Packaging, electronics, automotive, clinical diagnostics… Smart cameras have made their way into all sorts of industries and applications. Machine vision engineers never get to rest on their laurels because there’s always some new process to improve. Today’s smart cameras need to be modular, scalable and customizable—as well as exceptionally powerful and high-performing—to meet ever-increasing demands in automatic identification, machine vision, quality inspection, robot guidance and automation in general.
Fortunately, there are many ways that today’s smart cameras can be designed to be versatile and powerful at the same time. From lights to lenses to processing technology, machine vision experts have multiple opportunities to enhance flexibility while maintaining speed and performance.
1. GET THE LIGHT JUST RIGHT
There’s a reason why “Lights… Camera… Action!” is always in that order. Without proper lighting, little else matters. Advanced software algorithms can enhance contrast to some extent, but it’s much better to bring out the contrast with smart use of illumination. One of the tricky aspects of machine vision lighting is that no single light source is optimal for all situations. Dark field illumination, for example, is great when you’re inspecting the raised edges of a part. However, if you’re trying to capture printed human-readable characters on the curved surface of a metal part, you’ll need an entirely different sort of light.
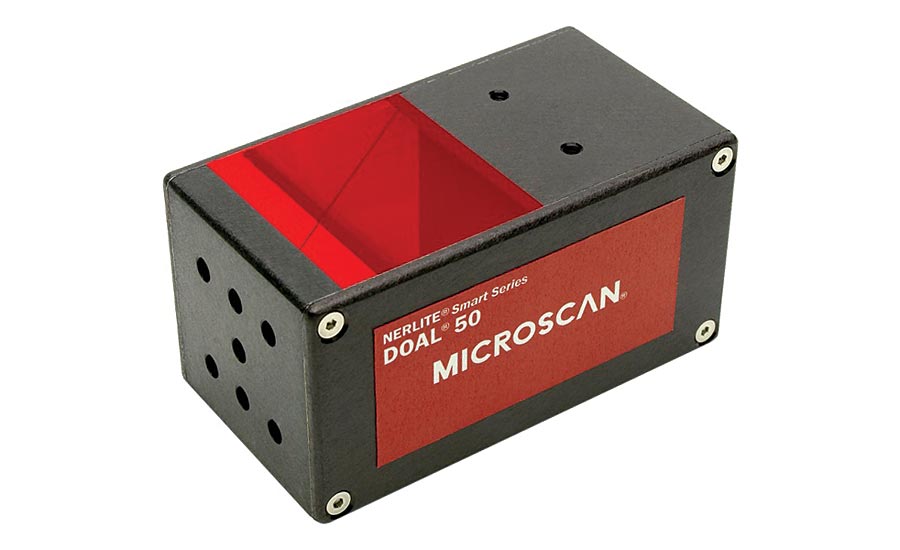
Diffuse, uniform illumination can increase the accuracy and repeatability of machine vision inspection.
Adapt to the Surface
When trying to read barcodes, or perform optical character recognition, the marking surface really matters. It could be flat, bumpy, curved, shiny, or a combination of the above, and there are different lighting recommendations for each. Almost any light type is good for imaging non-shiny, or flat diffuse surfaces. For shiny surfaces, such as codes covered in cellophane, special types of diffuse and/or polarized light sources make a huge difference.
Play with Color
When parts are marked with different ink colors, it’s possible to enhance contrast by choosing illumination from the opposite end of the color spectrum. Blue markings on metal, for instance, will show up better under red light. Infrared and UV light can also improve contrast for certain special types of ink that respond to these wavelengths.
The takeaway point here is that smart cameras need to be able to support numerous lighting arrangements to deal effectively with the wide variety of surface textures and color combinations that they may encounter. Changing the light source color or bringing it in at a different angle could make a huge difference in contrast. Modern smart cameras won’t be able to incorporate all lighting options, but they should be able to support a wide variety of lighting arrangements. The shape of the lens also affects lighting options because it determines the amount of space on the camera that can be used for LED placement.
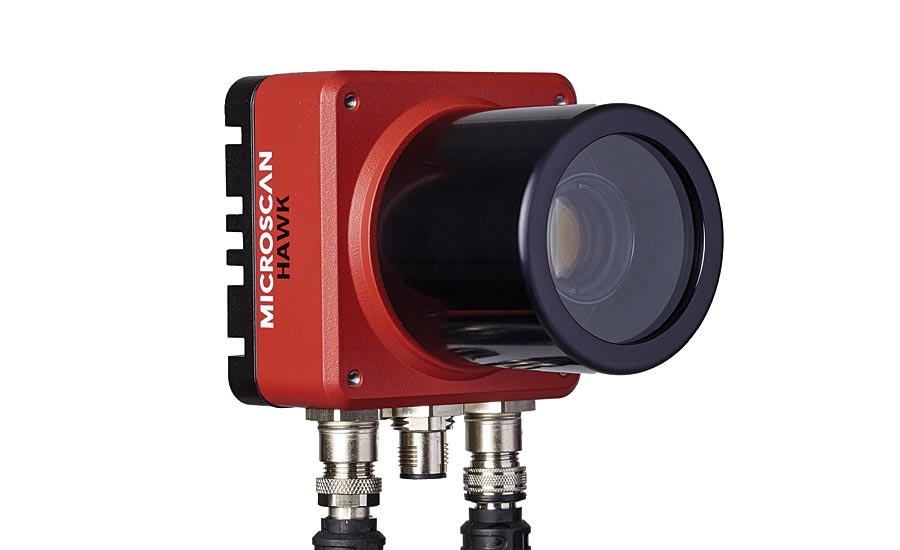
Although a C-Mount lens takes up a large amount of space on the front of a smart camera, it can be very helpful for tasks like defect detection and gaging.
2. CHOOSE THE BEST LOOKING-GLASS
Viewing the world through rose-colored glasses can make quite a difference, and machine vision systems also have choices in how they “see” things. From variations in field of view width to different focus methods, each vision task has a specific lens requirement. There are benefits and constraints for each type of lens, so a good smart camera will be able to support a variety of them.
M12 Lenses
M12 optics typically come in handy for applications best suited to integrated lighting. Since these lenses are small, they leave plenty of room on the face of the camera to incorporate lighting-related accessories such as LEDs. M12 lenses can be either fixed focus, or paired with an autofocus element, so they’re versatile while also being relatively affordable.
C-Mount Lenses
First used in cinematography (“C” stands for cinema), C-Mount lenses work well in applications where high quality imaging is necessary. They’re relatively large however, so they don’t offer much room for accessory light placement on the face of the camera. They are typically used with remotely mounted lights. The advantages of C-Mount lenses are most pronounced in demanding applications such as defect detection and gaging.
Match the Sensor
To work in harmony with the camera as a whole system, lenses need to be on a par with sensors. For instance, a 1” format megapixel sensor should be coupled with lenses that are specifically designed to work with 1” format megapixel sensors. The extra money spent on high-quality sensor technology might be wasted if a lens can’t provide the same level of quality.
3. EMBRACE REAL-TIME PSEUDO-HARDWARE
Manufacturers always want their production lines to move as quickly as possible. Smart cameras are expected to keep pace with parts that could be moving past them at more than a thousand units per minute. When these parts enter the camera’s view, the camera is triggered to take a picture. However, if the delay between the trigger input and camera’s photo-taking is too long, the item might have moved out of the field of view before it can be photographed. This is a major problem for cameras that control the input, sensor and outputs using general-purpose input/outputs and software.
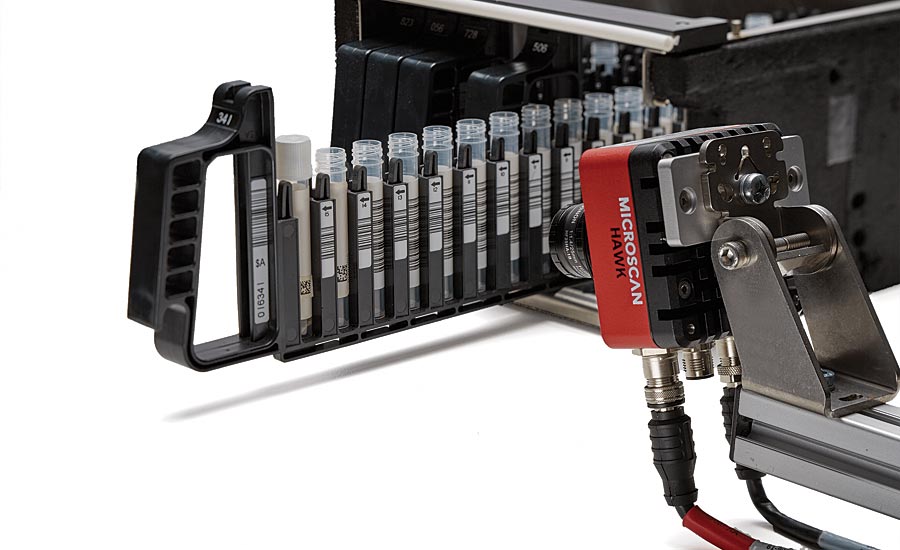
The addition of an FPGA has worked wonders for the speed and processing power of today’s smart cameras.
Fortunately, there’s a much faster option. The field-programmable gate array, or FPGA for short, has proven to be a great solution to the speed problem for today’s smart cameras. It controls the input, sensor and output with a single, reconfigurable integrated circuit so that these highly time-sensitive operations can be done in microseconds. Basically, the FPGA is a piece of pseudo-hardware that allows the camera to achieve a real-time response to triggers.
FPGAs are also extremely helpful in smart camera development and testing because their logic is reconfigurable, unlike that of application-specific integrated circuits (ASICs), which can’t be altered in any way after they’re manufactured. Using FPGAs, engineers can reap the benefits of speedy, specialized hardware coordination and also use a single integrated circuit to test out multiple pseudo-hardware configurations.
4. SYNC IT UP
Smart cameras are capturing data at a rapid-fire pace on fast-moving automation lines arrayed with many other elements such as conveyors, robots and reject mechanisms. Synchronization between these elements is extremely important. Fortunately, there’s a fail-safe way to keep smart cameras in concert with one another and with the rest of the production line. Also known as IEEE 1588, the Precision Time Protocol (PTP) produces synchronized timestamps through a system of multiple clocks that all of these elements can use to stay in time-step with one another. In fact, PTP can synchronize multiple devices to within just a few microseconds of each other.
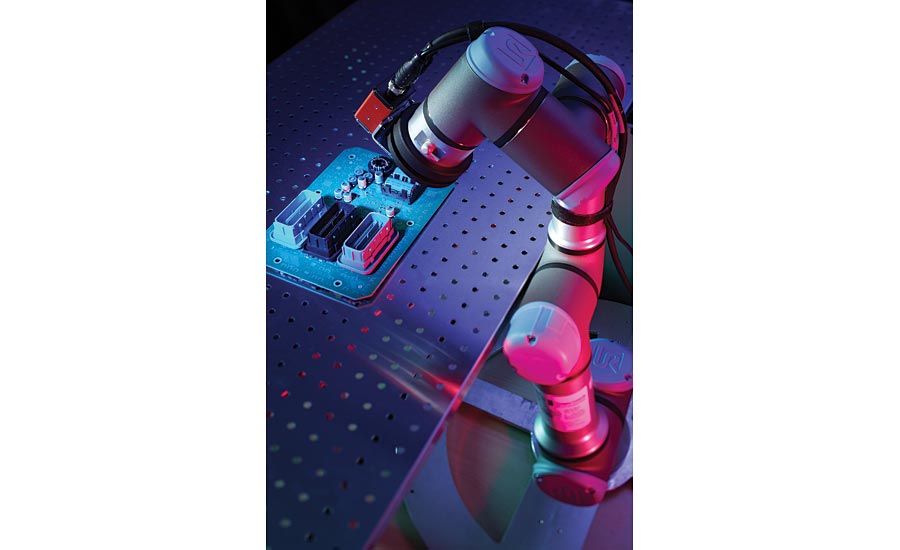
Smart cameras can be attached to robots to help guide them in various tasks. In such applications, precise timing is essential.
PTP uses a master-slave setup in which clocks running on each camera and other automation components are coordinated with a “master” clock running on the network. The master clock sends a signal across the network that is picked up by the “slave” clocks and used to synchronize their own timestamps based upon the calculated delay in signal arrival. The precise synchronization that results from this process is used to record data such as trigger time, part position and conveyor belt speed and then to guide actions that the robots or machinery will take. It could, for instance, direct a robot to grasp a part in a specific location many seconds later when it’s further down the conveyor line.
5. KEEP IT SIMPLE
With so much functionality incorporated into a single device, it may seem impossible to turn the resulting product into a paragon of simplicity. Nonetheless, simplicity—the sort that makes it possible to start reading and inspecting right out of the box—is crucial to the power and versatility of modern smart cameras. If these devices were tricky to integrate into the typical industrial automation system, manufacturers would be less likely to adopt them. For this reason, the final consideration for smart camera design is to make sure that the most important tasks can be accomplished with intuitive, plug-and-play technology.
Simplicity and flexibility are, to some extent, a trade-off. This is where much of the challenge of smart camera design lies, and it’s also the driving force behind much of the innovation. Engineers who love a good puzzle will find an infinite source of inspiration here. With the demand for automation systems to accomplish more without requiring the constant input of experts, the simplicity/flexibility trade-off for machine vision will surely occupy the attention of engineers for years to come. V&S