging to answer and overwhelming to someone implementing their first “automation” solution. However, it is very important for the customer to understand that there can, and should, be a roadmap established at the very beginning of a project. This overall plan allows for future expansion during the digitization journey and garners maximum ROI for the system. There also needs to be a clear cut place to start an automation project…and there are a variety of affordable and non-disruptive solutions that will get a manufacturer’s feet wet, without a full scale tsunami shutdown of operations.
For companies with coordinate measuring machines (CMMs), a lights-out metrology system that automates the inspection process is an ideal entry point. This type of implementation tends to be far less disruptive to daily operations, as measurement tasks can be performed across multiple inspection systems. Testing can occur systematically on each measurement system, according to a smart automation roadmap. Ultimately, quality control processes can continue during the implementation of a lights-out metrology system, contingent upon the company having more than one multipurpose inspection system.
How does a lights-out system work? In a nutshell, these fully automated solutions provide autonomous measurement of parts on a coordinate measuring machine and automatically identify out-of-tolerance parts. Designed to be an off-the shelf addition to new or existing CMMs, these systems integrate easily into established workflows. Configurable with multiple, easily accessible drawers, a system can be loaded with a full shift’s worth of parts and set to run without further operator interaction. Furthermore, sophisticated software enables an operator to load drawers and queue inspection programs as the system is running, allowing for uninterrupted operation. A collaborative robot arm manipulates the parts and fixturing on the CMM. In addition to the light’s out advantages, these systems also perform high volume, repetitive tasks allowing for the improved utilization of highly skilled machinists and reduce the potential for repetitive stress injuries. During the ebb and flow of business, factories of any size can maintain output even when their own CMM operators are unavailable.
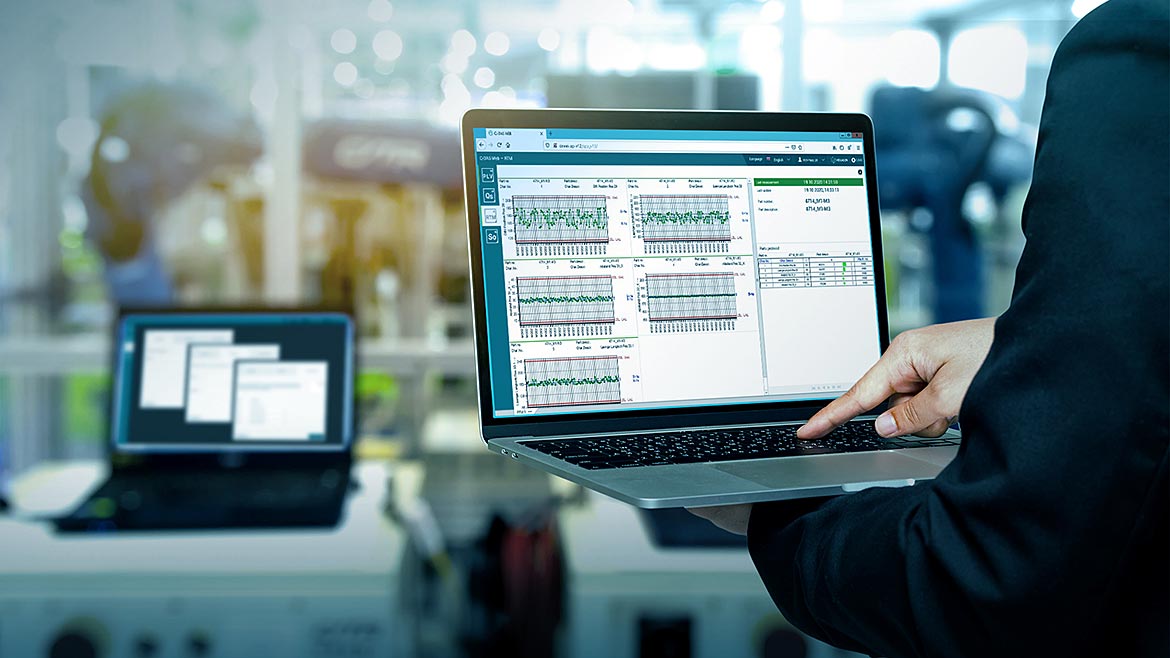
This measurement data management software acquires metrology data from every production site to provide a single reliable source of quality data. The solution manages data throughout the manufacturing process so that tools can automatically compare inspection data to design data to ensure product quality.
Software Drives Metrology Automation To The Next Level
Oftentimes, dimensional and other types of inspection tend to be the singular process that occurs outside of the manufacturing and assembly processes. Although there are tremendous benefits to automating metrology with batch loading processes as described above, the natural evolution of metrology in manufacturing is to push quality or inspection into the production workflow, supplementing or even replacing traditional in-process checks.
It is an exciting time for automotive design and manufacturing as all of our accumulated technology advances are being applied to the evolving frontier of electric vehicles. At the same time, carmakers are taking serious steps to push into this emerging level of metrology automation and embed these traditional laboratory quality inspections right down into their smart manufacturing facilities. These new systems are designed to measure mid-to-large sized parts and powered by the incredible accuracy of the latest laser trackers. Portable measurement combined with automation solutions gives manufacturers the ability to utilize lab-grade metrology technology on the shop floor in-line, near-line, and off-line. Supporting a variety of customer applications, laser trackers enable flexible implementations that include high-accuracy surface scanning, feature calculation and discrete point measurement that drive the highest level of quality into the manufacturing process.
These new-generation ‘scan cells’ are made possible by sophisticated software programs for robotic automation, metrology reporting and measurement data management platforms. Robotic automation software provides the toolset to efficiently plan, program and control robotic cells, as well as integrating with the wider manufacturing software ecosystem, simplifying the data acquisition process for smarter manufacturing processes. Created specifically to orchestrate the sensors, software and robotic equipment of an inspection scan cell from a single, intuitive interface, this software makes automated measurement more accessible, efficient and reliable. To maximize equipment utilization, an offline programming environment is also needed to provide accurate path simulation that allows virtual commissioning of the system and rapid deployment of programs to the real scan cell.
A reporting software solution is critical to the cause as it consolidates customers’ disparate reporting tools into one central location. This approach gives users the confidence that all their data is flowing into one tool with guaranteed access to the data when they need it. In addition to the data itself, users gain additional insights and analysis from this data, providing essential intelligence to information that would otherwise be missing.
Lastly, an enterprise IT solution is needed to structure and manage 3D measurement data, thus closing the information gap in the quality assurance process. This software provides controlled access to measurement plans, alignment systems, tolerances, measurement results, and analysis sessions. This solution should be scalable and capable of supporting small teams in an OEM department or in a supplier manufacturing site, in addition to global implementations with multiple sites and thousands of users. Also, look for some significant innovations in terms of automatic prediction (AI) functionality giving customers the ability to learn more about processes in terms of stability and potential tolerance deviation. With an automatically generated forecast, manufacturers are able to act before real problems occur.
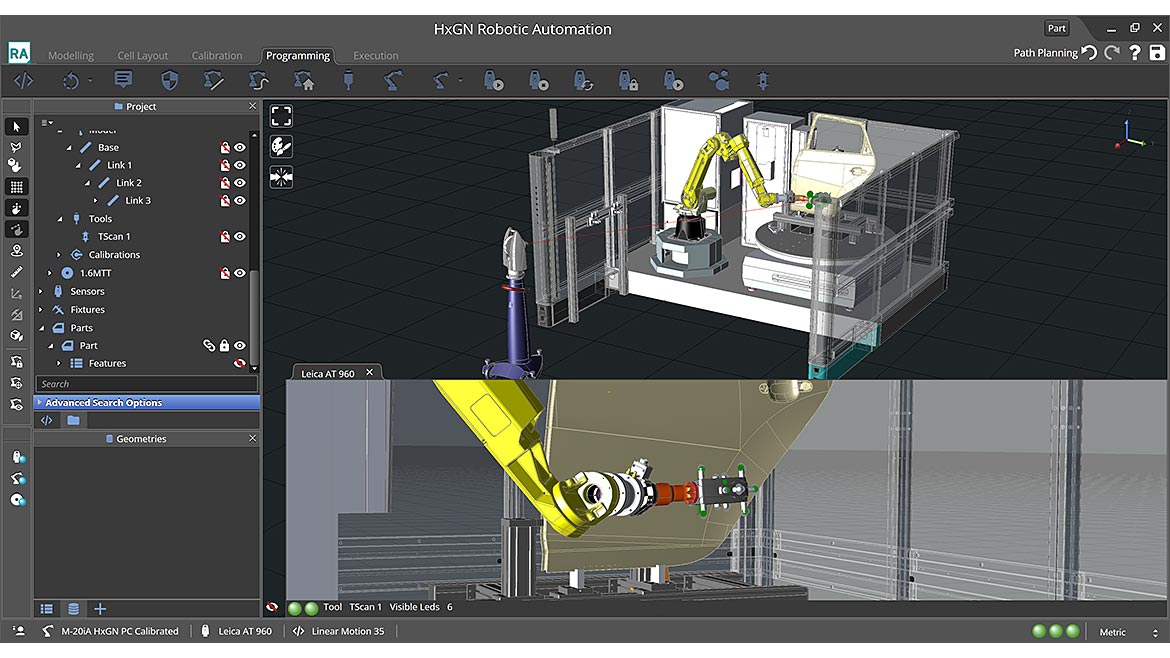
This is a flexible and scalable robotic control software designed to simplify programming for automated measurement and inspection applications.
Metrology Automation Is Shape-Shifting For Smart Factories
The planets have aligned in the metrology-assisted automation realm where robotics, 3D measurement systems, and vital supporting software solutions ensure rich data capture without the complexity of legacy automation platforms. Companies who have taken the time to develop a roadmap guiding them to smart manufacturing technologies are realizing greater efficiency, productivity and process innovation. A digital transformation can start with consecutive steps and incremental investments that do not break the bank. Taking the first step in automating quality processes can be a game changer, as a manufacturer can address current quality control challenges, and also gain an understanding of what lies further down the Industry 4.0 path for other downstream operations.
Looking for a reprint of this article?
From high-res PDFs to custom plaques, order your copy today!