Recent years have undoubtedly highlighted the growing importance of industrial automation amid labor shortages, supply chain issues, and disruptions related to COVID-19. However, the demand for automation technologies was primed for growth regardless, as businesses of all types seek out a means to improve production efficiency and deliver higher production rates to meet customer needs and keep pace with competitors.
While robots are likely the first component that comes to mind when automation systems are discussed, these systems are comprised of several different types of technologies, including machine vision. Pairing machine vision technologies with robots creates a flexible automation system with capabilities that go far beyond the bounds of performing preprogrammed and repeatable tasks. With machine vision, robots can be deployed for a wide selection of tasks, including pick and place (Figure 1), palletizing and depalletizing, flexible inspection, and automated assembly. As machine vision technologies advance, automation systems — and businesses around the world — are reaping the benefits. For example, 3D imaging, artificial intelligence (AI) software, and industrial computing have all seen notable developments in recent years. In fact, these technologies are often integrated together into systems that perform new tasks across a range of industries.
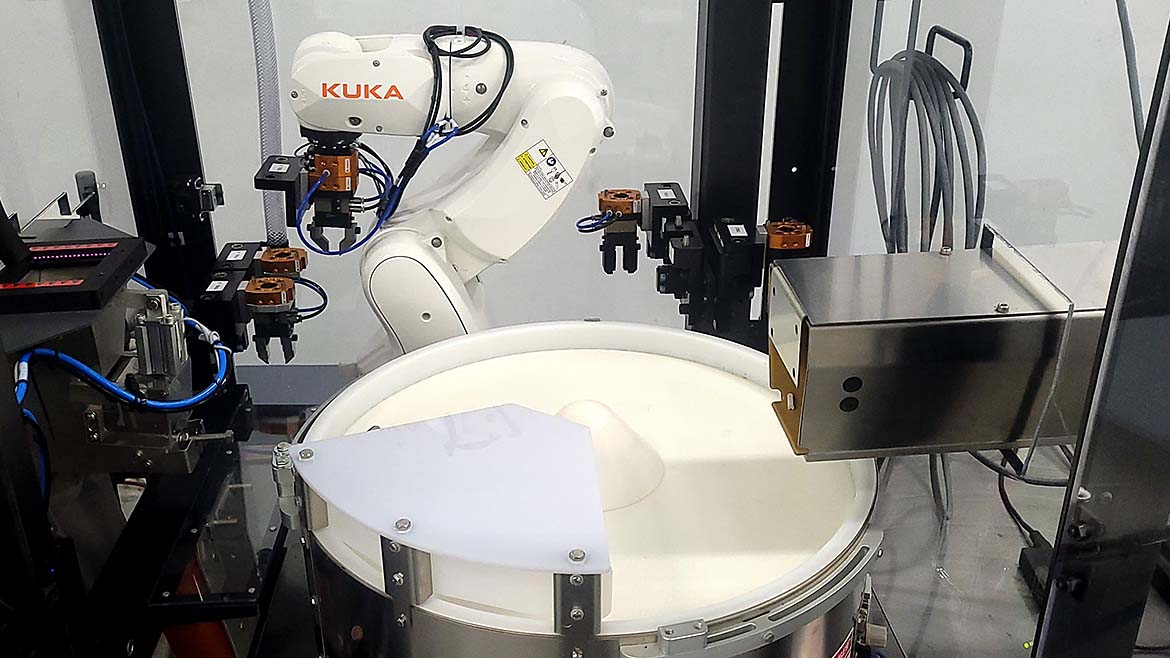
Warehouse Automation on the Rise
Market figures in 2023 show a down year for automation according to the Association for Advancing Automation (A3), which shows less robot orders year over year. A silver lining can be found, however, as 2022 figures were likely inflated by the post-COVID surge in orders. In fact, the overall automation market should continue to grow at a healthy rate in the coming years. The International Federation of Robotics’ World Robotics 2023 Report shows that a record 600,000 units are predicted to be installed in 2024, while market intelligence company Interact Analysis forecasts 5%–7% growth in the industrial robot market out to 2027.
Warehouse automation is a key growth driver in the overall automation space. While overall order intakes were down in 2023, Interact Analysis predicts a rebound in 2024 and double-digit growth into 2025 and beyond. While many types of automation technologies are deployed in warehouses and fulfillment centers today, application-specific vision-guided robot systems have become an integral part of many processes, so companies can deploy a turnkey system instead of building a system from the ground up, which reduces deployment time, removes the need for customization with every installation, and makes automation more accessible to a broad range of industries. In addition, such systems represent a convergence of some of the most notable technological advancements in machine vision and automation. For example, 3D imaging continues to progress and has become more accessible to systems integrators and vision engineers.
3D Imaging Eases Pick-and-Place Concerns
Once considered an emerging technology, 3D imaging has become an established and critical part of the machine vision ecosystem. This technology continues to advance to adapt to changing market conditions and customer needs. Take robotic pick-and-place or bin-picking systems, for example. Robots today are deployed to identify, pick, and place many different product or object types, which can vary in size and shape and might be shiny or reflective. It can be difficult to capture images of such objects at high speeds, but 3D advances have eased this problem.
Today, 3D cameras offer faster cycle times and higher resolutions, higher sensing accuracy, higher dynamic range, and sometimes the ability to capture 3D images of transparent objects or objects in motion. In addition, today’s 3D cameras offer lower costs, smaller footprints, less maintenance, and overall improved ease of use. While 3D imaging continues to progress and enhance the capabilities of vision-guided robots, pairing it with other advancing technologies such as artificial intelligence software creates even more flexible systems that can address major hurdles and enhance productivity even further.
AI Adds Flexibility
Pick-and-place or bin-picking operations have evolved over time — from manual picking to 2D systems to 3D systems and now to 3D systems enhanced with deep learning or machine learning capabilities. This evolution has transpired in the wake of new challenges, including the need to recognize and handle a wide variety of different product or part types without a significant amount of custom programming and configuration.
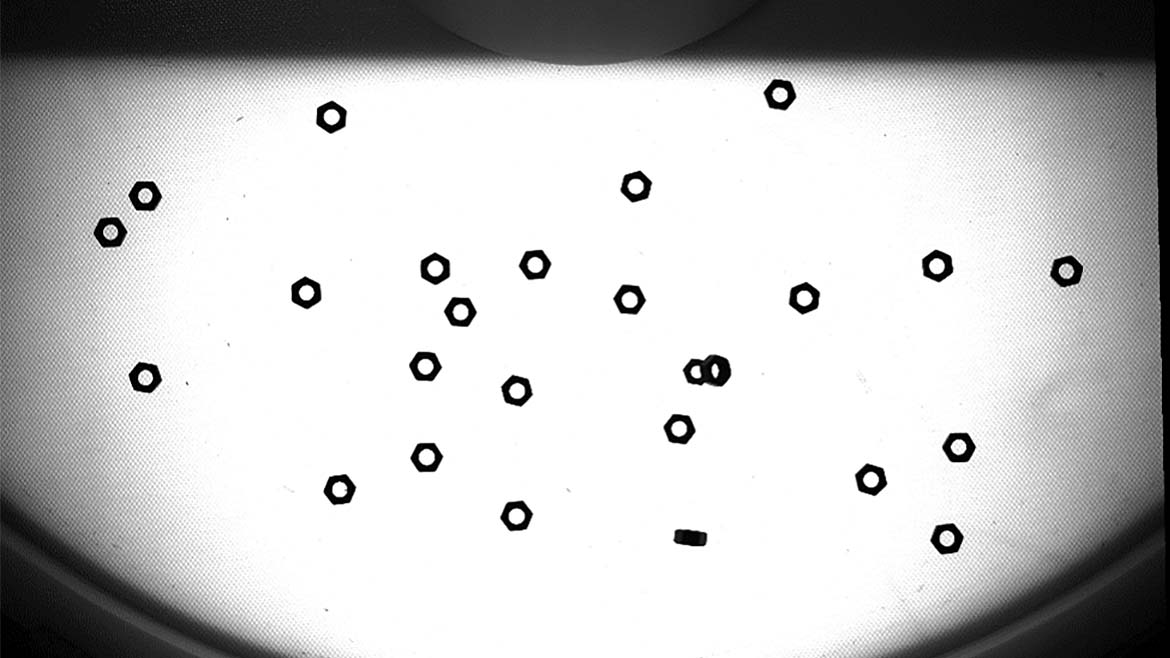
Adding machine learning or deep learning software into a robotic pick-and-place or bin-picking system improves object detection and pick accuracy as the software learns over time. The system can also recognize and pick a much wider variety of parts, which may be of different shapes, sizes, colors, or materials (Figure 2). In addition, AI-based software allows a system to recognize and classify objects it has not seen before based on similar objects it has been trained on or previously encountered. A system can also be trained on specific datasets to pick unusual or custom items, such as fruits, vegetables, or proteins.
Continuously Improving Robot Picking
Shutdowns related to the initial wave of COVID-19 highlighted the importance of automation systems like these in logistics and fulfillment operations. For example, right around this time, a packaged consumer goods company in Asia began to lean heavily on an autonomous pick-and-place robot to handle the more than 20,000 SKUs that it stocks. The system combines a collaborative robot, 3D imaging, advanced gripping, and continuous machine learning to automate the fulfillment process. In operation, the system uses 3D imaging to capture point clouds, allowing the software to direct the robot where to pick, while machine learning algorithms allow for the model-free picking of new products and learn over time to continuously improve picking.
At a digital pharmacy facility in Europe, the same autonomous pick-and-place system has been deployed to handle more than 100,000 product types. In this use case, an automated storage and retrieval system (ASRS) presents inventory totes to each robot. These robots then autonomously handle inbound receiving and outbound order fulfillment tasks, including picking, scanning, and placing thousands of SKUs each day. With this technology, the company has no more than 20 employees working alongside the automation system to achieve an output of 25,000 to 30,000 parcels per day. Competitors might have as many as 300 people working around the clock to achieve similar results.
Powerful Processing for the Edge
Robotic pick-and-place systems and others can solve new problems and add new capabilities based on the progression of several different types of technologies, such as 3D imaging, robotics, AI-based software, and processing (Figure 3). When dealing with compute-intensive applications such as these, systems needs a powerful computer that can keep pace in hectic industrial environments.
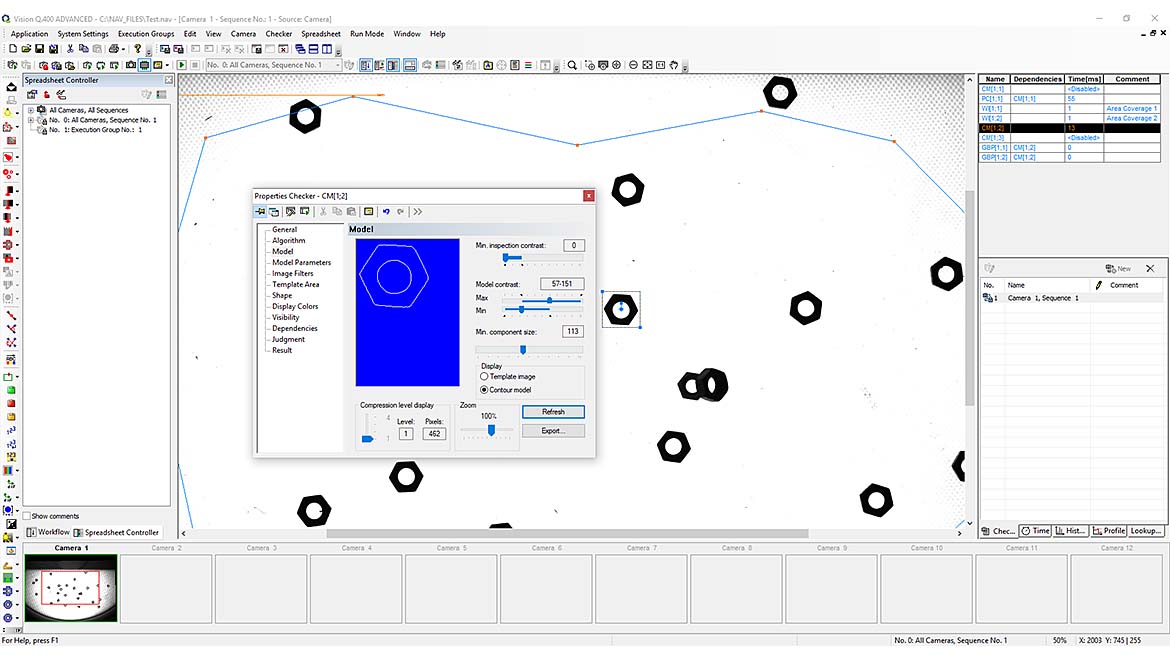
Industrial PCs and their underlying components continue to push automation capabilities forward as companies release technologies specifically designed for edge AI and robotics. Examples include NVIDIA’s Jetson platform. This compact, high-performance system-on-module (SOM) incorporates GPU, CPU, memory, power management, and high-speed interfaces. These systems require less power while still delivering fast, powerful processing capabilities.
Automating Tomorrow
Manufacturing and logistics businesses continue to look for ways to enhance efficiency and increase throughput to keep pace in an ever-competitive landscape. Vendors within the automation space — including those developing 3D imaging, AI-based software, and more — continue to advance technologies and unlock new capabilities in the systems of tomorrow.