Whether its manufacturing, warehousing and logistics, food processing, or beyond, automation technology has become a nearly ubiquitous presence in everyday life. The ability for systems leveraging robots, machine vision, motion control, and other complementary technologies to help companies enhance productivity and stay competitive, drive revenue, and attract and retain top talent has become invaluable.
An automation system is greater than the sum of its parts, however. In most automation systems, complementary technologies converge to accomplish a wide range of different tasks. For example, robots alone can automate many pre-programmed and repeatable tasks across different industries, but pairing a robot with machine vision technologies opens the door to significantly more applications. Ultimately, automation systems progressing and continuing to enhance operational efficiencies worldwide requires the advancement of system subcomponents in tandem.
Take lighting, for example. No matter the industry or application, all machine vision systems require light – whether visible or non-visible – to capture images. High quality output relies on high quality images, which require adequate lighting. In machine vision, illumination creates repeatable contrast between features of interest and the background, or other features, which can help overcome wide ranges of part variation, position variation, and changing part types to achieve imaging flexibility and reliability.
Novel lighting approaches designed for today’s challenging and evolving automation applications have created new opportunities and simplified existing approaches. Examples include flexible robotic inspection in automotive manufacturing, multispectral and hyperspectral imaging in food processing, and bin picking, palletizing, and depalletizing in logistics and warehousing.
Robotic Inspection Gets More Flexible
While static illumination designs suit many of today’s automation systems, dynamic configurations offer significant flexibility when it comes to dealing with part and process variations. A dynamic lighting solution also offers variable geometry, which allows for the use of more than one type of lighting geometry in an integrated, compact unit. Dynamic lighting also offers the ability to change the illumination wavelength or intensity quickly for short production runs of widely varying parts, oftentimes on parts of the plant floor where size and space constraints present challenges (Figure 1).
Take the industry in which automation is most prevalent – automotive manufacturing – for example. During body assembly, adhesive beads are applied during multiple steps, including joining inner and outer panels and applying noise suppression or sealant materials to panels. These beads must be inspected for width and volume as well as the presence of skips, bubbles, or voids. Systems integrators often affix a camera to the end of a collaborative robot (or traditional robot) arm to perform these different inspections, but doing so requires lighting that can accommodate different inspections, which may include presence/absence, defect detection, color matching, color identification, alignment, and more.
When performing multiple tasks such as these, the ideal lighting can vary by inspection type, which may have traditionally meant changing out the lighting for each step, which adds time and costs to the scenario. Novel lighting designs, however, have removed the need for additional lights for individual inspections. Multifunctional lighting units – which include dome light, low-angle dark field ring light, mid-angle dark field ring light, RGBW ring light, four-quadrant ring light, NIR ring light, and sequencing controller – enable advanced control capabilities for disparate inspection tasks, without having to change the light (Figure 2).
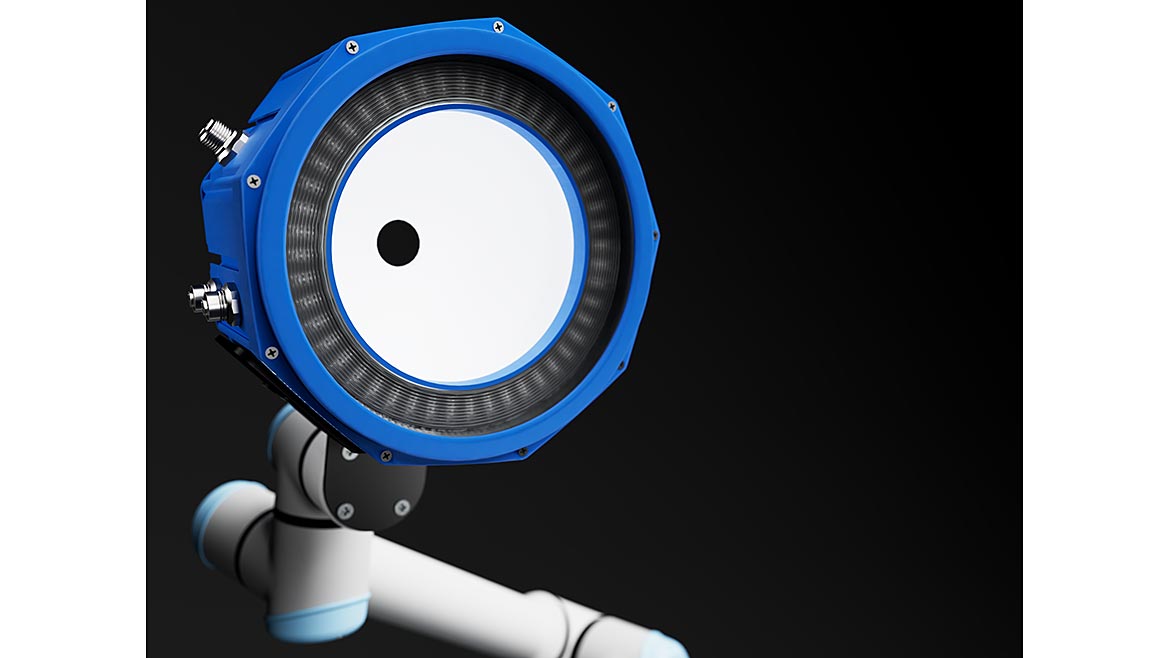
Tire inspection represents another key application where specialized lighting implementations are required. Challenges emerge when using machine vision technology to read raised letters, black-on-black text such as Department of Transportation (DOT) tire identification number (TIN) or other data such as brand, model, or tire size. In addition, the embossed and debossed nature of the tires makes imaging that much more difficult. To solve this challenge, a photometric stereo technique is often implemented, where a single high-resolution camera captures illumination of a tire surface from different angles in multiple different images so that software can combine the images and create a profile image of the tire sidewall.
A traditional photometric stereo implementation may involve the use of four different lights positioned at different angles separated by 90°– so 90°, 180°, 270°, and 360° -- around the tire perimeter, controlled by an LED controller. As the camera triggers an exposure, the controller triggers a light from a different direction, illuminating the tire and capturing different images for the software to reconstruct. By deploying a multifunctional lighting unit with four-zone multi-drive LED driver and multiple lighting options onto the end of a cobot arm, systems integrators have the added flexibility of moving the camera directly to the tire to read and verify codes, while removing the need for four different lights.
Automate Food Quality
Elsewhere, in the burgeoning food processing industry, several different types of automation technologies – including robots and machine vision – come into play, but these applications often require specialized components and technologies. Examples include food-safe soft robot grippers, washdown-rated enclosures, and specialized imaging devices such as multispectral cameras, which can aid in foreign object detection, quality analysis, and content analysis, while providing robots the data required to make picks and place items into a tray or carton for packing.
Vision & Sensors
A Quality Special Section
Different options exist when it comes to deploying multispectral imaging systems, including the use of fully integrated multispectral cameras or a simplified approach that leverages multispectral lighting with independently controlled RGB lighting channels and a grayscale camera. With the later method, the light source cycles through each individual color channel and the camera captures a subsequent image from each channel corresponding to the object’s reflectance for red, green, or blue, and combining the three images into an RGB image.
In this simplified setup, other features can be isolated from the RGB image based on how they respond to the individual lighting channels. For example, a multispectral lighting setup with SWIR LED wavelengths, a grayscale InGaAs camera, a four-zone lighting sequencer, and a lighting driver can help reveal details on fat, bone, and meat content in raw pork chops. Images from four different wavelengths are captured, generating an image cube (or a stack of images in which each image corresponds to a discrete spectral band. The resultant image cube shows that the fat, muscle, and bone reflect light differently depending on the wavelength band selected. Basic arithmetic is done on the image cube, producing images in which either the bone or the various fat tissue types are accentuated in high contrast to the other parts.
Different multispectral lighting options exist on the market today, including linear, ring, bar, and brick formats covering white, UV, blue, cyan, green, red, infrared, SWIR, RGB, and RGBW lights. For environments where the product and/or inspection type change, or in environments where the integrator and customer are looking to save on space, cost, and effort, a multifunctional lighting unit can be deployed. A recently introduced novel lighting solution incorporating RGBW as well as NIR and UV wavelength capabilities along with extra ports to connect auxiliary lights such as spot or linear lights — all in the same system — allows the imaging system to cover any spectrum.
Keep Pace in the Warehouse
Warehouse and logistics environments with e-commerce represent another industry primed for significant growth in terms of automation adoption. For a snapshot into this segment, take the fact that the warehouse automation market in China – the largest market for industrial robots in the world – is predicted by market intelligence company Interact Analysis to expected to grow at a compound annual growth rate of 13.5% over the next five years.
Warehouse automation involves several different types of technologies, including autonomous mobile robots, automated guided vehicles, traditional industrial robots, collaborative robots, machine vision, barcode scanning, motion control, and more. In recent years, the market has seen a rise in application-specific automation systems purpose built for a specific task that help further democratize robotics by focusing on ease-of-use and cost-effectiveness.
High-speed pick and place systems combining robots, software (often including artificial intelligence capabilities), and machine vision, for example, help optimize the picking and placing of mixed items products, bags, and parcels. In such a scenario, mixed items enter on a conveyor that moves items into a robot cell, where an overhead vision system identifies items and makes decisions on which products should be picked next (Figure 3). Software then instructs the robot to pick and place the next item onto the downstream location while a quality check ensures pick success.
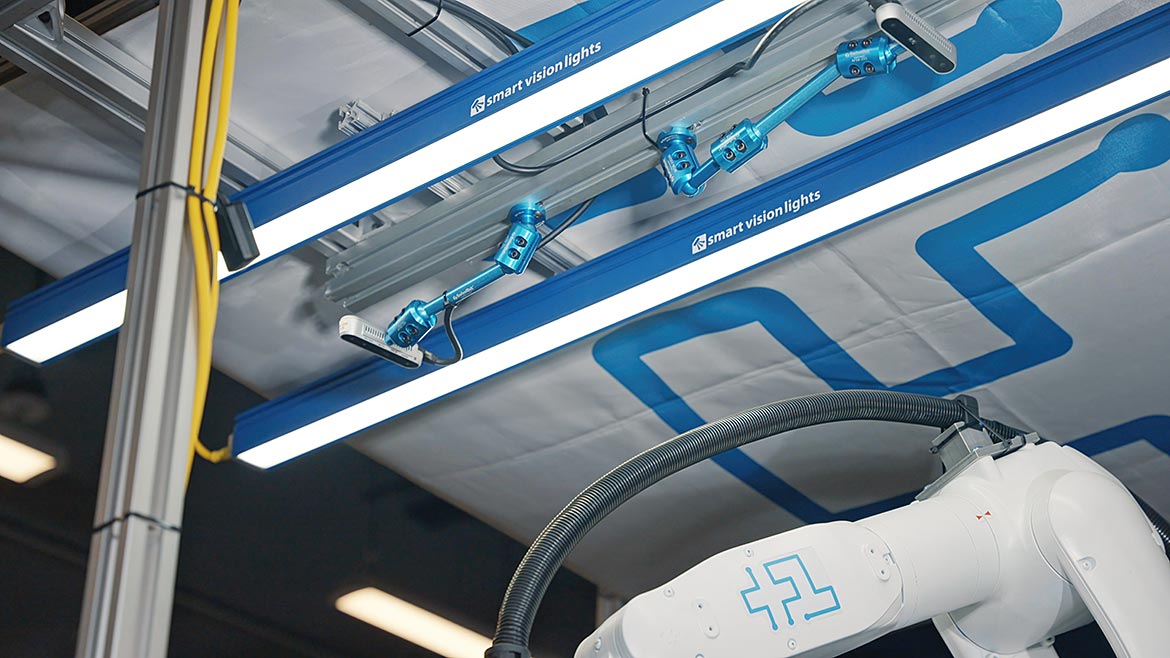
When seeing such a system in action, much of the focus might be on the robot’s high speed, accurate picks of various items, but pick success is contingent upon several contributing factors – including consistent, controlled lighting. Integrating the ideal illumination setup for such a system creates a more robust and repeatable process, particularly when considering the variability of the products that such a system deals with. High-quality lighting is ultimately key to any successful application-specific system that leverages machine vision lighting, and each system may require different lighting formats, wavelengths, and intensities. Systems integrators and OEMs today, of course, have a wide range of options from which to choose, including lights in bar/linear, ring, brick, dome, backlight, spot/project formats or multifunctional lights that include six different lighting options in one.
Automation Advances On
Manufacturers around the world will continue to seek out new technologies and processes to keep pace in an increasingly competitive world, while also looking to protect themselves against factors such as labor shortages and supply chain issues. As a result, suppliers within the automation industry will continue to innovate and provide systems integrators and OEMs with the solutions required to build the automation systems of today and tomorrow. When designing an integrating such systems, however, don’t wait to specify the lighting until the last minute, as a properly designed and implemented lighting system can significantly improve the capabilities and effectiveness of any system leveraging machine vision.