In the field of nondestructive testing (NDT), industrial ultrasonic testing (UT) is a long-established method for ensuring the quality of critical composites, metals, alloys, and industrial assets with complex geometries. However, new materials and components are finding their way to the industry, requiring continuous technological advances to improve the reliability and, most importantly, the practicality of ultrasonic technology. As industry faces increasingly stringent regulations and standards compliance, a shortage of qualified personnel, and increasing inspection requirements in all industries worldwide, the need for smarter, more efficient inspection methods has become paramount.
While in the past R&D focused primarily on improving and refining hardware, today’s efforts include electronics and software-based automation in UT inspection solutions - from large testing machines to manually operated handheld devices. Where previously many mechanisms had to be controlled manually, the goal now and in the future is to drastically reduce these mechanics, increase automation and operator support in industrial UT inspection and provide a multi-dimensional and more compact technology which ensures the highest possible defect detection and reduces the potential for human error in operation.
Matrix technology: a leap beyond phased array
Phased array ultrasonic testing (PAUT) has changed the NDT landscape, offering improved flexibility and accuracy compared to conventional methods. In contrast, a conventional ultrasonic probe or transducer relies on a single crystal to generate ultrasound, which can only produce a single A-scan image at a specific location or spot. The path of the beam is one-dimensional with a fixed shape, orientation and angle of propagation. Unlike conventional UT systems, the beam of PAUT systems can be shaped, for example focused, and the beam angle can be changed electronically. However, with rising demands in inspection quality, a new trend in ultrasonic testing has emerged – the utilization of matrix technology.
Matrix and phased array ultrasonic testing differ from conventional ultrasonic methods in that they use multiple elements to transmit and receive sound waves. Originally rooted in the healthcare sector, where matrix-array ultrasound has proven its worth, it is now paving its way into industrial testing. In this advanced approach, the active transducer area is carefully designed to consist of a multitude of ultrasound emitting and receiving elements strategically arranged in a checkerboard, ring, or spiral pattern. This intricate design allows for electronically controlled, multi-dimensional sound field manipulation and provides the highest flexibility, detection sensitivity and resolution.
NDT
Related Article
Matrix technology represents the next evolutionary step beyond phased array, offering a more flexible and advanced approach to ultrasonic inspections with less mechanical effort. This is especially valuable as time and skilled personnel are chronically in short supply. The main advantage of matrix technology in the industrial sector is its ability to reduce human error through simplified operation and to improve and speed up overall functionality through enhanced electronics, thereby increasing the overall quality of inspection results. The trend continues to benefit from more automation and more functionality.
The technology is evolving rapidly. Ongoing efforts are being made to improve the spatial resolution of matrix array probes. Matrix technology only leverages its full capability in combination with powerful ultrasound electronics which developed in recent years. This allows for more detailed and accurate imaging of materials during inspection. Originally used in the aerospace and healthcare industries, it is now finding its way into other industries such as automotive, oil and gas, rail, and manufacturing. The versatility of matrix arrays makes them suitable for a wide range of materials and components. Matrix array probes are being used more frequently and complement imaging techniques such as Full Matrix Capture (FMC) and Total Focusing Method (TFM) to provide improved defect detection and sizing capabilities. The sophisticated probes are designed and tailored for specific applications and inspection scenarios to ever increase efficiency and accuracy.
Reducing complexity of inspection tasks
The integration of automation and electronics into complex industrial UT testing tasks is a building block for smarter inspections. Advances in miniaturization have led to the development of smaller, smarter and more powerful UT probes in combination with powerful electronics. This facilitates inspections in challenging environments and improves accessibility to components with complex geometries. It plays a crucial role in streamlining and simplifying complicated inspection processes. This is especially true in the light of increasing global mobility, reducing carbon output by less weight and, hence, less energy usage, and the resulting higher quality requirements and safety standards of the growing mobility infrastructure for example.
Rigorous inspection protocols are more important than ever to meet the growing demands of mobility industries as railway and aviation – safety remains a top priority here. And inspection solutions need to help quality managers and operators to tackle these challenges.
In 2022, China reached approximately 40,500 kilometers of high-speed rail lines, making it the largest high-speed rail network in the world, according to the International Union of Railways (UIC). However, countries such as South Korea, Japan and Germany surpass China in the ratio of high-speed lines to national territory. Spain claims the second longest network with approximately 3,900 kilometers, while Germany’s high-speed ICE trains operate on approximately 1,600 kilometers of track, illustrating the dynamic landscape of high-speed rail development worldwide.
Commercial aviation, both passenger and cargo, is also trending upward. Passenger business has largely recovered in 2023 after the Covid-19 pandemic and market analyses predict a global growth of 14% YoY. The cargo sector also shows stable forecasts. As a result, the MRO (Maintenance, Repair & Operations) aftermarket gains in importance and NDT in aerospace is impacted by the recovery of commercial aviation revenues. At the same time, a shortage of skilled workers is driving the need for greater efficiency and streamlined processes. As the commercial aviation sector continues to grow, smart NDT is in a prime spot to help ensure the safety and reliability of aircraft components and structures.
Efficient under-car rail wheel inspection for rail safety
Let’s take a closer look at the railway industry as an example. As critical elements of rail vehicles, railway wheels are subject to tremendous stress, exacerbated by increasing speeds, loads, and distances. According to global railway standards, ultrasonic testing is a mandatory practice to ensure the safety and reliability of these assets. As a result of these standards and the volume of inspections, automation through electronics is necessary.
To cope with this set of requirements, state-of-the-art inspection machines have been established that allow comprehensive testing without removing the wheelset from the rail car. Since wheelsets are overly complex geometries, the mechanical effort of testing without NDT is impractical and meaningless. Potential defects are often inside the asset and not accessible without NDT. With state-of-the-art systems, a high test rate per complete wheel set is achieved in less than 20 minutes.
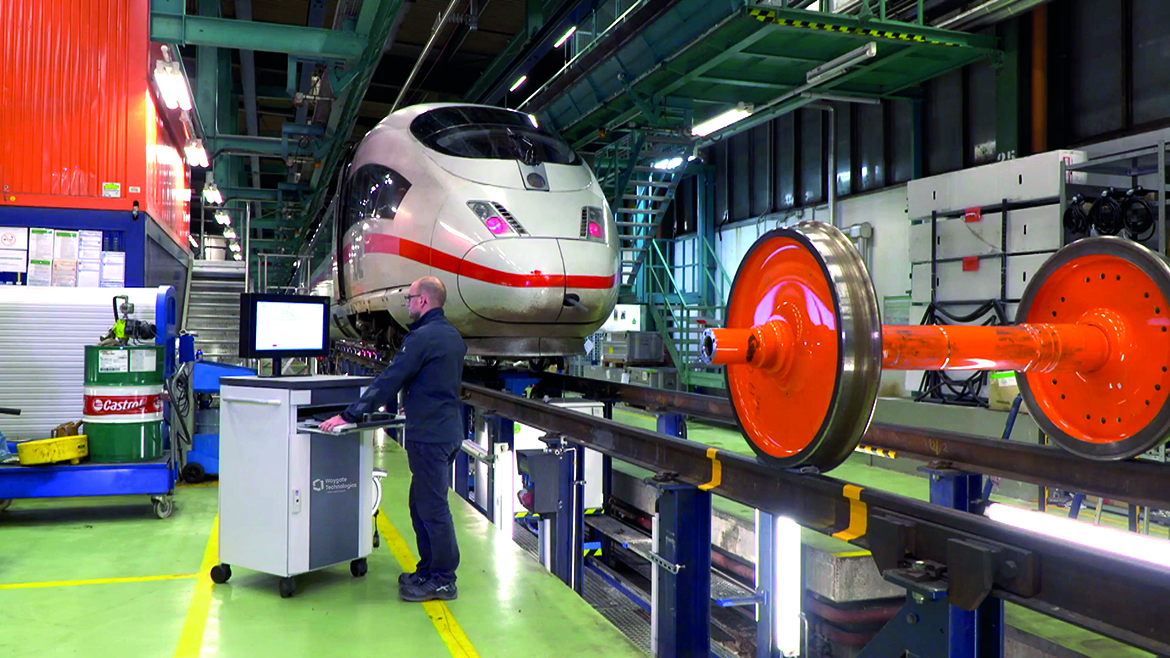
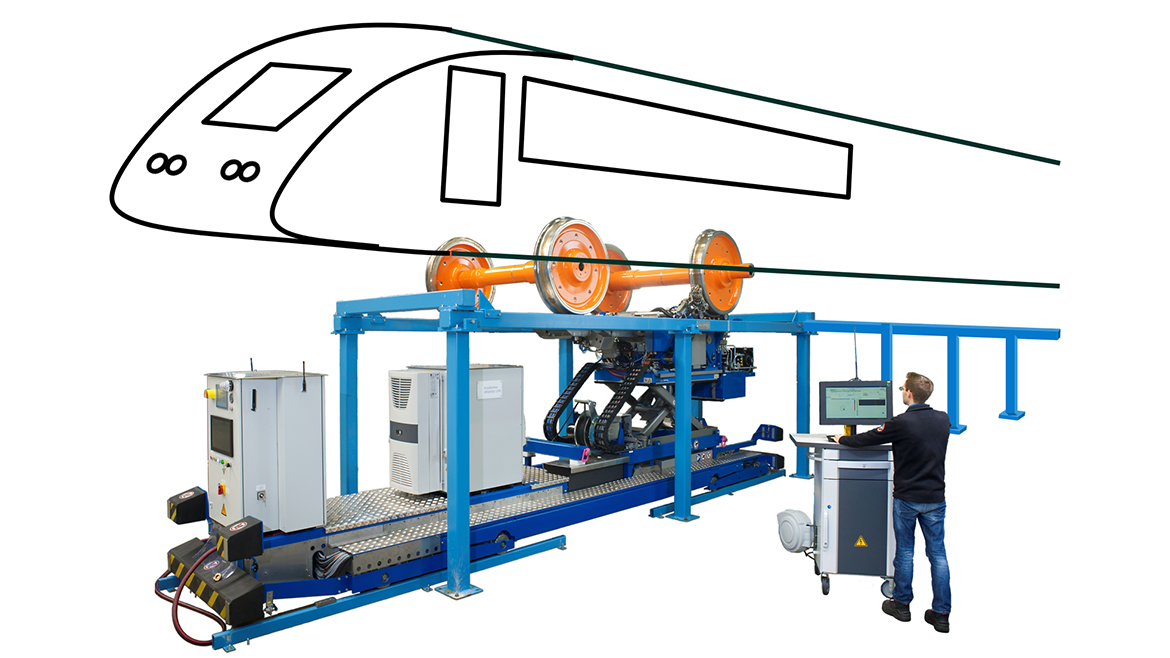
Matrix technology’s ability to dynamically adjust beam parameters allows inspectors to cover these complex geometries faster and more efficiently: Potential defects or irregularities are detected with a high degree of accuracy, reducing the risk of failures and enhancing the overall safety and reliability of rail systems.
Equally important is the ease of use including quick and easy training of staff. Integrated PLC (Programmable Logic Controller) control, for example, ensures a smooth workflow while automated reporting capabilities can further increase the efficiency of a UT system. An example calculation: A 20-minute typical cycle time including evaluation per wheel set with only 90 seconds of net inspection time per wheel maximizes productivity. Crucially, the system used eliminates the need for wheel set removal and tedious pre-positioning and streamlines job preparation with pre-programmed wheel types.
Fully automated inspection leaves no room for error. The system carefully inspects the tread, face, flange and straight web areas of the wheel and presents the results in multiple projection views.
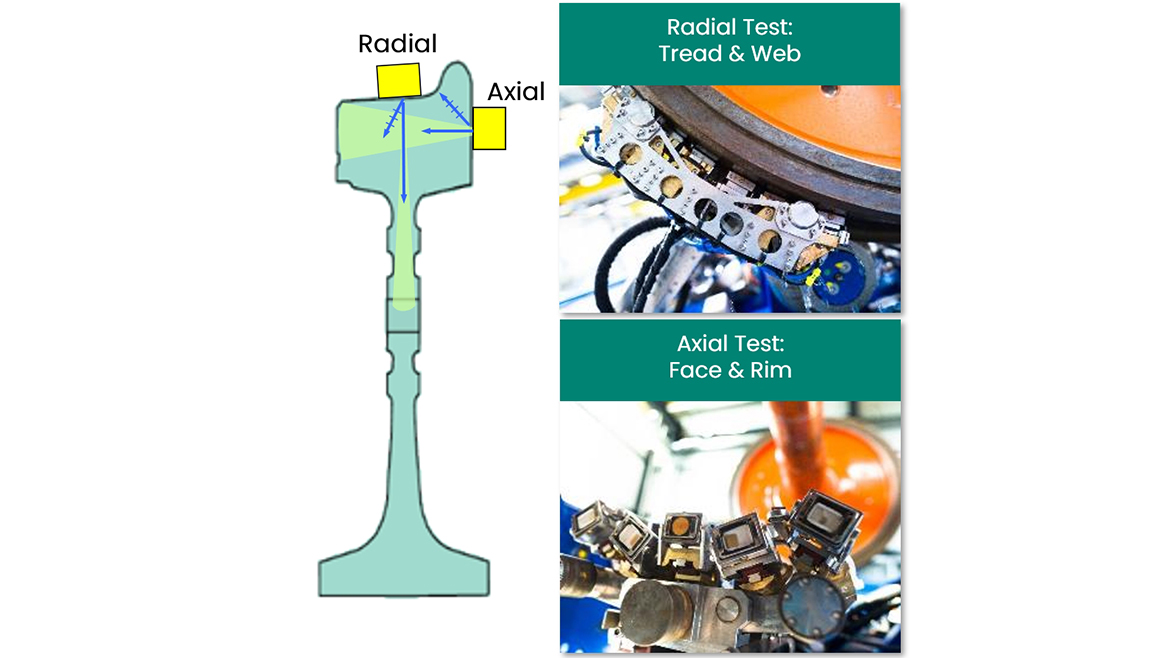
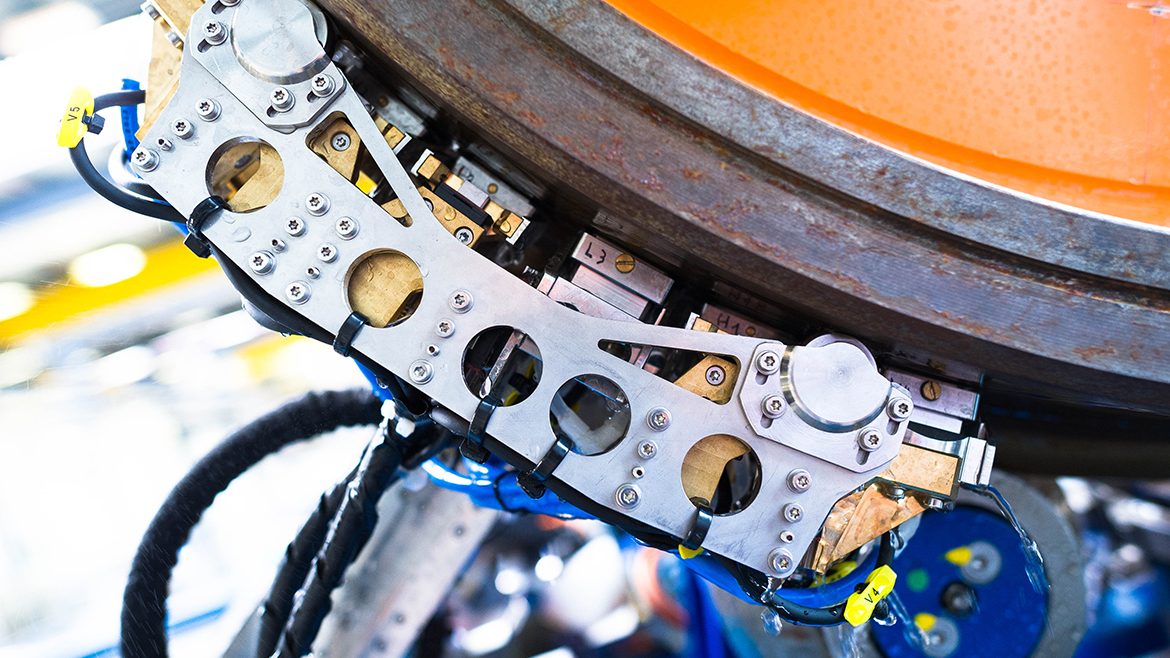
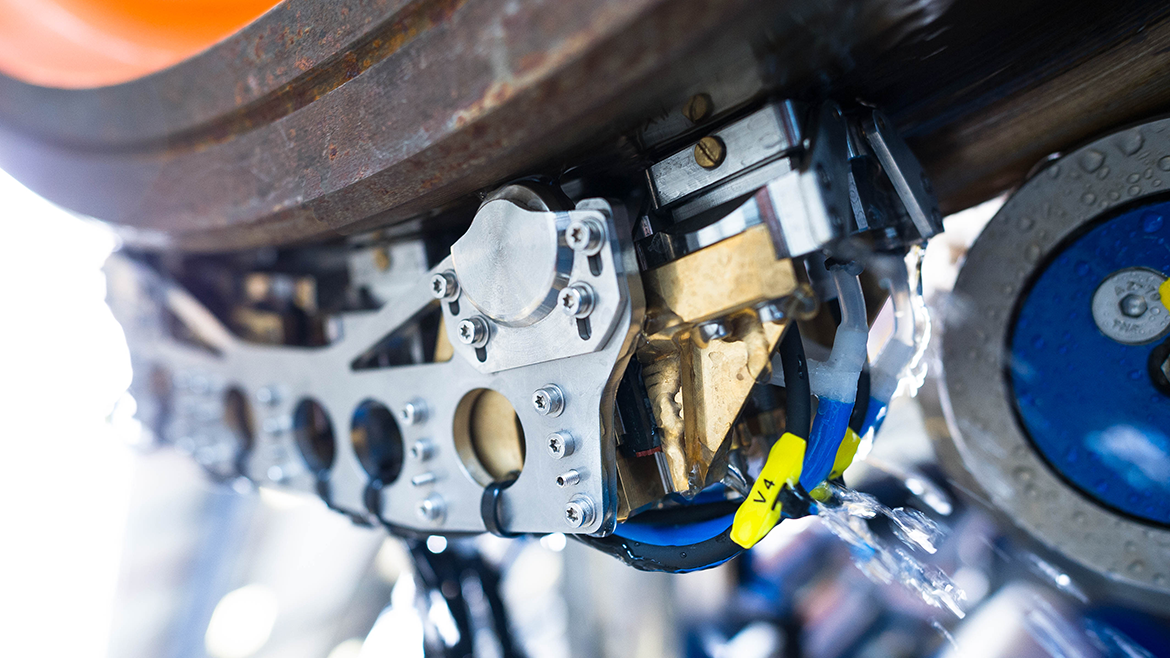
Such an intelligent system significantly reduces false calls by eliminating geometric echoes. Automatic defect recognition (ADR) is just the next consequential step forward. This not only increases the accuracy of defect detection and allows for easy interpretation by the operator, but also contributes to a more efficient and reliable inspection process.
Manual testing: empowering inspectors in the field
In the aerospace sector, or in any industry where manual inspections are required in confined spaces or in rugged conditions, portable phased or matrix array ultrasound technology is a significant advance without much additional equipment. Efficiency, portability, and accessibility are key factors for operators in these industries. Newly patented technologies on the market take a unique approach by integrating phased array power including front-end electronic directly into the probe. This eliminates the need for an additional phased array instrument, resulting in a lighter, and more versatile and cost-effective solution. Combined with advanced roller probes, such solutions are ideal for inspecting large-format, non-necessarily flat composite materials such as those used in the aerospace, space exploration, and wind energy industries. The portability and ease of use of this handheld solution is unmatched, giving inspectors unparalleled flexibility and accessibility in their inspections.
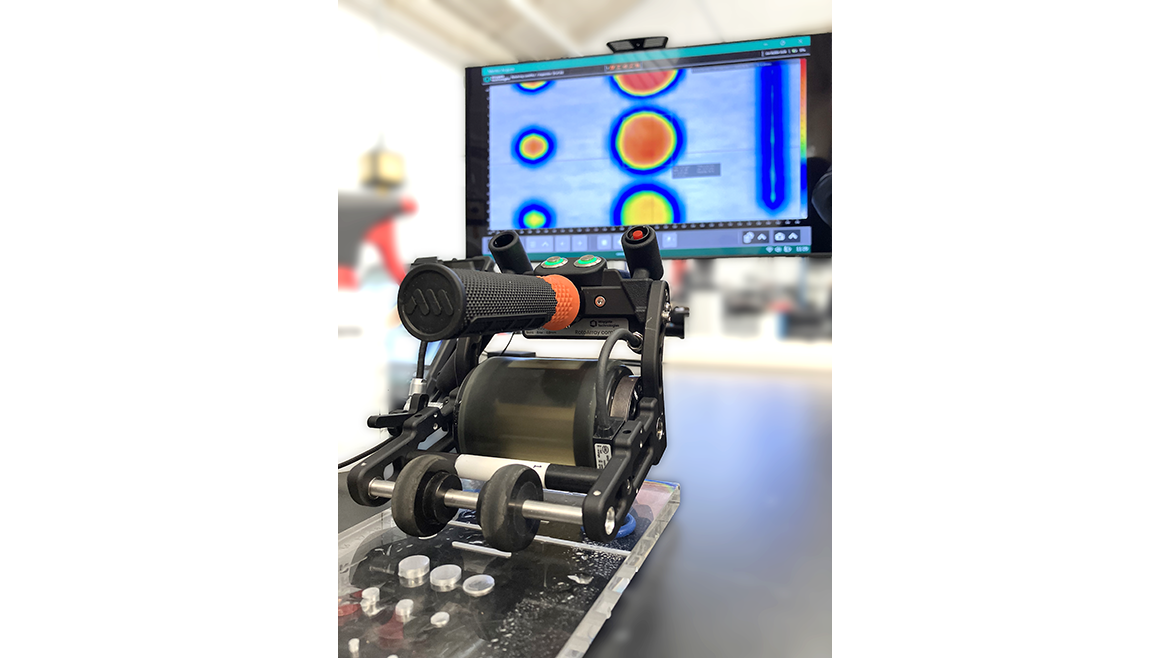
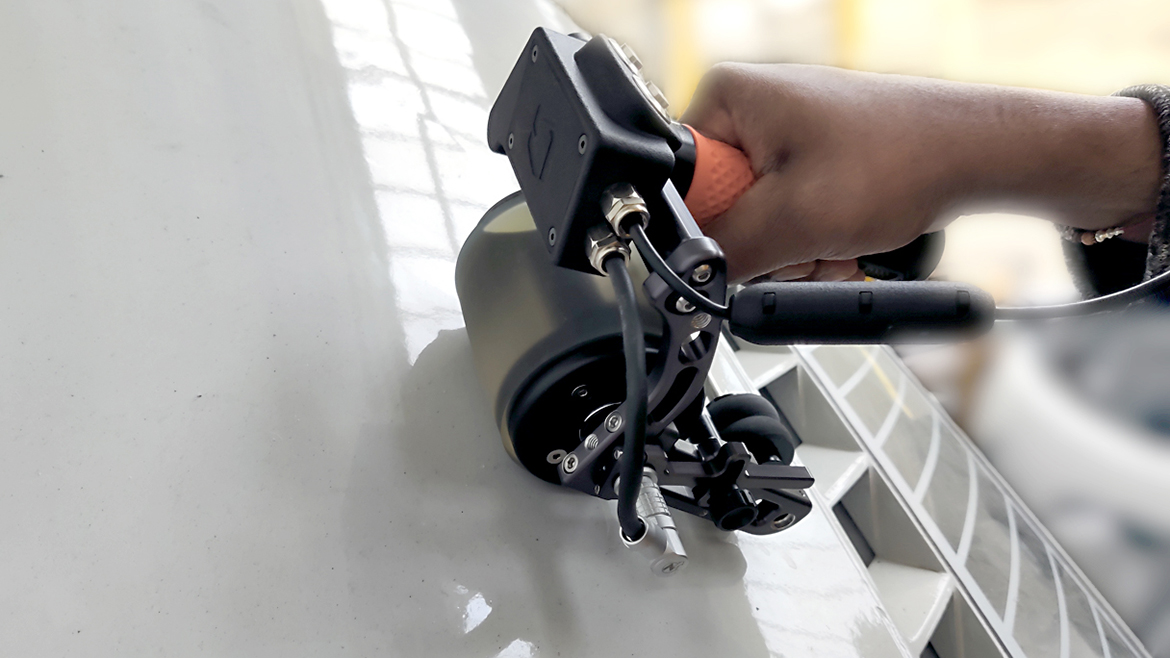
The latest technology ensures maximum compactness by minimizing the functionality of the phased array electronics to a remarkably compact chip the size of half a thumb and allowing power to be supplied via a USB port on a tablet or PC. This makes such solutions not only technically efficient, but also cost effective.
The future is smart
In the landscape of industrial ultrasonic testing, the advent of smart technology represents a significant leap forward. Its roots in the healthcare sector have paved the way for its integration into industrial applications, promising enhanced testing quality, reduced human error, and improved overall efficiency.
As we navigate an era of increased regulatory scrutiny, a shortage of skilled operators, and an ever-growing need for thorough inspections, the adoption of smart inspection technologies becomes imperative. Matrix technology and miniaturization through electronics stands at the forefront of this technological revolution, offering a glimpse into the future of ultrasonic testing.